Технология производства и изготовления пеноблоков
Производство пенобетонных блоков состоит из нескольких основных стадий, таких как: затворение пенобетонной смеси, формовка, сушка, распалубка, распиловка, термообработка, упаковка, складирование и так далее. В зависимости от выбора технологии изготовления пеноблоков и имеющегося оборудования, производители используют различные комбинации и варианты перечисленных стадий. Начнем по порядку.
Производство пенобетонной смеси
Современное производство пенобетонной смеси можно поделить на два основных вида: баротехнология и получение пенобетона с помощью пеногенератора. Каждая из технологий имеет свои плюсы и минусы. Первая более проста и экономична. Вторая более затратна, но позволяет получать пенобетон более высокого качества. Более подробно об плюсах и минусах этих двух технологий Вы можете прочитать в разделе производство пенобетона.
Формовка пеноблоков
На сегодняшний момент существует две основных технологии получения готовых пенобетонных блоков: литьевая и резательная.
Литьевая технология Литьевой способ производства пеноблоков очень похож на классическое изготовление изделий из железобетона, при котором готовая бетонная смесь отливается в металлическую форм-оснастку, сушится до набора необходимой прочности и затем вынимается из форм уже в виде готового изделия.
При производстве пеноблоков по литьевой технологии используются кассетные формы, представляющие из себя металлический поддон со съемными бортами и переборками, делящими форму на несколько отдельных секций. Похожая кассетная форма для приготовления льда лежит у Вас в холодильнике. Почти такая же применяется и на производстве пенобетонных блоков, только из металла, разборная и размером побольше. Чаще всего используются кассетные формы высотой 600 мм.
Главными минусами литьевой технологии являются:
- Неудовлетворительная геометрия готовых пеноблоков. То есть, габариты пенобетонных блоков по высоте, длине и ширине «пляшут». Происходит это из-за смещения металлических переборок при заливке пенобетонной смеси в кассету.
Как правило, переборки сделаны из тонкого металла и при неравномерной заливке они могут смещаться, деформироваться и т.д.
Конечно же существуют качественные блок-формы, с переборками из толстой листовой стали, отлично подогнанные по размерам. Но такие формы дороги, и многочисленные кустари используют дешевые покупные или самодельные формы. Более подробно о возможных проблемах с геометрией изделий из пенобетона читайте в разделе размеры пеноблоков.
- Наличие так называемой «горбушки». Горбушка образовывается в верхнем слое залитой кассеты. Для примера вспомните кубики льда из холодильника, верхняя часть которых имеет неровную поверхность. Аналогично образуется неровность и на поверхности застывшего пенобетона. Многие наверное помнят верхнюю часть плит перекрытий и тому подобных железобетонных изделий, у которых все стороны ровные кроме одной — верхней, которая не «обжимается» опалубкой. Горбушку на пеноблоках, изготовленных по литьевой технологии, почти всегда можно обнаружить на одном из торцов.
- Необходимость использования специализированных переборок для кассет, заточенных под конкретный размер пеноблоков. Для того, чтобы выпускать три-четыре размера пенобетонных блоков, производители должны иметь несколько видов переборок с разными размерами ячеек.
- При распалубке кассет происходит частичное повреждение углов и поверхностей готовых блоков. Происходит это из-за прилипания пенобетона к стенкам кассеты, так как к моменту распалубки пенобетон не успевает набрать достаточной прочности. Время-деньги. Нужно побыстрее вынуть едва вставшие блоки, чтобы залить очередную партию.
Из плюсов литьевой технологии производства пенобетонных блоков можно выделить лишь экономическую выгоду для производителя: отсутствие необходимости приобретения дорогостоящего резального оборудования и простота процесса. Впрочем, для конечного потребителя это преимущество не имеет никакого значения.
Резательная технология Подобный способ производства пеноблоков состоит из двух ступеней: отливка массива пенобетона в большую форму и его распалубка с дальнейшей резкой на блоки заданного размера. Происходит это на специальных резательных установках. В различных типах резательных установок используются разные виды режущих элементов. Это могут быть специальные струны, ленточные и цепные пилы.
Эта технология производства пенобетонных блоков обладает целым рядом преимуществ. Вот основные из них:
- Великолепная геометрия поверхностей получаемых пеноблоков, соответствующая требованиям ГОСТ 21520-89. Благодаря этому, блоки можно монтировать на клей с минимальной толщиной шва.
- На гранях и углах пеноблоков отсутствуют сколы и неровности. Этот нюанс особенно важен для сокращения расходов и трудозатрат при дальнейшей отделке стен.
- За счет отсутствия на поверхностях блоков остатков смазки (а тем более масляной обработки) которой смазываются формы-кассеты, готовые стеновые блоки обладают хорошей адгезией и привлекательным внешним видом. И если внешние данные не столь важны, то хорошая адгезия пеноблока — один из важнейших критериев успешного оштукатуривания или шпатлевания стены при проведении внешней и внутренней отделки дома.
- Возможность изготовления пеноблоков произвольных размеров. Перенастройка шага пильных струн позволяет нарезать готовые блоки по размерам заказчика.
- Благодаря обрезке массива пенобетона со всех сторон, решается и проблема с пресловутой «горбушкой» на торце блока. Она просто срезается.
Впрочем, есть у резательной технологии и свои неприятные моменты. При использовании разных видов режущих элементов должны быть четко соблюдены определенные требования к своевременности проведения резки.
При разрезке пенобетона ленточными пилами массив наоборот должен иметь более высокую прочность, так как при резке он кантуется (переворачивается на резальном столе). И если прочность будет недостаточной, он просто будет ломаться при кантовании.
Перечисленные проблемы скорее досаждают производителям пенобетонных блоков, нежели их конечным потребителям. В любом случае, Ваша главная задача — сделать правильный выбор.
Сушка пеноблоков и набор прочности
При производстве блоков из пенобетона литьевым способом возможны две технологии первоначальной сушки изделий. Первый вариант — естественная сушка, подразумевающая 10 часовой набор прочности пенобетона в форме и его дальнейшая распалубка. Второй вариант — термическая обработка пенобетонных блоков в пропарочной камере. В отличие от естественной сушки, пропарка в камере позволяет пенобетону за несколько часов набрать 65-75% расчетной прочности.
Стоит заметить, что по подобной технологии производятся почти все железобетонные изделия. Группа BESTO поставляет пеноблоки, произведенные с применением термо-влажностной обработки в пропарочных камерах. Производство пеноблоков расположено на территории завода ЖБИ-16 в Москве.
Резательная технология производства пенобетонных блоков подразумевает естественную сушку массива в течение 4-14 часов с дальнейшей его разрезкой. Время сушки перед разрезкой зависит от использования того или иного вида режущих элементов (струны, ленточные пилы, цепи), а так же ускорителей твердения, добавляемых в пенобетонную смесь при затворении.
Производство пеноблоков в домашних условиях
Пенобетон востребован в строительстве, как недорогой, но качественный материал. Он легкий, хорошо сохраняет тепло, обладает неплохими звукоизоляционными качествами. Пеноблоки пожаробезопасны, имеют очень низкие коэффициенты водопоглощения и усадки, хорошо переносят любые атмосферные изменения. Технология производства довольна проста и экологически чиста, поэтому изготовление и продажа блоков может стать выгодным домашним бизнесом.
Материалы для пенобетона
Производство пеноблоков в домашних условиях требует определенных затрат. На производство 1 кубического метра (или 720 литров пены) необходимы:
- Цемент. В среднем требуется около трехсот кг. Ячеистый бетон (это еще одно название блоков) может иметь разную плотность, поэтому для изготовления пенобетона разного назначения и плотности необходим цемент различных марок. Каких именно, определяют Госстандарты и Технические условия. Ниже вы увидите таблицу, в которой указаны необходимые параметры цемента.
- Песок очищенный, речной: около 200 кг.
- Вода: 100 литров + 50 литров для пены.
- Пенообразователь (синтетический или из натуральных составляющих): — около двух литров в зависимости от плотности блоков.
Самыми популярными и доступными по цене являются пенообразователи ПБ 2000 или «Люкс»(УСХК), СДО-М (ООО Технология), FOAMIN C (Италия), «Форвард» (ООО Роскосметика).
- Отвердитель.
- Смазка для форм.
Оборудование для производства пеноблоков
Для того чтобы своими руками изготавливать блоки, придется приобрести оборудование. Потребуются:
- Парогенератор, способный производить не меньше 200 литров в минуту.
- Компрессорная установка.
- Бункер -мешалка. Для начинающих предпринимателей достаточно агрегата мощностью 2,2кВт и рабочим объемом около 280 литров.
- Форма для стандартных блоков 200х300х600мм.
- Вспомогательные приборы: манометры, насосы.
Оборудование в виде готового комплекта можно купить в специальных магазинах. Можно так же сделать оборудование под заказ. Второй способ намного дороже и финансово оправдан только тогда, когда домашнее производство вышло на полную мощность.
При организации производства следует оборудовать помещение для сушки готовых блоков. Важно так же учесть общую потребляемую мощность, чтобы обеспечить бесперебойную работу оборудования.
Технология изготовления пенобетонных блоков своими руками
На одной установке можно изготавливать блоки разной плотности. В зависимости от того, в каких пропорциях взяты составляющие, можно получить ячеистый бетон плотностью от 200 до 1500 килограммов на квадратный метр.
Схема производственного процесса очень проста. В ней можно выделить три самостоятельных процесса:
- Приготовление песчано-цементной смеси. Пропорции зависят от предполагаемой плотности готового материала, которая определяется ГОСТами и техническими условиями. Для получения средней плотности обычно берут равные количества цемента и песка.
- Приготовление раствора- пенообразователя. Для блоков средней плотности достаточно 4-5 граммов концентрированного пенообразователя.
- Разливка полученной смеси по стандартным формам.
Подготовка смеси из песка и цемента
Для приготовления смеси берут портландцемент М-400, 500 и мелкий, без глинистых примесей кварцевый песок. Воду можно брать водопроводную: она чаще всего свободна от кислотных или щелочных примесей. Примерные пропорции для получения пенобетона, соответствующего ГОСТ21520-89 и 25485-89 указаны в таблице:
Рекомендуемые пропорции смеси для получения 1 кубометра ячеистого бетона | ||||||
Плотность, кг/м3 | 400 | 600 | 800 | 1000 | 1200 | 1400 |
Пропорция цемента и воды | — | 0.41 | 0.44 | 0.46 | 0.5 | — |
Количество воды | 400 | 600 | 800 | 1000 | 1200 | 1400 |
Плотность, кг/м3 | 165 | 155 | 185 | 215-220 | 235 | 265 |
Количество цемента | 361 | 361 | 481 | 581 | 651 | 690 |
Количество песка | — | 155 | 205 | 281 | 381 | 600 |
Количество концентрата | 1.![]() | 1.0 | 0.95 | 0.9 | 0.85 | 0.7 |
К содержанию ↑
Подготовка пенообразователя
Если в производстве используется готовый пенообразователь, то его достаточно смешать с водой, чтобы получить готовый рабочий состав. Пенообразователь некоторые делают сами. Цена его получается меньше, но трудовые затраты — больше.
Как сделать пенообразователь самостоятельно? Измельчить и смешать 150 г едкого натра, килограмм канифоли и 60 граммов столярного клея. Состав подогревается и перемешивается до однородной консистенции. Учитывая, что на изготовление такого пенообразователя уходит довольно много времени и сил, экономически целесообразно, считают многие предприниматели, покупать готовый пенообразователь.
К содержанию ↑Подготовка форм
Обычно формы входят в готовый набор оборудования, предназначенного для создания пеноблоков. Однако их можно самостоятельно изготовить из фанеры или листового железа. В этом случае важно точно соблюсти геометрическую форму форм: иначе готовые блоки не будут соответствовать требованиям. Для смазки можно использовать эмульсии, растворы или суспензии.
Растворы можно готовить из веретенного масла или солидола, автола или петролатума, разведенных в керосине или масле (соляровом).
К суспензиям относятся готовые цементно-маслянные, известковые, меловые, графитовые и т.п. смазки.
К содержанию ↑Эмульсии могут быть двух видов
Первые можно изготовить:
- Из 10-15% гигрола 3 марки, 1% хозяйственного мыла и 85-89% воды.
- 10% кислого синтетического эмульсола, 0,6% соды и 89% воды.
Вторые изготавливают:
- Из эмульсола (20%).
- Солярки (5%-10%).
- Насыщенного раствора извести (70%-75%).
Производство блоков
В бункер-мешалку закладывают смесь из песка и бетона, хорошо перемешивают, медленно добавляют воду и подготовленный пенообразователь, а после образования устойчивой пены — отвердитель. Самым доступным отвердителем является хлористый кальций. Обычно его количество составляет 1%-2% от количества цемента. Через 2-3 минуты перемешивания состав готов. Он заливается (транспортируется) в предварительно обработанные смазкой и сушится 48-60 часов при температуре 50°-60°.
Обучающее видео по производству пеноблоков
На этом видео можете посмотреть процесс производства пеноблоков при помощи готового комплекта оборудования:
Чтобы предотвратить растрескивание поверхности, формы со смесью накрывают полиэтиленовой пленкой. Смесь можно заливать в большие емкости, а затем полувысушенный состав разрезать. Готовые блоки складывают в поддоны и отправляют к месту строительства.
Читайте также:
Оборудование для производства пеноблоков: технология, машины, станки, линии
Производство пеноблоков, как направление бизнеса очень привлекательно.
В первую очередь, постоянной востребованностью продукции, даже в зимний период всегда находятся покупатели.
К другим плюсам этого производства можно отнести повсеместную доступность сырья, а самое главное – низкая себестоимость продукции.
Что такое пеноблокиБлоки с пористой структурой, ровными гранями и четкими ребрами, изготовленные из пенобетона, называют пеноблоками. Такие блоки, благодаря ячеистой структуре, имеют неплохие показатели в качестве не только кладочного, но и утепляющего, и звукоизолирующего материала.
Как делают валенки и что для этого надо? Познакомьтесь, из каких этапов состоит процесс производства валенок, узнайте, чем привлекателен этот бизнес.
Интерес к оборудованию для производства стройматериалов порождает немалый спрос. Здесь видео о технологии производства арболита.
Пеноблоки имеют относительно небольшой объемный вес, что не создает больших нагрузок на перекрытие, если требуется устройство разделительной перегородки.
Используются блоки в любых конструктивных частях зданий и сооружений: при кладке стен подвалов и фундаментов, для возведения наружных и внутренних стен, для устройства перемычек и др.
Кроме уже названных достоинств, пеноблоки еще прочны, биологически стойки к разного рода организмам. Для получения вполне пригодной для реализации продукции требуется срок, не превышающий 3-х дней.
Чтобы сделать такие искусственные камни, нужно иметь песок, цемент, пенообразователь, воду. Все составляющие вполне доступны, даже суспензия алюминиевой пудры, которая и является источником пены, обеспечивающей ячеистость структуры.
Готовые пеноблоки имеют серый цвет, в отличие от газоблоков, окрашенных в белесый светло-серый цвет (из-за добавления в раствор извести).
Технология производства пеноблоков
Никакой сложности технологический процесс по изготовлению блоков не представляет. Нужно выполнить следующие операции:
- приготовить пену;
- сделать раствор из песка, цемента и воды;
- ввести пену в раствор, размешать до получения однородной массы;
- готовый раствор разлить в подготовленные формы;
- дать пеносодержащему раствору набрать прочность;
- достать готовые блоки из форм.
Вышеприведенная технология называется литьевой.
Можно обойтись без применения форм, тогда приготовленный раствор выливают в объемную кассету, где блочная масса достигает требуемой технологией прочности.
После чего специальное устройство с вертикальными и горизонтальными струнами режет массу на блоки.
Эта технология производства пеноблоков дает возможность получить высокую точность размеров блоков, с допусками в 1 мм. Чтобы разрезать массив на 16 блоков с размерами 200х300х600 мм, агрегату потребуется не более 7 минут. Возможно получение блоков других размеров.
Линии по производству пеноблоков
До момента разлива смеси в формы оба технологических метода, литьевой и разрезной, имеют идентичную технологию и оборудование для производства пеноблоков.
Перечень основного оборудования таков: бункер или бадья для смешивания ингредиентов, пеногенератор, дозатор, формы.
Вместо бункера может быть применен баросмеситель, который можно назвать станком.
В таком смесителе составляющие не только перемешиваются, но под давлением готовый раствор доставляется непосредственно в формы, которые могут располагаться на расстоянии до 115 м и на высоте до 40 м.
В этом случае нужен компрессор с комплектом шлангов для подачи воздуха, и шланги для транспортировки раствора.
Установка РСГ-500 представляет собой станок для производства пеноблоков и совмещающий пеногенератор с бункером, в котором взбивается пена, готовится раствор, снова происходит размешивание и сразу может подаваться готовая смесь в формы.
Если предприниматель решит готовить блоки с соблюдением точных размеров и геометрической формы, с минимумом брака и отходов, тогда нужен станок для резки пенобетона, одним из представителей которого может быть комплекс резательный «РК-3″ для распиливания пенобетонных массивов.
Конечно, идеальным компактным, комплексным оборудованием является линия для производства пеноблоков.
Такое оборудование не требует применения физической силы работников, оно весьма производительно, в смену готовый раствор приготавливается, в зависимости от параметров линии, в объеме от 40м3 до 80 м3 за смену.
Автоматика контролирует все процессы технологии, от дозирования компонентов, до контроля плотности массы, так как пеноблоки можно изготовить с разным объемным весом.
О ведущих производителях оборудования
В зависимости от начального капитала предпринимателя, к его услугам как оборудование от отдельных узлов и станков, так и линий, и даже мини-заводов по производству пеноблоков.
Компания «СТС» специализируется на подобном оборудовании, здесь можно приобрести любой станок, линию и даже завод, это один из ведущих отечественных производителей.
Выбор узлов, станков, отдельных агрегатов, что именно и требуется начинающему предпринимателю.
Отличные варианты станков может предложить машиностроительное предприятие “СтройМеханика“, выпускающая пеногенераторы, станции дозирования и целые комплексы по ценам, которые смогут быть доступными даже на старте бизнеса.
Комплектуемые ООО “ТСК“ г.Красноярск наборы оборудования привлекают прежде всего ценовыми рамками, а также лаконичностью. Набор из пеногенератора и смесителя с горизонтальным корпусом – основа начального бизнеса.
Как хранят и транспортируют товары? В материале узнайте, почему так выгодно производство поддонов и в чем значение этого бизнеса.
Какими бывают современные строительные материалы? Стеклопластиковая арматура постепенно вытесняет с рынка стальную. На этой страничке посмотрите видео о производстве стеклопластиковой арматуры.
Колбаса занимает особое место в производстве пищевых товаров. Из материала http://buisiness-oborudovanie.com/dlya-pishheproma/oborudovanie-dlya-proizvodstva-kolbasy/ Вы сможете узнать, каким бывает производство сыровяленых колбас.
Надежный, не требующий больших капиталовложений бизнес по выпуску пеноблоков является одним из самых перспективных направлений. Доступное сырье, простота технологии, получение готовой продукции в течение нескольких дней – отличный выбор сектора для развития малого бизнеса.
Видео о производстве пеноблоков
Republished by Blog Post Promoter
Технология производства пенобетона в домашних условиях
Строительство дома, как правило, сопровождается значительными расходами. Желая оптимизировать их, многие принимают решение выполнять часть работ самостоятельно, в том числе и изготавливать строительный материал. Покупка необходимого количества пеноблоков стоит не дешево.
Разобравшись, в чем заключается технология пенобетона, не составит труда выполнить работы по его изготовлению самостоятельно. Производство ячеистого блока выполняется достаточно легко при правильном подходе.
Последовательность выполняемых работ:
- приготовление раствора из смеси цемента и песка;
- приготовление пенного раствора;
- формирование блоков.
Материалы и инструменты:
бетономешалка;
емкости или формы;
пеногенератор;
цемент;
песок;
затвердитель;
пенообразователь.
Качество будущего изделия напрямую зависит от пропорций, соблюдаемых при заготовке раствора. Песок и цемент следует брать в равных частях, а пенообразователь и затвердитель добавлять в количествах, указанных в инструкции по применению.
Технология производства пенобетона предусматривает подготовку смеси основных ингредиентов (песок, цемент и вода), как это делается для классического варианта бетона.
Далее следует постепенно добавлять пенообразующий раствор. Рекомендовано использовать синтетический пенообразователь или изготавливать его аналог, используя такие составляющие, как канифоль, столярный клей и едкий натрий.
Для приготовления добавки нужно измельчить, перемешать, а затем подогреть ингредиенты. Формирование такой смеси возможно исключительно при наличии пеногенератора. Готовая однородная смесь соединяется с бетоном и формирует состав для создания пеноблоков.
Особенности формирования раствора бетона:
- песок выбирается мелкий, без примесей глины;
- воду можно использовать водопроводную.
Наличие солей и кислот недопустимо;
- оптимальные марки используемого цемента – М400, М500.
Приготовление раствора
Имея все необходимые средства и инструменты, нужно приступать к изготовлению раствора, соблюдая следующие правила:
- бетономешалка должна быть заводского исполнения. Самодельные устройства не всегда могут дать нужный результат;
- для изготовления форм можно взять фанеру, при этом важно соблюдение размеров и пропорций;
- для скорейшего затвердения состава следует воспользоваться ускоряющими средствами. Один из часто используемых ускорителей – хлористый кальций. Его следует добавлять в готовую смесь из бетона и пенообразователя в количестве, равном примерно 2% от общей массы;
- полученные в результате блоки нужно выкладывать на поддоны, после чего отправлять на стройплощадку.
Цемент необходимой марки и речной песок (1:3) засыпаются в бетономешалку. Далее постепенно заливается вода и пенообразователь. После тщательного перемешивания состава следует добавить отвердитель. Спустя 1-2 минуты раствор готов к дальнейшим манипуляциям.
Заливка форм
Перед началом формирования блоков нужно подготовить емкости. Для этого нужно очистить форму от остатков смеси или грязи, после чего смазать ее специальным составом (без масел).
Смазка необходима для того, чтобы готовый блок можно было легко извлечь из формы. С этой же целью можно обтянуть емкость полиэтиленом. Изготовление изделий может выполняться двумя способами: литье и резка.
Литьевая технология формирования блоков
Предусматривает заливку бетонной смеси в металлическую форму, выполняющую роль оснастки. Находясь в металлическом блоке высотой 60см, бетонная смесь высыхает, затвердевает и обретает нужную прочность.
После этого готовое изделие извлекается из формы. Такая технология не требует приобретения дорогостоящего оборудования, однако, имеет ряд недостатков:
- возможно отклонение от геометрических параметров при использовании форм из тонкого металла.
Применение более плотного материала позволит избежать этого недостатка;
- с помощью готовой формы можно изготовить блоки одинакового размера. Получение блоков разной величины возможно с использованием дополнительной оснастки;
- на краях изделия возможно образование изогнутой формы;
- на этапе распалубки блоки могут повредиться из-за недостаточной смазки форм.
Хорошее застывание пенобетона обеспечивает температура в помещении не менее +5 градусов. Спустя сутки после заливки форм можно извлечь готовые изделия, уложить на подготовленные поддоны и оставить их так на 16 часов.
Формирование блоков способом резки
Такой метод подразумевает заливку бетонной смеси в большую форму с последующей нарезкой готового блока на нужные размеры. Преимущества данной технологии:
- возможность получения элементов различной формы в процессе одной заливки и без дополнительных расходов;
- отсутствие сколов и неровностей на углах и гранях, что дает возможность экономить на последующей отделке стен;
- эстетичный внешний вид изделий;
- хорошая адгезия;
- отсутствие «горбов» на крайних блоках.
Данную неровность просто срезают.
После выполнения всех этапов работы, получив блоки нужного размера, можно приступать непосредственно к строительству. Если результат не удовлетворяет своим качеством или прочностью, следует пересмотреть используемое сырье – возможно, оно не соответствует критериям отбора.
Кроме того, причина может быть в несоблюдении пропорций и температурного режима. Устранив все имеющиеся недочеты, следует приступить к изготовлению следующей порции блоков.
Самостоятельное производство позволит значительно сократить расходы на строительный материал. Справиться с этой задачей может каждый. Важно правильно подобрать сырье, подготовить необходимые инструменты и формы для заливки пенобетона.
литьевая и резательная. Оборудование для производства пеноблоков :: BusinessMan.ru
Практичность при выполнении монтажных операций и оптимизация расходов – первостепенные условия, к которым стремятся участники строительной отрасли. Достигаются они разными путями и способами, но в итоге облегчают рабочий процесс и позволяют обеспечивать качественный результат. Переход от традиционных стройматериалов на более современные и даже инновационные часто выступает именно как средство оптимизации и повышения качественных характеристик сооружения.
В этом смысле интересна технология изготовления пеноблоков, которая базируется на классическом способе приготовления строительного раствора, но при этом отличается доступностью. Использовать ее может и домашний мастер, но для этого придется в деталях ознакомиться с нюансами создания такого рода блочных стройматериалов.
Из чего делают пеноблоки?
В качестве основы применяется портландцемент, причем самой высокой марки – например, подходит М 400. Цемент должен отвечать свойствам данной марки, иначе он не сможет выполнять свои функции после изготовления. Отличительной чертой пеноблока является пористая структура, благодаря которой он входит в группу ячеистых бетонов. Поэтому процесс его изготовления не обойдется и без пенообразователя. Это может быть органический или синтетический компонент, в перечень задач которого будет входить как раз образование неплотной, пористой структуры. На практике она обеспечит стенам немало эксплуатационных преимуществ.
Также в основу иногда добавляют глину, золу и некоторые разновидности промышленных отходов. С точки зрения повышения технико-физических свойств в такой разбавке особого смысла нет – добавление второсортного сырья обычно ставит целью удешевление состава путем вымещения дорогостоящего портландцемента. Также в обязательном порядке в состав вводится песок и вода.
Своего рода функциональный сегмент компонентов формируется клеем и фиброй. Что касается клеевого раствора, то он потребуется и для состава, и для кладки. Это может быть один и тот же продукт – главное, чтобы он соответствовал требованиям для использования в конкретных условиях. С точки зрения приготовления раствора важны будут такие свойства, как вязкость, сцепление, хваткость и химическая безвредность. В качестве средства формирования кладки клей для пеноблоков в чистом вид используется редко, но в любом случае он должен быть морозостойким, терпимым к влажности, прочным и огнеупорным. Фиброволокно, в свою очередь, выполняет задачу армирования. Тоже в некотором роде функция сцепки, но в более выраженном механическом варианте. Волокна позволяют минимизировать риск образования трещин, усиливают конструкции стен и перекрытий, а также снижают нагрузки на смежные конструкции.
Характеристики пеноблока
Эксплуатационные характеристики отражаются уже в самой маркировке пеноблока. Например, для акцента на теплоизоляции стоит выбирать марки от D150 до D400. Данный материал благодаря высокой плотности (числовое значение указывает на соотношение кг/м3) обеспечивает достаточное утепление для домов, расположенных в средних широтах. В плане прочности это не самый выгодный вариант на фоне традиционного кирпича, например. В среднем прочностный предел составляет 9 кг на 1 см3. Другое дело, что даже производство пеноблоков в домашних условиях допускает внесение пластификаторов и наполнителей, способных повышать отдельные свойства, в том числе прочность и морозоустойчивость.
В заводских условиях технические качества улучшаются и за счет базового состава. Марки D500-D900 считаются конструкционно-теплоизоляционными, то есть пригодными и для обеспечения тепла в северных регионах, и для поддержания надежности в плане физических нагрузок. К слову, наиболее крепкие блоки способны выдерживать до 90 кг на 1 м2 – это марка D1200. Типоразмеры могут быть разными, но существует стандартизированный формат выпуска материала, который считается оптимальным. Это пеноблок 200х300х600 мм, который в зависимости от состава обеспечивает плотность стены от 300 до 1200 кг/м3. При этом водопоглощение стабильно составляет 14 %.
Технология изготовления литьем
На первом этапе выполняется подготовка самого раствора, которую можно производить в обычном строительном бункере с функцией автоматического замеса. Далее созданная смесь выливается в кассетные формы, где масса пенобетона принимает заданные физические параметры. Традиционные литьевые технологии предусматривают возможность дальнейшей вибрации и трамбования в формах, что улучшит качества блока. Однако в упрощенных кассетных формах данная функция отсутствует из-за недостатка электропривода, который мог бы обеспечить вибрационный эффект.
Более современные матрицы с опалубкой позволяют менять конфигурацию ячеек. То есть пользователь сам может настраивать толщину и длину блока в соответствии со своими запросами. Это также дает возможность создавать пеноблок с индивидуальными параметрами в единичных экземплярах – например, для кладки в сложных местах. Период полимеризации, то есть застывания, варьируется в среднем от 10 до 20 час. Это во многом зависит от того, какой использовался клей для пеноблоков – водостойкий, на силиконовой или полимерной основе. После базового укрепления структуры можно освобождать блоки от стен опалубки.
Оборудование для литья
Реализовать литьевой метод позволят три категории оборудования. В первую очередь это установки для создания пенобетонной смеси. Они отличаются от обычных бункеров тем, что имеют устройство для генерации пены. Средняя производительность такого агрегата составляет 20-30 м3 в сутки, опять же, она зависит от конкретного состава. На следующем этапе может использоваться мобильное оборудование для пеноблоков, которое облегчит задачу транспортировки смеси к формам. Это могут быть и самоходные машины с бункерами, и прямые стационарные каналы подачи раствора целенаправленно к матрице.
Относительно самих форм уже отмечалось, что они представляют собой матричные кассетные ячейки, в которые заливается смесь. В домашних условиях аналог такого приспособления можно изготовить из обычных металлических листов. Конструируется своего рода обрешетка, причем для нее не обязательно наличие дна – в процессе работы даже заводские конструкции часто ставятся на ровную поверхность, и этого хватает, чтобы получить геометрически правильный материал кладки. Другое дело, что технология изготовления пеноблоков литьевым способом также предусматривает возможность легкого и быстрого демонтажа формы после застывания раствора.
Технология изготовления резкой
Этот способ создания пеноблоков тоже предусматривает отдельные этапы приготовления и доставки смеси к непосредственному месту конечного формирования материала. Но в отличие от предыдущего метода предполагает другой подход к самой подготовке блоков. Они формируются не в ячейках матрицы, а путем механического разделения общего массива. То есть изначально также производится заливка, но не по отдельным матричным формам, а в общий поддон. Затем осуществляется раскрой вылитого раствора по секторам. Как именно будет выполняться эта операция – зависит от того, в каких условиях применяется резательная технология. Пеноблоки заводского типа на крупных предприятиях режутся лазерами и термическими головками. На малых и средних комбинатах это делается посредством пил, нитей и других механических резчиков, которые заслуживают отдельного внимания.
Оборудование для резки блоков
Профессиональное изготовление пеноблока не обходится без специальных линий резки, которые работают с монолитным бетоном. В плане режущего инструмента это очень разнообразное оборудование – могут использоваться ленточные резчики, струны, циркулярные пилы, металлические тросы и т. д. Базируется такое оборудование для пеноблоков на платформе или станине, предназначенной также и для размещения целевого материала. В процессе работы резчики проходят по монолиту, оставляя за собой полосы разделенных сегментов. Поперечное прохождение завершает операцию резки, оставляя уже готовые блоки.
У данного метода есть несколько преимуществ перед литьевым. В первую очередь обеспечивается точность формирования граней и сторон. Благодаря этому повышается и качество будущей укладки. К тому же, если формовка требует в некоторых случаях нанесения специальной смазки на края металлических ячеек, из-за чего страдает адгезия поверхностей блоков, то резка сохраняет шероховатость граней и тем самым улучшает их сцепку с другими инородными поверхностями. Кроме того, остается полная свобода в регуляции параметров, с которыми выпускаются пеноблоки. Размеры и вес изделий могут разниться: их выполняют и в стандартном формате 200х300х600 со средней массой 500 кг на 1 м2, и с индивидуальными характеристиками.
Технология выполнения распалубки
Этот способ по сути напоминает литьевой, но с большей долей автоматизации. Классическая формовка может полностью выполняться вручную с применением самодельных металлических ячеек. Автоматическая распалубка требует участия оператора только в процессе регуляции заливки в изначальные формы. Далее машина самостоятельно забирает формы на поддон и удерживает их в своем бункере (иногда с тепловым воздействием) до момента полного застывания. Такое производство пеноблоков в домашних условиях организовать затруднительно, поскольку оборудование может требовать подключения к сети в 380 В, но при наличии трехфазной линии – вполне возможно. Тем более что смесь также готовится сторонним образом без подключения специальных агрегатов. После застывания установка автоматически открывает бункер, выносит на поддоне форму с блоками и убирает опалубку.
Сушка блоков из пенобетона
В условиях поточного производства, когда нет времени на многочасовые и даже суточные ожидания полимеризации блоков, используют дополнительный технологический этап – термическую сушку. Для этого применяется специальная камера, в которую загружают пеноблоки. Строительные технологии по изготовлению кирпича в обязательном порядке предусматривают использование печей как средства обжига и укрепления. Пенобетон — менее плотный материал, поэтому без термического воздействия часто обходятся – но для экономии времени и укрепления структуры данный этап лишним не будет. По расчетам специалистов, печная пропарка за пару часов позволяет блоку набрать еще порядка 70 % от базовой прочности. Организационно данная технология изготовления пеноблоков возможна только на автоматизированных линиях. Машина должна автоматически управлять загрузочно-разгрузочными процессами, связанными с перемещением кассетных форм в печь.
Мини-заводы для создания пеноблоков
На небольших производствах в целях оптимизации часто используют небольшие линии изготовления, в которых компактно концентрируются функциональные площадки. Концепция мини-завода для пеноблока строится на тех же принципах. Оператору не нужно искусственно заполнять бреши между технологическими этапами – от начала до конца производство контролируется автоматикой. Начинается линия с бункера, в котором размешивается смесь для пенобетона. Оператор вносит в нее все необходимые компоненты с добавками и устанавливает программу приготовления строительной смеси. Далее раствор подается в емкость, которая сформирует прямоугольный монолит.
Типовой мини-завод по производству пеноблоков работает по методу нарезки блоков, так как изначально ориентируется на получение элементов с точными геометрическими размерами. После естественного или печного застывания монолит отправляется на этап автоматической резки, откуда уже в виде готовых блоков переправляется на пункт приема.
Заключение
Изготовление пенобетонного стройматериала гораздо проще, чем кирпича или панельных плит. Но так ли оправдывает себя этот материал на практике эксплуатации? Такие блоки отличаются небольшой массой, поэтому и прочность изначально будет несравнима с обычным кирпичом. Но есть и положительные свойства у ячеистого бетона. Даже упрощенная технология изготовления пеноблоков без специальных добавок позволяет добиваться высоких теплоизоляционных качеств. Поэтому даже при скромной массе и плотности такой блок может гарантировать оптимальный микроклимат. С точки зрения экологической безопасности это тоже неплохой вариант для строительства дома. Опять же, если обойтись без специальных модификаторов, то конструкция будет химически безопасна для жильцов.
Но главное достоинство пеноблока заключается в финансовой экономии. И технология изготовления, и логистика при строительстве и транспортировке требуют минимальных вложений по сравнению с альтернативными кладочными и панельными стройматериалами.
Производство пеноблоков технология и оборудование
Бизнес производство пенобетонных блоков. Пеноблоки: технология производства, оборудование.
Пеноблок (пенобетонный блок) – строительный материал с пористой структурой на основе вспененного бетона, изготовляется по классической или баротехнологии из смеси на основе пены и бетона.
Наиболее распространённые типоразмеры пеноблоков:
- 600×300х200.
- 600×300х150.
- 600×300х100.
- 500×300х200.
- 500×300х150.
- 500×300х100.
Пенобетон подразделяется по основным свойствам и характеристикам на несколько видов:
- Теплоизоляционный.
- Конструкционно-теплоизоляционный.
- Конструкционный.
Теплопроводность пенобетона таблица.
Морозостойкость, класс по прочности на сжатие.
Оборудование для производства пеноблоков.
Комплект оборудования зависит от технологии производства, если используется классическая технология, то установка для производства пеноблоков будет состоять из оборудования:
- Смесителя.
- Пеногенератора.
- Форм для отливки.
Для производства пенобетонных блоков по баротехнологии понадобится следующие оборудование:
- Бароустановка.
- Формы для отливки блоков.
Производственная линия.
Сырье для производства пенобетонных блоков.
- Портландцемент М500Д20, М400Д0, М400Д20, если используется баротехнология то понадобится цемент марки М500Д0.
- Песок ГОСТ 8736-93. (вместо песка можно использовать известняковую или доломитовую муку, отсев).
- Фиброволокно (армирующий элемент).
- Вода ГОСТ 23732-79.
- Пенообразователь (синтетический для бароустановки или белковый для классической).
Технология производства пеноблоков.
Для производства пеноблоков применяется два варианта технологий:
Классическая.
Классическая технология основана на использовании пеногенератора. В пеногенераторе приготавливается пена, а в смесителе подготавливается бетонная смесь. Затем пена добавляется в бетонную смесь, полученный состав заливается в формы где и застывает.
Баротехнология.
В баротехнологии для приготовления пенобетона применяется бароустановка (герметичный высокооборотистый миксер). При замешивании смеси в бароустановку подаётся под давлением сжатый воздух и компоненты для раствора, таким образом в бароустановке производится пенобетонный раствор который и разливается шлангом в формы для отливки.
Плюсы такой технологии в дешевизне и в простоте производства, минусы в повышенном расходе пенообразователя и меньшая прочность получаемого пенобетона по сравнению с классической технологией.
Независимо от технологии производства, чтобы получить блоки из пенобетона применяется один из двух вариантов.
Заливка пенобетона в формы с перегородками.
Получение блоков методом заливки пенобетона в кассетные формы, пенобетон застывает 2 — 3 суток, после чего форма разбирается и извлекаются готовые пеноблоки.
Второй метод резка пенобетона.
Пенобетон отливается в форме в один массив объёмом около 2 куб. м затем на резательной установке его распиливают пилами на блоки.
Производство пеноблоков.
Рассмотрим процесс изготовления пенобетонных блоков по классической технологии.
Подготовка форм для отливки.
Разборные металлические формы для отливки собирают и покрывают смазкой, в качестве смазки используется эмульсионный разделительный состав.
Приготовление бетонной смеси.
Сначала в смеситель заливается вода и добавляется фиброволокно, затем добавляется цемент и наполнитель (песок).
В это время отдельно готовится концентрат, в пенообразователь добавляется вода, смесь перемешивается и заливается в пеногенератор.
В бетонный раствор добавляется приготовленная пена, смесь перемешивается до однородной консистенции.
Заливка форм.
В подготовленные и смазанные формы заливается пенобетонная смесь.
Выдерживание.
Чтобы пенобетон набрал необходимую первоначальную прочность ему нужно выстояться в формах не менее 3 суток, после чего его можно будет укладывать на поддоны.
Распалубка или резка.
На данном этапе пенобетон набирает достаточную прочность, чтобы его можно было извлекать из форм или распиливать массив на блоки.
Производится распалубка форм, блоки извлекаются, укладываются на деревянные поддоны, после чего блоки нужно обмотать стрейч плёнкой чтобы бетон быстро не терял влагу.
Для окончательного набора прочности блоки нужно ещё оставить на 28 дней на складе, после чего их можно отправлять на продажу и использовать для строительства.
Производство пеноблоков видео.
На видео показан процесс производства пенобетонных блоков.
Преимущества применения пеноблоков в строительстве.
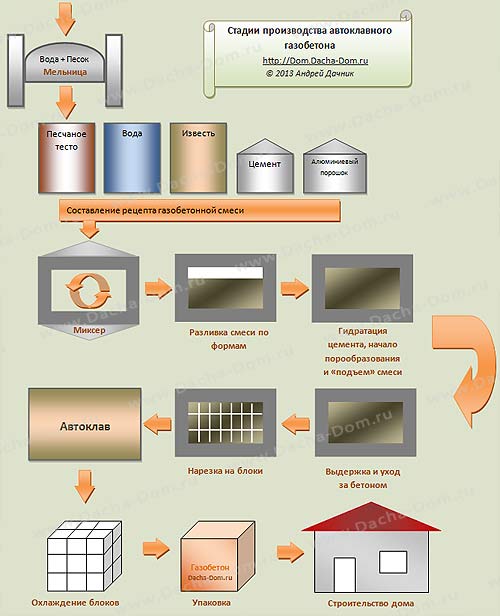
Пенобетонный блок обладает высокой прочностью.
Экологичность. Пеноблоки не выделяют вредные вещества, коэффициент пенобетона по экологичности – 2, дерева – 1, кирпича – 10.
Обладает высоким термическим сопротивлением, помещение из пеноблоков способно аккумулировать тепло в холодный период и удерживать прохладу в летний зной.
Пенобетон способен регулировать влажность воздуха в помещении, путём впитывания и отдачи влаги по аналогии помещений из древесины.
Скорость монтажа. Благодаря большим размерам и сравнительно лёгкому весу блоков скорость кладки возрастает в несколько раз по сравнению с кирпичной кладкой.
Лёгкость в обработке. Пенобетон достаточно легко поддаётся обработке, его можно распиливать на нужные куски, делать каналы под электропроводку, трубы.
Звукоизоляция. Пеноблоки обладают достаточно хорошим поглощением звука, помещение из пенобетона полностью соответствует требованиям звукоизоляции.
Оборудование для производства пеноблоков
Популярность пенобетона как строительного материала связана не только с его прекрасными эксплуатационными характеристиками. В немалой степени ее определяют простота изготовления и экономичность. Производство блоков из пенобетона требует небольшого количества сырья и может быть развернуто на минимальной площади в краткий срок.
Весь процесс достаточно прост. Сырьевые компоненты – песок, цемент, вода и пенообразователь перемешиваются между собой до образования однородной массы. Из нее формируются либо стандартные блоки, либо базовые, которые впоследствии доводятся до нужного размера.
Для приготовления основной смеси необходимо следующее оборудование для производства пенобетона:
- пеносмеситель
- пеногенератор
- компрессор
- миксер
Пеносмеситель отвечает за приготовление пенной смеси, состоящей из воды и пенообразователя. Конструктивно представляет собой емкости, в которых хранятся и перемешиваются компоненты для образования пенной суспензии. Для улучшения перемешивания компонентов применяется предварительный подогрев воды.
Пеногенератор вспенивает суспензию до образования мелкодисперсной пены, которая затем подается в миксер. Компрессор является одной из основных силовых установок и служит для генерации потока воздуха под давлением. Может работать как от стационарной электросети, так и от дизель-генератора. Это позволяет развернуть производство пеноблоков в полевых условиях.
Миксер – основная часть установки для производства пенобетона. В нем перемешиваются пена, подаваемая из пеногенератора, песок и цемент. После приготовления базовой смеси она заливается в формы. Их размер определяется технологией получения готовых блоков.
Технологии производства пеноблоков
Блоки из пенобетона изготавливаются по двум технологиям:
- Литьевая технология
- Резательная технология
Каждая из них имеет свои достоинства и недостатки.
Литьевая технология производства пенобетона основана на разливе базовой смеси в формы стандартного размера. В них пенобетон минерализуется и застывает. К преимуществам такого способа можно отнести отсутствие необходимости дальнейшей обработки блоков и дополнительного оборудования для этого. Недостатки литьевого способа состоят в строго ограниченном размере блоков.
Резательная технология производства пенобетона более универсальна по отношению к литьевой. При этом способе сначала формируются блоки большого размера. После застывания смеси блок распиливается при помощи резательного станка. Преимущества такого способа заключаются в возможности получения блоков любого размера, изготовления нестандартных изделий из пенобетона и возможности быстрой перенастройки оборудования для выпуска блоков разного типоразмера. Недостаток заключается в необходимости содержания дополнительного оборудования. Затраты на его приобретение достаточно существенные.
При отборе поставщиков оборудования для производства пеноблоков главным критерием является качество изготовления комплексов. Ведь от него зависит бесперебойность производственного процесса, а также время, которое тратится на обслуживание и поточный ремонт.
В практике организации производства пенобетона, как правило, одновременно используются оба способа. Литьевой используется для поточного производства блоков наиболее востребованных типоразмеров. Резательный, в свою очередь, дополняя литьевой, применяется когда есть потребность в изготовлении нестандартной продукции. Совместное использование обеих технологий, несмотря на большие первоначальные затраты увеличивает прибыльность и уменьшает время окупаемости всего цеха в целом.
Производство пеноблоков — видео
Производство пеноблоковВ этом видео показан технологический процесс производства пеноблоков |
Статья написана для promplace. ru
ссылка обязательна
Машина для производства порционного пенопласта для матрацев, обивки, подушек и изделий различной формы
FP4 — Машина для производства порционной блочной пены для матрацев, обивки, подушек и изделий различной формы
Линия состоит из дозирующей головки (для полиолов, изоцианатов, добавок), резервуаров для смешивания продуктов, форм для формования блоков и других дополнительных устройств, таких как системы транспортировки, специальные насосы, датчики нагрузки и индивидуальная электронная система. Он был разработан для прерывистого производства блоков из гибкого или жесткого пенополиуретана: вы можете производить блоки разных размеров, плотности, форм и цветов, чтобы обеспечить максимальную гибкость.
Система поставляется с сенсорным дисплеем и интуитивно понятным программным обеспечением для ввода производственных параметров и рецептов, настройки всех данных клиента, мониторинга процесса в реальном времени, проверки потока компонентов, потребления и статистики.
Эта модульная линия может быть спроектирована в соответствии с требованиями заказчика и предварительно сконфигурирована для будущего расширения при необходимости; с помощью этой машины можно сократить расходы на управление материалами, время выполнения заказа и площадь производственных площадей.
Мы можем поддержать наших клиентов в разработке всего проекта: от выбора сырья, оценки дополнительных опциональных устройств для станка, роботизированных систем манипулирования пеноблоком до выбора лучших решений для резки.
FP4 — МАШИНА ДЛЯ БЛОКА РАЗМЕРА ПУ-ПЕНЫ
СИЛОСЫ FP4
Пример вырезанного и профилированного блока пенополиуретана
Невероятная машина для производства пеноблоков по низкой цене Местное послепродажное обслуживание
Увеличьте производительность вашего производства кирпича с помощью чудесных средств. Машина для производства пеноблоков . Они доступны на Alibaba.com в виде заманчивых предложений, которые нельзя игнорировать. Премия. Машина для производства пеноблоков обладает непревзойденными качествами, которые были достигнуты благодаря передовым технологиям и изобретениям. Они увеличивают скорость производства кирпича, следовательно, экономят время и энергию. Материалы, используемые в. Машина для производства пеноблоков прочные и долговечные, что обеспечивает долгий срок службы и неизменно высокую производительность.
Обширная коллекция. Машина для производства пеноблоков существует в различных моделях, которые учитывают различные бизнес-спецификации и индивидуальные особенности для всех типов строительных работ. Alibaba.com стремится убедить всех покупателей, что товары только высшего качества. Машины для производства пеноблоков продаются на сайте. Соответственно, поставщики подвергаются тщательному контролю на предмет соблюдения всех нормативных стандартов. Таким образом, покупатели всегда получают. Машина для производства пеноблоков , которая превосходит то, что обещает.
Благодаря постоянному технологическому прогрессу производители внедрили изобретения, которые снижают потребность в энергии. Машина для производства пеноблоков . В результате вы экономите больше денег на счетах за топливо и электроэнергию. Файл. Машина для производства пеноблоков также обладает исключительными характеристиками безопасности, чтобы гарантировать минимальный риск, связанный с операциями. При относительно низких затратах на их приобретение и обслуживание расширение. Машина для производства пеноблоков разумно доступна и предлагает соотношение цены и качества.
Это ваше время, чтобы сэкономить деньги и время, делая покупки в Интернете на Alibaba.com. Исследуй разные. Машина для производства пеноблоков на сайте и остановитесь на наиболее привлекательном и подходящем для вас. Если вы ищете настройки в соответствии с конкретными требованиями, ищите. Машина для производства пеноблоков и достигнет своих целей. Откройте для себя доступное качество на сайте уже сегодня.
Как изготовить пеноблоки?
Нас часто просят подробно рассказать о технологии изготовления пеноблоков и пенобетона на пенобетонных машинах серии BAS.Несмотря на то, что эта технология действительно проста, в этой статье мы расскажем, как делать пенобетонные блоки и другие легкие изделия из стеклопластика.
Как без проблем изготовить пеноблоки
Но новички или те, кто только собирается заниматься производством пенобетона, хотят знать как можно больше о том, как производить пеноблоки. Это позволяет избежать ошибок при производстве и сэкономить деньги. Поэтому мы решили помочь нашим клиентам. Один из наших клиентов любезно предоставил видео, на котором наглядно показано, как производить пеноблоки на небольшой площади.К каждой нашей машине прилагается инструкция и рецепт пенобетонной смеси. В ролике автор рассказывает о тонкостях рецептов в разных регионах и затрагивает тему использования старого и «мертвого» цемента.
Также на видео наш заказчик демонстрирует формы для изготовления пеноблоков из ламинированной фанеры оригинальной конструкции, разработанной им самим. И он рассказывает о своем опыте работы с различными формами блоков из легкого бетона.
Как выгодно и просто производить легкие бетонные блоки clc
Чтобы понять, как сделать производство пеноблоков экономически выгодным, каждый производитель должен четко понимать, что он хочет получить от этого бизнеса.
Если вы собираетесь заняться производством пеноблоков, чтобы построить 1-2 дома, то не стоит тратить большие деньги на покупку машины типа BAS350 или BAS500.
Для этих целей вполне подойдет BAS130 или BAS200.Мы производим машины BAS130 и BAS200 с питанием от однофазной сети 110 или 220 вольт. Это дает возможность проводить мобильные работы по устройству стяжек, стен, перегородок из монолитного пенобетона непосредственно на месте строительства.
Если вы собираетесь начать производство пеноблоков на продажу как бизнес, то вам следует подумать о более мощном станке, таком как BAS250, BAS350 или BAS500. Необходимо понимать, что покупка этих машин подразумевает питание от трехфазной промышленной сети на 240 или 380 вольт.Это зависит от стандартов электроснабжения в вашей стране.
В любом случае мы всегда рекомендуем покупать машины с питанием от промышленной трехфазной сети.
Основная причина — нестабильность однофазного питания в большинстве мест.
Если вы все же решили приобрести машину с питанием от однофазной сети 110/220 вольт, то перед этим сначала проверьте, выдержит ли она мощность, потребляемую машиной для производства бетонных блоков. Это защитит вашу машину от повреждений.И ваш бизнес от простоев.
ECO-SLAB компактная идея — Cannon Viking
Разработанный для удовлетворения растущего спроса на рынке на компактное решение, способное производить широкий спектр высококачественных гибких пеноблоков, Eco-Slab был разработан с использованием последнего поколения процесса дозирования, компьютерного управления и систем смешивания, упакованных вместе в модульной конструкции, дающей клиенту максимальную гибкость при проектировании машины на заказ в соответствии с его требованиями к пеноматериалам, а также возможность практической модернизации в будущем.
По этой причине Eco-Slab имеет уникальные преимущества:
- Благодаря компьютерному контролю Omega последнего поколения, эта система, разработанная и поддерживаемая собственными силами, позволяет оператору полностью управлять рецептурой, автоматическим контролем дозирования химикатов, замкнутым контуром управления с удобным интерфейсом и историческая информация о заводе.
- Снижение потребления энергии и химикатов: благодаря компьютерному управлению, системам мониторинга завода и точной системе дозирования химикатов Eco-Slab особенно эффективен и позволяет покупателю получить общую финансовую экономию, которая может легко превысить 10% по сравнению с обычная машина для производства плит.
- Малая занимаемая площадь для уменьшения площади и затрат на строительство: благодаря небольшому размеру Eco-Slab можно легко интегрировать с предыдущими установками.
- Гибкость для производства различных типов пен при помощи различных методов: Eco-Slab может использоваться для производства всех типов пенополиуретана, включая стандартные пенополиэфирные пеноматериалы, пенопласты HR, пенопласты с эффектом памяти / вязкости, сверхмягкие пенопласты, полужесткие и жесткие пенопласты.
Он также может производить пеноблоки с использованием:
- Желоб: химическая реакция происходит внутри желоба перед подъемом сверху на регулируемую опускную пластину, которая затем ведет пеноблок по горизонтальному конвейеру с металлическими пластинами для завершения подъема пены и начального отверждения.
- Жидкая укладка: этот процесс дает пенопласт более высокого качества, уменьшая количество точечных отверстий, потому что химическая смесь вводится через прямую укладку пены на разливочную плиту.
- Комбинация обеих систем.
Eco-Slab отражает рыночную философию Cannon Viking: гибкий подход, основанный на внимании к потребностям клиентов. Фактически, компания не предоставляет только стандартные машины, но, исходя из конкретных запросов клиентов, может предложить индивидуальные решения.
Как свидетельствует Ник Вуд, операционный директор Vita Group, «… [Eco-Slab] занимает мало места, и, хотя он способен производить большие объемы на высокой скорости, он может производить индивидуальную новую эффективную пену. Он обладает высокой гибкостью и возможностью легко заменять различные присадки для проявки. Он добился того, что нам было нужно ».
Eco-Slab обладает многими из самых популярных и успешных функций, замеченных на других машинах непрерывного действия Cannon Viking, при этом соблюдая самые высокие стандарты машиностроения.
Узнайте больше об Eco-Slab: посетите продукт на стр. или узнайте обо всех решениях Cannon Viking для производства плит .
Как перейти в бизнес по производству пенобетонных блоков
Производство пенобетона и пеноблоков — довольно прибыльная отрасль строительного бизнеса и достаточно хорошее вложение в бизнес. Спрос на пеноблоки стабильно высок, так как они имеют широкий спектр применения.
Пенобетон в строительстве можно использовать для:
- Изготовление несущих конструкций, в т.ч.е. настил и кровля, и несущие стены;
- Элементы инженерные и теплоизоляционные, т.е. наружные стены и внутренние перегородки;
- Строительство трехслойных стен, у которых пенобетон или блоки из него служат теплоизоляцией;
- Заливка монолитного каркаса пенобетонными блоками;
- Изготовление теплоизоляционных элементов кровли и фундамента;
- Изготовление заборов и оград из пенобетона;
- Заливка пенобетона в несъемные формы;
- Изготовление армированных и неармированных строительных элементов;
- Теплоизоляция трубопроводов;
- Теплоизоляция оборудования;
- Шумоизоляция промежуточных этажей.
При запуске бизнеса по производству пенобетона в первую очередь необходимо определить некоторые критические факторы и детали, такие как: тип производимого пенобетона, наличие производственных площадок и их площадь, наличие сырьевой базы и т. Д. Специалисты нашей компании попросят вас заполнить анкету, чтобы учесть все ваши предложения, на основании которых мы подберем для вас лучший комплект оборудования.
Затем мы делаем расценки на установку производственной линии.Чтобы помочь клиенту принять решение, он посетит небольшие предприятия и автоматизированные заводы различной производительности, которые уже успешно используют технологии и оборудование компании.
Для начала вашего производства будет достаточно помещения площадью 60 кв.м. Поэтому производство пеноблоков так хорошо для небольших городов, где не нужны такие большие объемы производства. Как и в крупных, где производство пеноблоков исчисляется сотнями кубометров в сутки.
Смесь цемента, кремнеземистого компонента (песок, летучая зола), воды и пены используется для изготовления неавтоклавного пенобетона. Эта смесь изготавливается на пенобетонных станциях.
По согласованию с заказчиком заключаются договоры на выполнение проектно-конструкторских работ, поставки оборудования, пусконаладочных работ. Предложение предусматривает выезд технолога-технолога к вам для выбора состава, разработки технологических режимов, изготовления продукции и обучения персонала.
По завершении этих работ запуск линии в эксплуатацию. Изготовлены опытные образцы, которые затем проходят испытания в сертифицированных центрах.
Как производятся блоки из пенопласта и 3 факта
EPS (пенополистирол) или «геопена» набирает популярность как широко приемлемый и экономичный строительный и изоляционный материал. Поскольку геопена чрезвычайно легкая и может выдерживать суровые условия, она обычно используется для конструкционного наполнителя, при строительстве надземных плит, при строительстве дорог, стабилизации откосов, насыпей мостов и многого другого.С тех пор, как геопена была представлена в 1950-х годах, она использовалась в тысячах и тысячах различных строительных проектов по всему миру.
Итак, как же изготавливаются эти многоцелевые пеноблоки из EPS? Вот ваше руководство о том, как производятся блоки из пенопласта, и 3 факта, о которых вы, возможно, не знали.
Из чего сделана геопена EPS?Пенополистирольный геопенополистирол, обладающий многими теми же характеристиками, что и пенополистирол, изготавливается из материала, называемого полистирольным полимером.Одно различие между широко известными листами пенополистирола и геопеной из пенополистирола заключается в способе изготовления блоков фундамента из пенопласта. Все начинается с «бусинки» полистирольной смолы. Геопена EPS затем загружается в бункер для производства вместе с добавлением тепла и давления. Это термопластический материал, которому можно многократно придавать форму и форму.
Полимеризация полистирола Блоки Geofoam производятся с помощью процесса, называемого полимеризацией, который представляет собой процесс создания полистирола путем приложения тепла и давления внутри формы. В зависимости от того, сколько тепла и давления добавлено к шарикам внутри формы, можно производить геопенополистирол различной плотности.
Для создания блоков геопенопласта гранулы полистирола сначала расширяются в предварительные затяжки, а затем загружаются в специальную форму для окончательного расширения. На этапе предварительной затяжки ограниченное количество шариков смолы помещается в расширительный бак. Затем в сосуд вводят пар для размягчения шариков твердой смолы и частичного или полного испарения внутри них вспенивающего агента.Количество тепла от пара определяет, насколько плотны предварительные затяжки и сколько в них осталось вспенивающего агента.
Чтобы контролировать плотность материала геопены, производители прекращают подавать тепло, когда предварительные затяжки достигают желаемого объема и размера, что в конечном итоге приведет к образованию блока геопены EPS. Затем предварительные затяжки хранятся в тканевых мешках для охлаждения до комнатной температуры и желаемого давления перед подачей в окончательную блочную форму.
Заключительный этап создания блоков геопены — этап формования.Предварительные затяжки помещаются внутрь блочной формы, и горячий пар вводится в форму под контролируемым давлением. Пар смягчает предварительную затяжку, что делает ее готовой к расширению. Тепло от пара заставляет эти шарики непрерывно расширяться. По мере расширения шариков ограниченное пространство внутри формы вынуждает шарики сливаться друг с другом, образуя таким образом блок геопенополистирола EPS. После этого процесса блок извлекается из формы, обрезается, маркируется и отправляется на строительные, ландшафтные и строительные площадки для самых разных применений геопены.
3 факта о Geofoam, которых вы не знали Теперь, когда вы лучше познакомились с тем, как производится геопена, вот 3 основных факта об этом универсальном материале, которые можно добавить в банк знаний.
Многие архитекторы, инженеры и строители предпочитают геопену из-за ее легкости и способности выдерживать значительную нагрузку.Он весит всего от 0,7 до 2,85 фунтов на кубический фут, в то время как почва может весить от 110 до 120 фунтов на кубический фут. Это делает конструкционные пеноблоки более выигрышным вариантом по сравнению с грунтовым покрытием для фундамента. Его сопротивление сжатию колеблется от 317 до 2678 фунтов на квадратный фут при деформации 1 процент. Эта высокая прочность на сжатие делает геопену более прочной и устойчивой к повреждениям.
EPS Geofoam не наносит вреда окружающей среде Поскольку экологичное строительство становится все более популярным, строители все больше и больше обращают внимание на геопену EPS из-за ее экологичных свойств.Наполнитель на 100% пригоден для вторичной переработки и не содержит гидрохлорфторуглеродов или формальдегида. Кроме того, это сверхэффективный теплоизолятор, позволяющий экономить общее потребление энергии, что в конечном итоге снижает углеродный след многих конструкций. Пенополистирол Geofoam также может быть изготовлен с определенным процентом переработанного содержимого из предыдущих блоков Geofoam в зависимости от требований проекта.
Помимо обеспечения изоляции для многих различных зданий, различные области применения геопеноблоков бесконечны и чрезвычайно универсальны.Например, блоки из пенопласта можно складывать друг на друга для создания сидений на стадионе. В качестве альтернативы эти прочные блоки с низким содержанием влаги можно использовать для поддержки различных ландшафтов и структур, таких как террасы у бассейнов и сады на крышах. Geofoam также является основным наполнителем, который составляет основу проезжей части благодаря его способности поглощать вибрации и сильное сжатие. Ознакомьтесь с нашим постом о самых популярных применениях геопен для строительства.
Компания Geofoam International является ведущим экспертом в индустрии пенополистирола, от предоставления информации до того, как изготавливаются блоки из геопены, до сбора фактов, подтверждающих ее достоинства.Воспользуйтесь нашими услугами и индивидуальными блоками из пенопласта для всех ваших строительных нужд, и позвольте нам направить вас на пути включения геопены в ваш следующий проект.
Для получения дополнительной информации или бесплатного предложения, пожалуйста, напишите по электронной почте [email protected] .
Полная автоматизация для сжатия блоков
Если вы хотите снизить затраты на производство пенопласта, рулонная упаковка дает одну из самых больших экономий для предприятия по производству пенопласта. Пеноблоки большие, тяжелые и наполненные воздухом. Они занимают много места как на производственном участке, так и на грузовике.
Этот воздух обходится производителям в большие деньги. Независимо от того, занимает ли он место на вашем полу или вы доставляете его по стране, вы тратите ресурсы зря. Вот почему машина для сжатия блоков — идеальный способ сэкономить на накладных расходах.
Посмотрите видео, чтобы узнать больше о достижениях нашего новейшего компонента в машине для сжатия блоков.Благодаря регулируемому каркасу безопасности теперь вы можете упаковать больше на одной машине, используя при этом полную автоматизацию.
Без сжатия пенообразователи отводят много воздуха. Размер и форма блоков означают, что они занимают много места в грузовике, но достигают только 1/8 от его общего предела веса, прежде чем грузовик будет заполнен. Компрессионная упаковка удаляет этот воздух, а это означает, что каждый отдельный продукт занимает меньше объема. Этот метод упаковки настолько эффективен, что вы можете заполнить грузовик до максимальной массы, но при этом в нем останется место для примерно в 7 раз больше блоков, упакованных в рулонах.То, что раньше требовало восьми грузовиков для перевозки, теперь помещается в один, и остается свободное место. Это снижает стоимость доставки до 200 долларов за упаковку!
Переменная клетка защищает бюджеты и продукты
Как видите, приобретение машины для сжатия блоков быстро окупится за счет экономии затрат на транспортировку. Наш BC2496 выводит эти инвестиции на новый уровень, учитывая разнообразие вариантов упаковки и обеспечивая защиту продукта. Размер рулонных пакетов может составлять от 16 до 24 дюймов, и наша система может даже пропускать этап прокатки, а также просто упаковывать блоки в плоскую упаковку.Независимо от метода упаковки, который требуется вашему блоку, вы можете быть уверены, что он восстановится после открытия пакета.
Как мы узнаем, что продукт безопасен?
Ранее мы рассказывали вам, насколько интеллектуален пресс в наших компрессорных машинах. Пресс предназначен для отслеживания обратной связи, которая обеспечивает быструю, реактивную, сбалансированную и сильную реакцию, постоянно применяя правильное давление — ни больше, ни меньше. Блочно-прессовая машина BC2496 выводит этот интеллект на новый уровень, как на входе, так и на регулируемых секциях каркаса.Благодаря разнообразию датчиков и измерительных устройств операторы теперь вводят гораздо меньше информации.
На входе датчики определяют вес, высоту, длину и плотность блока. Если вы помните страницы 2-3 нашей брошюры, это все измерения, которые мы используем в нашем калькуляторе каркаса безопасности, чтобы определить минимальные безопасные размеры конечной упаковки. Раньше оператору нужно было ввести эти данные в HMI в качестве рецепта. Если бы размер блока отличался от размера, указанного в рецепте, каркас безопасности по-прежнему создавал бы ту же окончательную упаковку. Во многих случаях с небольшими отклонениями это нормально, но оставляет возможность того, что блок, не соответствующий техническим характеристикам, может оказаться чрезмерно сжатым или даже повредить каркас безопасности.
Теперь с нашим регулируемым каркасом безопасности машина снимает эти измерения с устройства подачи и пресса и передает их непосредственно на каркас безопасности — вмешательство оператора не требуется. Клетка раскатывает продукт до нужного диаметра на основе этих измерений. Скажем, у вас есть два блока равной плотности; один — 80 x 60 x 48 и 267 фунтов, другой — 80 x 60 x 50 и 278 фунтов.Роликовый сепаратор знает, что первый может быть упакован диаметром 22, а второй может быть упакован диаметром 22 без риска схватывания при сжатии. Каждый продукт упаковывается до минимально возможного диаметра без риска чрезмерного сжатия. Вы можете запускать эти продукты последовательно и быть уверенными, что они будут правильно упакованы, без каких-либо изменений в HMI.
Если вы заинтересованы в модернизации или покупке машины для сжатия блоков C³, трудно игнорировать преимущества этой новой технологии.