Производство Проволоки: оборудование, технология изготовления
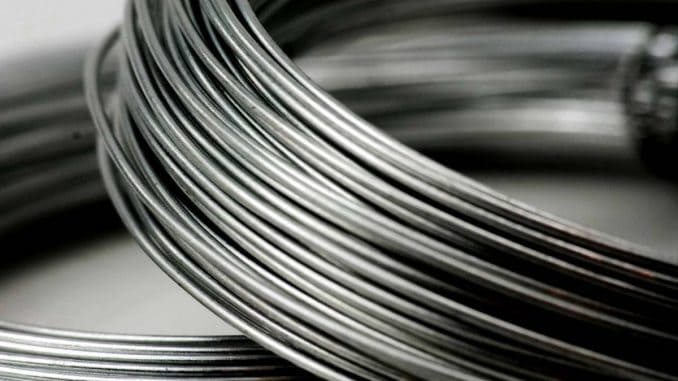
Проволока представляет собой металлическую нить или шнур. Как правило, проволока круглого сечения, но встречаются изделия и шестиугольного, квадратного, трапециевидного или овального сечения. Проволока может быть выполнена из стали, меди, алюминия, цинка, никеля, титана и их сплавов, а также массы других металлов. Стали также выпускать биметаллические и полиметаллические проволоки.
Чаще проволока производится посредством протяжки или волочения через последовательно уменьшаемые отверстия. В результате можно получить проволоку разного диаметра вплоть до десятков миллиметров.
Проволока отличается широтой применения. Так ее можно использовать при изготовлении электрических проводов, пружин, метизов, свёрл, электродов, термопар, разнообразных электронных приборов и для прочих целей.
Оборудование для производства проволоки + видео
Станы для мокрого волочения, как правило, работают по технологии скольжения, и могут совмещаться со станами сухого волочения любой кратности. Их оборудуют независимыми синхронизированными электродвигателями в разных модификациях.
Также широко применяются прямоточные станы для сухого волочения, которые отличаются наиболее современной конструкцией. Преимущественно используется такие станы для производства проволоки небольшого диаметра из высоко-, низкоуглеродистой и нержавеющей стали. Главные отличительные черты стана – это компактность, отсутствие ремней и шкивов между приводами и барабанами, бесшумность работы, отсутствие вибраций. Конструкционный дизайн является главной особенностью таких станов. Благодаря прочности и устойчивости рамы, стан можно полностью транспортировать, отсюда минимум временных затрат на установку и прокладку кабелей.
Прямоточные станы сухого волочения отличаются горизонтальным расположением барабанов. Такие станы, как правило, используются для производства проволоки из низко-, высокоуглеродистых сталей, а также из нержавеющих сталей. Преимущества такого оборудования – высокая надежность, эргономичность и простота в эксплуатации конструкции, которая при монтаже не требует специального фундамента. Также в установке применена высокоэффективная система охлаждения барабанов и предлагается опциональное оборудование.
Разнообразные размоточные устройства для катанки также пригодятся для производства проволоки.
Видео как делают катанку из меди:
Также в сфере производства широко применяются крутильные машины сигарного типа, машины двойной скрутки и бугельного типа.
Технология производства проволоки + видео как делают
Производство проволоки включает ряд классических операций, которые могут повторяться вплоть до трех раз. Количество повторений зависит от того, какой нужен размер диаметра проволоки.
Первой стадией процесса является термическая обработка металла. Затем происходит подготовка поверхности металла к волочению. На конечном этапе осуществляется само волочение на заданный размер.
Как делают:
С целью обеспечения проволоки специальными свойствами, в процессе ее производства вводят дополнительные операции. К примеру, наносятся разные покрытия или осуществляют термическую обработку. Главным оборудованием при производстве проволоки является печь с малоокислительным нагревом. Посредством растворов соляной и серной кислот осуществляется снятие окалины. Бура, известь, фосфатные соли и медь используются при волочении в качестве подсмазочного слоя.
Другим не менее важным оборудованием для производства проволоки являются станы с интенсивным охлаждением барабанов и волок. Именно их и применяют непосредственно для использования волочения. Применение такого процесса обеспечивает высокие пластичные и прочностные свойства металла.
За счет использования современных смазочных материалов обеспечивается высокая коррозионная стойкость, высокая адгезия к различным материалам и оптимизация количества смазки.
С целью увеличения качества изготавливаемой проволоки, следует систематически обновлять волочильное оборудование, оснащая его дополнительными приспособлениями, например, для снятия внутреннего напряжения и для прочих целей.
Для того чтобы получить различную толщину покрытия рекомендуется наносить цинковое покрытие способом погружения проволоки в соответствующий раствор. При использовании специальных обтирочных материалов и эмульсий, можно придать цинковому покрытию максимального блеска, гладкости и защиты от коррозии в течение длительного периода времени.
Линия цинкования:
Качество готовой продукции во многом зависит от соблюдения всех требований и норма изготовления проволоки. Стабильность технологического процесса оказывает непосредственное влияние на качество готовой продукции.
Следует отметить, что одной из тенденций современного производства проволоки является переход от классической технологии химического травления в стандартном растворе соляной кислоты для очистки поверхности катанки от окалины к более перспективной и максимально безопасной для окружающей среды, бескислотной технологии механической очистки. Для этого используется современное оборудование для механического удаления окалины. С его помощью можно добиться высокой степени очистки, сравнимой с получаемой при стандартном кислотном травлении. При этом технология характеризуется весьма большим практическим применением. Более того, новая технология позволяет избежать значительных проблем, которые связаны с утилизацией отработанных растворов.

Волочение проволоки — особенности технологии и оборудование
Одним из способов качественной обработки металлических заготовок является волочение проволоки. Это особая технология на станках, при которой цветные металлы протягивают сквозь круглое или фасонное отверстие (фильеру) специального инструмента – волоки. Результатом процесса является уменьшение заготовки и увеличение ее длины. Это актуально для производства проволоки разного профиля и другой проволочной продукции, применяемой во всех областях человеческой деятельности.
Особенности процедуры
Процесс волочения несложный. В качестве исходного сырья используют катаную, литую или прессованную заготовки. Работы выполняют на специальном оборудовании – волочильных станках. Форма, диаметр и сечение готового длинномерного изделия зависят от параметров фильеры. По сравнению с прокаткой металла, технологическая операция имеет много преимуществ:
- Высокая производительность за счет автоматизации процессов станков.
- Волочение проволоки направлено на получение геометрически правильной продукции, с ровной и чистой поверхностью. Это позволяет снизить объем последующей обработки.
- Изделия обладают улучшенными механическими характеристиками.
- Возможность производить разные виды металлического шнура, в том числе порошковой проволоки, а также калиброванные прутки, тонкостенные трубы диаметром до 5 мм.
- Диаметр изделий варьируется от 1 до 10 микрон.
- Низкие затраты на волочильные станки.

Схема процесса волочения
Этапы волочения
Технология производства проволоки разделена на пять этапов.
Этап №1
Процедура травления с целью удаления поверхностного слоя материала – окалины, которая мешает волочению:

Травление металла в непрерывном травильном агрегате
- Подготовка поверхности: обезжиривание, шлифование, полировка, вырезание бракованных участков.
- В окалине присутствуют сложные соединения других элементов, поэтому исходное сырье подвергают химической или механической обработке.
- Выбор метода травления зависит от природы металла. Удаление окалины производят фосфорной, соляной, азотной, плавиковой или серной кислотой, нагретой до 50 0C.
- Обрабатываемую поверхность очищают от продуктов травления. Это промывка заготовок с помощью специального растворителя или воды.
- После процедуры металл должен приобрести матовый оттенок.
- Сушка проволоки в течение часа при температуре 75–100 0C. Для этого используют специальные станки с сушильными камерами.
Этап №2

К термической относят процессы
Термическая обработка проводится для того, чтобы заготовку сделать полумягкой, с мелкозернистой структурой, свободной от внутренних напряжений. Металл нагревают до определенной температуры, некоторое время выдерживают в таких условиях, охлаждают.
Отжиг изменяет свойства материала и облегчает процесс волочения проволоки. Скорость нагрева зависит от теплопроводности металла. Быстрота охлаждения определяется твердостью, которую нужно достичь после отжига. Стальные проволоки охлаждаются медленнее, чем углеродистые соединения.
Этап №3
При помощи специального молота или ковочных валок концы заготовки сплющивают и выравнивают. Процедура позволяет закреплять металл на барабане станка и пропускать сквозь фильеру.

Фильера для волочения проволоки
Этап №4
Волочение проволоки: протравленное обработанное сырье протягивают на станке с максимальной скоростью через плавно сужающийся канал. По числу одновременно протягиваемых прутов процесс бывает:
- Однониточный.
- Многониточный.
По типу конечного продукта:
- Длинномерные изделия в виде мотков или катушек.
- Калиброванные прутки.
По количеству переходов волочение проволоки имеет две разновидности:
- Однократное – при котором протягивание осуществляется через одну волоку. Процесс подходит для толстой, плохо деформируемой проволоки.
- Многократное, когда материал подвергается сжатию последовательно на нескольких волоках.
Станок для волочения формирует профиль и размеры готовой продукции.
Этап №5
Завершающий этап предполагает выполнение отжига. Это делается с целью устранить вредное напряжение после волочения. Изделие становится мягким, устойчивым к разрывам, податливым к загибам, удлинению и скручиванию. После термической обработки проводят дополнительные отделочные операции, среди которых:
- Цинкование проволоки.
- Консервационная смазка.
- Разрезание на части.
- Маркировка.

Вид готовой проволоки после всех процессов обработки
Оборудование для выполнения волочения проволоки
Волочение проволоки происходит на станке, оборудованном специальным инструментом – волоком с отверстием, которое называется «глазком». Отверстие имеет постепенно уменьшающееся сечение, через которое протягивают заготовку.
Конструкция оборудования зависит от особенностей тянущего механизма:
- Станок для волочения, в котором металл наматывают на барабан и снимают в виде мотка или катушки. Барабанные машины бывают однократными и многократными.
- Агрегат, обеспечивающий прямолинейное движение заготовки. Устройства этой группы разделяются на цепные, реечные и винтовые.
Основной рабочий инструмент станка для производства проволоки – волока. Он состоит из двух элементов: непосредственно волоки и обоймы. Такая конструкция обусловлена условиями эксплуатации и материалом, из которого сделана фильера. Ее изготавливают из качественных твердых сплавов, которые устойчивы к истиранию, расколу и механическому воздействию. Инструмент станка условно разделен на четыре рабочие зоны:
- входная;
- смазочная;
- деформирующая;
- калибрующая.

Волоки для волочения проволоки
Волоки бывают монолитными и составными из нескольких сопряженных частей. Сборная конструкция экономичнее монолитного механизма по расходу электроэнергии.
Во время волочения проволоку укладывают в стальную обойму, которая служит изделию защитой от излишнего сжимания.
На многих больших предприятиях калибровочные цеха оснащены разноплановыми станками под всевозможные виды продукции.
Удаление окалины
Волочение проволоки будет успешным при условии качественной обработки поверхности заготовки. Удалить окалину с поверхности можно тремя способами.
Электрохимический
Или электролитический метод позволяет увеличить скорость снятия ржавчины и окалины с поверхности металла под воздействием электрического тока и раствора кислоты. Процессы электрохимической обработки включают в себя два варианта.
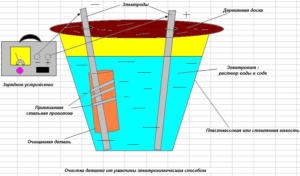
Очистка деталей от ржавчины электрохимическим способом
Анодный – основан на растворении металла в контакте с положительным плюсом источника тока. Выделяющийся кислород способствует механическому отрыванию оксидов. Применяется для легированной и углеродистой стали с целью удаления тонких пленок.
Катодный – оксиды железа восстанавливаются под воздействием атомов активно образующегося водорода. Это опасный способ по сравнению с предыдущим, так как отрыв окалины плохо контролируется, и изделие обретает травильную хрупкость.
Химический способ
Незаменим, когда в качестве сырья используется кислостойкая сталь. Остатки флюсов и окислов удаляют с помощью раствора хлористых солей, щелочи или кислоты. Любое химическое вещество требует специальных знаний и осторожного обращения.
Традиционное кислотное травление предполагает последовательную обработку металла в двух ваннах – сернокислотной и азотнокислотной при определенной температуре.
Есть много вариантов этого способа. Выбор раствора и условия обработки зависят от состава и структуры окисной пленки.
Механический
Подразумевает шлифовку, галтовку, полировку и крацевание. В основе метода лежат такие процессы:
- деформация изгибом;
- скручивание, растяжение;
- прямое воздействие на поверхность изделия специальных реагентов или абразивных материалов;
- использование инструментов: щетки, иглорезы, микрорезцовые приборы.

Оборудование для механического удаления окалины на проволоке
Комбинированный
Способ основан на применении химического и электрохимического методов.

Механические и комбинированные методы очистки
Особенности при волочении медной проволоки
Изделия, полученные путем волочения на станках, находят широкое применение в электронной и электрической областях. Как правило, используют проволоку толщиной от 20 мм до 10 мкм.
Изготавливать проволоку из меди следует на основе литых заготовок соответствующего профиля. Их подвергают плавлению, затем в горячем виде прокатывают. Поскольку процедура способствует появлению тонкой оксидной пленки, перед волочением проволоку обрабатывают водным раствором серной кислоты при температуре 45–50 0C.
Основной технологический процесс такой же, как и в производстве продукции из других металлов:
- Медную заготовку охлаждают воздухом, водой или специальным раствором.
- Поверхность смазывают мыльно-масляной эмульсией.
- Волочение проволоки проводят на 22-х и 18-кратных станках с применением прочной алмазной волоки.
- В процессе вытягивания заготовки используют волоки, отверстия которых четко соответствуют диаметру изделий.
- Рабочий инструмент может иметь одну или несколько матриц.
- Изделия диаметром до 0,05 мм оставляют без промежуточного отжига. К ним применяется технология погружного формования.
- Для максимально тонкого материала важно правильно подобрать смазочный состав. Это могут быть комплексные химические растворы, эмульсии или синтетические вещества.
- При необходимости медь подвергают термической обработке безокислительного типа в специальных электропечах, лишенных доступа воздуха.
- Кроме стандартного оборудования, для медных заготовок могут использоваться станки с роликами вместо отверстий для прохождения катанки.
- Благодаря такой технологии, готовые изделия имеют гладкую блестящую поверхность и соответствующий диаметр.
Многие промышленные предприятия эксплуатируют станки с совмещением операций волочения и отжига. Данный метод позволяет не только изготавливать проволоку из меди, но и производить медные трубы.
Видео по теме: Волочение проволоки — как это происходит
Волочение проволоки – особенности технологии и оборудование
Волочение, посредством которого производят проволочную продукцию, является несложной технологической операцией. Между тем, чтобы в итоге выполнения такой процедуры получить качественное изделие, осуществлять ее необходимо в правильной последовательности и использовать для этого соответствующее оборудование.
Линия производства проволоки по методу волочения
Основные этапы
Суть технологии, по которой выполняют волочение проволоки, заключается в том, что металлическую заготовку из стали, меди или алюминия протягивают через сужающееся отверстие – фильеру. Сам инструмент, в котором такое отверстие выполнено, называется волокой, его устанавливают на специальное оборудование для волочения проволоки. На то, какими диаметром, сечением и формой будет обладать готовое изделие, оказывают влияние параметры фильеры.
Принцип волочения металла
Выполнение волочения, если сравнивать такую технологическую операцию с прокаткой, позволяет получать изделия, отличающиеся более высокой чистотой поверхности и исключительной точностью геометрических параметров. Такими изделиями могут быть не только различные типы проволоки (электротехническая, используемая для сварки, вязочная и др.), но также фасонные профили, трубы и прутки разного диаметра. Полученные по такой технологии изделия отличаются и лучшими механическими характеристиками, так как в процессе волочения металла с его поверхностного слоя снимается наклеп. Что касается именно производства проволоки, то методом волочения можно получить изделия, диаметр которых находится в интервале от 1–2 микрон до 10 и даже более миллиметров.
Технология волочения сегодня уже хорошо отработана, для ее реализации используются современные модели волочильных станков, работающих без сбоев и позволяющих выполнять технологический процесс на скорости, доходящей до 60 метров готового изделия в секунду. Использование такого оборудования для волочения, кроме того, позволяет обеспечить значительную величину обжатия заготовки.
Технологическая схема волочения проволоки из нержавеющей стали
Изготовление проволоки по технологии волочения включает в себя несколько этапов.
- Исходная заготовка подвергается процедуре травления, для чего используется сернокислый раствор, нагретый до 50 градусов. С поверхности металла, прошедшего такую процедуру, легко снимается окалина, за счет чего увеличивается срок службы матриц волочильных станков.
- Чтобы увеличить пластичность обрабатываемой заготовки, а ее внутреннюю структуру довести до мелкозернистого состояния, выполняют предварительный отжиг металла.
- Остатки травильного раствора, который является достаточно агрессивным, нейтрализуют, после чего заготовку подвергают промывке.
- Чтобы конец заготовки можно было пропустить в фильеру, его заостряют, для чего может быть использован молот или ковочные валки.
- После завершения всех подготовительных операций заготовка пропускается через фильеры для волочения проволоки, где и формируются профиль и размеры готового изделия.
- Производство проволоки завершается выполнением отжига. После волочениия изделие также подвергают ряду дополнительных технологических операций – резке на отрезки требуемой длины, снятию концов, правке и др.
Особенности процедуры
Любой волочильщик проволоки знает такой недостаток волочения, как недостаточно высокая степень деформирования готового изделия. Объясняется это тем, что оно, выходя из зоны обработки волочильного станка, деформируется только до степени, ограниченной прочностью конца заготовки, к которому и прикладывается соответствующее усилие в процессе обработки.
В качестве исходного материала, который подвергают обработке на волочильных станках, служат металлические заготовки, полученные методом непрерывного литья, прессованием и катанием из углеродистых и легированных сталей, а также цветных сплавов. Наибольшую сложность процесс волочения представляет в том случае, если обработке подвергается стальной сплав. В таких случаях для качественного волочения необходимо довести микроструктуру металла до требуемого состояния. Чтобы получить оптимальную внутреннюю структуру стали, раньше использовали такую технологическую операцию, как патентирование. Заключался этот способ обработки в том, что сталь сначала нагревали до температуры аустенизации, а затем выдерживали в свинцовом или соляном расплаве, нагретом до температуры около 500°.
Методы волочения
Современный уровень развития металлургической промышленности, используемые в ней технологии и оборудование для получения металлов и сплавов позволяют не готовить металл к волочению таким сложным и трудоемким способом. Стальная заготовка, выходящая с прокатного стана современного металлургического предприятия, уже обладает внутренней структурой, оптимально подходящей для волочения.
Сама технология волочения и волочильное оборудование также совершенствовались на протяжении многих лет. В результате волочильщик проволоки сегодня имеет возможность применять современные волочильные устройства, позволяющие с минимальными трудозатратами гарантированно получать изделия высокого качества. Качество и точность обработки, выполняемой на таких волочильных специализированных станках, обеспечивается не только их оснащением современным рабочим инструментом, но и использованием при их работе комбинированной системы охлаждения, для которого применяются воздух и вода. Выходя с такого станка для волочения, готовое изделие обладает не только требуемым качеством и точностью геометрических параметров, но и оптимальной микроструктурой.
На каком оборудовании выполняется волочение металлов
Оборудование, которое волочильщик проволоки использует в своей профессиональной деятельности, называется станом. Обязательным элементом оснащения волочильной специализированной машины является «глазок» – волока. Диаметр волоки, разумеется, всегда должен быть меньше, чем размеры поперечного сечения протягиваемой через нее заготовки.
Соотношения первоначального и финального диаметров проволоки при различных типах волочения
На сегодняшний день производственные предприятия применяют волочильные специализированные станки двух основных типов, которые отличаются друг от друга конструкцией тянущего механизма. Так, различают:
- станки, в которых готовое изделие наматывается на барабан, чем и обеспечивается тянущее усилие;
- оборудование с прямолинейным движением готовой проволоки.
Прямоточный волочильный стан с программным управлением
На устройствах второго типа, в частности, выполняют волочение труб и других изделий, которые не требуют намотки на бухты. Именно проволоку, а также трубные изделия небольшого диаметра производят преимущественно на станках, оснащенных барабанным механизмом. Такие станки в зависимости от конструктивного исполнения могут быть:
- однократными;
- многократными, работающими со скольжением или без него, а также те, в которых используется принцип противонатяжения заготовок.
Многониточный волочильный стан обладает большей производительностью и выгоден на крупных предприятиях
Наиболее простой конструкцией отличается однократный станок для волочения. Манипулируя таким оборудованием, волочильщик проволоки выполняет ее протягивание за один проход. На волочильном устройстве многократного типа, которое работает по непрерывной схеме, формирование готового изделия осуществляется за 2–3 прохода. Крупные предприятия, производящие проволоку в промышленных масштабах, могут быть оснащены не одним десятком волочильных станков разной мощности, на которых изготавливается продукция различного назначения.
Основным рабочим органом любой волочильной машины, как уже говорилось выше, является фильера, для изготовления которой используют твердые металлокерамические сплавы – карбиды бора, молибдена, титана, термокорунд и др. Отличительными характеристиками таких материалов являются повышенная твердость, исключительная устойчивость к истиранию, а также невысокая вязкость. В отдельных случаях, когда необходимо изготовить очень тонкую проволоку из стали, фильера может быть изготовлена из технических алмазов.
Фильеры волочильной машины
Фильера устанавливается в прочную и вязкую стальную обойму. Это так называемая волочильная доска. За счет своей пластичности такая обойма не оказывает значительного давления на фильеру и одновременно снижает растягивающие напряжения, которые в ней возникают.
На современных предприятиях волочение металлов часто проводят с использованием сборных волок, которые позволяют эффективно выполнять такой процесс даже в условиях повышенного гидродинамического трения. Кроме того, применение такого инструмента снижает расход электроэнергии и увеличивает производительность работы оборудования на 20–30%.
Подготовка металлических заготовок
Волочильщик проволоки, используя специализированное оборудование, только в том случае сможет добиться качественного конечного результата, если поверхность заготовки будет соответствующим образом подготовлена. Такая подготовка заключается в удалении окалины, для чего могут быть использованы следующие методы:
- механический;
- химический;
- электрохимический.
Более простым и экономически выгодным является механический способ очистки от окалины, который используют для заготовок из углеродистых сталей. При выполнении такой очистки заготовку просто гнут в разные стороны, а затем обрабатывают ее поверхность при помощи металлических щеток.
Технология работы окалиноснимателя
Более сложной и затратной является химическая очистка от окалины, для выполнения которой используют растворы соляной или серной кислоты. Специалист, выполняющий такую сложную и достаточно опасную операцию, должен быть хорошо подготовлен и строго соблюдать все правила безопасности работы с агрессивными растворами. Без химического способа очистки не обойтись, если проволоку необходимо сделать из заготовок, выполненных из нержавеющих и других типов высоколегированных сталей. Следует иметь в виду, что сразу после выполнения химической очистки поверхность заготовки следует тщательно промыть горячей, а затем холодной водой.
Электрохимический способ очистки от окалины основан на методе травления в электролитическом растворе. В зависимости от особенностей выполнения такой метод может быть анодным и катодным.
Волочение медной проволоки
Чтобы более подробно познакомиться с технологией волочения, можно рассмотреть ее на примере того, как делают медную проволоку. Заготовки для выполнения такой операции получают методом литья, после чего их сплавляют между собой и прокатывают. Чтобы волочение медной проволоки было выполнено максимально качественно, с поверхности заготовки необходимо удалить оксидную пленку, для чего ее обрабатывают раствором кислоты.
Намотка готовой проволоки на барабан
Сам процесс волочения мало чем отличается от производства сварочной проволоки (или любой другой). Проволочный стан в таком случае тянет заготовку, пропуская ее через фильерные отверстия определенного диаметра. Для изготовления медной проволоки очень небольшого диаметра (до 10 мкм) ее формирование может осуществляться в специальном смазочном составе (погружной метод). В качестве таких составов, в частности, могут использоваться:
- комплексные растворы;
- специальные эмульсии;
- комплексные вещества.
Использование таких составов, через которые проволока проходит в процессе своего формирования, позволяет получать изделия, наружная поверхность которых отличается максимальной чистотой.
Оценка статьи:
Загрузка…Поделиться с друзьями:
Катанка и проволока — производство и использование
Проволока — один из самых востребованных видов изделий из металла. Она может быть стальной, медной, титановой, из алюминия, цинка, никеля и их сплавов. Бывают и биметаллические и полиметаллические проволоки. Без проволоки невозможно представить себе электротехнику — но не только.
Стальная проволока нужна и при производстве пружин, гвоздей электродов, свёрл. Хотя для таких целей используется даже не сама проволока, а ее полуфабрикат — стальная катанка. Посмотрим, как ее, а потом и проволоку, производят из цельной стали.Собственно, изготавливают катанку так же, как и всякий иной прокат: заготовку в виде бруска (блюма) раскаляют до состояния «красной мягкости», а затем пропускают через вальцы, которые вытягивают горячий металл в катанку с сечением до 10 мм. — и далее поступает на мотальный станок, где и укладывается кольцами.
Ответственное охлаждение
После этого наступает этап охлаждения катанки. Оно может быть естественным (в этом случае катанка получает маркировку ВО) и ускоренное (маркировка УО).
Естественное охлаждение дает более мягкую и пластичную катанку (а затем и проволоку), а ускоренное — более жесткой и упругой. Ускорить охлаждение катанки могут промышленные установки-вентиляторы или потоки воды. При первом способе охлаждения в маркировке катанки будет указываться УО1, а при втором – УО2.
Ускоренно охлажденную катанку (предназначенную для производства проволоки в дальнейшем) зачищают от окалины, которой на катанке УО1 не должно быть более 18 килограмм на тонну, а для катанки УО2 – не более 10 кг/т. Окалина удаляется либо механическим путем (тогда катанка пропускается через специальный станок-окалиноломатель), либо химическим, когда поверхность катанки протравливают раствором серной кислоты с добавлением поваренной соли, тринатрийфосфата и др. добавок.
Химический способ дает более ровную поверхность, но он же чреват приобретением металлом т.н. «травильной хрупкости». Механический способ в этом отношении безопасен, поскольку — но он менее надежен и выдает шероховатую поверхность.
Гвозди, болты и ГОСТы
Какой же из способов очистки катанки лучше? Это зависит от того, что из нее собираются делать.
Для гвоздей требуется заготовка с гладкой поверхностью, а для изготовления арматуры, электродов или болтов подойдет и шероховатая.
Кроме того, на поверхности катанки, предназначенной для производства проволоки, могут образовываться специфические дефекты — заусенцы либо закаты. Заусенцы — это выпуклости, которые при дальнейших операциях будут сдираться и «закатываться» (отсюда и название другого дефекта — закаты).
Плохо влияют на свойства металла в катанке заварившиеся пузыри – волосовины — и «усадочные раковины», которые возникают, если перед прокаткой металл был нагрет слишком сильно и оттого утратил часть углерода, «выгоревшего» при прокаливании.
Для проверки качества катанку подвергают испытаниям, главным из которых является проверка эластичности. Качественная катанка может спокойно выдерживать изгиб на 180 градусов вокруг штырька, имеющего такой же диаметр, как и у подвергаемой испытанию катанки. Более подробно ознакомиться с требованиями, предъявляемыми к такому металлопрокату, можно в ГОСТе 30136–95.
В этом ГОСТе диаметры катанки в 5, 5,5, 6, 6,3, 6,5, 7, 8 и 9 мм определены как стандартные и обязательные к изготовлению для всех производителей. По желанию заказчика металлургические предприятия могут производить катанку с сечением и больше 9 мм, но такие заказы бывают довольно редко.
В силу технологических особенностей дешевле всего обходится производство катанки диаметром 8 мм – она и пользуется наибольшим спросом. Добавляет «калибру» 8 мм. и удобство расчетов:
-один метр катанки диаметром 8 мм. имеет массу около 400 г. (395 г., если быть точным),
—в тонне такой катанки будет 2531 метр (то есть 2,5 километра «с небольшим запасом»).
Это очень удобные цифры — их легко запомнить, не надо заглядывать в специальные таблицы.
Поставка и маркировка
Готовая катанка сматывается в бухты весом не менее 160 кг. Обычно каждая бухта представляет собой сплошной отрезок, который маркируется по требованиям ГОСТ 7566. На каждый моток крепится маркировочная метка, в которой указывается завод-изготовитель, диаметр катанки, сорт и марка стали, номер плавки. Тем не менее, допускается сматывание в одну бухту и двух отрезков катанки – но если только один отрезок не будет больше 10% от массы мотка. При этом производитель должен гарантировать свариваемость изделий и поставить два маркировочных ярлыка – по одному на каждый отрезок.
По техническим условиям ТУ 14-15-254-91 катанка по ТУ изготавливается 4-х классов:
класс ВК — катанка канатная высококачественная;
класс ВД — катанка высокой деформированности;
класс КК-катанка канатная качественная;
класс ПД — катанка конструкционная.
Катанка в деле и производстве
Катанка считается полуфабрикатом, но довольно широко используется и сама по себе. Стальная катанка служит средством крепления при перевозке по железной дороге крупногабаритных грузов. Ей же скрепляют несущие элементы конструкций и армируют железобетон (для этого очень хорошо подходит самая дешевая 8-миллиметровая катанка). Продукцию толщиной 6,5 мм используют для упрочения кирпичной кладки, устройства громоотводов и изготовления тросов, применяемых при строительстве вантовых мостов. Однако главное назначение катанки – все-таки роль промежуточного полуфабриката при производстве гвоздей, сварочных электродов, намотки пружин — и, разумеется, производстве проволоки.
Производство проволоки
Технология превращения катанки в проволоку на первый взгляд особой хитрости не представляет: металл заготовки последовательно протаскивают (проволакивают) через все более узкие глазки (волоки) – до тех пор, пока не будет достигнут необходимый малый диаметр проволоки.
Однако на самом деле волочение требует нескольких этапов, а именно:
— травление полуфабриката (катанки) в 50% растворе серной кислоты при температуре около 50 градусов очистки от окалины;
— предварительный отжиг металла, который производится для придания металлу мелкозернистой структуры;
— нейтрализация сернокислого раствора и промывка заготовок;
— утончение концов катанки при помощи молота или специальных валков;
— производство самого волочения;
— выполнение финального отжига.
Само волочение может быть :
— однократным, если заготовка протягивается через одну волоку, после чего накручивается на барабан и снимается.
— многократным, когда проволока протягивается последовательно через несколько волок, которых может быть до 15 и более. Такая технология уменьшает время, которое затрачивается на производство проволоки, обеспечивает высокую производительность и постоянство условий обработки (которые могут сильно нарушаться при повторении однократных волочений).
Но при всех достоинствах многократного волочения на заводах применяют сдвоенные волоки. При этом они при работе нагреваются от трения нагреваются до столь сильно, что нуждаются в системе охлаждения, для которой обычно используется водный раствор мыла, который одновременно является и смазкой.
Однако на самом деле волочение – это только половина дела. При этом процессе металл подвергается огромным нагрузкам на растяжение, в результате чего его кристаллическая решетка деформируется, а внутренние напряжения накапливаются. Полученная таким путем проволока получается малопластичной, приобретает хрупкость, плохо гнется и легко ломается.
И чем больше удлиняется катанка при волочении – тем сильнее проявляются эти неприятные эффекты.
Поэтому важным этапом в изготовлении проволоки является ее повторная термообработка – отжиг, который должен восстановить кристаллическую решетку и снять перенапряжения в металле. Для этого требуется уже протянутую проволоку нагреть и медленно охладить.
Существует два вида отжига, применяемых в производстве проволоки:
светлый – он производится в колпаковых печах в атмосфере из какого-то инертного газа. Поверхность полученной этим способом проволоки будет чистой, безо всякой окалины, но и цена продукции – более высокой. В маркировке этот вид термообработки будет обозначен литерой «С»;
темный – он происходит в присутствии кислорода, отчего проволока покрывается слоем окислов и окалиной. Наличие окалины плохо влияет на товарный вид, проволока пачкается, но на ее рабочие качества это не влияет никак – зато обходится «темный» вариант отжига гораздо дешевле. Проволока после такой обработки маркируется буквой «Ч».
Отожженные изделия приобретают пластичность и становятся удобны при плетении различных видов сеток.
Видео по теме:
Производство алюминиевой проволоки – виды и характеристики
Алюминиевая проволока представляет собой длинномерное металлоизделие с круглым сечением малого размера. Производство алюминиевой проволоки востребованное. Изделия используют в пищевой, мебельной промышленности, приборостроении, машиностроении, в строительстве при проведении сварочных работ, для прокладки кабелей электролиний.
Свойства проволоки из алюминия
Алюминий – универсальный материал, которому присущи такие характеристики:
- малый вес;
- гибкость;
- прочность;
- влагоустойчивостью;
- хорошая износостойкость;
- температура плавления 660 0C;
- стойкость к агрессивным средам;
- слабые магнитные свойства;
- биологическая инертность;
- долговечность.
По сравнению с другими видами аналогичных изделий, алюминиевая проволока имеет много преимуществ. Материал устойчивый к коррозии, поэтому его применяют там, где объекты контактируют с водой. Технический алюминий легко поддается обработке. Он обладает электро- и теплопроводностью. Металл безопасный в использовании, так как соответствует необходимым санитарно-техническим требованиям.
Для изготовления профиля используют чистый алюминий разных марок и его деформируемые сплавы в виде слитков или катанки. Свойства изделия зависят от химического состава и способа производства. Диаметр готовой продукции варьируется от 0,08 до 10 мм.
Виды и марки проволоки из алюминия
Производство длинномерных алюминиевых изделий регламентируется стандартами ГОСТ. Длинномерный профиль из алюминия имеет разную классификацию, основанную на эксплуатационных характеристиках.
По химическому составу стали:
- низкоуглеродистая — с массой углерода до или выше 0,25%;
- легированная;
- высоколегированная;
- на основе особых сплавов.
По форме сечения:
- круглая, овальная;
- квадратная, прямоугольная;
- трапециевидная;
- многогранная;
- сегментная;
- клиновидная;
- зето- и иксообразная;
- периодического, специального, фасонного профиля.
По виду поверхности:
- полированная;
- шлифованная;
- травленная;
- с металлическим или неметаллическим покрытием;
- светлая;
- черная.
Каждому специалисту известно понятие «марка металла». Расшифровка символов дает сведения о химическом составе и физических свойствах материала. Сплавы маркируют буквами и цифрами, по которым определяют состав химических элементов и их количество. В соответствии с ГОСТ круглую проволоку обозначают таким образом:
- Твердая – АТ.
- Полутвердая – АПТ.
- Мягкая – АМ.
- Повышенной прочности – АТп.
По ГОСТ 14838-78 производят изделия для холодной высадки на основе технического алюминия или его сплавов. ГОСТ 7871-75 позволяет изготавливать проволоку для сварки. ГОСТ 4784-97 регулирует химический состав продукции. Согласно ГОСТ 24231-80, проводят пробы с целью определить содержание компонентов металла.
Особенности производства алюминиевой проволоки
Основой для изготовления проволоки является катанка алюминиевая диаметром от 9 до 14 мм. Ее получают тремя способами.

Схема получения проволоки
Прокаткой, если в качестве исходного сырья имеются алюминиевые слитки. Для этого используют проволочно-прокатный стан. Это комплекс автоматизированных механизмов, оснащенный нагревательными печами с электрическим, газовым или нефтяным обогревом.
Методом непрерывного литья и проката, если сырье представлено в виде расплавленного алюминия. Это передовой способ, который предполагает загрузку жидкой массы в кристаллизатор. Специальное вращающееся колесо с вырезом на ободе охлаждается водой. Во время движения металл кристаллизуется и передается на прокатные валки. Готовую продукцию сворачивают в катушки, помещают в полиэтиленовые пакеты.
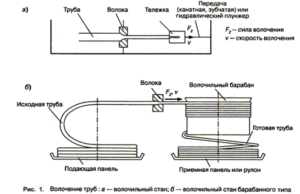
Холодное волочение алюминиевой проволоки
На некоторых заводах, оснащенных гидравлическими прессами, электротехническую катанку изготавливают методом прессования. Нагретый слиток помещают в специальный контейнер с матрицей. На ней есть отверстие, соответствующее форме сечения изделия. Обработка давлением происходит за счет пуансона со сменной прессшайбой, которая плотно заходит в пространство контейнера.
Последний способ подходит для изготовления сложных профилей разного сечения, прутков, гладких и ребристых труб диаметром до 400 мм. Прессованная продукция, в отличие от литой, может выпускаться в виде прямолинейных отрезков от 1 до 2,5 метра.
Предварительная обработка
Чтобы алюминиевая проволока на выходе приобрела нужные свойства, ее подвергают предварительной обработке:

Закалка и старение алюминиевых сплавов сплавов
- Для крепости изделий из неупрочняемых сплавов применяют холодную деформацию. Это характерно для марок АД1, АМг3, АМг5.
- Термоупрочняемые сплавы подвергают закалке и старению: Д1П, Д16П, Д18.
- Для достижения пластичности проволоку отжигают.
- На завершающей стадии изготовления изделий с помощью специального инструмента проводится абразивная обработка. Она помогает удалить заусеницы и закруглить ребра металлического шнура.
Метод волочения
Алюминиевая проволока получается из катанки методом волочения. Заготовку диаметром от 7 до 20 мм протягивают через несколько отверстий – волок. Их размер намного меньше, чем сечение проволоки. Поскольку при горячей прокатке металл покрывается безвредной окисной пленкой, его не подвергают процедуре травления. Если катанка алюминиевая хранится долгое время, слой окислов необходимо стравливать. Для этого металл погружают в водный раствор серной кислоты.
Изготовление изделий проводят по такой схеме:

Современное производство проволоки
- Алюминий при помощи загрузчика подают в плавильную печь с рабочей температурой 700–800 0C.
- Расплавленную массу пропускают через фильеру с целью получения литой заготовки диаметром до 3,5 мм.
- Обрабатываемый материал охлаждают, кладут на индивидуальный компенсатор.
- Волочение катанки осуществляют на многократных станках без скольжения с применением густой смазки.
- С компенсатора заготовка поступает в волочильное устройство.
- Волочение заготовок меньшего диаметра производят на агрегатах со скоростью 18м/сек. и скольжением.
- Технологический процесс предполагает использованием мыльно-масляной эмульсии.
- При многократно повторяющемся волочении величину вытяжек делают на 5% меньше, чем для меди. Это снижает вероятность обрывов проволоки.
Области применения алюминиевой проволоки
Длинномерная нить из алюминия нашла широкое применение в разных сферах человеческой деятельности.

Применение алюминиевой проволоки
Круглую проволоку используют в качестве сварочного материала при ручной, дуговой, аргонной и автоматической сварке. Шов из алюминия защищает предмет от коррозии и термической деформации. При минимальном весе металл обеспечивает прочность конструкций. Данные виды работ характерны для строительства, судо-, машино- и авиастроения.
Длинномерный алюминиевый шнур является универсальным крепежным материалом. Его задействуют при изготовлении мебели. Пружины, сетки, фурнитура, заклепки, декоративные детали из алюминия – это далеко не весь перечень полезных предметов из катаного алюминия.
Пищевая промышленность: сырное и колбасное производство.
Проволока тесно связана с электротехнической промышленностью. Это антенны, разные виды кабелей и проводов для прокладки линий электропередачи, электроды, коммуникации. Из проволоки изготавливают метизы, сверла, пружины, электроды.
Металлическая нить незаменима в производстве деталей для оборудования химической промышленности и высокотехнологичных приборов.

Алюминий используется в очень большом количестве различных отраслей
Алюминиевую ленту применяют в различных отраслях современного народного хозяйства: для сварки, электропроводки, сооружения конструкций, которые контактируют с влажной средой.
Проволоку используют для изготовления декоративных предметов, сувениров, украшений, которые могут быть отдельными вещами или частью интерьера. Плетение из проволоки является современным видом творчества.
Длинномерный материал нашел применение в ландшафтном дизайне, при изготовлении беседок, скамеек, оград.
Проволока из алюминия обладает уникальными техническими характеристиками. Это многофункциональный металл, который помогает реализовать инновационные проекты в науке и технике.
Видео по теме: Станок для волочения проволоки СВ 6
Технологический процесс изготовления проволоки из цветных металлов и сплавов :: Технология металлов
- ОБЩИЕ СВЕДЕНИЯ
Технологический процесс изготовления проволоки — это ряд последовательных операций (травление, термообработка, волочение и другие), при осуществлении которых происходит уменьшение сечения заготовки и достигаются необходимые свойства проволоки.
Качество изделия и экономические показатели производства проволоки зависят от технического уровня процесса. Важным условием снижения трудовых затрат в производстве проволоки является сокращение циклов. Это достигают путем волочения проволоки с максимально возможными суммарными обжатиями (табл. 1).
Таблица 1
Допустимые суммарные обжатия
Сплав или металл | Максимальное суммарное обжатие, % | Сплав или металл | Максимальное суммарное обжатие, % |
Медь M1 | 99,9 | Константан | 99 |
Л80 | 95—99 | Никель | 99 |
Л62 | 80—96 | Алюмель | 80-90 |
ЛС 59-1 | 40—50 | Хромель | 80—90 |
БрБ-2 | 35-85 | Монель-металл | 80-95 |
БрКМцЗ-1 | 80—90 | Алюминий | 99,9 |
БрОЦ4-3
| 80—99 | Цинк | 99,9 |
Манганин
| 99 | Титан (ВТ1) | 45-60 |
Они зависят главным образом от пластичности металла и диаметра обрабатываемой проволоки. Чем меньше диаметр, тем больше допустимое суммарное обжатие. Например, при волочении проволоки бериллиевой бронзы из катанки 7,2 мм в начале процесса до размера 4,5 мм допускаются обжатия между отжигами, равные 30—40%, а из заготовки диаметром 1,0—0,5 мм волочение ведется с суммарным обжатием 75—85%.
Важным фактором, определяющим технологию производства проволоки, является заготовка и способ ее получения. От диаметра заготовки, ее качества зависит трудоемкость производства и качество проволоки.
2. ЗАГОТОВКА ДЛЯ ПРОВОЛОКИ
Заготовку для изготовления проволоки получают следующими способами:
1. Прокаткой слитков на проволочно-прокатном стане до диаметра 6,5—19 мм. Этот способ является наиболее производительным и широко используется для получения заготовки из меди, медных сплавов, алюминия, никеля, никелевых и медно-никелевых сплавов, латуней (Л62, Л68, ЛА85-0,5), цинка, бронз (ОЦ4-3, КМЦ-3-1, ББ2), титана и титановых сплавов.
2. Горячим прессованием на гидравлических прессах. Этим способом можно получить заготовку диаметром 5,5—20 мм и выше с высоким качеством поверхности. Однако этот метод менее производителен, чем прокатка, и связан с получением значительных геометрических отходов — от 10 до 25%. В то же время при прокатке эти отходы составляют 2—4%. Прессованием получают заготовку из сплавов, сортовая прокатка которых затруднена, например латуни ЛС59-1, ЛС63-3 и др., а также при необходимости получения проволоки с высоким качеством поверхности и сложным профилем.
3. Разрезкой холоднокатаных дисков по спирали специальными ножницами на прямоугольную заготовку (например, размером 6×8 мм). Этот способ применяется для сплавов, не выдерживающих горячей деформации. К таким сплавам относится фосфористая бронза.
4. Металлокерамическим способом — путем спекания порошков в длинные прямоугольные заготовки и последующей ковки их на ротационно-ковочных машинах. Этот способ применяется для тугоплавких металлов (молибден, вольфрам и др.).
3. ИЗГОТОВЛЕНИЕ ПРОВОЛОКИ ИЗ МЕДИ
Заготовкой для волочения медной проволоки служит катанка диаметром 7,2—19 мм или прямоугольного сечения. Для изготовления проволоки сложного профиля применяется прессованная заготовка соответствующего профиля. Заготовку травят в 8—12%-ном водном растворе серной кислоты, подогретом до 40—50 °С. Волочение катанки диаметром 7,2 мм, предварительно сваренной встык, производят на машинах со скольжением типа ВМ-13 на размер 1,79—1,5 мм. Для смазки и охлаждения применяется мыльно-масляная эмульсия. Далее волочение ведут на 22-кратной машине на размер 0,38—0,2 мм, скорость волочения до 18 м/сек. Затем волочение на 18-кратных машинах на диаметры 0,15—0,05 мм. На последнем переделе волочения применяют алмазные волоки. Угол рабочего конуса волок 16—18°.
Проволоку диаметром 0,15—0,05 мм изготавливают без промежуточного отжига. При необходимости проводится безокислительный отжиг, как правило, на готовых размерах в конвейерных электропечах с водяным затвором или в шахтных электропечах без доступа воздуха.
На некоторых заводах кабельной промышленности эксплуатируются волочильные машины с совмещенным отжигом медной проволоки. Применение таких машин позволяет снизить трудоемкость изготовления проволоки и повысить степень автоматизации производства. В настоящее время работают над улучшением качества отжига проволоки на этих машинах.
4. ИЗГОТОВЛЕНИЕ ПРОВОЛОКИ ИЗ АЛЮМИНИЯ
Алюминиевую проволоку изготавливают из катаной заготовки диаметром 7—19 мм. При горячей прокатке алюминий покрывается очень тонким слоем окислов, влияние которого на процесс волочения незначителен, поэтому горячекатаную заготовку обычно не травят. Но при длительном хранении на металле образуется слой окислов, который рекомендуется стравливать. В этом случае производят травление в водном растворе, содержащем 8—12% H2SO4 .
Изготовление алюминиевой проволоки средних и тонких размеров проводится по следующей схеме.
Волочение катанки диаметром 7,2 мм на 1,8 мм осуществляется на многократных машинах без скольжения типа ВМА-10/450. Далее волочение на размер 0,47—0,59 мм проводится на 15 волочильных машинах со скольжением; скорость волочения до 18 м/сек.
На машинах без скольжения применяется густая смазка, на машинах со скольжением — мыльно-масляная эмульсия.
При многократном волочении алюминиевой проволоки в целях снижения обрывности принимают величину вытяжек на 5% ниже, чем для меди. Волоки применяются с углом рабочего конуса, равным 24—26°.
5. ИЗГОТОВЛЕНИЕ ПРОВОЛОКИ ИЗ ЦИНКА
Цинковая проволока изготавливается из цинка марок ЦО и Ц1. Заготовкой для волочения служит катанка диаметром 7,2 мм, ее протягивают на размер 3,7 мм на 6-кратной машине со скольжением типа 6/480. Смазкой служит мыльно-масляная эмульсия, приготовленная из пасты Ц4 с добавкой серного цвета. Далее волочение на машинах со скольжением типа 8/250, 10/250 с диаметра 3,7 мм на готовые размеры 1,5—2 мм. Смазка та же, что и для предыдущего передела волочения. При волочении цинковой проволоки особое внимание должно уделяться подготовке смазки и волок. Для снижения усилий на преодоление трения рекомендуется уменьшить площадь контактирования проволоки в очаге деформации, для чего угол рабочего конуса волоки увеличивают до 24—26°, а длину рабочего пояска уменьшают до 0,3 диаметра готовой проволоки.
Цинковую катанку обычно не подвергают травлению, так как тонкий слой окислов, покрывающий ее, не оказывает влияния на процесс волочения.
6. ИЗГОТОВЛЕНИЕ ПРОВОЛОКИ ИЗ ТИТАНА
Заготовкой для волочения проволоки из титана служит катанка диаметром 8 мм. Волочение ведут на однократных или многократных машинах без скольжения в твердосплавные металлокерамические волоки. Для смазки применяют сухой порошкообразный графит. Скорость волочения от 20 до 50 м/мин. Допустимые суммарные обжатия при волочении проволоки из титана марки ВТ1 — от 45 до 60%. После такой деформации проводится отжиг в электропечах при температуре 620—640°С, выдержка при данной температуре 20 мин.
Отожженные бухты проволоки погружают в соляноизвестковый раствор следующего состава: 100—150г/л гашеной извести (СаО) и 80—100 г/л поваренной соли (NaCl). Температура раствора 80—90 °С. После обработки в растворе бухты просушивают в токе теплого воздуха. Полученный на поверхности проволоки известковый слой способствует лучшему захвату сухого порошкообразного графита.
Готовую проволоку травят для снятия альфированного слоя. После травления проволоку подвергают вакуумному отжигу для повышения пластичности и снижения содержания водорода. Температура отжига 750— 800 °С, время выдержки 4—6 ч, охлаждение в печи до 250 °С. В печи поддерживается вакуум от 13,3 до 6,65 мн/м2 (от 1 · 10-4 до 5 10-5 мм рт. ст.).
По указанной технологии изготавливается проволока из титана марки BT1 диаметром от 1,2 до 7 мм. Волочение ведут в твердосплавные металлокерамические волоки с углом рабочего конуса 8—10°.
Проволоку из титановых сплавов изготавливают по этой же технологии, но с большим количеством промежуточных отжигов, так как допустимое суммарное обжатие при обработке сплавов снижается до 30—40%.
7. ИЗГОТОВЛЕНИЕ ПРОВОЛОКИ ИЗ НИКЕЛЯ И ЕГО СПЛАВОВ
Проволоку из никеля и его сплавов изготавливают из катаной заготовки. Поверхность катанки из никелевых сплавов и заготовка после отжига имеют весьма плотную окисную пленку, препятствующую процессу волочения, поэтому в производстве проволоки особое внимание уделяется подготовке поверхности. С этой целью применяется комбинированное щелочно-кислотное и кислотно-солевое травление, известково-солевое покрытие поверхности заготовки .
Волочение проволоки из никелевых и медно-никелевых сплавов, обладающих высокой твердостью и прочностью, связано с повышенным износом волок, поэтому в процессе производства этой проволоки вопросу стойкости волок также уделяется большое внимание. С этой целью повышается качество подготовки поверхности металла, подготовки волок и смазки, внедряется волочение проволоки в условиях жидкостного трения. В настоящее время волочение проволоки из никеля, кремнистого никеля, никеля марганцовистого, константана, хромеля на многократных машинах без скольжения ведется в так называемые сборные волоки , создающие условия жидкостного трения.
Проволоку из никеля и его сплавов отжигают в электропечах шахтного типа без доступа воздуха, а также в протяжных электропечах. Для получения светлой поверхности рекомендуется вести отжиг в среде генераторного газа, диссоциированного и неполностью сожженного аммиака, содержащего 5% водорода, или в чистом осушенном водороде. Отжиг термоэлектродной проволоки на готовых размерах ведется в окислительной среде для получения надежной окисной пленки, которая в значительной мере определяет свойства проволоки (стабильность т. э. д. с).
8. ИЗГОТОВЛЕНИЕ ПРОВОЛОКИ ИЗ ВОЛЬФРАМА
Заготовкой для вольфрамовой проволоки служат вольфрамовые штабики квадратного сечения 15X 15 мм, длиной около 0,5 м, полученные металлокерамическим способом.
Перед волочением штабики проковывают на ротационно-ковочных машинах на диаметр 2,5—3,0 мм. Кованую заготовку протягивают на диаметр 1 мм на цепных волочильных станах длиной до 30 м. Волочение горячее, для чего стан оборудован газовой печью. Перед задачей в волоку конец прутка заостряют путем нагрева до вишнево-красного цвета и погружения в коробку с сухим азотнокислым калием или натрием. Под действием высокой температуры соль растворяется и равномерно растворяет концы вольфрамовых прутков на длине 100—120 мм. Следует избегать попадания азотнокислого калия или натрия в канал волоки во избежание его порчи. После заострения с конца прутка смывают остатки азотнокислого калия или натрия водой и смазывают его коллоидно-графитовым препаратом марки B-1. Заостренный конец нагревают в печи и затягивают в волоку на длину до 200 мм. Затем конец прутка прогревают вместе с волокой, быстро устанавливают в волокодержатель и протягивают.
Волочение ведется на скорости 0,1—0,15 м/сек. Волоки твердосплавные с углом рабочего конуса 8—10 град. Перед волочением волоку нагревают до температуры 500 °С, а проволоку до 1000—850 °С в зависимости от диаметра (с уменьшением диаметра снижается температура).
Таким образом процесс повторяют 7—8 раз до диаметра 1 мм, после чего проволоку сворачивают в моток.
Далее волочение на размер 0,5—0,55 ведут на однократных волочильных машинах в 6 протяжек. С фигурки проволока проходит через смазочную коробку с коллоидно-графитовым препаратом марки В-1, разбавленным дистиллированной водой в соотношении 1:1, попадает в газовую печь, где нагревается до температуры 800—750 °С, протягивается в победитовую волоку со скоростью 0,16—0,20 м/сек и принимается на барабан диаметром 500 мм.
Волочение на более тонкие размеры проводится по этой же схеме с приемом проволоки на барабаны диаметром 200 мм или на катушки. Скорость волочения до 0,3—0,4 м/сек. Для смазки применяют препарат марки В-1, разбавленный дистиллированной водой в соотношении 1 : 2. Волочение проволоки диаметром 0,34—0,32 мм и ниже ведется в алмазные волоки типа Т, которые нагревают перед волочением до 400 °С.
9. ИЗГОТОВЛЕНИЕ ПРОВОЛОКИ ИЗ БЛАГОРОДНЫХ И РЕДКИХ МЕТАЛЛОВ
Для изготовления проволоки из серебра применяют катаную или прессованную заготовку диаметром 7—8 мм. Волочение заготовки ведут без промежуточного отжига до размера 0,26 мм по следующей схеме. До диаметра 3—3,5 мм применяют однократное волочение. В качестве смазки используют хозяйственное мыло. Волочение на этом переделе можно вести на многократных волочильных машинах со скольжением типа ВМ-13 или СМВ-П-9. Волочение до размера 1,2 мм ведут на 15-кратной машине со скольжением типа 15/250, затем на машине типа 22/200 до диаметра 0,26 мм. На этом размере проводится отжиг в камерной электропечи при температуре 250 °С, выдержка 30 мин.
Дальнейшее волочение на тончайшие размеры до 0,02 мм проводится на 18 волочильных машинах со скольжением без промежуточного отжига. На машинах со скольжением смазкой служит мыльная эмульсия. Волоки твердосплавные металлокерамические с углом рабочего конуса 16—18 град. Для тончайшего волочения применяют алмазные волоки типа М.
В процессе обработки серебряной проволоки заготовка и промежуточные размеры после отжига травлению не подвергаются. Особое внимание уделяется чистоте рабочего места, качеству поверхности проволоки, подготовке производства с целью исключения обрывности и потерь металла.
Для получения проволоки тончайших диаметров (до 0,001 мм) из золота, платины и сплавов благородных металлов применяют волочение в медной рубашке, для чего пруток из благородных металлов или сплавов диаметром до 2 мм закладывают в .медную трубку диаметром 10 мм и с толщиной стенки 4 мм. Такую биметаллическую заготовку подвергают волочению до расчетного размера.
Так, для получения платиновой проволоки диаметром 0,01 мм волочение биметаллической заготовки ведут до диаметра 0,05 мм, для получения диаметра 0,005 мм — волочение до 0,025 мм, для диаметра 0,004 мм — волочение до 0,02 мм и т. д. Перед применением проволоки из благородных металлов с нее стравливают верхний слой металла (медную рубашку) раствором азотной кислоты в дистиллированной воде в соотношении 1:1.
Проволоку из бериллия и его сплавов диаметром от 1 до 0,12 мм производят волочением при температурах 420—450 °С. Обжатие за проход составляет 25%. В качестве смазки используют коллоидный графит в масле, а также смесь графита с дисульфидом молибдена. После каждого третьего прохода проволоку подвергают промежуточному отжигу при 800 °С в течение 6 ч 30 мин. Очистку поверхности проволоки производят ультразвуковым методом, так как травление снижает ее механические свойства.
10. ИЗГОТОВЛЕНИЕ ПРОВОЛОКИ ИЗ ЛАТУНЕЙ
Пластичность латуней ниже пластичности меди, поэтому в процессе обработки они быстрее нагартовываются и требуются промежуточные отжиги. По пластичности латуни можно условно разделить на три группы: 1) пластичные латуни, содержащие выше 78—80% меди. К ним относятся латуни Л80, ЛА85-0,5, Л90 и др.; 2) латуни средней пластичности, содержащие 60—70% меди. К ним можно отнести Л62, Л68; 3) латуни низкой пластичности. К ним относятся латуни марок ЛС59-1, ЛО60-1.
Изготовление проволоки толстых и средних размеров из латуней первой группы можно вести без промежуточного отжига; тонких размеров—с одним промежуточным отжигом и тончайших—с двумя отжигами.
Из латуней второй группы изготовление проволоки толстых размеров ведется без промежуточных отжигов; средних размеров— с одним и двумя промежуточными отжигами; тонких размеров — с тремя отжигами и тончайших — с четырьмя промежуточными отжигами.
Проволока из латуней третьей группы диаметром выше 5 мм производится из прессованной заготовки соответствующего диаметра без промежуточных отжигов. Проволоку диаметром ниже 5 мм изготовляют с промежуточными отжигами через каждые 30—40% обжатия.
С улучшением технологии подготовки поверхности металла перед волочением, повышением качества волочильного инструмента и смазки, а также улучшением качества заготовки суммарные обжатия при волочении латунной проволоки могут быть повышены и, следовательно, сокращено количество промежуточных отжигов.
В связи с большой градацией латунной проволоки по механическим свойствам термическая обработка в технологическом процессе ряда марок латунной проволоки (Л62, Л68 и др.) имеет важное значение, определяющее качество проволоки (механические свойства) и условия ее дальнейшей обработки. В процессе производства латунной проволоки особое внимание должно уделяться отжигу, с точки зрения его равномерности, и подготовке поверхности проволоки после отжига для дальнейшей обработки. Многократное волочение латунной проволоки средних и тонких диаметров ведется с частными обжатиями 17—18%. Желательно работать на меньших обжатиях, если позволяет машина.
Травление заготовки проволоки и промежуточных размеров после отжига проводится в 5—15%-ном водном растворе серной кислоты. Удовлетворительное качество травления латунной проволоки получается при условии погружения ее в раствор на приспособлении, обеспечивающем равномерное травление каждой бухты .
Для получения светлой поверхности проволоки после отжига в отдельных случая проводится травление в растворе, содержащем 2 ч. серной кислоты, 1 ч. азотной кислоты и 6 ч. воды с последующим пассивированием в водном растворе, содержащем 150 г/л хромпика и 400—450 г/л серной кислоты. После пассивирования производится нейтрализация в щелочном растворе. Латунная проволока отжигается в шахтных электропечах без доступа воздуха и в протяжных электропечах.
Наиболее равномерный отжиг получается в протяжных электропечах, а также в шахтных электропечах с принудительной циркуляцией воздуха. Хорошие результаты по равномерности отжига проволоки Л62 получены в шахтных электропечах колодцевого типа, оборудованных автоматическим регулированием температур по зонам с учетом тепловой инерции печи. При этом достигнуты узкие пределы механических свойств проволоки в одной партии: предел прочности от 400 до 460 Мн/м2 (40— 46 кгс/мм2), а в одном мотке колебания не превышают 30 Мн/м2 (3 кгс/мм2) (проволока была изготовлена из латуни марки Л62 с содержанием меди 62—63%).
Для волочения латунной проволоки применяют твердосплавные металлокерамические волоки с углом рабочего конуса 14— 18 град. Проволоку диаметром ниже 0,2 мм протягивают в алмазные волоки типа П.
Источник:
Хаяк Г.С. Волочение проволоки из цветных металлов и сплавов,Металлургия, 1967.
Технология производства стальной проволоки
1.Влияние химических элементов на качество сырья.
Материалом для стальной проволоки является катанка. Для изготовления используют стали,выплавленные в мартеновских и электропечах и конверторах.
— катанка должна иметь постоянный хим. состав и однородную структуру по всей длине.
— поперечное сечение должно быть точным по форме и размерам.
1.Влияние отдельных элементов на качество.
Углерод — придает стали повышенную прочность и определенный уровень пластичности, повышает упругость, износостойкость и выносливость при переменных нагрузках.
Марганец и кремний — раскисляют сталь при выплавке. Они повышают плотность и однородность металла, упрочняют его, делают более упругим, повышают сопротивление истиранию. Марганец нейтрализует вредное действие серы в стали, образуя с ней соединения. Если кремний находится в виде скоплений окислов, то уменьшает пластичность стали.
Сера и фосфор — вредные примеси. Они склонны к ликвации — способны скапливаться в отдельных частях. Повышенное содержание серы вызывает в стали красноломкость (хрупкость при высоких температурах). Содержание серы и фосфора ограничивается в стали до 0,03 % каждого и в сумме до 0,05 %.
Хром — попадает в углеродистую сталь, как правило, из шихты при выплавке в печах. При патентировании хром оказывает вредное действие, поэтому его содержание ограничивается до 0,1-0,15%.
Никель — при небольших содержаниях его в углеродистой стали не оказывает вредного действия, не задерживает процесс патентирования.
Неметаллические включения — относятся к деффектам. Они ухудшают механические свойства.
Азот — вызывает деформационное старение, т.е. повышает твердость, хрупкость с течением времени.
2.Деффекты и другие недостатки сырья(катанки).
Деффекты катанки существенно влияют на качество готовой проволоки.
Заусенцы и закаты — заусенец (ус) имеет вид выпуклости, тянущейся по длине катанки. Если заусенец появился в подготовительном калибре,то в последующих переходах он закатывается в закат.
Катанка с заусенцем и закатом не пригодна для производства проволоки.
Волосовины — вытянувшиеся по направлению прокатки не заварившиеся пузыри, также снижают механические свойства металла.
Усадочные раковины и рыхлость — эти деффекты ослабляют сечение проволоки, приводят их к обрывам, понижают механические свойства.
Обезуглероживание — происходит при нагреве слитков под прокатку, поверхность обедняется углеродом. Обезуглероживание очень вредно в катанке для канатной проволоки.
Неправильная форма катанки и неточные размеры сечения (овал)- овальное сечение и отклонение сечения от формы круга приводит к неравномерной деформации заготовки в процессе волочения. Из-за этого ухудшаются механические свойства проволоки и на ее поверхности возникают трещины.
Неудовлетворительная структура. В тех. условиях на катанку оговариваются требования к микроструктуре — она не должна иметь следов усадочной раковины, рыхлости, ликвации углерода, не допускаются мартенситные участки.
Удовлетворительной структурой в катанке является сорбит, образующийся в результате интенсивного охлаждения после прокатки катанки. Такая структура облегчает условия волочения катанки и удешевляет производство проволоки.
Перепутывание плавок (марок)- приводит к резкому ухудшению качества проволоки,расстройству технологического процесса производства проволоки, дополнительных затрат на ликвидацию создавшегося положения при переработке катанки.
Для производства стальной среднеуглеродистой и высокоуглеродистой проволоки используются стали с содержанием углерода 0,5 до в 0,85%, т.е. марки 50 — 85.
Двухзначные числа в марках стали обозначают среднее содержание углерода в сотых долях процента, например марка 50 содержит углерода 0,47-0,55% С.
3.Требования ГОСТа к составу катанки.
Катанка используется по ГОСТ 1050-74; ГОСТ 14959-79 для патентирования группы В11.
По техническим условиям ТУ 14-15-254-91 катанка по ТУ изготавливается 4-х классов:
класс ВК — катанка канатная высококачественная;
класс ВД — катанка высокой деформированности;
класс КК-катанка канатная качественная;
класс ПД — катанка конструкционная.
Отличие ТУ 14-15-254-91 от ГОСТ 1050-14 и ГОСТ 14954-79:
1.Допуск по ТУ +/- 0,2 мм.; допуск по ГОСТ +/- 0,3 : 0,5 мм
2.Овальность по ГОСТ не более 0,5мм, по ТУ не более 0,3 мм.
3.По ТУ оговорено количество окалины — 5 кг/т, по ГОСТ окалина не оговаривается.
4.По техническим условиям оговаривается наличие пластинчатого перлита первого бала не менее 30%, по ГОСТ эта величина не оговаривается.
5.По техническим условиям оговаривается глубина обезуглероженного слоя — 2,5% для катанки ВК, ВД и ПД и 3% для катанки КК.
Нормируются также следующие
По тех. условиям | По ГОСТ |
азот — 0,008 % | |
мышьяк — 0,08 % | |
медь — 0,10-0,15% | |
алюминий — 0,005 % | |
титан — 0,005 % |
Подусадочная неоднородность (ликвация) для классов регламентирована:
По тех.условиям | По ГОСТ |
азот — 0,008% | |
мышьяк — 0,08 % | |
медь-0,10-0,15 % | |
алюминий — 0,005% | |
титан — 0,005 % |
4.Поставка и складирование катанки.
Катанка поставляется партиями, в вагоне должно быть не более двух партий (плавок). Каждый моток катанки маркируется, где указано:диаметр, марка стали, номер плавки и завод-изготовитель.
Катанка на складе обязательно складируется повагонно, «колбаской»,по маркам и плавкам, это условие в дальнейшем при переработке существенно сказывается на качестве работы.
Перед выдачей катанки в работу она проверяется ОТК внешней приемки на соответствие ее сертификатным данным, после чего ОТК дает разрешение на запуск катанки в производство.
При переработке катанки должна вырабатываться каждая плавка полностью, недоработка отдельных плавок (хвосты) в дальнейшем резко ухудшают работу и приводят в отдельных случаях к браку изготовленной проволоки. При выдаче катанки в работу данные регистрируются в журнале и обязательно с разрешения ОТК внешней приемки.
5.Травление катанки.
Поверхность катанки перед волочением подвергают тщательной подготовке. Травление применяют для удаления окалины с поверхности катанки. Удаление окалины перед волочением необходимо для уменьшения трения в канале волок и снижения силы волочения, температуры в очаге деформации и величины остаточных напряжений в проволоке после волочения.
Окалину удаляют химическим способом в водных растворах серной кислоты. Для травления применяется серная кислота по ГОСТ 2184-77. Марки контактная 92,5 — 94 %; башенная- 75 %.
Скорость травления в серной кислоте максимальная при ее концентрации 2,5 %. На практике кислоту высокой концентрации не применяют, чтобы избежать сильного разъедания металла и насыщения его водородом, приводящего к возникновению травильной хрупкости. Чтобы избежать травильной хрупкости при травлении, в травильную ванну вводят следующие ингибиторы травления:
а) ингибитор С-5 | ТУ 14-6-156-78 |
б) И1В и И2В | ТУ 38-103339-76 |
в) лигнофосфат | ГОСТ 13-183-83 |
г) соль поваренная | ГОСТ 13830-84 |
д) тринатрийфосфат | ГОСТ 201-76. |
В ванну травления также добавляется пенообразователь для предотвращения испарения кислоты в воздух травильного отделения.
Травление производится в «садочных» ваннах. Перед опусканием катанки в ванну бунты освобождают от вязов с тем, чтобы был свободный доступ кислоты к виткам катанки. Время выдержки зависит от концентрации кислоты и наличия толщины (кг/т) окалины на катанке.
После травильной ванны катанку промывают водой.
Промывка катанки водой производится в садочных ваннах путем окунания бунтов в ванну. Промывка катанки производится с целью удалить с поверхности металла остатки кислоты, окалины, а так же сернокислой соли и грязи. Промывку производят в двух ваннах: — первая в горячей воде; — вторая в холодной воде. После промывки металл должен иметь матовый цвет.
Нанесение подсмазочного слоя. После травления и промывки на поверхность катанки наносится подсмазочный слой. В качестве подсмазочного слоя используется бура по ГОСТ 3429-70 Концентрация буры в пределах 50-70 г/л; t=80 C. Время погружения от 5 до 10 мин. Обработка металла в буре заметно улучшает условия волочения, предохраняет проволоку от ржавления в течение длительного времени, улучшаются условия сварки, так как бура является флюсом.
Сушка металла — это заключительная операция при травлении металла. В процессе сушки с поверхности металла удаляется влага, устраняется травильная хрупкость. Сушка производится в ванне (баке) нагретым циркулирующим воздухом. Качество поверхности катанки подготовленной к волочению определяет успех при волочении на станах. Подготовленная к волочению катанка передается в волочильное отделение на волочильные станы.
6.Волочение проволоки из катанки.
Однократное волочение — это когда заготовка протягивается только через одну волоку, полностью наматывается на волочильный барабан и передается на катушку или снимается в виде мотка.
Многократное волочение — проволока протягивается одновременно через несколько волок, барабанов и волок может быть 15 и более. В основном это сводится к механизации передачи проволоки на последующую протяжку и возможности повышения скорости волочения. Кроме того повышается производительность и .облегчается труд. При многократном волочении улучшаются условия волочения, например не нарушаются условия смазки, наблюдаемые при однократном волочении в процессе передачи проволоки с одного стана на другой.
В цехе катанка проходит волочение на волочильных станах. Катанка
O 6,5 мм. может протягиваться доO 2,8 мм. в зависимости от требуемой заготовки по технологии до конечного размера на готовой проволоке с требованиями по механическим свойствам.
Инструментом при волочении является волока, представляющая собой инструмент с воронкообразными отверстиями определенной формы, через которое протягивается обрабатываемая .проволока. Для изготовления волок применяют твердые сплавы марки ВК-6; ВК-5.
На заводах в основном применяется сдвоенные волоки. Сдвоенные волоки представляют собой две волоки вмонтированные в металлическую обойму, одна является напорной, другая — чистовой. Сдвоенные волоки работают в режиме гидродинамического трения, что значительно снижает усилия трения в очаге деформации.
В процессе волочения волочильный инструмент от сил трения нагревается до весьма высоких температур, поэтому на волочильных станах имеется система охлаждения волок водой.
Смазкой при волочении является мыльный порошок, который засыпается в мыльницу, где устанавливается волока. Мыльный порошок втягивается в зону деформации с помощью движения проволоки.
7.Патентирование заготовки.
После волочения катанки или заготовки (проволоки) на заданный размер, когда этот металл исчерпал свои пластические свойства и дальнейшее волочение уже невозможно, его подвергают термообработке (патентированию).
Патентирование в цехе производится на протяжных агрегатах, которые в своем составе имеют:
а) печь для нагрева;
б) селитровую ванну;
в) промывочную ванну — 2шт;
г) травильную ванну;
д) ванну для бурения;
е) сушильное устройство;
г) намоточное устройство (24 катушки или 16 ).
Патентирование заключается в нагреве заготовки до температуры 950-980 и охлаждение ее в селитровой ванне при температуре 450-550 (Эти температуры зависят от химического состава металла). Селитра используется по ГОСТ 821-77. При выходе из селитровой ванны заготовки подвергается промывке в горячей воде, где удаляются остатки соли.
Травление заготовки осуществляется в протяжной ванне в серной кислоте ГОСТ 2184-79. Травление необходимо для удаления окалины образовавшейся в процессе нагрева заготовки в печи.
Промывка заготовки после травления производится в протяжной ванне в проточной воде, в процессе промывки удаляются кислотные загрязнения.
Обработка в растворе буры. Бура (ГОСТ 8429-77) наносится на поверхность как подсмазочный слой, для улучшения условий волочения, повышения стойкости волок. Концентрация буры в ванне должна быть в пределах 50-70 г./л, температура ванны 80
Сушка заготовки. После бурирования сушка необходима для удаления влаги, так как наличие влаги на заготовке затрудняет волочение, приводит к преждевременному выходу из строя волочильного инструмента (раскол волок).
Намотка заготовки на катушки. Намотка заготовки на катушки является заключительной операцией. Заготовка на катушках транспортируется на волочильные станы для дальнейшего волочения на меньшие размеры проволоки.
8.Оцинкование проволоки.
Оцинкование производится по следующей схеме:
а) обезжиривание проволоки в растворе едкого натрия технического по ГОСТ 2263-79;
б) промывка в горячей воде;
в) травление в соляной кислоте по ТУ 6-01-193-80;
г) промывка в воде;
д) флюсование для улучшения сцепления цинка с металлом;
е) цинкование в растворе цинка при температура раствора 420-460 ? Цинк используется по ГОСТ 3640-79 марки Ц-0, Ц-1;
ж) охлаждение проволоки водой;
з) намотка готовой проволоки на катушку.