Технология производства портландцемента — мокрый способ
Мокрый способ целесообразно применять, если в глине имеются посторонние примеси при значительных колебаниях химического состава сырья и его высокой влажности.
К недостаткам этого способа относится высокий расход топлива на обжиг — в 1,5 — 2 раза больший, чем при сухом.
Технологическая схема получения цемента по мокрому способу
1 — щековая дробилка;
2 — молотковая дробилка;
3 — склад сырья;
4 — мельница «Гидрофол»;
5 — мельница мокрого помола;
6 — вертикальный шламбассейн;
7 — горизонтальный шламбассейн;
8 — вращающаяся печь;
9 — холодильник;
10 — клинкерный склад;
11 — мельница;
12 — силос цемента.
Обычно содержание СаСО3 в шламе составляет 75 — 78%. Отклонение от него допускается не более 0,1%. Откорректированный шлам хранится в горизонтальных шламбассейнах. Из них шлам перекачивают мощными насосами в распределительный бачок установленный над печью. Из бачка шлам поступает в печь на, обжиг.
При выдерживании происходит гашение атмосферной влагой СаО несвязанного. Одновременно с этим стекловидная часть клинкера кристаллизуется, двухкальциевый силикат 2СаО•SiО2 из β-модификации частично превращается γ-форму. Все это приводит к стабилизации состава клинкера, некоторому разрыхлению его и облегчению последующего помола.
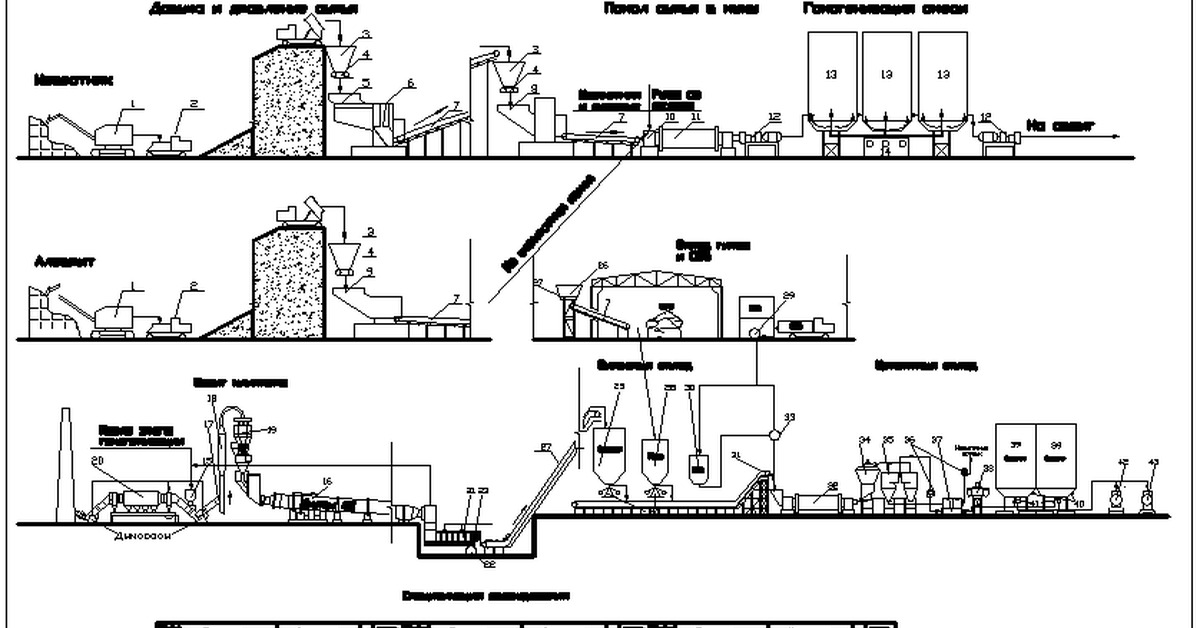
Открытые клинкерные склады оборудованы мостовыми кранами с грейферными захватами, с помощью которых клинкер и минеральные добавки подают в расходные бункера цементных мельниц.
В силосных складах составляющие цемента поступают на сборный ленточный конвейер, который доставляет их к мельницам. Питание шаровых мельниц осуществляется с помощью тарельчатых дозаторов, установленных под расходным бункером возле каждой мельницы.
Влажность размалываемых материалов не должна превышать у клинкера — 0,3%, у минеральных добавок — 2%, у гипса — 10%. При необходимости минеральные добавки перед помолом высушиваются.
Тонкость помола оказывает существенное влияние на свойства портландцемента. Чем тоньше размолот клинкер, тем быстрее схватывается и твердеет цемент и выше его прочность в начальные сроки твердения.
Цемент упаковывается в мешки специальными машинами, производительность которых достигает 120 т/ч. Каждая партия его снабжается паспортом, в нем указываются масса, марка, название цемента.
© Авторское право принадлежит «Мега Пауэр Гонконг Груп Лимитед».
В случае использования ссылка на сайт обязательна
Технология производства | Газметаллпроект
Технология производства портландцемента

Производство портландцемента включает в себя следующие основные этапы: добыча сырья; приготовление сырьевой смеси; обжиг сырьевой смеси и получение клинкера; совместный помол клинкера с гипсом, а в некоторых случаях также с различными добавками, способными придать портландцементу специальные свойства, причем первые три этапа являются наиболее энергоемкими и дорогостоящими, на них приходится около 70% себестоимости цемента.
Добыча мергеля осуществляется открытым способом в карьерах. Карьеры мергеля разрабатываются горизонтальными уступами высотой от 15до 20м. Основными процессами при добыче и переработке мергеля являются производство вскрышных работ, разрушение и добыча материала, погрузка экскаваторами и внутрикарьерное транспортирование карьерными самосвалами. Мергель из карьера поступает в дробильное отделение, где подвергается одно – либо двухстадийному дроблению в щековых, ударно – отражательных, молотковых дробилках. Дробленый мергель по системе транспортеров поступает на склад.
Существует два основных способа производства портландцемента – «мокрый» и «сухой».При «мокром» способе производства сырьевые материалы измельчают в помольных установках в присутствии воды, в результате чего получается текучая сметанообразная масса, называемая шламом, с влажностью 37 — 38%. Полученная таким образом сырьевая смесь подается на обжиг в длинную вращающуюся печь с внутрипечными теплообменными устройствами.
Печь «мокрого» способа производства можно условно разделить на 6 технологических зон: сушки, подогрева, кальцинирования (декарбонизации), экзотермических реакций, спекания и охлаждения.

При выборе способа производства учитываются различные факторы: однородность химического состава сырьевых материалов, их физико – механические характеристики.
В настоящее время наиболее востребован «сухой» способ производства цемента, как более экономичный: удельный расход условного топлива на 1 тонну клинкера при «сухом» способе производства в два раза меньше, чем удельный расход условного топлива при «мокром» способе производства.
Полученный одним из способов портландцементный клинкер после охлаждения поступает на склад клинкера и добавок.

Для получения портландцемента клинкер подвергается тонкому измельчению в мельничных агрегатах совместно с гипсом (применяется для регулирования сроков схватывания цементного теста), а также при производстве некоторых видов цемента — с различными добавками.
Способы производства цемента
Настоящая Политика конфиденциальности персональной информации (далее — Политика) действует в отношении всей информации, которую ООО «УФАСТРОЙСНАБ» (ОГРН: 1100280041443, ИНН: 0278174031, адрес регистрации: 450001, РБ,
г. Уфа, ул. Левченко, д. 2, оф.1) и/или его аффилированные лица, могут получить о пользователе во время использования им сайта http://ufastroysnab.ru/.
Использование сайта http://ufastroysnab.ru/ означает безоговорочное согласие пользователя с настоящей Политикой и указанными в ней условиями обработки его персональной информации; в случае несогласия с этими условиями пользователь должен воздержаться от использования данного ресурса.
- Персональная информация пользователей, которую получает и обрабатывает сайт http://ufastroysnab.ru/
1.1. В рамках настоящей Политики под «персональной информацией пользователя» понимаются:
1.1.1. Персональная информация, которую пользователь предоставляет о себе самостоятельно при оставлении заявки, совершении покупки, регистрации (создании учётной записи) или в ином процессе использования сайта.
1.1.2 Данные, которые автоматически передаются сайтом http://ufastroysnab.ru/ в процессе его использования с помощью установленного на устройстве пользователя программного обеспечения,том числе IP-адрес, информация из cookie, информация о браузере пользователя (или иной программе, с помощью которой осуществляется доступ к сайту), время доступа, адрес запрашиваемой страницы.
1.1.3. Данные, которые предоставляются сайту, в целях осуществления оказания услуг и/или продаже товара и/или предоставления иных ценностей для посетителей сайта, в соответствии с деятельностью настоящего ресурса:
— имя
— электронная почта
— номер телефона
1.2. Настоящая Политика применима только к сайту http://ufastroysnab.ru/ и не контролирует и не несет ответственность за сайты третьих лиц, на которые пользователь может перейти по ссылкам, доступным на сайте http http://ufastroysnab.ru/. На таких сайтах у пользователя может собираться или запрашиваться иная персональная информация, а также могут совершаться иные действия.
1.3. Сайт в общем случае не проверяет достоверность персональной информации, предоставляемой пользователями, и не осуществляет контроль за их дееспособностью. Однако сайт http://ufastroysnab.ru/ исходит из того, что пользователь предоставляет достоверную и достаточную персональную информацию по вопросам, предлагаемым в формах настоящего ресурса, и поддерживает эту информацию в актуальном состоянии.
- Цели сбора и обработки персональной информации пользователей
2.1. Сайт собирает и хранит только те персональные данные, которые необходимы для оказания услуг и/или продаже товара и/или предоставления иных ценностей для посетителей сайта http://ufastroysnab.ru/.
2.2. Персональную информацию пользователя можно использовать в следующих целях:
2.2.1 Связь с пользователем, в том числе направление уведомлений, запросов и информации, касающихся использования сайта, оказания услуг, а также обработка запросов и заявок от пользователя
- Условия обработки персональной информации пользователя и её передачи третьим лицам
3.1. Сайт http://ufastroysnab.ru/ хранит персональную информацию пользователей в соответствии с внутренними регламентами конкретных сервисов.
3.2. В отношении персональной информации пользователя сохраняется ее конфиденциальность, кроме случаев добровольного предоставления пользователем информации о себе для общего доступа неограниченному кругу лиц.
3.3. Сайт http://ufastroysnab.ru/ вправе передать персональную информацию пользователя третьим лицам в следующих случаях:
3.3.1. Пользователь выразил свое согласие на такие действия, путем согласия, выразившегося в предоставлении таких данных;
3.3.2. Передача необходима в рамках использования пользователем определенного сайта http://ufastroysnab.ru/, либо для предоставления товаров и/или оказания услуги пользователю;
3.3.3. Передача предусмотрена российским или иным применимым законодательством в рамках установленной законодательством процедуры;
3.3.4. В целях обеспечения возможности защиты прав и законных интересов сайта http://ufastroysnab.ru/ или третьих лиц в случаях, когда пользователь нарушает Пользовательское соглашение сайта http://ufastroysnab.ru/.
3.4. При обработке персональных данных пользователей сайт http://ufastroysnab.ru/ руководствуется Федеральным законом РФ «О персональных данных».
- Изменение пользователем персональной информации
4.1. Пользователь может в любой момент изменить (обновить, дополнить) предоставленную им персональную информацию или её часть, а также параметры её конфиденциальности, оставив заявление в адрес администрации сайта следующим способом:
Email: [email protected]
4.2. Пользователь может в любой момент, отозвать свое согласие на обработку персональных данных, оставив заявление в адрес администрации сайта следующим способом:
Email: [email protected]
- Меры, применяемые для защиты персональной информации пользователей
Сайт принимает необходимые и достаточные организационные и технические меры для защиты персональной информации пользователя от неправомерного или случайного доступа, уничтожения, изменения, блокирования, копирования, распространения, а также от иных неправомерных действий с ней третьих лиц.
- Изменение Политики конфиденциальности. Применимое законодательство
6. 1. Сайт имеет право вносить изменения в настоящую Политику конфиденциальности. При внесении изменений в актуальной редакции указывается дата последнего обновления. Новая редакция Политики вступает в силу с момента ее размещения, если иное не предусмотрено новой редакцией Политики. Действующая редакция всегда находится на странице по адресу http://ufastroysnab.ru/
6.2. К настоящей Политике и отношениям между пользователем и Сайтом, возникающим в связи с применением Политики конфиденциальности, подлежит применению право Российской Федерации.
- Обратная связь. Вопросы и предложения
7.1. Все предложения или вопросы по поводу настоящей Политики следует направлять следующим способом:
Email: [email protected]
мокрый и сухой способ производства цемента
Сухой цемент представляет собой искусственное вещество, которое поставляется в формате порошка и используется в качестве вяжущего в процессе замешивания разного типа бетонных растворов. В момент смешивания с водой цемент провоцирует прохождение химической реакции с изменением структуры материала, который застывает и превращается в камень, обеспечивая монолиту должные характеристики прочности, стойкости, способности выдерживать механические нагрузки.
Что входит в состав цемента:Состав цемента может быть разным, что напрямую зависит от вида вяжущего и возложенных на него функций, требуемых свойств материала. Классический цемент делают из клинкера (обожженные и спаянные в куски известняк и глина, взятые в определенной пропорции), смешанного с гипсом и различными минеральными добавками.
- Известь (оксид кальция) – около 60%.
- Кремниевый диоксид – до 20%.
- Алюминий (глинозем) – 4%.
- Гипс, оксиды железа – до 2%.
- Магния оксид – 1%.
Данное процентное соотношение актуально для портландцемента – самого распространенного вида материала. Пропорции могут меняться, в соответствии с классном и технологией производства цемента. Ввиду существования большого числа марок и видов цемента точного рецепта его производства (и химической формулы) не существует – тут все зависит от показателей минералогического состава.
Производство цемента осуществляется из клинкера – продукта обжига глины и известняка, взятых в пропорции 1:3. Клинкер представляет собой полуфабрикат для создания цемента. После обжига при высокой температуре (до 1500 градусов) клинкер мелко измельчают до гранул величиной около 6 сантиметров. Потом клинкер измельчают до порошкообразного вида, вводя различные добавки.
Что входит в состав клинкера при измельчении:- Гипс, который регулирует длительность схватывания.
- Корректирующие добавки для улучшения определенных характеристик цемента (присадки, пластификаторы и т.д.).
В качестве основного исходного сырья в производстве цемента используют различные горные породы – карбонатного типа (могут быть с кристаллической либо аморфной структурой, определяющей уровень эффективности взаимодействия материала с остальными компонентами состава в процессе обжига) и осадочного происхождения (глинистое сырье с минеральной базой, которое при сильном увлажнении разбухает и становится пластичным, увеличиваясь в объеме; материал вязкий, применяется при производстве сухим способом).
Основные способы производства цемента:- Сухой – предполагает минимальную себестоимость и энергозатраты, так как несколько технологических этапов объединены в единый процесс. При поступлении в шаровую мельницу компоненты размалываются и сушатся одновременно.
- Мокрый способ производства цемента – тут известь заменяют мелом, в процессе производства используют воду. Цемент делают из сырья, в качестве которого выступает шихта (смесь исходных материалов), обладающая влажностью на уровне 50%.
- Комбинированный – данный метод объединяет особенности мокрой и сухой технологии. В результате обжига тут получают полусухой состав, влажность которого находится примерно на уровне 18%.
Мокрая технология производства цемента
Производство цемента мокрым методом начинается так же, как и в любом другом случае: с добывания твердого известняка из карьеров, который потом дробят на куски разной величины. Потом куски измельчают в специальных дробильных агрегатах до тех пор, пока фракция известняка не будет равна максимум 8-10 миллиметрам.
Потом на завод доставляют глину из карьера, ее обрабатывают в вальцевых дробилках до тех пор, пока размер кусков не будет равен максимум 100 миллиметрам. Измельченную смесь глины отмачивают в болтушках до момента получения глиняного шлама влажностью в пределах 70%. Потом шлам отправляют в мельницу, где его смешивают и размалывают вместе с известняком.
Далее шлам, влажность которого находится уже на уровне 40%, отправляют в вертикальный бассейн, где осуществляется окончательный процесс корректировки. Данная операция чрезвычайно важна, так как именно тут формируется и обеспечивается правильная химическая формула состава шлама.
После проверки качества шлама его транспортируют для реализации последующих этапов: цементную массу из вертикального бассейна транспортируют в горизонтальный, где смесь хранят до того, как отправить в печь для обжига. Сырье в горизонтальном бассейне постоянно перемешивается механически с использованием сжатого воздуха. Это не позволяет шламу выпадать в осадок и дает возможность полностью гомогенизироваться.
В случае, когда производство цемента предполагает использование сырья с неизменным химическим составом, корректирование состава шлама выполняется в горизонтальном бассейне.
Далее шлам отправляют на обжиг в печь, где он превращается в клинкер. Клинкерная основа, полученная в итоге, отправляется в промышленный холодильник и там охлаждается. Потом клинкер дробят, подают в емкости мельниц, повторно измельчают до состояния порошка.
В случае, когда процесс обжига шлама требует применения твердого топлива, необходимо позаботиться о строительстве дополнительного помещения (где будет храниться, готовиться уголь). Если технологическая схема производства цемента требует применения газообразного/жидкого топлива, процесс обжига клинкера упрощается.
На завершающем этапе производства цемент из бункеров мельниц направляют в специальные помещения, где он хранится. Здесь лаборанты исследуют качество продукции, определяют марку. Только по завершении проверки цемент может отправляться на упаковочные аппараты.
Преимущества
Рассматривая мокрый способ производства цемента, стоит учитывать его плюсы и минусы. Как и любой технологический процесс, данный обладает своими особенностями.
Ключевые достоинства мокрого метода производства цемента:- Понижение технологических затрат на измельчение сырьевой базы – глина и мел прекрасно намокают в воде в бассейне при первичной обработке, в связи с чем измельчаются легче и проще.
- Транспортировка, усреднение, корректировка шлама осуществляются проще, безопаснее с точки зрения экологии, особенно в сравнении с аналогичными процессами при производстве цемента сухим способом.
- Намного меньше образуется пыли.
- Печи обжига по конструкции простые, надежные, обладают высоким коэффициентом использования пространства (варьируется в пределах 0.89-0.91).
- Есть возможность использовать в производстве компоненты с достаточно «пестрым» (разным) химическим составом, а также обеспечена хорошая гомогенизация шлама.
Недостатки
Недостатков в мокром методе производства цемента мало, но они есть и не учитывать их нельзя.
Основные минусы мокрого метода производства цемента:- Высокий удельный расход тепловой энергии в процессе обжига сырья. Сырье, которое поступает для обжига, обладает в среднем влажностью до 45%. И для испарения влаги, правильного прогрева компонентов необходимо до 6800 кДж/кг тепловой энергии либо 35% тепловой мощности печи.
В связи с такими расчетами часть обжиговой печи функционирует в качестве сушильного агрегата с последующими сложностями.
- Высокий уровень материалоемкости печей для обжига наряду с не очень большой производительностью.
Указанные недостатки приводят к достаточно низкой производительности труда, существенным эксплуатационным и технологическим расходам, что обуславливает высокую стоимость всего производства.
Сухая технология производства
Сухой способ производства цемента использует другую технологическую схему. Известняк и глина, которые добывают из карьера, дробятся и отправляются в сепараторную мельницу. Тут они смалываются, смешиваются, сушатся. Полученную смесь доставляют в смесительные аппараты, окончательно перемешивают с использованием сжатого воздуха. Сейчас же корректируется и химический состав цемента.
При применении глинистого компонента сырье подают для смешивания в шнеки, где частично увлажняют водой. Создаются прочные гранулы со влажностью максимум 14%, потом они поступают для обжига в печь.
Обжиг сырья при сухом методе может осуществляться в разных печах – в данном случае особое внимание обращают на приготовление сырья. А дальнейшие этапы производства сходны с мокрым методом.
Плюсы технологии
В сравнении с мокрым, сухой метод обладает некоторыми преимуществами, которые обязательно нужно учитывать при расчетах (когда планируется организовать бизнес по производству цемента, к примеру).
Главные достоинства сухого метода:- Сравнительно невысокий удельный расход энергии тепла на обжиг клинкера – в пределах 2900-3700 кДж/кг.
- Объем печных газов меньше на 30-40%, их можно вторично применять для сушки сырья и значительно снизить энергозатраты на создание клинкера, уменьшить затраты на обеспыливание.
- Значительно меньшая металлоемкость печей для обжига при повышенной производительности в сравнении с мокрой технологией. Мощность печей при «сухом» методе составляет 3000-5000 тонн в сутки, что больше в 1-2 раза аналогичного оборудования мокрого метода.
- Нет необходимости в мощных источниках воды.
Минусы технологии
Несмотря на явные преимущества, есть у технологии и свои минусы.
Какие недостатки есть у сухого метода производства цемента:- Значительно больше выделяется пыли, что усложняет соблюдение санитарных норм, правил охраны окружающего пространства.
- Сложность конструкции печей для обжига и их требовательность в плане колебаний химического состава сырья, его степени влажности, дисперсности.
- Сравнительно низкий коэффициент использования печей – где-то 0.7-0.8.
Отличия мокрой технологии производства от сухой
Обе технологии производства цемента обладают своими нюансами, плюсами и минусами. Но есть ключевые особенности, которые необходимо учитывать в первую очередь при планировании бизнеса и просчете расходов, прибыли. Главный недостаток мокрого метода производства цемента – существенная энергоемкость всего процесса, которая отражается соответствующим образом на цене конечного продукта в сторону повышения.
Сухая же технология менее экологична и опасна для окружающей среды, в связи с чем требует значительных расходов на устранение этого фактора. При этом, сам процесс производства обходится дешевле по всем пунктам, позволяет понизить цену конечного продукта.
Особенности полусухого способа
Полусухой метод производства цемента достаточно схож с сухим, но предполагает некоторые отличия. Фракция сырья, что проходит стадию гранулирования, равна примерно 10-20 миллиметрам, уровень влажности 11-16%. Сначала сырье обжигают в печах Леполь, потом создавшиеся гранулы отправляют в конвейерный кальцинатор.
Из печи выходят газы, проходящие сквозь гранулы, находящиеся на решетке. Таким образом сырье нагревается до 900 градусов, полностью высушиваясь в процессе. Такая термообработка способствует декарбонизации смеси примерно на 25-30%, что нужно для производства. После сырье отправляют в печь – это завершающий этап производства цемента.
Гранулированный цемент может обжигаться и в шахтных печах – в таком случае гранулирование осуществляется с частицами угля, после чего цемент уходит на хранение.
Комбинированный метод производства
Данный способ базируется на подготовке компонентов сырья по мокрому методу, а вот их обжиг осуществляется по схеме полусухого метода. Шлам, полученный в сырьевой мельнице, обладает влажностью в диапазоне 30-45%, он отправляется в фильтр: тут обезвоживается до уровня влажности в 15-20%, потом сырье смешивают с пылью, влажность доводят до показателя в 12-14%.
На следующем этапе смесь отправляется на обжиг, который осуществляется в печах полусухого способа изготовления цемента. Все остальные операции ничем не отличаются от аналогичных этапов мокрого метода производства.
Подходящий метод производства цемента выбирают в соответствии с технологическими и технико-экономическими факторами – качеством и типом сырья, влажностью и однородностью смеси, наличием соответствующего оборудования, возможностей и т.д. В Москве заводы работают по всем трем схемам и поставляют на рынок цемент высокого качества.
Мокрый способ производства цемента в Одинцово
Из всех существующих технология производства цемента мокрым способом остается наиболее популярной и распространенной во всем мире. В разных странах – лидерах соответствующего сегмента рынка — объем производства мокрого цемента составляет от 60 до 90% от общего количества выпускаемого материала. Несмотря на то, что мокрый способ производства цемента более энергозатратен (в сравнении с сухим), он предоставляет возможность получать высококачественный конечный продукт при использовании неоднородных сырьевых компонентов с повышенной влажностью:
Особенность мокрого способа заключается в присутствии воды при подготовке и соединении отдельных составляющих портландцементного клинкера. Начальные этапы производства мокрого цемента
Завершающий цикл создания цемента мокрым спосбомВажным этапом производства является обжиг подаваемого насосами шлама в специальных вращающихся печах. Благодаря происходящим при этом химическим реакциям происходит образование портландцементного клинкера, который затем охлаждают и несколько недель выдерживают на складе. В завершение клинкер перемалывают, сушат и в цементных мельницах соединяют с гипсом и активными минеральными добавками. Готовый цемент отправляют на хранение и последующую фасовку в цементные силосы. Дата публикации: 13.01.2015 07:19
|
Добавлено в корзину
Цена бетона в РФ в июне 2019 года
«Мосметрострой» дорыл тоннель до мэрии
Минстрой и Минфин готовят предложения по стимулированию строительства
Отгрузка цемента по ж/д вновь демонстрирует рост
Наши награды:
ООО СФ СМУ-152 Трансинжстроя стала лауреатом Ежегодной Всероссийской Премии «ПРЕДПРИЯТИЕ ГОДА» в области имиджа и деловой репутации
в 2014 году.
подробнее →
Наши проекты
метро «Борисово»
метро «Зябликово»
метро «Шипиловская»
Посмотреть больше »
7. Технология производства портландцемента
7.1. Способы производства портландцемента
Производство портландцемента включает ряд технологических операций, которые можно разделить на две основные группы. Первая — это операции по производству клинкера, вторая — измельчение клинкера совместно с гипсом, а в ряде случаев и с другими добавками, т. е. приготовление портландцемента. Получение клинкера — наиболее сложный и энергоемкий процесс, требующий больших капитальных и эксплуатационных затрат. Доля клинкера в стоимости портландцемента достигает 70—80 %. Производство клинкера состоит из добычи сырьевых материалов, дробления, помола и смешивания их в определенном соотношении, обжига сырьевой смеси и магазинирования клинкера.
Комплекс операций
по получению из клинкера портландцемента
включает следующие технологические
процессы: дробление клинкера, сушку
минеральных добавок, дробление гипсового
камня, тонкое измельчение клинкера
совместно с активными минеральными
добавками и гипсом, складирование,
упаковку и отправку цемента потребителю.
Даже в пределах одного месторождения химико-минералогический состав сырья меняется в широких пределах. Поэтому получение сырьевой смеси постоянного состава — сложная задача. С другой стороны, перерабатываемое цементной промышленностью сырье отличается не только составом, но и физико-техническими свойствами (влажностью, прочностью и т. д.). Для каждого вида сырья должен быть выбран такой способ подготовки, который обеспечивал бы тонкое измельчение и равномерное перемешивание компонентов шихты с минимальными энергетическими затратами. Это послужило причиной появления в цементной промышленности трех способов производства, отличающихся технологическими приемами подготовки сырьевых смесей: мокрого, сухого и комбинированного При мокром способе тонкое измельчение сырьевой смеси производят в водной среде с получением шихты в виде водной суспензии — шлама влажностью 30—50%. При сухом способе сырьевую шихту готовят в виде тонкоизмельченного сухого порошка, поэтому перед помолом или в процессе его сырьевые материалы высушивают. Комбинированный способ может базироваться как на мокром, так и на сухом способе приготовления шихты. В первом случае сырьевую смесь готовят по мокрому способу в виде шлама, а затем обезвоживают на фильтрах до влажности 16—18 % и подают на обжиг в печи в виде полусухой массы. Во втором варианте сырьевую смесь готовят по сухому способу, а затем гранулируют с добавкой 10—14 % воды и подают на обжиг в виде гранул диаметром 10—15 мм. Каждый способ производства может быть реализован в виде нескольких технологических схем, отличающихся как последовательностью операций, так и видом используемого оборудования. Выбор конкретной технологической схемы, определяется свойствами перерабатываемого сырья (твердостью, однородностью, влажностью).
Мокрый способ
производства.На отечественных
цементных предприятиях при подготовке
сырьевой смеси по мокрому способу в
большинстве случаев используют твердый
карбонатный (известняк) и мягкий глинистый
(глина) компоненты. Принципиальная
технологическая схема получения
портландцемента представлена на схеме
1.
Известняк как более твердый материал предварительно подвергается дроблению, а пластичная глина измельчается в присутствии воды в специальных аппаратах (болтушках или мельницах-мешалках). Окончательное тонкое измельчение с получением однородной смеси известняка, глиняного шлама и корректирующих добавок происходит в шаровых трубных мельницах. Хотя компоненты дозируют в мельницы в заданном соотношении, из-за колебаний их химико-минералогических характеристик не удается получить в мельнице шлам состава, отвечающего установленным параметрам. Поэтому необходима специальная технологическая операция по корректировке его состава. После проверки соответствия состава шлама заданным показателям его подают на обжиг во вращающуюся печь, где завершаются химические реакции, приводящие к получению клинкера. Затем клинкер охлаждается в холодильнике и поступает на склад, где также хранятся гипс и активные минеральные добавки. Эти компоненты предварительно должны быть подготовлены к помолу. Активные минеральные добавки высушивают до влажности не более 1 %, гипс подвергают дроблению. Совместный тонкий размол клинкера, гипса и активных минеральных добавок в шаровых трубных мельницах обеспечивает получение цемента высокого качества. Из мельниц цемент поступает в склады силосного типа. Отгружают его либо навалом (в автомобильных и железнодорожных цементовозах), либо упакованным в многослойные бумажные мешки.
При приготовлении
шлама из двух мягких (мела и глины) и
двух твердых компонентов (известняка
и глинистого мергеля) последовательность
основных технологических операций не
меняется. Однако особенности свойств
измельченного сырья и стремление к
выбору наименее энергоемких технических
решений обусловливают существенные
отличия способов измельчения компонентов.
При использовании двух мягких компонентов
принципиальная технологическая схема
будет такой, которая показана на схеме
2.
Такая технологическая схема позволяет эффективно использовать способность мягкого сырья распускаться в воде. Применение мощного современного оборудования для предварительного измельчения сырья (например, мельниц «Гидрофол») позволяет отказаться от его дробления. Однако на стадии предварительного измельчения часть сырья остается недоизмельченной, и получение шлама также должно завершаться в шаровой трубной мельнице.
При использовании двух твердых компонентов принципиальная технологическая схема приобретает новый вид (см. схему 3).
В данной технологической схеме повышенная твердость глинистого сырья обусловливает необходимость его предварительного дробления. Тонкое измельчение всех компонентов происходит в одну стадию в шаровой мельнице. Очевидно, что этот вариант технологической схемы связан с большими трудностями получения однородной тонкодисперсной смеси и большим расходом энергии.
В водной среде облегчается измельчение материалов и улучшается их перемешивание. В результате снижается расход электроэнергии (при мягком сырье экономия может достигать 36 МДж/т сырья) и получается более однородная шихта, что, в конечном счете, приводит к росту марки цемента. Кроме того, при мокром способе упрощается транспортировка шлама и улучшаются санитарно-гигиенические условия труда. Сравнительная простота мокрого способа и возможность получения высокомарочной продукции на сырье пониженного качества обусловили его широкое распространение в цементной промышленности нашей страны. В настоящее время этим способом выпускается около 85 % клинкера.
Схема 1
Схема 2
Схема 3
В то же время
введение в шлам значительного количества
воды (30—50 % массы шлама) обусловливает
резкое повышение расхода теплоты на ее
испарение. В результате расход теплоты,
при мокром способе (5,8— 6,7 МДж/кг) на
30—40 % выше, чем при сухом способе. Кроме
того, при мокром способе возрастают
габариты и соответственно металлоемкость
печей. Исходя из этого в нашей стране
принято решение прекратить проектирование
и дальнейшее наращивание мощностей по
выпуску портландцемента мокрым способом.
Сухой способ производства.Последовательность технологических операций производства портландцемента сухим способом такая же, как и при мокром, однако при подготовке сырьевых смесей имеются существенные отличия, зависящие от влажности и твердости сырья. При переработке сырья повышенной твердости и умеренной влажности принципиальная технологическая схема имеет вид, представленный на схеме 4.
Высокая твердость измельчаемых материалов требует предварительного их дробления. Тонкое измельчение материалов может производиться при влажности не более 1 %. В природе такое сырье практически не встречается, поэтому обязательная операция сухого способа производства — сушка. Желательно совмещать ее с размолом сырьевых компонентов. На большинстве новых предприятий, работающих по сухому способу производства, в шаровой трубной мельнице совмещаются процессы сушки, тонкого измельчения и перемешивания всех компонентов сырьевой смеси. Из мельницы сырьевая смесь выходит в виде тонкодисперсного порошка — сырьевой муки. В железобетонных силосах производятся корректировка ее состава до заданных параметров и гомогенизация перемешиванием сжатым воздухом. Готовая сырьевая смесь поступает на обжиг. Вращающиеся печи сухого способа производства оборудованы запечными теплообменными устройствами (циклонными теплообменниками). В них за несколько десятков секунд сырьевая смесь нагревается до 700—800°С, дегидратируется и частично декарбонизируется. Завершается обжиг клинкера во вращающейся печи.
Необходимость
экономии расхода топлива вынуждает
перерабатывать по сухому способу
материалы со все более высокой влажностью.
Технологическая схема производства
портландцемента из такого сырья выглядит
следующим образом (см. схему 5).
Предварительное измельчение материалов повышенной влажности при сухом способе целесообразно осуществлять в мельницах самоизмельчения типа «Аэрофол», позволяющих перерабатывать сырье с влажностью до 25 %. Однако полностью высушиться сырье при этом не успевает и в шаровой мельнице одновременно с доизмельчением крупных частиц и получением однородной сырьевой смеси производится ее досушка.
Приготовление сырьевой смеси в виде порошка усложняет технологическую схему. Увеличивается число энергоемкого оборудования, более «капризного» при эксплуатации. Сложнее при сухом способе обеспечить санитарные условия и охрану окружающей среды. Но решающим его преимуществом является снижение расхода теплоты на обжиг клинкера до 3,4—4,2 МДж/кг. Кроме того, на 35—40 % уменьшается объем печных газов, что соответственно снижает стоимость обеспыливания и дает больше возможностей по использованию теплоты отходящих газов для сушки сырья.
Важнейшее преимущество сухого способа — более высокий съем клинкера с 1 м3печного агрегата. Это позволяет проектировать и строить печи по сухому способу в 2—3 раза более мощные, чем по мокрому. В целом по технико-экономическим показателям сухой способ превосходит мокрый. При использовании мощных печей он обеспечивает снижение удельного расхода топлива на обжиг клинкера примерно вдвое, рост годовой выработки на одного рабочего примерно на 40 % и уменьшение себестоимости продукции на 10 % и сокращение капиталовложений при строительстве предприятий на 50 %. Это обусловило интенсивное его распространение в мировой цементной промышленности. Широкое внедрение сухого способа производства — важнейшая задача, стоящая перед цементной промышленностью нашей страны. Доля прироста мощностей сухого способа в отрасли за период 1986—1990 гг. составит около 80 %.
Схема 4
Схема 5
Однако надо
учитывать, что возможности применения
сухого способа ограничены влажностью
перерабатываемого сырья. Переработка
сырья с влажностью более 20—25 % по сухому
способу связана с высокими расходами
теплоты на сушку, и этот способ становится
неэкономичным.
Комбинированный способ производства.Наиболее перспективна технологическая схема комбинированного способа производства, представленная на схеме 6.
Такая схема позволяет использовать преимущества подготовки сырьевой смеси по мокрому способу и одновременно снизить расход теплоты на обжиг. При этом почти на 30 % уменьшается расход топлива и примерно на 10% — капитальные затраты по сравнению с мокрым способом, но на 15—20 % повышается расход электроэнергии. Такая схема — наиболее реальный путь снижения расхода топлива предприятиями, работающими на сырье высокой влажности. В настоящее время в стране ведутся работы по переводу предприятий с мокрого способа производства на комбинированный. Наиболее сложным при этом является создание и внедрение надежных и высокопроизводительных аппаратов для фильтрации шлама. При базировании комбинированного способа производства на приготовлении сырьевой смеси сухим способом технологическая схема будет такой, которая показана на схеме 7.
Принципиальное отличие этой схемы от схемы сухого способа — это появление дополнительной технологической операции — грануляции сырьевой смеси, осуществляемой с добавкой 10—14 % воды в специальных аппаратах — тарельчатых грануляторах. Гранулированную смесь с размером зерен 10—15 мм обжигают в шахтных печах или печах с конвейерными кальцинаторами. Этот способ требует несколько большего, чем сухой, расхода теплоты, необходимой на испарение введенной при грануляции воды; не всякая сырьевая смесь способна давать прочные гранулы, не разрушающиеся при обжиге; сложна конструкция используемых печных агрегатов. В то же время обжиг гранулированного сырья позволяет стабилизировать режим работы печей, улучшить теплообмен, повысить качество клинкера.
Таким образом, каждый способ производства портландцемента имеет свои достоинства и недостатки. Преобладание того или иного способа в разных странах определяется технико-экономическими особенностями развития цементной промышленности.
Производство цемента по мокрому способу (Реферат)
Министерство общего и профессионального образования
Российской Федерации
Белгородская государственная технологическая академия
строительных материалов
Кафедра экономики и организации предпринимательства
КУРСОВОЙ ПРОЕКТ
по дисциплине:
«Организация производства на предприятиях ПСМ»
на тему:
«Организация производства цемента по мокрому способу»
Выполнил: студент гр. ЭК-31 ФЭМ Пашнев В.А.
Руководитель: к.э.н., доцент Выборнова В.В.
— Белгород 1999 г. —
Министерство общего и профессионального образования
Российской Федерации
Белгородская государственная технологическая академия
строительных материалов
Кафедра экономики и организации предпринимательства
ЗАДАНИЕ
К КУРСОВОМУ ПРОЕКТИРОВАНИЮ
Студент группы: ЭК-31
Специальность 06.08.
Пашнев Владислав Александрович
Задание:
Срок выполнения:
Руководитель: Выборнова В.В.
ОГЛАВЛЕНИЕ.
Реферат на тему «Предпринимательство в РФ, проблемы, перспективы».
Организация производства цемента.
Характеристика продукции и технологических способов её производства.
Производственная и организационная структура предприятия.
Построение циклограммы и расчет длительности производственного цикла.
Выбор и обоснование режима работы.
Расчет производственной программы по цехам.
Определение потребности в оборудовании по основным участкам.
Расчет производственной мощности по цехам и построение профиля.
Анализ профиля мощности и проектирование мероприятий по достижению проектной производственной программы.
План расстановки оборудования по цехам.
2.10. Определение новой проектной производственной программы и планирование мероприятий по ее достижению.
Оценка экономической эффективности проекта.
Определение инвестиций в проектируемое предприятие.
Расчет изменения численности и изменения ФОТ.
Расчет изменения себестоимости продукции в связи с проектируемым мероприятием.
План доходов, денежные потоки и финансовый профиль проекта.
Определение точки безубыточности проекта.
Заключение.
Список литературы.
Задание к курсовому проекту.
В состав производства цемента входит три отделения:
Сырьевой цех.
Цех обжига.
Цех помола.
Режим работы отделений:
— непрерывный, трехсменный для цеха обжига.
Годовая производственная программа:
Параметр
Значение
Величина объема производства, млн. т.
1,90
Увеличение объема производства, %
34
Процент добавок, %
13
Расход шлама на 1 т. клинкера, т.
1,59
2.1. Характеристика продукции и технологический метод её производства.
Цемент – один из важнейших строительных материалов, предназначенных для бетонов и строительных растворов, скрепление отдельных элементов (деталей) строительных конструкций, гидроизоляций и др. Цемент представляет собой гидравлический вяжущий материал, который после смешения с водой и предварительного затвердевания на воздухе продолжает сохранять и наращивать прочность в воде.
Производство цемента обусловлено необходимостью его производства для применения в главным образом в строительстве. Строительство жилья на основе цемента позволяет получить объекты с низкой теплопроводностью и высокой морозостойкостью.
Технология цементное производство позволяет использовать в нём отходы добывающей, металлургической отраслей, а также побочные продукты этих производств. Некоторые отходы даже улучшают свойства цемента. Гибкая технология позволяет осуществлять комбинирование производства цемента с производством металлов, химических продуктов и энергии.
Существует много как бы подвидов цемента. Они отличаются друг от друга конечными свойствами, условиями производства и наличием в них различных видов добавок.
Портландцементом (далее п.ц.) называется гидравлическое вяжущее вещество, твердеющее в воде и на воздухе, получаемое путём совместного размола портландцементного клинкера и гипса для регулирования сроков схватывания. Марку п.ц. определяют при испытании на сжатие стандартной цементной палочки размерами 4*4*16 мм.
Существуют следующие марки п.ц., выпускаемые промышленностью строительных материалов:
ПЦ 400 ДО и ПЦ 400 Д20. Применяется для производства асбестоцементных изделий, строительства жилья, промышленных зданий и сооружений.
ПЦ 500 ДО. Применяется для строительства мостов, путепроводов, железобетонных труб, пролетных строений и блоков.
ПЦ 600 ДО. Применяется для строительства мостов, туннелей, высокопрочных сооружений на объектах Министерства Обороны.
Мокрый процесс производства цемента
Цемент — это порошкообразный материал. При правильном смешивании с водой он превратится в суспензию. Суспензия постепенно затвердеет на воздухе и прочно склеит гранулированные или волокнистые материалы, такие как песок и камень. Он широко используется во всех сферах нашей жизни, таких как строительство метро, строительство мостов и строительство жилых домов. Это неотъемлемая часть нашего города.
Процесс производства силикатного цемента (также известного как портландцемент) типичен для производства цемента.Обычно в качестве основных материалов используются известняк и глина. После дробления, дозирования и измельчения до соответствующей степени зернистости большая часть сырья будет загружена в цементную печь для обжига клинкера, а затем мы обычно добавляем соответствующее количество гипса (иногда смешанного с другими материалами или добавками) в процессе измельчения цемента. , наконец, получение цементных изделий квалифицированной крупности. На цементном заводе, в соответствии с различными методами подготовки сырья, производство цемента можно разделить на сухой процесс (включая полусухой процесс) и мокрый процесс (включая полумокрый процесс).Далее мы подробно обсудим мокрый процесс производства цемента.
Схема процесса производства цементаМокрый процесс и сухой процесс
Мокрый процесс
Мокрый процесс производства цемента относится к измельчению сырья в суспензию после смешивания с водой с последующей подачей его в печь мокрого процесса для сушки и прокаливания и, наконец, образования клинкера. Содержание воды в суспензии обычно составляет от 32% до 36%. Кроме того, суспензия сырья также может быть обезвожена в блоки сырья и помещена в печь для обжига клинкера.Этот метод называется полумокрым процессом, который до сих пор относится к мокрому способу производства цемента.
Преимущества: мокрый процесс производства цемента отличается простотой эксплуатации, низким уровнем запыленности и легкостью транспортировки. Поскольку суспензия обладает текучестью, поэтому ее однородность хорошая, а качество клинкера улучшается. Более того, потребление энергии при измельчении сырья мокрым способом снижается почти на 30%.
Недостатки: потребление тепла мокрым процессом слишком велико, обычно между 5234-6490 Дж / кг, и потребление уязвимых частей шаровой мельницы также велико.По сравнению с другими методами обработки клинкер, полученный мокрым способом, имеет низкую температуру на выходе из печи, поэтому этот метод не подходит для производства клинкера с высоким содержанием кремнезема и высоким содержанием алюминия и кислорода.
Сухой процесс
Сухой процесс производства цемента означает, что после сушки, измельчения и измельчения сырьевых материалов с различными размерами частиц до порошков определенной степени измельчения они будут отправлены в сушильную печь для обжига, в результате чего образуется клинкер.Кроме того, порошкообразное сырье можно также превратить в шарики сырья, добавив необходимое количество воды, а затем направить его непосредственно в печь Лепол для обжига. Этот метод называется полусухим и относится к сухому способу производства цемента.
Преимущества: , поскольку сухой процесс заключается в непосредственной подаче порошка сырья во вращающуюся печь для обжига, а содержание влаги в сырье составляет около 1–2%, это позволяет экономить тепло, необходимое для испарения влаги.Таким образом, этот метод обладает преимуществами энергосбережения, высокой производственной эффективности и стабильной производительности, что позволяет удовлетворить производственные потребности крупных цементных заводов. В то же время при производстве цемента сухим способом сбрасывается меньше сточных вод. Это способствует защите окружающей среды. В настоящее время мы называем производственную линию с подогревателем и прекальцинатором новой линией по производству цемента сухим способом, что является направлением развития производства цемента сухим способом в будущем.
Недостатки: Недостатками сухого процесса являются неоднородный состав сырья, высокая энергоемкость и высокая запыленность цеха.
Процедуры мокрого процесса
Процедуры мокрого процесса в основном аналогичны сухому процессу, который можно разделить на три стадии: подготовка сырья, прокаливание клинкера и помол цемента. Все эти этапы описаны в статье «Что нужно знать о процессе производства портландцемента », о которой мы упоминали ранее.
Подобно сухому процессу, материалы также нуждаются в для разработки карьеров, первичного дробления, вторичного дробления, дозирования и измельчение на стадии подготовки сырья мокрого процесса. Самый большой разница между двумя методами заключается в том, что во влажном процессе вода обычно требуется в качестве технологической среды, добавляемой в сырую смесь для образования суспензии. После смешивания и смешивания, суспензия будет храниться в резервуаре для суспензии, ожидая дальнейшего обработка. В то время как на линии производства цемента сухим способом сырьевая смесь не нужна вода.
На стадии обжига цементная печь при влажном процессе дольше по сравнению с сухим процессом, и там Перед печью нет подогревателя и прекальцинатора. Температура в цементе температура печи может достигать 1400-1500 ℃, суспензия в ней нагревается и сушится и, наконец, формируется соединения клинкера, а именно силикат кальция, силикат трикальция, Трехкальциевый алюминат и тетракальциевый алюмоферрит. Клинкер — это разновидность частицы различных размеров и темно-зеленого цвета. После охлаждения в решетки охладителя, они будут отправлены в мельницу для последней обработки.
На последнем этапе клинкер будет измельчен. в квалифицированную тонкость помола в мельницах. Во время этого процесса мы обычно добавляем немного гипса и других материалов в клинкер, чтобы получить конечный цементный продукт различные свойства и способы использования. Например, мы добавляем гипс, чтобы получить обычный портландцемент и добавьте гипс и летучую золу для получения пуццолана. Портландцемент.
Применения в производстве цемента мокрым способом
Метод производства цемента мокрым способом может использоваться для производства различных типов портландцемента, таких как обычный портландцемент, белый портландцемент, цемент для нефтяных скважин и т. Д.Это может помочь вашему цементному заводу производить высококачественный цемент с высокой производительностью.
Производство обычного портландцемента Производство белого цемента Производство цемента для нефтяных скважинPS: Нажмите на картинку, чтобы узнать больше.
Производство портландцемента — материалы и процессы
При производстве цемента используются различные сырьевые материалы и различные процессы. Каждый процесс объясняется химическими реакциями при производстве портландцемента.
Цемент представляет собой порошок зеленовато-серого цвета, изготовленный из кальцинированной смеси глины и известняка. При смешивании с водой становится твердым и прочным строительным материалом.
История цемента восходит к Римской Империи. Современный цемент. То есть портландцемент был впервые произведен британским каменщиком Джозефом Аспдином в 1824 году, который варил цемент на своей кухне. Он нагрел смесь известняка и глиняного порошка на своей кухне и измельчил смесь в порошок, создав цемент, который затвердевает при смешивании с водой.Название Портленд было дано изобретателем, так как он напоминает камень, добытый на острове Портленд.
Впервые современный портландцемент был использован при строительстве туннеля в Темзе в 1828 году.
Процесс производства цементаПроцесс производства портландцемента описан ниже.
- Смешивание сырья
- горит
- Шлифовальный
- Хранение и упаковка
1.Смешивание сырья
Основным сырьем, используемым при производстве цемента, являются кальций, кремний, железо и алюминий. Эти минералы используются в различных формах в зависимости от наличия минералов.
В таблице показано сырье для производства портландцемента
Процесс смешивания при производстве цемента осуществляется 2 способами,
a) Сухой процессИзвестковое и глинистое сырье сначала измельчается в гирационных дробилках, чтобы раздельно получить куски размером 2-5 см.Измельченный материал снова измельчается, чтобы получить мелкие частицы в шаровой или трубчатой мельнице.
Каждый мелко измельченный материал после просеивания хранится в бункере. Теперь эти порошкообразные минералы смешиваются в требуемой пропорции, чтобы получить сухую сырьевую смесь, которая затем хранится в силосах и готовится к отправке во вращающуюся печь. Теперь сырье смешивается в определенных пропорциях, так что средний состав конечного продукта сохраняется должным образом.
Рис. Производство цемента сухим способом
b) Мокрый процессСырье сначала измельчается, превращается в порошок и хранится в силосах.Затем глину промывают в стиральных мельницах, чтобы удалить приставшие органические вещества, содержащиеся в глине.
Порошкообразный известняк и промытая водой глина направляются в каналы и передаются в мельницы, где они полностью смешиваются и образуется паста, известная как суспензия.
Процесс измельчения может производиться в шаровой или трубчатой мельнице или даже в том и другом. Затем суспензия направляется в сборный резервуар, где можно регулировать состав. Суспензия содержит около 38-40% воды, которая хранится в резервуарах для хранения и хранится в готовности для вращающейся печи.
Рис. Производство цемента мокрым способом
Сравнение сухого процесса и мокрого процесса производства цемента
Критерии | Сухой процесс | Мокрый процесс |
Твердость сырья | Довольно сложно | Любое сырье |
Расход топлива | Низкий | Высокая |
Время обработки | Малый | Высшее |
Качество | Низкое качество | Превосходное качество |
Себестоимость продукции | Высокая | Низкий |
Общая стоимость | Дорогостоящие | Дешевле |
Физическое состояние | Сырьевая смесь (твердая) | Шлам (жидкий) |
2.Сжигание сырья
Процесс обжига осуществляется во вращающейся печи, в то время как сырье вращается со скоростью 1-2 об / мин на ее продольной оси. Вращающаяся печь состоит из стальных труб диаметром 2,5-3,0 метра и длиной от 90 до 120 метров. Внутренняя сторона печи выложена огнеупорным кирпичом.
Печь опирается на колонны из кирпича или бетона и опирается на роликовый подшипник в слегка наклонном положении с уклоном от 1: 25 до 1: 30.Сырьевая смесь сухого процесса или скорректированного шлама мокрого процесса вводится в печь с верхнего конца. Печь нагревается с помощью порошкообразного угля, масла или горячих газов из нижнего конца печи, так что возникает длинное горячее пламя.
Поскольку положение печи наклонено и она медленно вращается, материал, загружаемый с верхнего конца, перемещается к нижнему концу со скоростью 15 м / час. В верхней части вода или влага из материала испаряются при температуре 400 ° C, поэтому этот процесс известен как зона сушки.
Центральная часть, т.е. зона обжига, температура около 10 000 ° C, где происходит разложение известняка. Оставшийся материал находится в форме небольших комков, известных как узелки после выхода CO 2 .
CaCO 3 = CaO + CO 2
Нижняя часть (зона клинкера) имеет температуру в пределах 1500-17000 ° C, где известь и глина вступают в реакцию с образованием алюминатов кальция и силикатов кальция. Эти алюминаты и силикаты кальция плавятся, собираясь в мелкие и твердые камни, известные как клинкеры.Размер клинкера варьируется от 5 до 10 мм.
Нижняя часть, т.е. зона клинкера, имеет температуру около 1500-1700С. В этом регионе известь и глина реагируют с образованием алюминатов кальция и силикатов кальция. Эти продукты из алюминатов и силикатов кальция плавятся вместе, образуя твердые и мелкие камни, известные как клинкеры. Размер мелкого и твердого клинкера колеблется от 5 до 10 мм.
2CaO + SiO 2 = Ca2SiO 4 (силикат декламированный (C 2 S))
3CaO + SiO 2 = Ca3SiO 5 (трехкальциевый силикат (C 3 S))
3CaO + Al 2 O 3 = Ca 3 Al 2 O 6 (алюминат дикальция (C 2 A))
4CaO + Al 2 O 3 + Fe 2 O 3 = Ca 4 Al 2 Fe 2 O 10 (тетракальцийалюмоферрит (C 4 AF)
Клинкер, поступающий из зоны обжига, очень горячий.Чтобы снизить температуру клинкера, воздух пропускается противотоком в основании вращающейся печи. Остывшие клинкеры собирают в небольшие тележки.
3. Измельчение клинкера
Охлажденный клинкер поступает из охлаждающих ванн и отправляется в мельницы. Клинкеры тонко измельчаются в порошок в шаровой или трубчатой мельнице. Порошковый гипс добавляется около 2-3% в качестве замедлителя при окончательном измельчении. Конечным продуктом является цемент, который не быстро оседает при контакте с водой.
По истечении начального времени схватывания цемента цемент становится жестким, а гипс замедляет растворение трикальциевых алюминатов, образуя трикальцийсульфоалюминат, который нерастворим и предотвращает слишком ранние дальнейшие реакции схватывания и твердения.
3CaO.Al 2 O 3 + xCaSO 4 .7H 2 O = 3CaO.Al 2 O 3 .xCaSO 4 .7H 3 2 O 9000
4. Хранение и упаковкаИзмельченный цемент хранится в силосах, откуда он продается либо в контейнерах, либо в мешках по 50 кг.
Страница не найдена для Manufacture_process_of_cement
Имя пользователя*
Эл. адрес*
Пароль*
Подтвердите Пароль*
Имя*
Фамилия*
Страна Выберите страну … Аландские острова IslandsAfghanistanAlbaniaAlgeriaAndorraAngolaAnguillaAntarcticaAntigua и BarbudaArgentinaArmeniaArubaAustraliaAustriaAzerbaijanBahamasBahrainBangladeshBarbadosBelarusBelauBelgiumBelizeBeninBermudaBhutanBoliviaBonaire, Санкт-Эстатиус и SabaBosnia и HerzegovinaBotswanaBouvet IslandBrazilBritish Индийского океана TerritoryBritish Virgin IslandsBruneiBulgariaBurkina FasoBurundiCambodiaCameroonCanadaCape VerdeCayman IslandsCentral африканского RepublicChadChileChinaChristmas IslandCocos (Килинг) IslandsColombiaComorosCongo (Браззавиль) Конго (Киншаса) Кук IslandsCosta RicaCroatiaCubaCuraÇaoCyprusCzech RepublicDenmarkDjiboutiDominicaDominican RepublicEcuadorEgyptEl SalvadorEquatorial GuineaEritreaEstoniaEthiopiaFalkland IslandsFaroe IslandsFijiFinlandFranceFrench GuianaFrench PolynesiaFrench Южный Территория нг КонгВенгрияИсландияИндияИндонезияИранИракОстров МэнИзраильИталия Кот-д’ИвуарЯмайкаЯпонияДжерсиИорданияКазахстанКенияКирибатиКувейтКиргизияЛаосЛатвияЛебанЛезотоЛиберияЛибияоЛихтенштейнЛихтенштейнЛитва ЮжныйAR, ChinaMacedoniaMadagascarMalawiMalaysiaMaldivesMaliMaltaMarshall IslandsMartiniqueMauritaniaMauritiusMayotteMexicoMicronesiaMoldovaMonacoMongoliaMontenegroMontserratMoroccoMozambiqueMyanmarNamibiaNauruNepalNetherlandsNetherlands AntillesNew CaledoniaNew ZealandNicaraguaNigerNigeriaNiueNorfolk IslandNorth KoreaNorwayOmanPakistanPalestinian TerritoryPanamaPapua Новый GuineaParaguayPeruPhilippinesPitcairnPolandPortugalQatarRepublic из IrelandReunionRomaniaRussiaRwandaSão Tomé и PríncipeSaint BarthélemySaint HelenaSaint Китса и NevisSaint LuciaSaint Мартин (Голландская часть) Сен-Мартен (французская часть) Сен-Пьер и MiquelonSaint Винсент и GrenadinesSan MarinoSaudi ArabiaSenegalSerbiaSeychellesSierra LeoneSingaporeSlovakiaSloveniaSolomon IslandsSomaliaSouth AfricaSouth Грузия / Sandwich ОстроваЮжная КореяЮжный СуданИспанияШри-ЛанкаСуданСуринамШпицберген и Ян-МайенСвазилендШвецияШвейцарияСирияТайваньТаджикистанТанзанияТаиландТимор-ЛештиТогоТокелауТонгаТринидад и ТобагоТунисТурция ТуркменистанТуркс и Острова КайкосТувалуУгандаУкраинаОбъединенные Арабские ЭмиратыВеликобритания (Великобритания) США (США) УругвайУзбекистанВануатуВатиканВенесуэлаВьетнамУоллис и ФутунаЗападная СахараЗападное СамоаЙеменЗамбияЗимбабве
Captcha *Регистрируясь, вы соглашаетесь с Условиями использования и Политикой конфиденциальности.*
Страница не найдена для 1_mixing_of_raw_material
Имя пользователя*
Эл. адрес*
Пароль*
Подтвердите Пароль*
Имя*
Фамилия*
Страна Выберите страну … Аландские острова IslandsAfghanistanAlbaniaAlgeriaAndorraAngolaAnguillaAntarcticaAntigua и BarbudaArgentinaArmeniaArubaAustraliaAustriaAzerbaijanBahamasBahrainBangladeshBarbadosBelarusBelauBelgiumBelizeBeninBermudaBhutanBoliviaBonaire, Санкт-Эстатиус и SabaBosnia и HerzegovinaBotswanaBouvet IslandBrazilBritish Индийского океана TerritoryBritish Virgin IslandsBruneiBulgariaBurkina FasoBurundiCambodiaCameroonCanadaCape VerdeCayman IslandsCentral африканского RepublicChadChileChinaChristmas IslandCocos (Килинг) IslandsColombiaComorosCongo (Браззавиль) Конго (Киншаса) Кук IslandsCosta RicaCroatiaCubaCuraÇaoCyprusCzech RepublicDenmarkDjiboutiDominicaDominican RepublicEcuadorEgyptEl SalvadorEquatorial GuineaEritreaEstoniaEthiopiaFalkland IslandsFaroe IslandsFijiFinlandFranceFrench GuianaFrench PolynesiaFrench Южный Территория нг КонгВенгрияИсландияИндияИндонезияИранИракОстров МэнИзраильИталия Кот-д’ИвуарЯмайкаЯпонияДжерсиИорданияКазахстанКенияКирибатиКувейтКиргизияЛаосЛатвияЛебанЛезотоЛиберияЛибияоЛихтенштейнЛихтенштейнЛитва ЮжныйAR, ChinaMacedoniaMadagascarMalawiMalaysiaMaldivesMaliMaltaMarshall IslandsMartiniqueMauritaniaMauritiusMayotteMexicoMicronesiaMoldovaMonacoMongoliaMontenegroMontserratMoroccoMozambiqueMyanmarNamibiaNauruNepalNetherlandsNetherlands AntillesNew CaledoniaNew ZealandNicaraguaNigerNigeriaNiueNorfolk IslandNorth KoreaNorwayOmanPakistanPalestinian TerritoryPanamaPapua Новый GuineaParaguayPeruPhilippinesPitcairnPolandPortugalQatarRepublic из IrelandReunionRomaniaRussiaRwandaSão Tomé и PríncipeSaint BarthélemySaint HelenaSaint Китса и NevisSaint LuciaSaint Мартин (Голландская часть) Сен-Мартен (французская часть) Сен-Пьер и MiquelonSaint Винсент и GrenadinesSan MarinoSaudi ArabiaSenegalSerbiaSeychellesSierra LeoneSingaporeSlovakiaSloveniaSolomon IslandsSomaliaSouth AfricaSouth Грузия / Sandwich ОстроваЮжная КореяЮжный СуданИспанияШри-ЛанкаСуданСуринамШпицберген и Ян-МайенСвазилендШвецияШвейцарияСирияТайваньТаджикистанТанзанияТаиландТимор-ЛештиТогоТокелауТонгаТринидад и ТобагоТунисТурция ТуркменистанТуркс и Острова КайкосТувалуУгандаУкраинаОбъединенные Арабские ЭмиратыВеликобритания (Великобритания) США (США) УругвайУзбекистанВануатуВатиканВенесуэлаВьетнамУоллис и ФутунаЗападная СахараЗападное СамоаЙеменЗамбияЗимбабве
Captcha *Регистрируясь, вы соглашаетесь с Условиями использования и Политикой конфиденциальности.*
Страница не найдена для 2_burning_of_raw_materials
Имя пользователя*
Эл. адрес*
Пароль*
Подтвердите Пароль*
Имя*
Фамилия*
Страна Выберите страну … Аландские острова IslandsAfghanistanAlbaniaAlgeriaAndorraAngolaAnguillaAntarcticaAntigua и BarbudaArgentinaArmeniaArubaAustraliaAustriaAzerbaijanBahamasBahrainBangladeshBarbadosBelarusBelauBelgiumBelizeBeninBermudaBhutanBoliviaBonaire, Санкт-Эстатиус и SabaBosnia и HerzegovinaBotswanaBouvet IslandBrazilBritish Индийского океана TerritoryBritish Virgin IslandsBruneiBulgariaBurkina FasoBurundiCambodiaCameroonCanadaCape VerdeCayman IslandsCentral африканского RepublicChadChileChinaChristmas IslandCocos (Килинг) IslandsColombiaComorosCongo (Браззавиль) Конго (Киншаса) Кук IslandsCosta RicaCroatiaCubaCuraÇaoCyprusCzech RepublicDenmarkDjiboutiDominicaDominican RepublicEcuadorEgyptEl SalvadorEquatorial GuineaEritreaEstoniaEthiopiaFalkland IslandsFaroe IslandsFijiFinlandFranceFrench GuianaFrench PolynesiaFrench Южный Территория нг КонгВенгрияИсландияИндияИндонезияИранИракОстров МэнИзраильИталия Кот-д’ИвуарЯмайкаЯпонияДжерсиИорданияКазахстанКенияКирибатиКувейтКиргизияЛаосЛатвияЛебанЛезотоЛиберияЛибияоЛихтенштейнЛихтенштейнЛитва ЮжныйAR, ChinaMacedoniaMadagascarMalawiMalaysiaMaldivesMaliMaltaMarshall IslandsMartiniqueMauritaniaMauritiusMayotteMexicoMicronesiaMoldovaMonacoMongoliaMontenegroMontserratMoroccoMozambiqueMyanmarNamibiaNauruNepalNetherlandsNetherlands AntillesNew CaledoniaNew ZealandNicaraguaNigerNigeriaNiueNorfolk IslandNorth KoreaNorwayOmanPakistanPalestinian TerritoryPanamaPapua Новый GuineaParaguayPeruPhilippinesPitcairnPolandPortugalQatarRepublic из IrelandReunionRomaniaRussiaRwandaSão Tomé и PríncipeSaint BarthélemySaint HelenaSaint Китса и NevisSaint LuciaSaint Мартин (Голландская часть) Сен-Мартен (французская часть) Сен-Пьер и MiquelonSaint Винсент и GrenadinesSan MarinoSaudi ArabiaSenegalSerbiaSeychellesSierra LeoneSingaporeSlovakiaSloveniaSolomon IslandsSomaliaSouth AfricaSouth Грузия / Sandwich ОстроваЮжная КореяЮжный СуданИспанияШри-ЛанкаСуданСуринамШпицберген и Ян-МайенСвазилендШвецияШвейцарияСирияТайваньТаджикистанТанзанияТаиландТимор-ЛештиТогоТокелауТонгаТринидад и ТобагоТунисТурция ТуркменистанТуркс и Острова КайкосТувалуУгандаУкраинаОбъединенные Арабские ЭмиратыВеликобритания (Великобритания) США (США) УругвайУзбекистанВануатуВатиканВенесуэлаВьетнамУоллис и ФутунаЗападная СахараЗападное СамоаЙеменЗамбияЗимбабве
Captcha *Регистрируясь, вы соглашаетесь с Условиями использования и Политикой конфиденциальности.*
Производство цемента — обзор
Причина и химия
Подкисление океана является прямым следствием увеличения выбросов CO 2 в атмосферу. Выбросы CO 2 значительно увеличились со времени промышленной революции из-за увеличения объемов сжигания ископаемого топлива, производства цемента и изменений в землепользовании, что привело к увеличению годового накопления CO 2 в атмосфере. Из-за увеличения концентрации CO 2 в атмосфере за последние 200 лет океан поглощает огромное количество антропогенного CO 2 ; в настоящее время это составляет около миллиона метрических тонн CO 2 в час (Brewer, 2009), что эквивалентно 25% накопленных выбросов CO 2 (Sabine et al., 2004; Ле Кере и др., 2009). Без поглощения океаном атмосферный CO 2 сейчас составлял бы около 450 частей на миллион, что примерно на 60 частей на миллион выше, чем сегодня. Хотя этот процесс частично сдерживает изменение климата за счет удаления CO 2 из атмосферы, он имеет серьезные последствия для химического состава океана.
Диоксид углерода (CO 2 , <1%), угольная кислота (H 2 CO 3 , <1%), бикарбонат-ионы (HCO3-, 91%) и карбонат-ионы (CO32-, 8 %) содержат формы растворенного неорганического углерода в морской воде при среднем значении pH морской воды 8.1 и соленость 35. Они происходят в динамическом равновесии, реагируя с водой и ионами водорода (уравнение 2.1; Zeebe and Wolf-Gladrow, 2001).
(2.1) CO2 + h3O↔h3CO3↔H ++ HCO3 − ↔H ++ CO32−
При обмене с атмосферой растворенный CO 2 вступает в реакцию с морской водой и карбонат-ионами с образованием угольной кислоты (уравнение 2.1). Общее увеличение выбросов в атмосферу приводит к увеличению на концентрации растворенного CO 2 , угольной кислоты и бикарбоната на , как и следовало ожидать из уравнения (2.1). Концентрации ионов водорода (H + ) также увеличиваются на на , таким образом, pH, мера концентраций H + падает, а кислотность увеличивается на . Следует отметить, что pH океана вряд ли станет кислым (то есть станет ниже pH 7), а термин «подкисление» отражает процесс повышения кислотности, так же как потепление отражает процесс повышения температуры, хотя это может быть из-за холода. чтобы не совсем так холодно.
Кроме того, что очень важно, наблюдается снижение на и концентрации карбонат-ионов, поскольку также происходит реакция между CO 2 и карбонатом, дополнительно на повышается уровней бикарбонатов:
(2.2) CO2 + CO32− + h3O → 2HCO3−
Другой ключевой результат снижения концентрации карбоната (CO32–) на заключается в том, что это увеличивает на скорость растворения минералов карбоната кальция (CaCO 3 ) в океан, с чистым эффектом:
(2.3) CaCO3 + CO2 + h3O → Ca2 ++ 2HCO3–
Состояние насыщения (Ω) используется для выражения степени насыщения CaCO 3 в морской воде:
(2,4) Ω = Ca2 + CO32− / Ksp
, где [Ca 2 + ] и [CO32−] — это концентрации кальция и карбоната in situ, , соответственно, а K sp — растворимость продукт для CaCO 3 (концентрации в состоянии равновесия, ни растворения, ни образования).Значения K sp зависят от кристаллической формы CaCO 3 ; они также меняются в зависимости от температуры и давления, при этом CaCO 3 необычен тем, что он более растворим в холодной воде, чем в теплой. Незащищенные раковины, скелеты и другие структуры карбоната кальция начинают растворяться, когда Ω падает ниже 1 для соответствующей минеральной фазы. Ω больше 1 соответствует пересыщению. Горизонт насыщения отделяет перенасыщенные воды (вверху) от недонасыщенных (внизу) вод и, по прогнозам, будет двигаться вверх к поверхности океана (мелководье) в результате этих изменений в химическом составе карбонатов океана, в результате чего большее количество организмов будет подвергаться воздействию коррозионных недонасыщенных вод. (Орр и др., 2005; Turley et al., 2007).
pH описывает концентрацию или, точнее, активность иона водорода в воде, a H , логарифмической функцией:
(2,5) pHT = −log10aH +
Активность ионов водорода важна для всех кислотно-основных реакций. Используется общая шкала pH (pH T ).
Эти изменения химического состава океана являются прямым следствием увеличения выбросов CO 2 в атмосферу и, несомненно, основаны на известных химических реакциях.Степень подкисления океана в будущем будет зависеть от концентраций и скорости выбросов CO 2 , и, если они известны, степень подкисления очень предсказуема (Caldeira and Wickett, 2003; Orr et al., 2005; Joos et al. , 2011).
Мокрый процесс производства цемента
Танви Лад — старший менеджер (гражданское дело). Она получила степень бакалавра в области гражданского строительства в 2013 году. Она возглавляет отдел оценки и тендеров SDCPL. Она следит за обзором проектов, калькуляцией, оценкой, тендером, оценкой тендера и детальным проектированием жилых, коммерческих и инфраструктурных работ.Она также ведет блог на gharpedia.com. С ней можно связаться в LinkedIn, Twitter.
Этот пост также доступен на: हिन्दी (хинди)
При мокром процессе, если используется мел, он тонко измельчается и диспергируется в воде в промывочной мельнице. Промывочная мельница представляет собой круглую яму, состоящую из вращающихся радиальных рычагов с граблями, которые разбивают твердые материалы на комки. В аналогичной промывочной мельнице глина также измельчается и смешивается с водой. Теперь две смеси перекачиваются так, чтобы смешаться в заданной пропорции, и пропускаются через серию сит.Полученный цементный раствор стекает в резервуары для хранения.
Необходимо прочитать: Сухой процесс производства цемента
Когда используется известняк, сначала необходимо его взорвать, затем измельчить в двух дробилках постепенно уменьшающихся размеров, а затем подать в шаровую мельницу с глиной, диспергированной в воде. Полученная суспензия перекачивается в резервуары для хранения.
Суспензия представляет собой жидкость кремообразной консистенции с содержанием воды от 35 до 50 процентов и небольшой фракцией материала примерно на 2 процента больше, чем размер сита 90 мкм.Для хранения навозной жижи предусмотрено несколько резервуаров. Осаждение взвешенных твердых частиц предотвращается механическими мешалками или барботированием сжатым воздухом.
Шлам с желаемым содержанием извести поступает во вращающуюся печь. Это большой, огнеупорная футеровка стального цилиндр, имеющий диаметр до 8 м, а иногда до тех пор, как 230 м. Стальной цилиндр медленно вращается вокруг своей оси и немного наклонен к горизонтали. Суспензия подается в печь с верхнего конца, а пылевидный уголь вдувается воздушной струей в нижний конец печи, где температура составляет около 1450 ° C.Уголь, используемый в печи, не должен иметь слишком высокое содержание золы, потому что 220 кг угля используется для производства одной тонны цемента. Это достойно при учете количества цемента.
Сухой материал подвергается серии химических реакций в самой горячей части печи, и от 20 до 30 процентов материала становится жидким, а известь, кремнезем и глинозем рекомбинируют. Расплавленная масса превращает плавкие предохранители в шары диаметром от 3 до 25 мм, известные как клинкер. Клинкер попадает в охладители, где охлаждается в контролируемых условиях.Охлажденный клинкер и 3-5 процентов гипса измельчаются в шаровой мельнице до требуемой степени измельчения, а затем отправляются в силосы для хранения, откуда цемент расфасовывается в мешки.
Печь должна работать непрерывно, чтобы обеспечить стабильный режим и, следовательно, однородность клинкера. Большая существующая печь на заводе мокрого процесса производит 3600 тонн клинкера в день.
Производство цемента мокрым способом энергоемко и поэтому неэкономично по сравнению с сухим и полусухим способом.
Также читайте: OPC против PPC: как сделать правильный выбор
Танви Лад — старший менеджер (гражданский).