Как делают обувь ручной работы
Думаю многим будет интересно как создаётся «bespoke» обувь. В этом посте покажу разные этапы создания пары и прокомментирую фото.
Сразу объясню что такое «bestpoke» и какая обувь ещё бывает.
Ready-to-wear (RTW), off-the-rack (OTR) — обувь, сшитая по готовым стандартизированным лекалам (колодкам) и продающаяся в магазинах.
Made-to-order (MTO) — обувь, созданная на стандартных колодках, но по индивидуальному заказу. Далеко не bespoke и даже не MTM, но в то же время — уже и не RTW.
Made-to-measure (MTM) — одежда и обувь, изготовленные по стандартизированным лекалам, слегка измененным по меркам заказчика, а также с учетом пожеланий заказчика относительно материала, фурнитуры и некоторых других деталей.
Bespoke — обувь ручной работы, изготовленная на заказ по индивидуальным выкройкам, на колодках изготовленных по размерам стопы клиента. Учитываются любые пожелания относительно материалов, фурнитуры и пр.
Начинается всё со снятия мерок, выбора фасона будущей пары обуви, рекомендаций модельера (бывает что в связи с анатомическими особенностями некоторые модели будут лучше смотреться или более удобны), подробно обсуждаем материал и особенности дизайна.
В этот раз выбор пал на кожу морского ската.
Если не удаётся выбрать из уже существующих моделей колодок, подключаем дизайнера, и получаем:
На колодке создаётся образ будущей пары, наносятся основные линии (на фото изготавливается другая пара, но суть ясна)
Переносим на плоскость, делаем более изящные изгибы, где необходимо припуски и прочие технологические тонкости и получаем первые выкройки.
Изготавливаем примерочную модель и приглашаем клиента на примерку. Примерочная модель изготавливается из низкосортной кожи и недорогих материалов. Эта модель визуализирует все пожелания клиента в дизайне, служит для выявления недостатков, корректировки выкроек, а возможно и самой колодки. После одобрительной примерки начинается работа над полноценной парой.
По заранее изготовленным лекалам делается раскрой материала с учетом его структуры, тягучести и имеющихся пороков.
Производится брусовка краев для гладкого сочленения деталей внахлёст, после сшиваются между собой в определенной последовательности.
После сшивания деталей приступаем к изготовлению несущей стельки из чепрачной кожи растительного дубления.
На ней прорезается бортик (губа), в губе делаются отверстия через которые будет пришит в ручную кожаный рант, такой тип крепления подошвы называется «Hand welted» или по русски — ручное рантовое крепление (аналогичная прошивка, но выполненная машиной «Goodyear welted»).
Теперь можно переходить к затяжке пары на колодку.
Следующий этап вшивания кожаного ранта (заранее подготовленного из чепрачной кожи).
Пришло время подошвы с заранее выдавленным логотипом. После приклейки выполняется сшивание кожаного ранта с подошвой. Тем временем набираются каблуки из кожаных «фликов» и устанавливаются на пару. Обтачиваем рашпилем, вышкуриваем наждачной бумагой разной зернистости, окрашиваем. В данной паре также устанавливаем набойку и профилактику.
И настала работа по выглаживанию и полировке уреза подошвы, каблука и верха. После полировки можно достать колодку и изготовить вкладную стельку, вдеть шнурки и пара готова!
Источник
Жми на кнопку, чтобы подписаться на «Как это сделано»!
Если у вас есть производство или сервис, о котором вы хотите рассказать нашим читателям, пишите Аслану ([email protected]) и мы сделаем самый лучший репортаж, который увидят не только читатели сообщества, но и сайта Как это сделано
Подписывайтесь также на наши группы в фейсбуке, вконтакте, одноклассниках, в ютюбе и инстаграме, где будут выкладываться самое интересное из сообщества, плюс видео о том, как это сделано, устроено и работает.
Жми на иконку и подписывайся!
— http://kak_eto_sdelano.livejournal.com/
— https://www.facebook.com/kaketosdelano/
— https://www.youtube.com/kaketosdelano
— https://vk.com/kaketosdelano
— https://ok.ru/kaketosdelano
— https://twitter.com/kaketosdelano
— https://www.instagram.com/kaketosdelano/
Официальный сайт — http://ikaketosdelano.ru/
Мой блог — http://aslan.livejournal.com
Инстаграм — https://www.instagram.com/aslanfoto/
Facebook — https://www.facebook.com/aslanfoto/
Вконтакте — https://vk.com/aslanfoto
Обувь своими руками, выбор материалов, пошаговый алгоритм создания
На чтение 12 мин. Просмотров 3.5k.
Несмотря на огромный ассортимент самой разной обуви на полках магазинов, часто люди заинтересованы в самостоятельном изготовлении тапочек, туфель или ботинок. Объясняется подобное желание многими причинами: возможностью удешевить готовое изделие, получить модель уникального дизайна, идеально соответствующую параметрам стопы, или даже попросту попробовать силы в новой для себя сфере. Как бы там ни было, чтобы сделать обувь своими руками, необходимо детально изучить все этапы производства, подобрать подходящее сырье и инструментарий, грамотно построить выкройку, выполнить множество других действий. Процесс длительный и сложный, требующий недюжинного терпения, концентрации внимания, усидчивости, при этом он вполне посильный, интересный и познавательный.
Особенности конструкции
Современный рынок представляет множество моделей обуви, которые отличаются друг от друга материалом и внешним видом. Перед изучением этапов изготовления изделий из кожи или замши стоит ознакомиться с конструкцией, составными частями, их отличиями.
Элементы, из которых состоит верхняя часть обуви:
- Носок — часть, закрывающая поверхность пальцев стопы, сохраняет ногу от механических повреждений, чаще всего вступает в контакт с внешней средой.
- Союзка — деталь, закрывающая тыльную поверхность стопы. При ходьбе постоянно поддается изгибам, поэтому деформируется первой.
- Берцы — охватывают нижние части голени и голеностопного сустава. При эксплуатации эта часть практически не поддается негативному воздействию извне.
- Люверс — место, предназначенное для проведения шнурков, веревок.
- Задник — деталь, которая закрывает пяточную часть стопы.
- Язычок — часть, прикрепленная к основанию ботинка, фиксирует ногу, предотвращает попадание внутрь пыли, грязи, мелких деталей.
- Стелька — слой мягкой и приятной кожи (или другого материала), который контактирует непосредственно со стопой, смягчает ходьбу, убирает дискомфортные ощущения даже при беге.
Нижняя часть обуви представлена следующими элементами:
- Подошва — самая значимая деталь низа, которая определяет не только удобство при хождении, но еще долговечность изделия. Она защищает ногу от неприятного контакта с грунтом, смягчает механическое воздействие при прыжке, беге, ходьбе.
- Каблук — деталь, которая предназначена для подъема пяточной части стопы. Может быть разных формы и размера, все зависит от модели, сезонной конструкции.
- Набойка — прикрепляется к поверхности каблука, защищает его от истирания.
- Рант — деталь, отвечающая за крепление низа обуви.
- Защитные вставки — элементы, сделанные из хлопковой ткани и полиуретана, предотвращающие натирание пятки, появление мозолей.
- Наполнитель — материал, который обеспечивает воздухопроницаемость, тепло, вентиляцию, защиту от сезонных погодных условий.
- Супинатор — деталь, которая размещается между подошвой и основой стельки, создает нужные жесткость и упругость.
На подошву приходятся огромные нагрузки, она подвергается постоянному износу при контакте с землей, поэтому материал для ее производства должен быть качественным и прочным.
Изготовление своими руками обуви требует соблюдения многих правил. Для каждой из описанных деталей существуют свои нюансы производства.
Материалы и инструменты
Перед тем как сделать обувь своими руками, важно подобрать правильный материал и собрать нужные инструменты. Взрослую или детскую продукцию чаще всего изготавливают из кожи, замши, текстиля. Популярностью пользуется именно натуральная кожаная обувь, потому что она долговечная, практичная, износостойкая, шансов натереть ноги гораздо меньше. Из этого сырья делают: кроссовки, ботинки, сапоги, туфли, кеды, шлепки.
Замша — приятный, мягкий, эластичный материал, используемый как для взрослой, так и для детской обуви. В ней нет лицевого слоя, она трудоемкая в изготовлении, поэтому достаточно дорогая. Текстиль — применяется для пошива летней обуви, пинеток для детей, кед, а также домашних тапочек. Материал очень нежный, мягкий, приятный на ощупь. В такой обуви нога всегда дышит, получает нужную вентиляцию, комфорт, тепло.
Текстиль экологически чистый, поэтому чаще всего его используют для изготовления детской обуви.
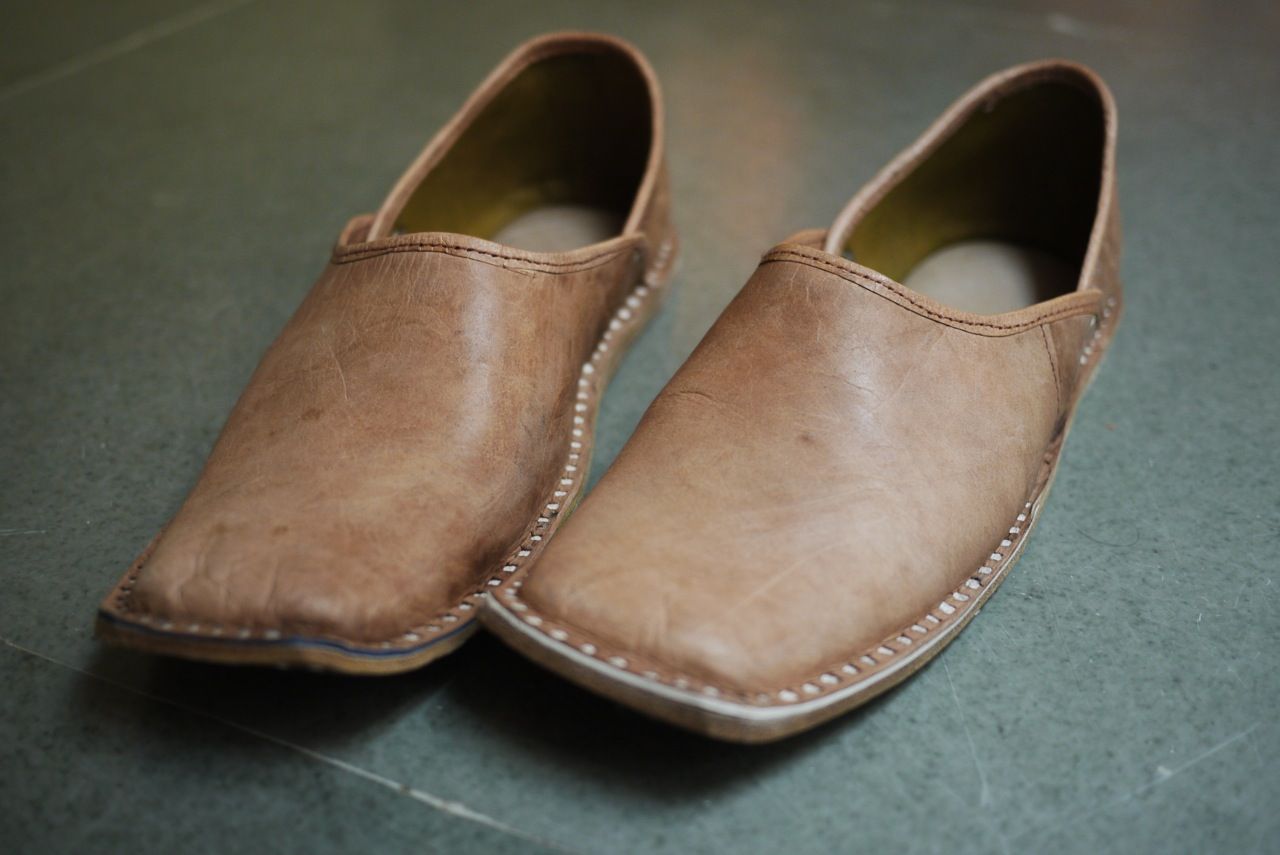
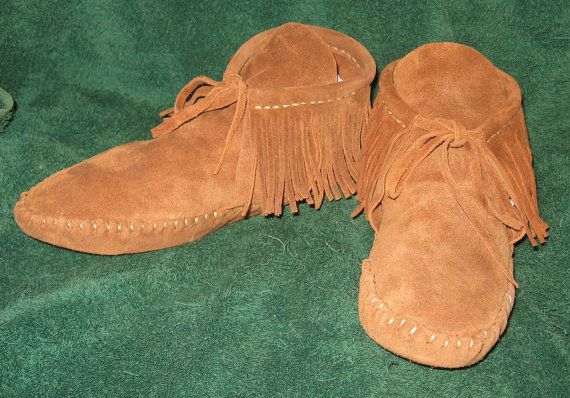
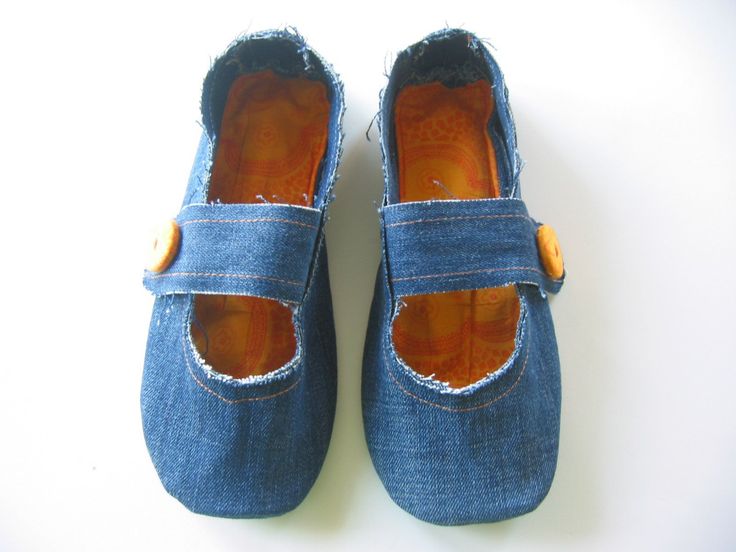
При изготовлении подошвы своими руками применяют:
- Кожу — обладает повышенной стойкостью, прочностью, защищает ногу от внешних повреждений, позволяет ей дышать. Кожаную подошву сделать своими руками не сложнее, чем из любого другого материала.
- Резину — износостойкий материал, устойчивый к морозам, перепадам температуры, обладающий термопластичностью. Характеризуется прочностью, практичностью, долговечностью. Единственным минусом является повышенная маркость такой подошвы.
- ПВХ — дешевый материал, который обладает хорошей износостойкостью, его можно красить. Используется для изготовления зимней обуви. Недостаток — слишком тяжелый.
- ТЭП — изготавливается из термопластичной резины, характеризуется хорошей износостойкостью, не скользит на мокрой дороге. Недостаток — невозможно придать четкие и ровные очертания.
- Полиуретан — имеет низкую теплопроводность, мягкий, легкий, из него изготавливаются любые сезонные модели. Легко поддается ремонту. Обувная индустрия часто использует этот материал. Недостаток — непрочный, быстро истирается.
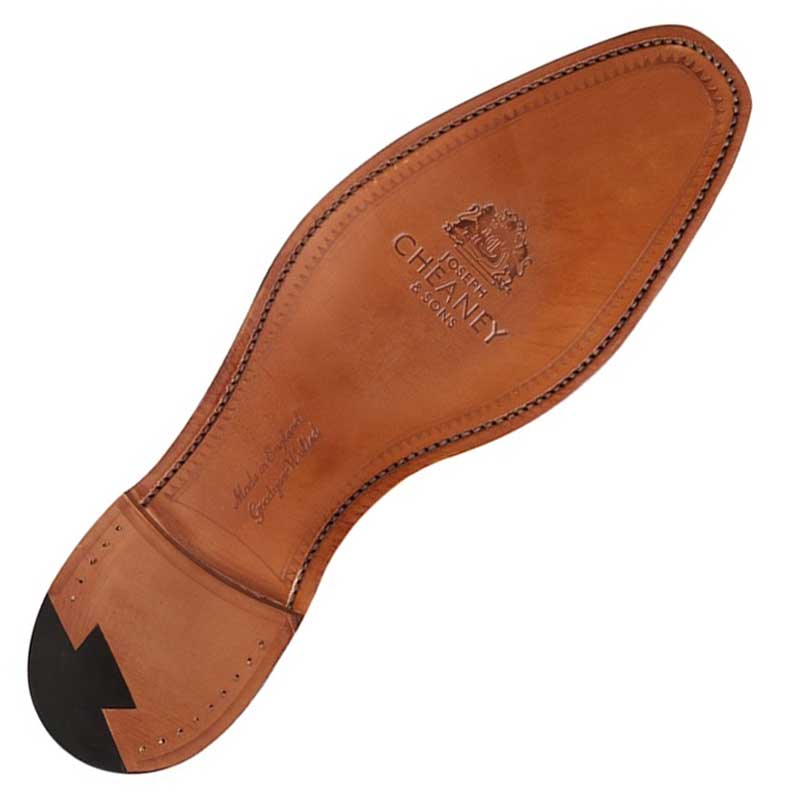
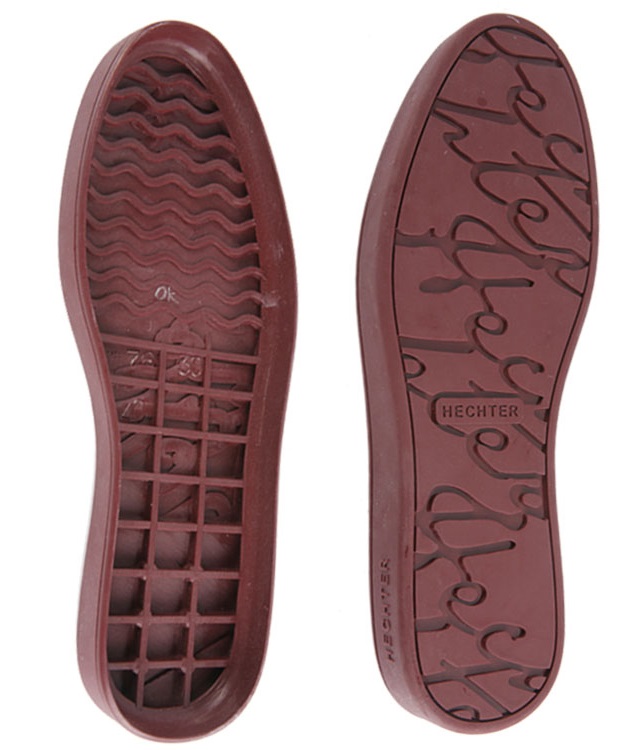
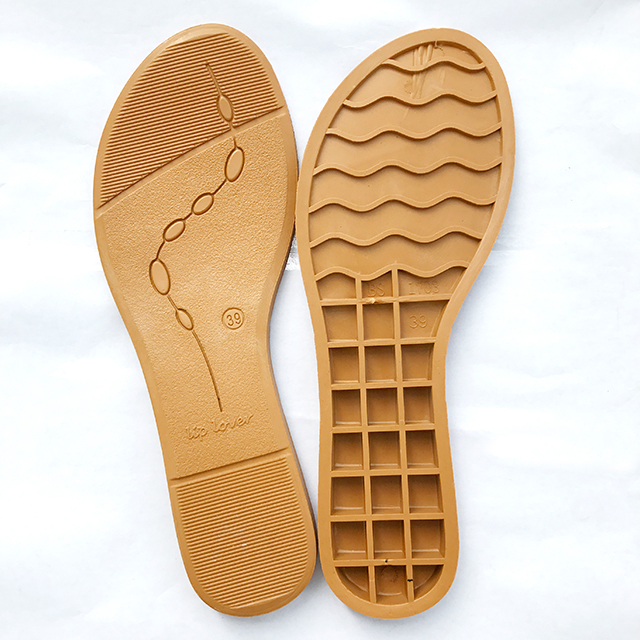
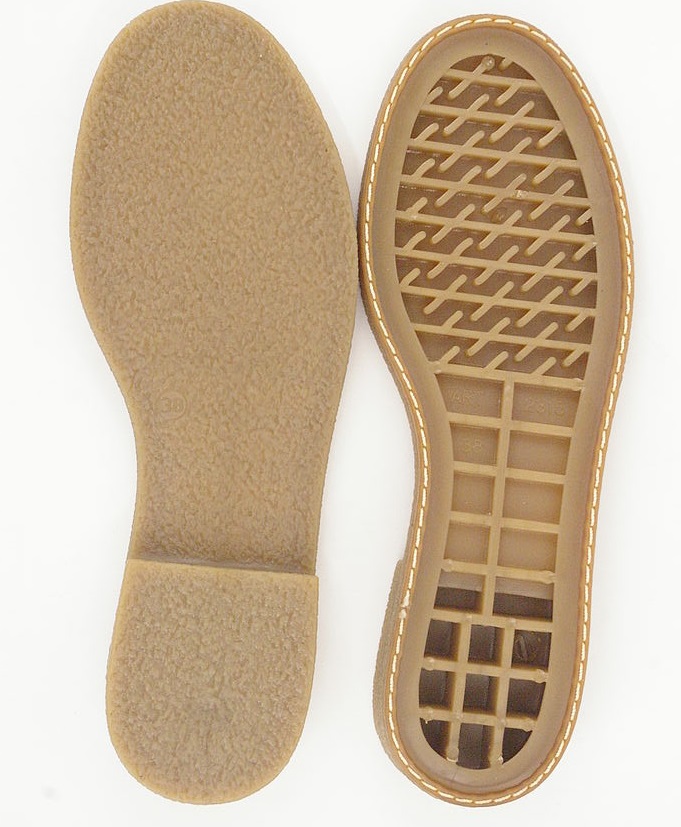
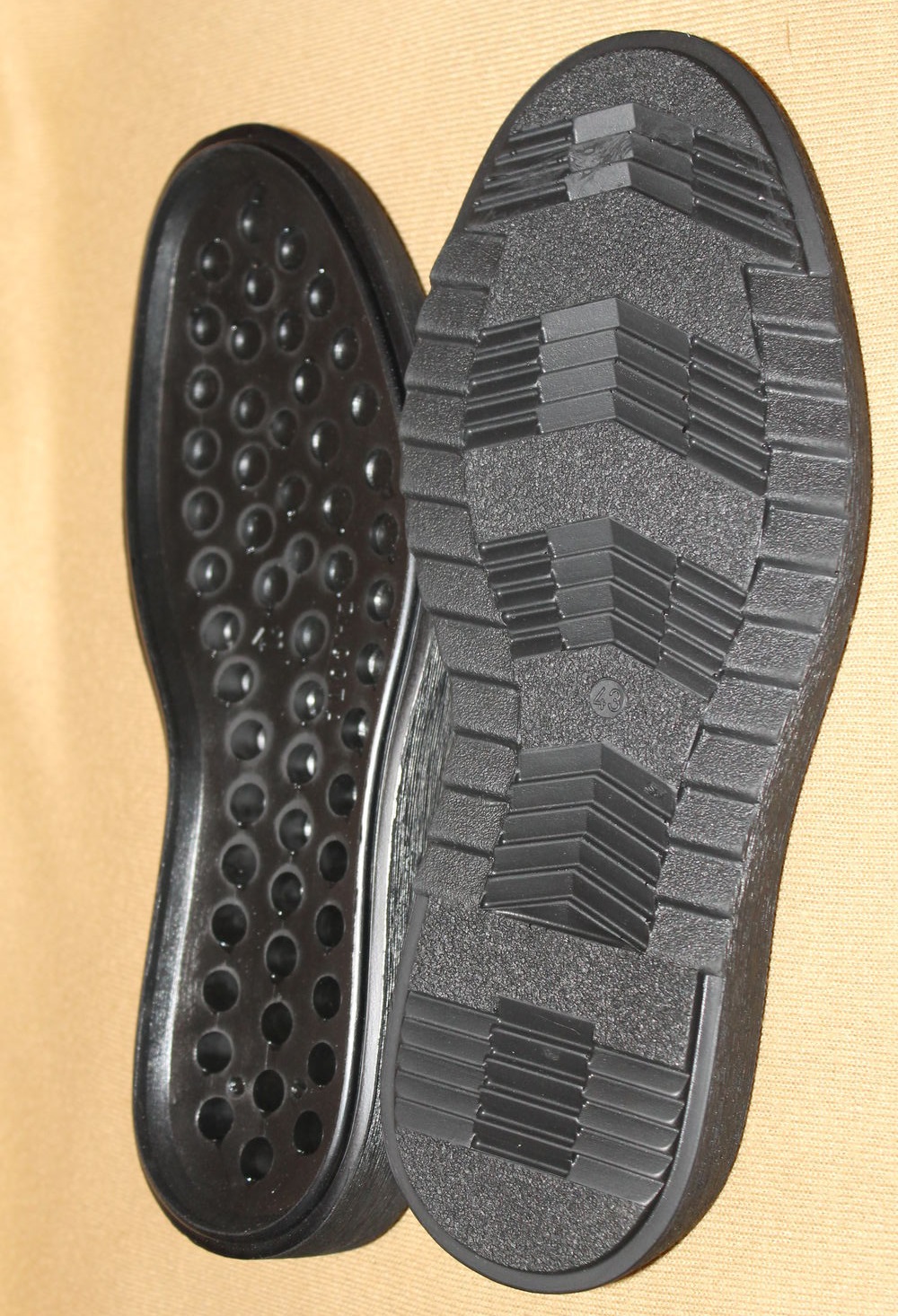
Пошив обуви будет невозможен без следующих инструментов и расходного сырья:
- напильник;
- токмач;
- пчелиный воск;
- шило;
- затяжные клещи;
- молоток;
- сапожный нож;
- полиуретановый клей «Десмокол»;
- гвозди;
- изолента.
Позаботиться о наличии всех необходимых материалов и инструментов стоит заранее, только потом можно переходить к процессу изготовления.
Этапы изготовления
Создание туфель или сапог состоит из последовательных этапов, которые важно соблюдать.
Снятие мерок
Снятие мерок для пошива обуви — первый значимый этап, он помогает определить нужный размер выбранной модели. Пошагово процесс выглядит так:
- нога ставится на белый лист бумаги, стопа обводится по контуру;
- ее длина определяется как расстояние между выступающим пальцем и пяткой, ширина — как расстояние между точками в самой широкой ее части;
- измеряется обхват подъема и лодыжки с помощью мерной ленты;
- определяются обхваты: икроножной мышцы (для высоких сапог), косой через пятку, стопы в самой узкой и самой широкой частях.
Карандаш при обведении стопы надо держать перпендикулярно плоскости бумаги.
Каждая снятая мерка записывается на лист, затем эти параметры используются при изготовлении макета и выкройки.
Создание макета
Следующим этапом создается колодка. В качестве материала используют дерево, которое характеризуется повышенной твердостью, устойчивостью ко влаге. Например, бук, березу, клен. Для работы понадобятся два куска дерева, предпочтительно квадратного сечения.
При выборе брусков надо понимать, какого типа колодка должна получиться: у сапожной горловина должна быть повыше, примерно на 3 см по сравнению с туфельной. Если для первой берется брусок сечением 15 × 15 см, то для второй будет достаточно 12 × 12 см.
Из инструментов нужны:
- топор;
- киянка;
- ножовка по дереву;
- рашпиль;
- набор стамесок и круглых резцов.
Кроме того, пригодится старая обувь, хорошо облегающая ногу. Пошаговый алгоритм:
- На одной стороне бруса рисуется по меркам подошва, а сбоку лекалом вырисовывается профиль будущей желаемой модели.
- Между верхней и нижней частями нужно сделать центральные линии, просверлив два сквозных отверстия.
- Ножовкой или топориком удаляются все ненужные сучки и осколки. После этого заготовке придается форма, схожая с формой ноги.
- Более грубая обработка делается с помощью киянки и стамесок. Потом в ход идут круглые резцы, так как в некоторых местах колодка бывает не только выпуклой, но и вогнутой внутрь.
- В конце проводится шлифовка с использованием наждачной бумаги или рашпилей. Если в обуви планируется каблук, для него нужно создавать специальное углубление.
Сделав колодку по меркам, переходят к созданию предварительного макета. Для этого готовое изделие обшивают тонкой, натуральной кожей. В этот момент уже нужно понять, какой будет модель, предусматриваются ли дополнительные внешние дизайнерские швы, рисунки. Они отмечаются на макете предварительно, затем, ориентируясь на готовый внешний вид модели, переходят к более сложным стадиям изготовления.

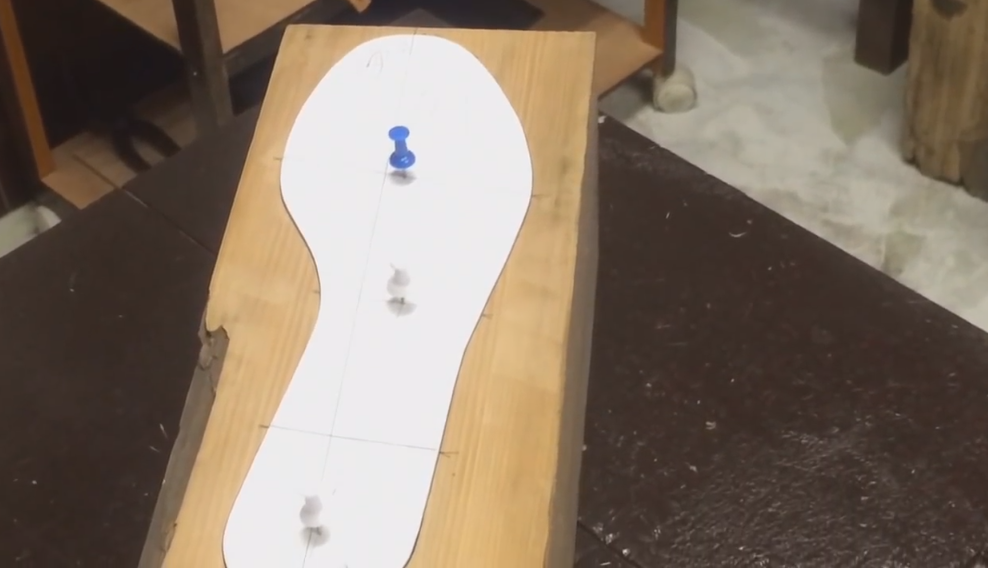
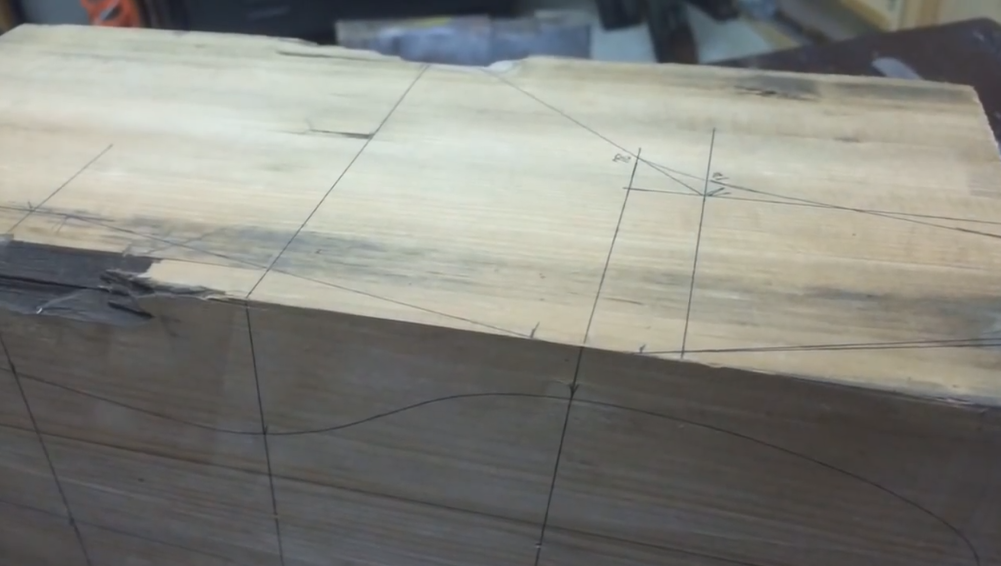
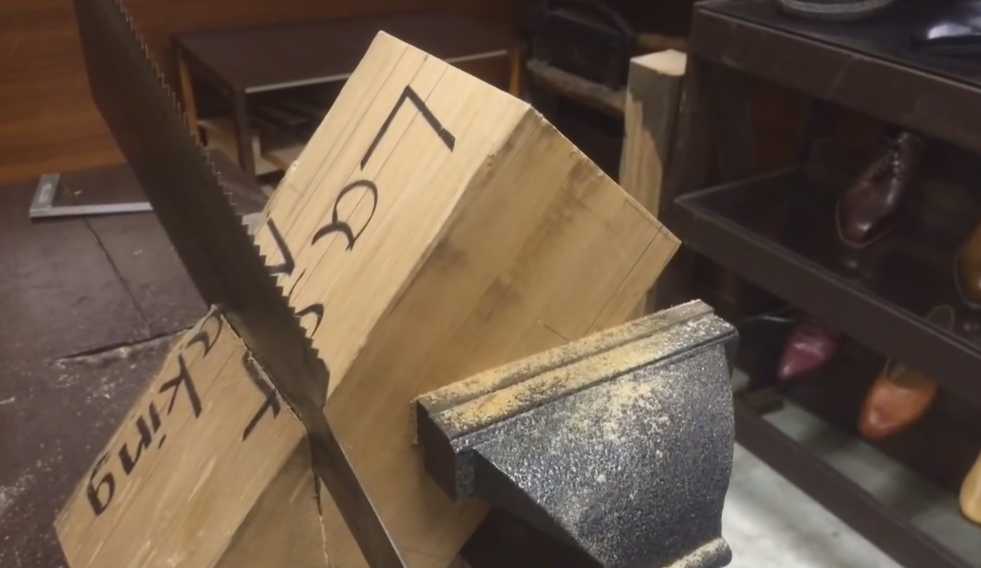
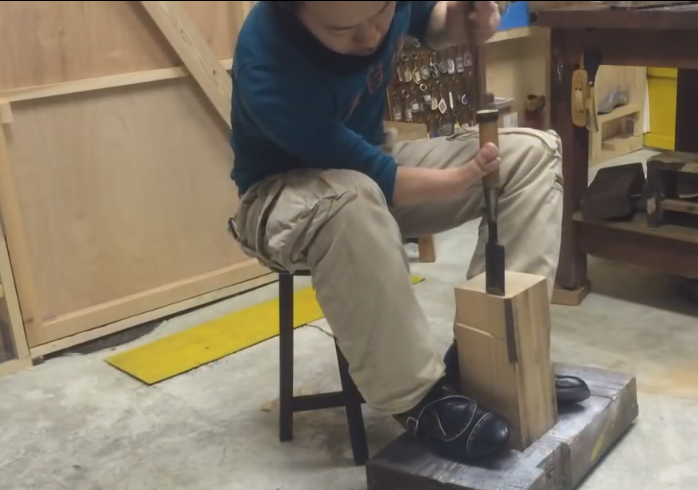
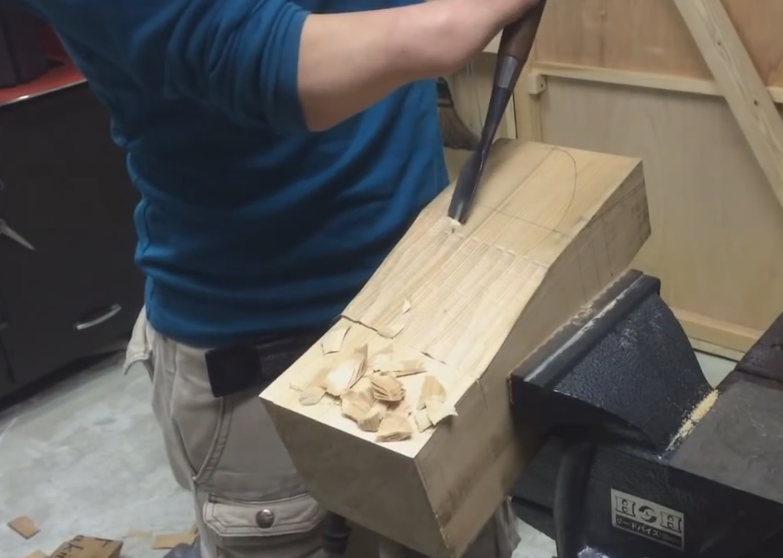
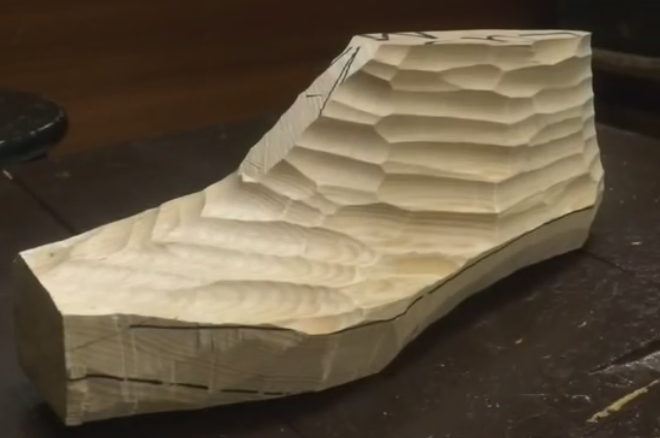
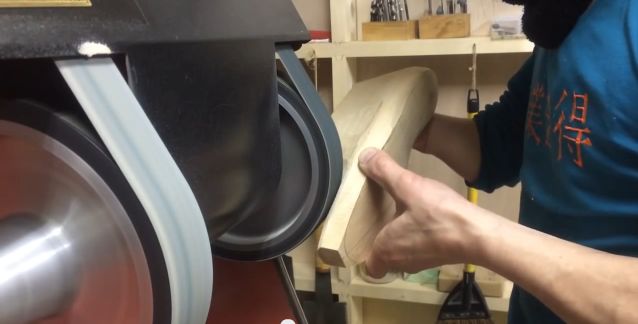
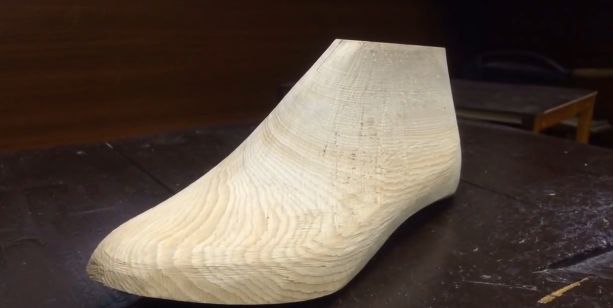
Подготовка выкройки и обметка
Выкройка стельки делается на основе обведенной стопы. При этом она должна быть немного длиннее, форму носка выбирают в зависимости от модели.
Верх строится следующим образом:
- По результатам измерений создается форма, показанная на рисунке. Внешняя и внутренняя длины верха должны точно совпадать с длинами внешнего и внутреннего контура стельки.
- Вырез строится приблизительно, учитывая желаемую глубину от носка в направлении подъема. В процессе работы стоит примерять лекало на ногу — для понимания правильности действий.
- По выкройке обуви, ее верхней части, вырезается заготовка из натуральной замши или кожи.
Вырезать заготовку нужно на 2–3 мм больше, нежели сама выкройка. В таком случае при изготовлении обуви она не будет маломерить.
Подкладку кроят по той же выкройке обуви. Верхняя и подкладочная части сшиваются или склеиваются друг с другом. Края нужно максимально подровнять, обточить кожу при необходимости, подкрасить изделие, чтобы оно имело вид, максимально приближенный к желаемой модели обуви.
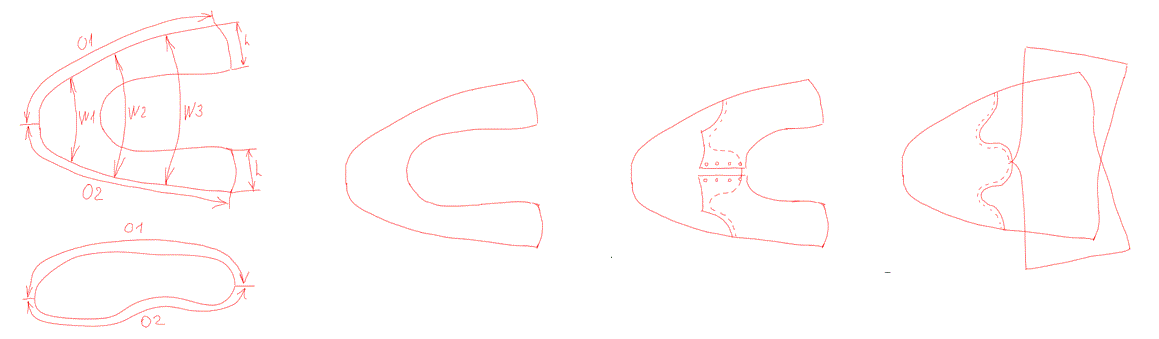
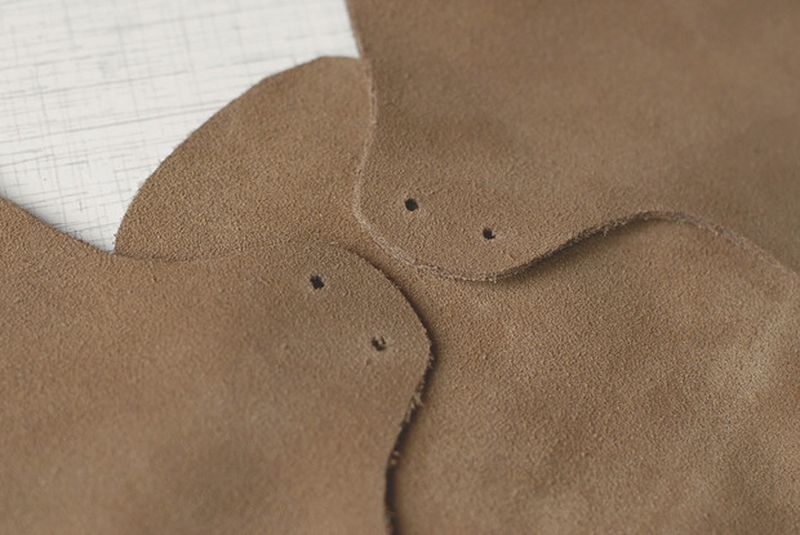
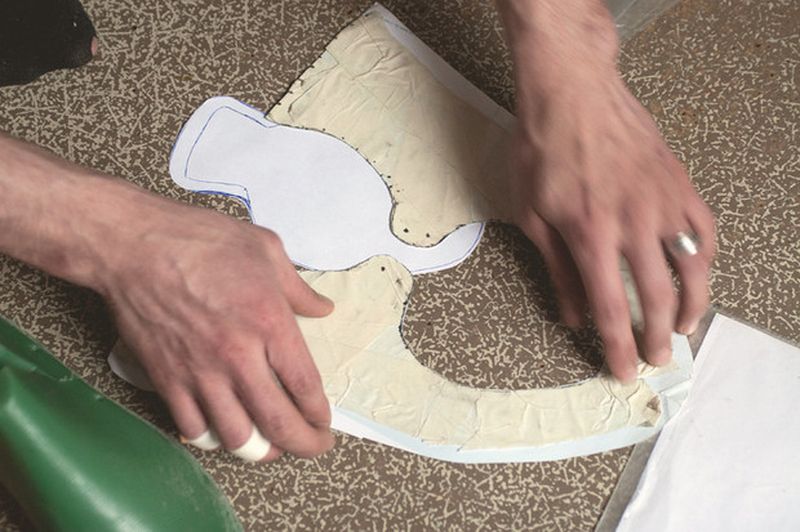
Натягивание заготовки и нашивка ранта
Изготовление продолжается: на подготовленную колодку нужно натянуть верх обуви, важно научиться это делать очень плотно. После чего надо уложить стельку. Этот этап производства особенно важен, от него будут зависеть удобство и комфорт при хождении.
Рант — это тонкая кожаная полоска, которая соединяет все части будущей модели, натянутые на колодку. Наличие этой детали позволяет ремонтировать любую модель в случае повреждения подошвы или колодки.
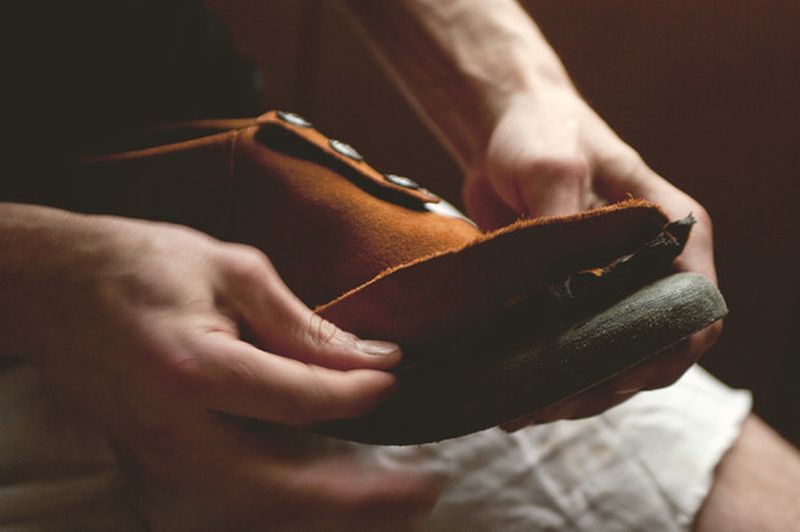
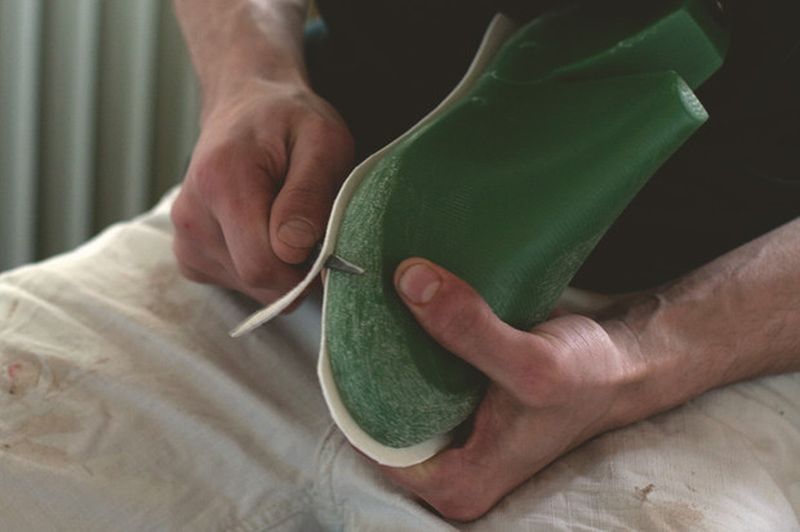
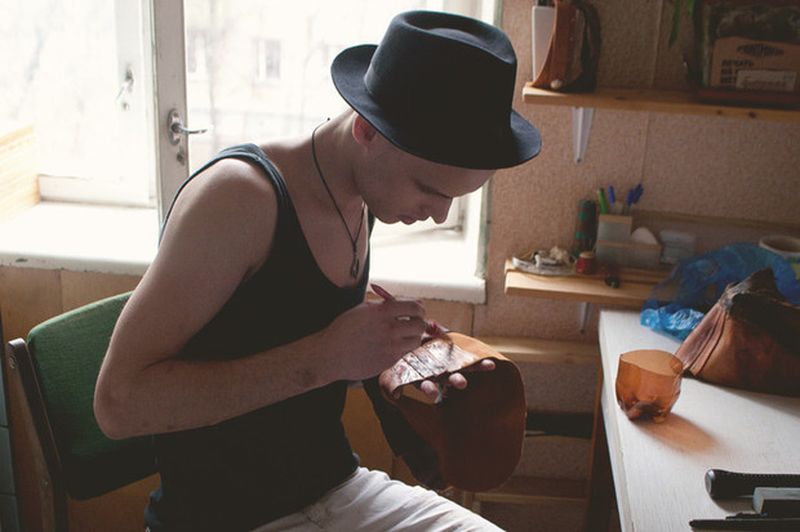
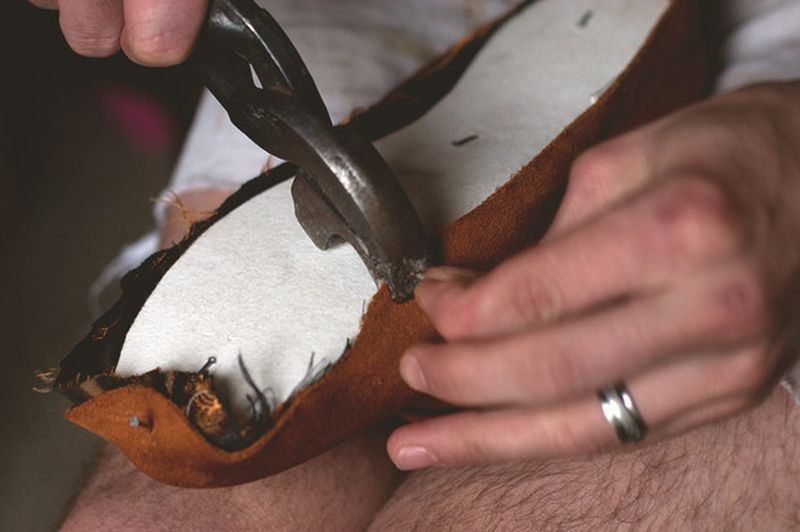
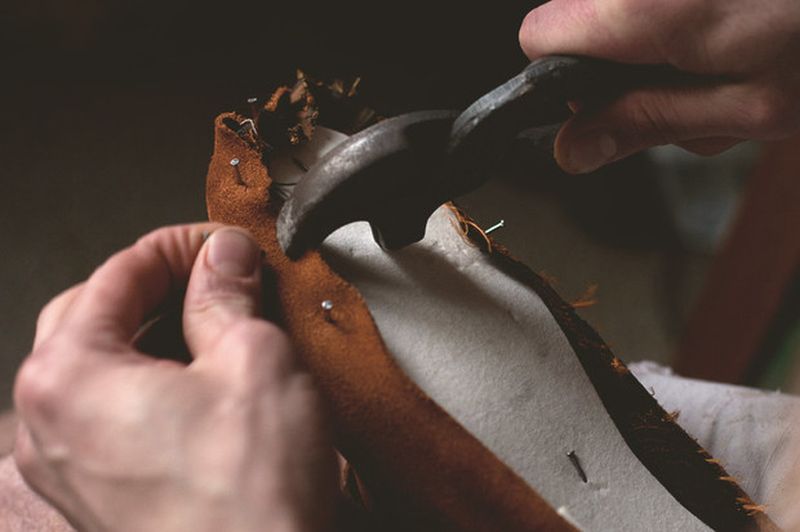
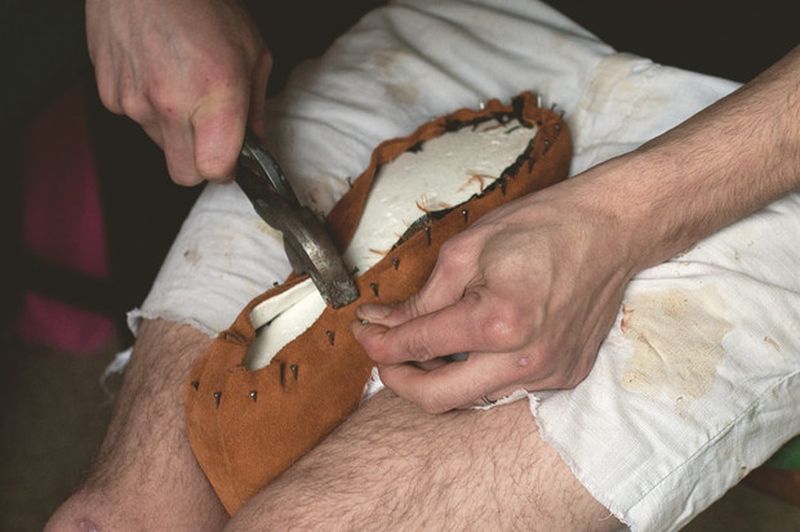
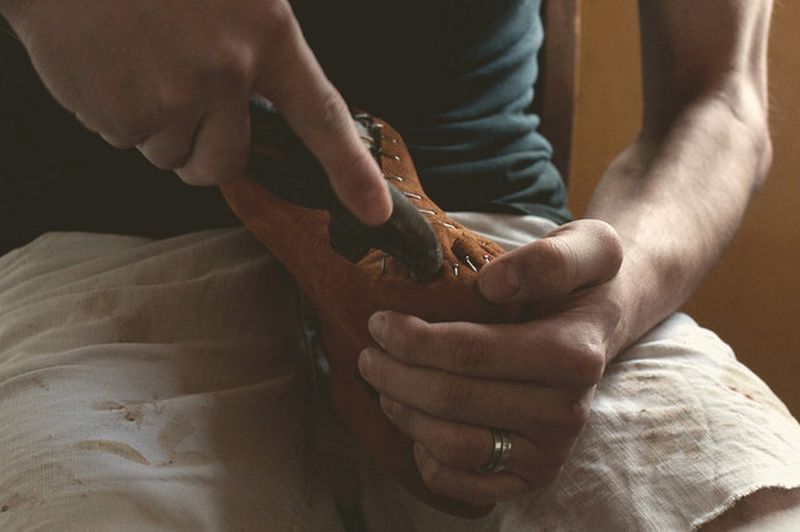
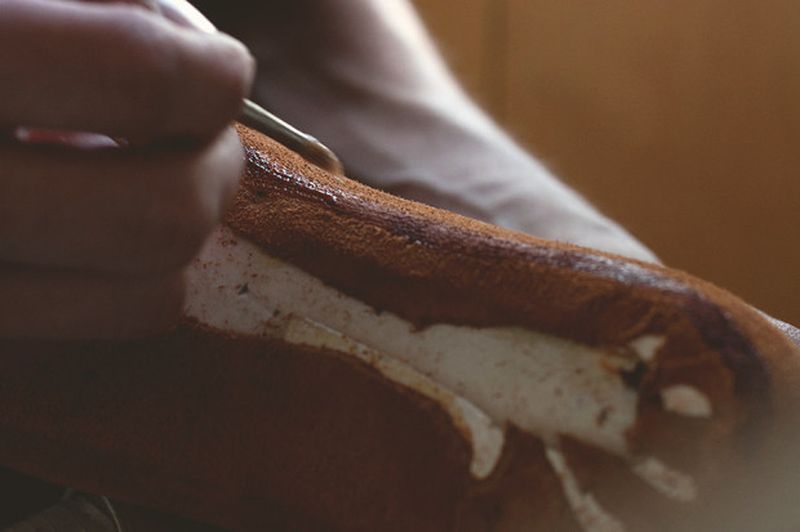

Пришивание, окрашивание и полирование подошвы
Подошва бывает разной, чаще каучуковой или кожаной. Укреплять ее нужно специальными маленькими гвоздиками, которые обеспечивают надежность и долговечность. Если нужно пришить каблук, используют несколько слоев кожи.
Недостаточно просто изготовить модель самому и сшить правильный макет, необходимо еще уметь профессионально окрасить подошву и отполировать ее. Цвет зависит от тона обуви. После нанесения краски нужно подождать, пока она полностью высохнет. Самостоятельное производство обуви заканчивается этапом полировки.
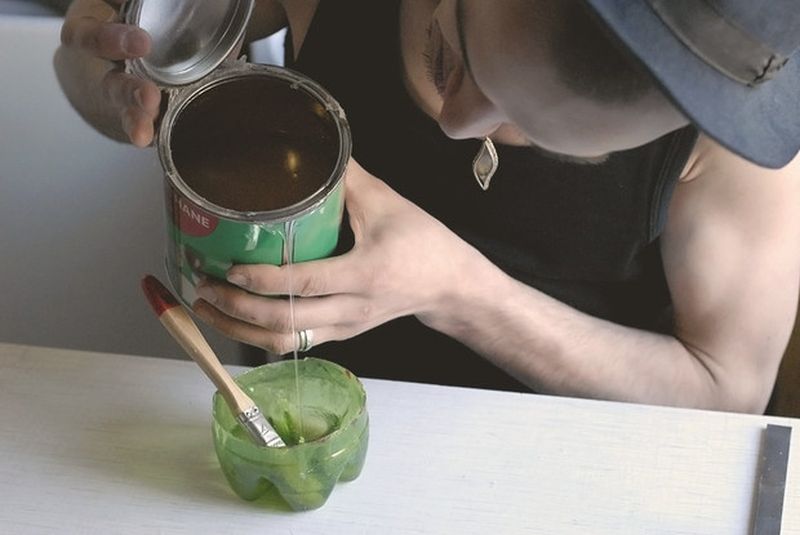
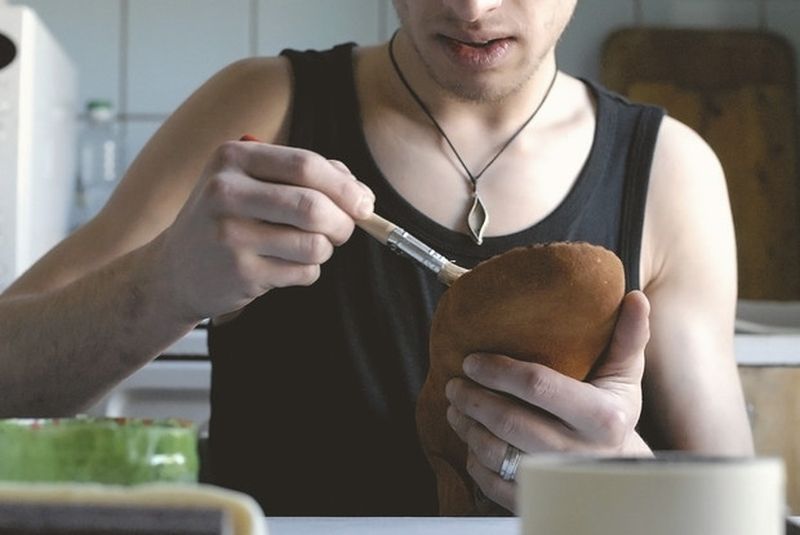
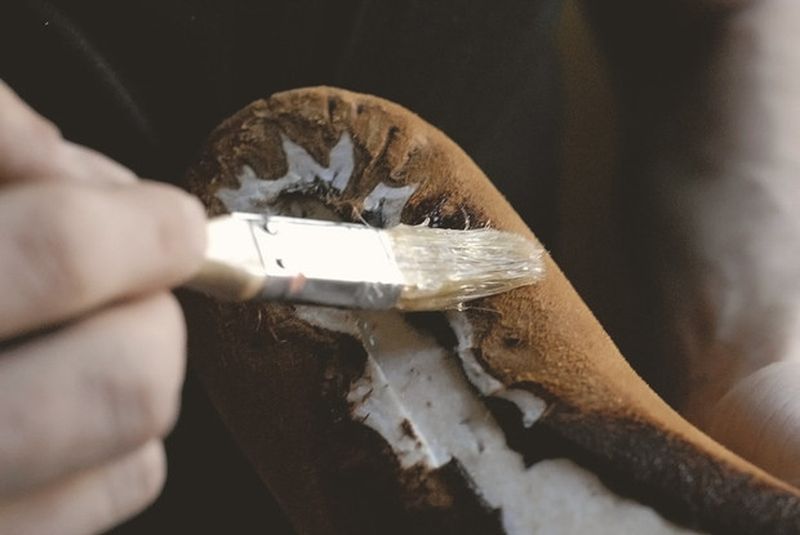
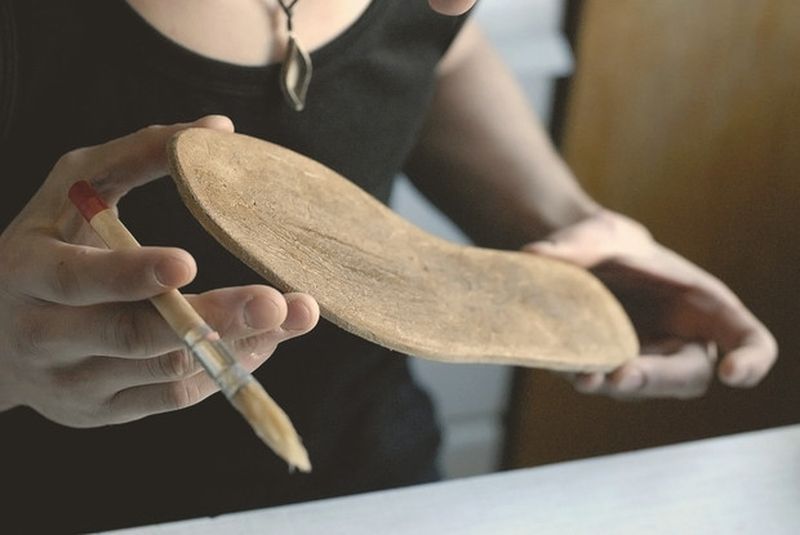
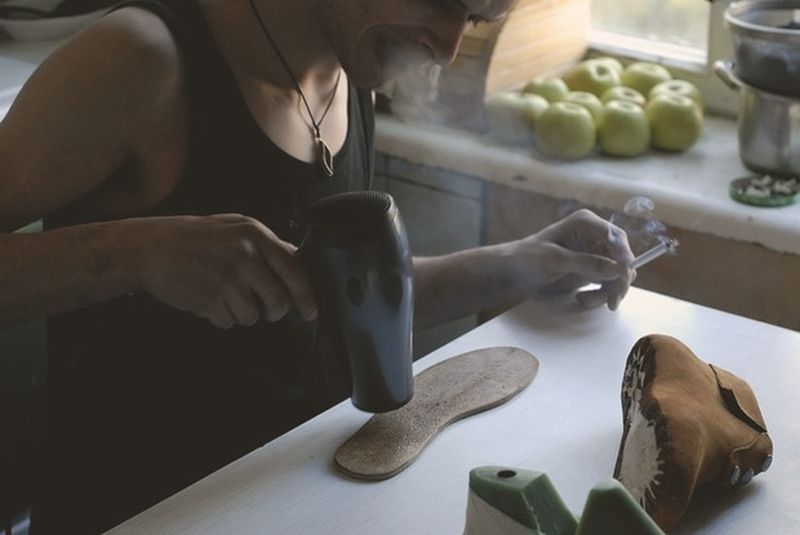
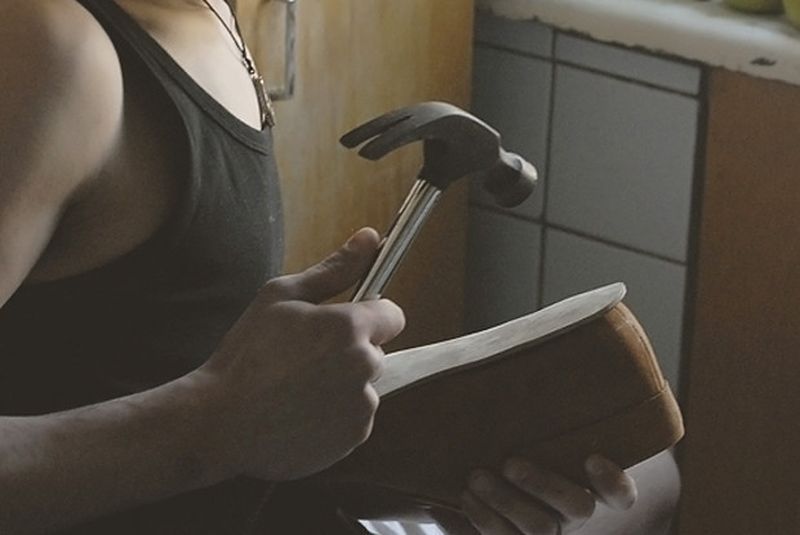
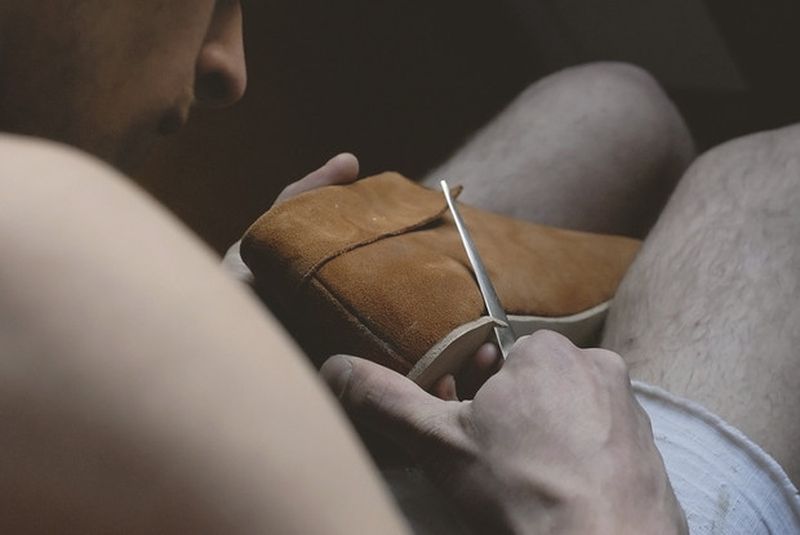
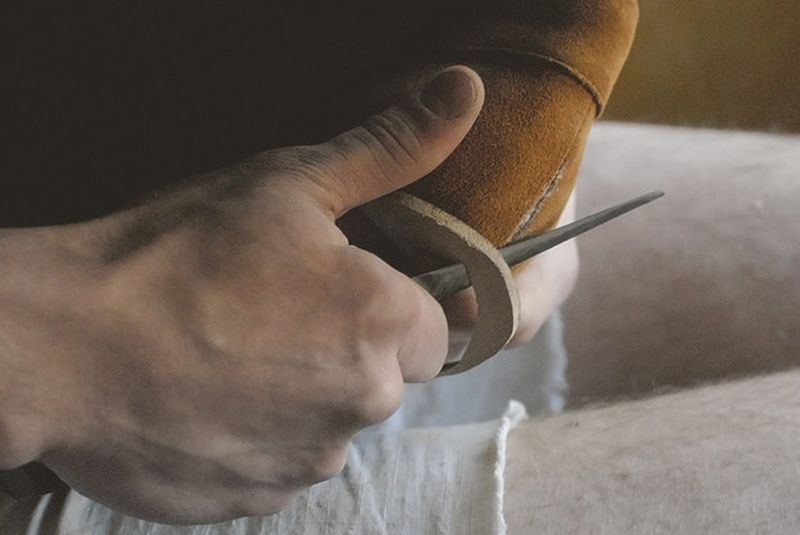
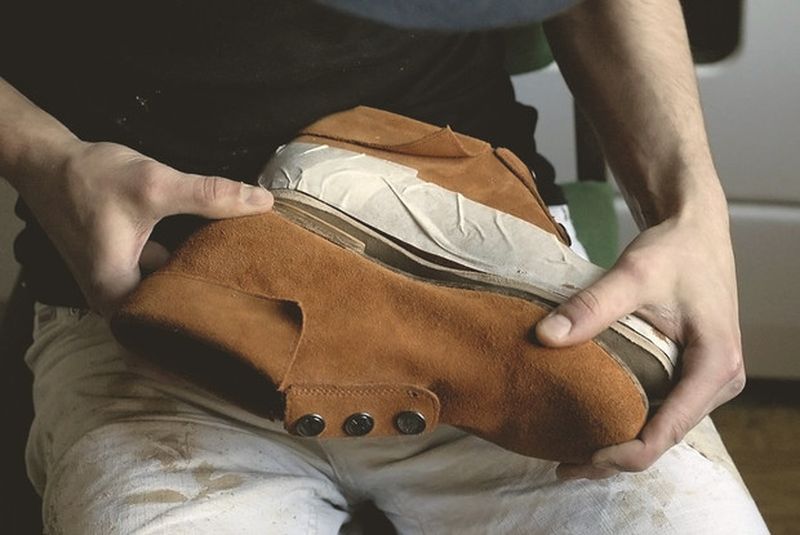
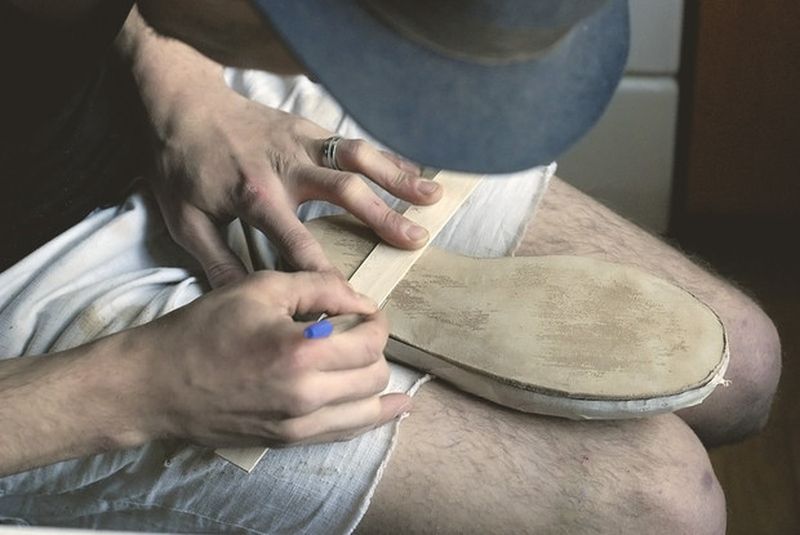
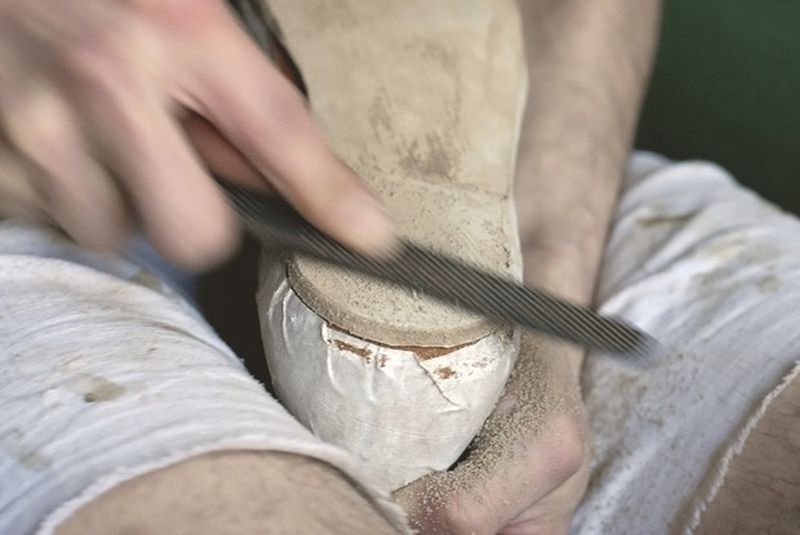
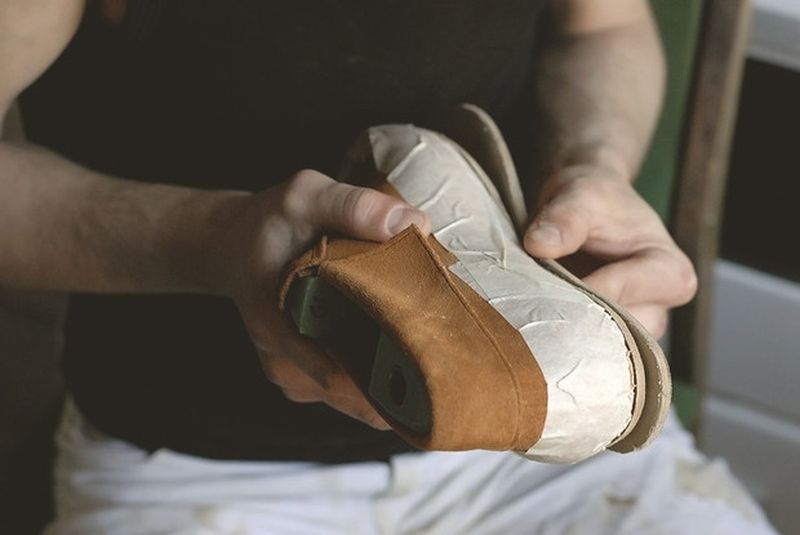
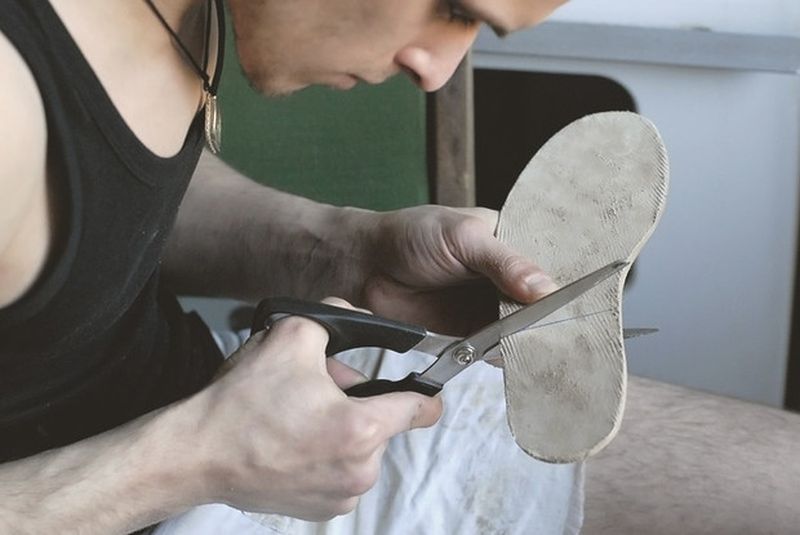
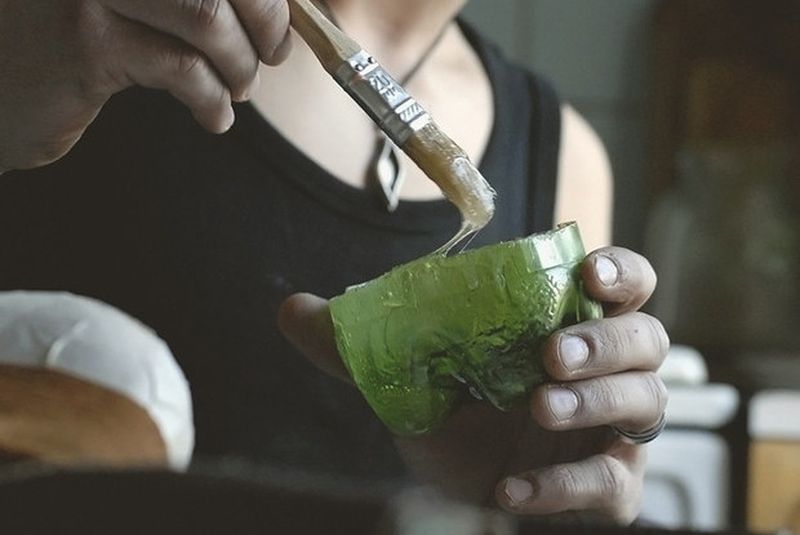
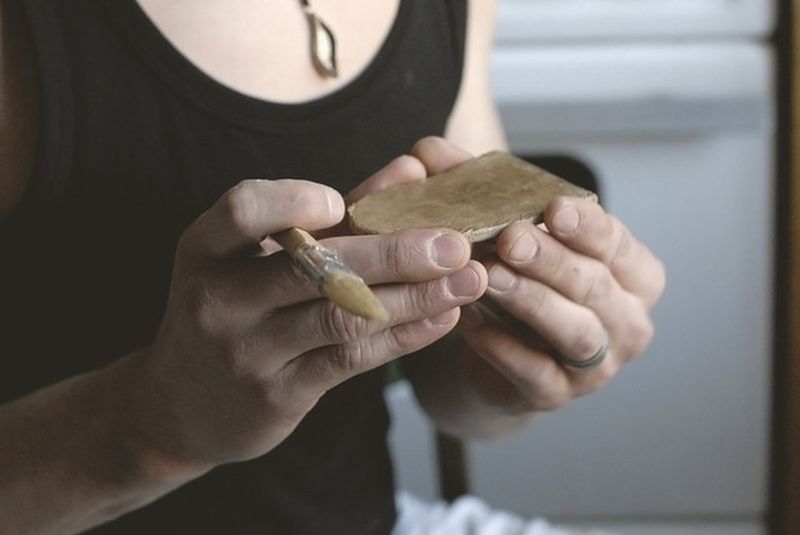

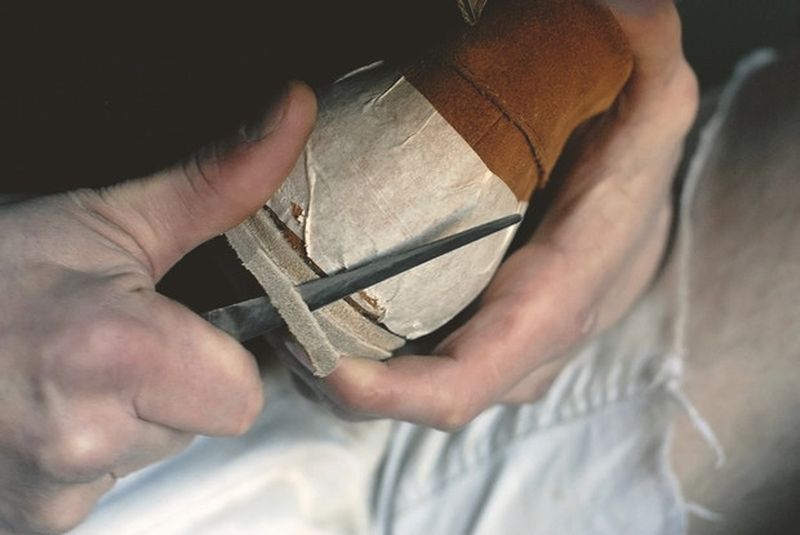
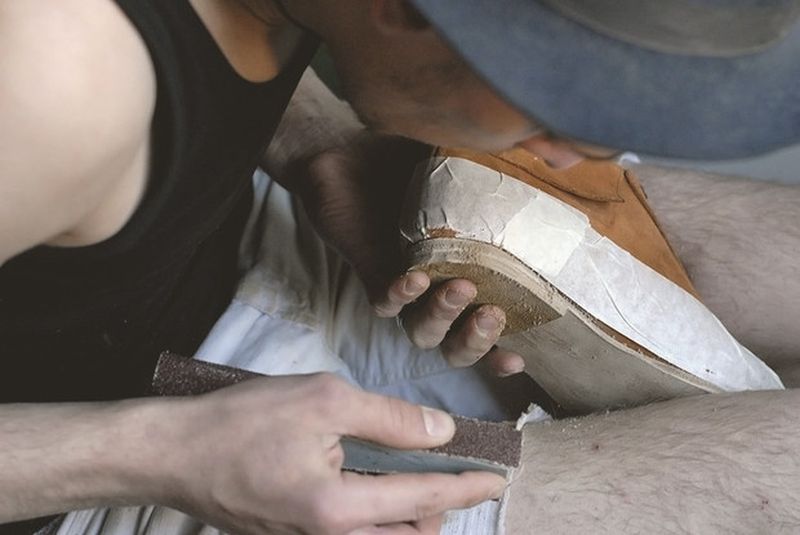
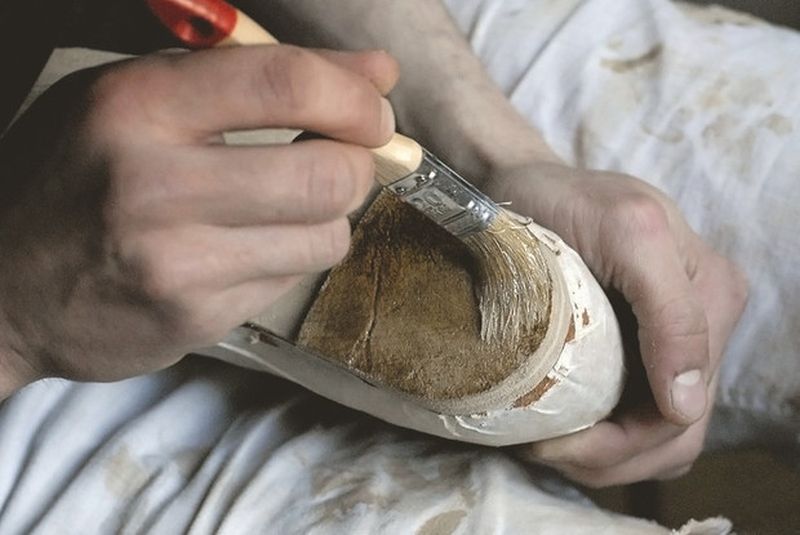
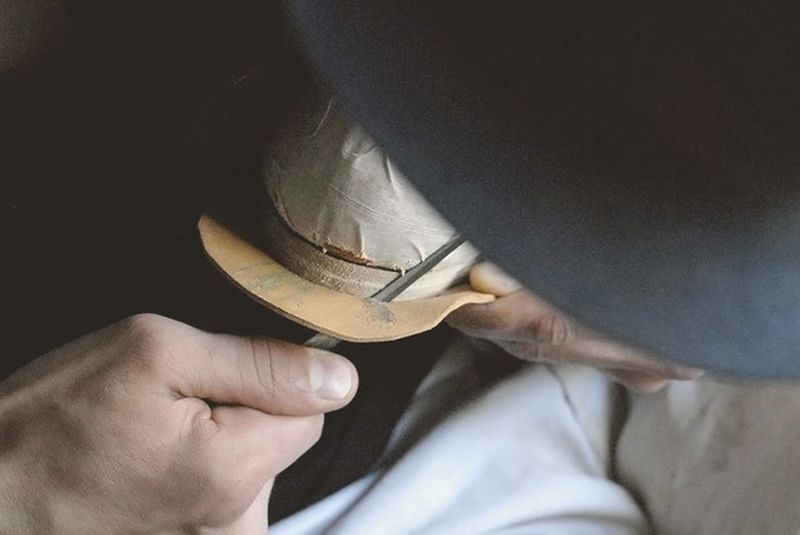
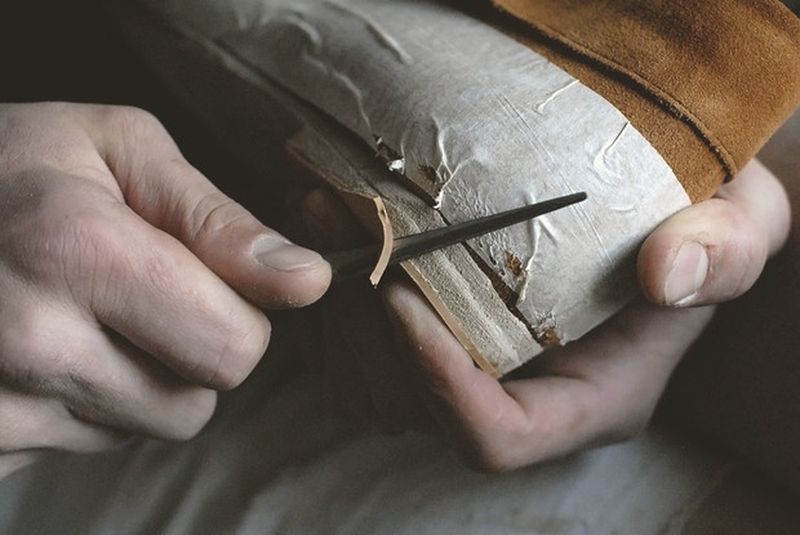
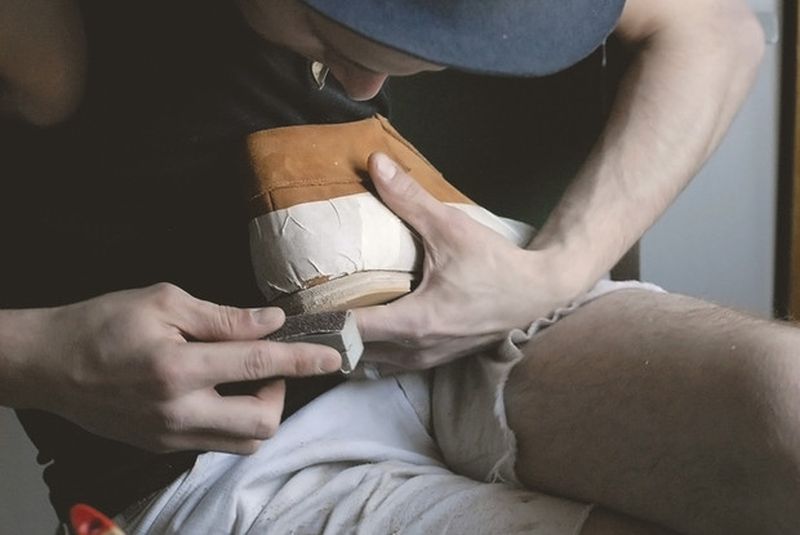
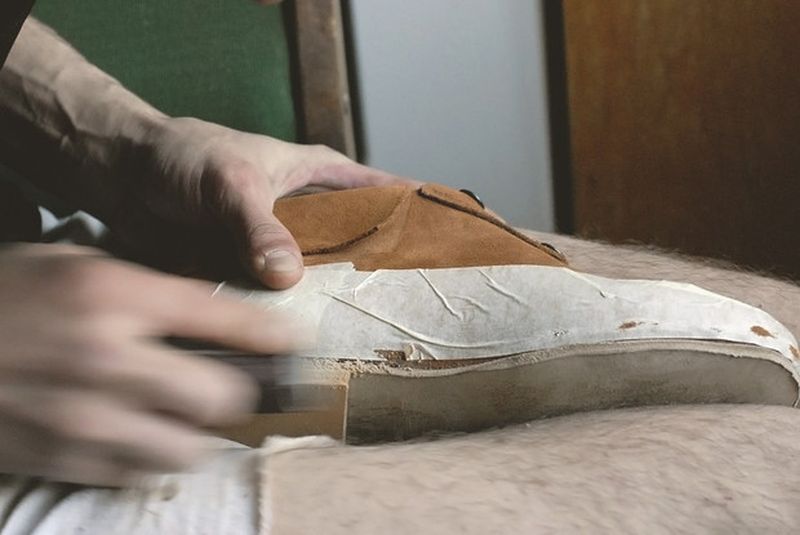
Декор
Самодельная обувь ручной работы может украшаться по фантазии мастера, используя различные стразы, банты, заклепки, кнопки и другие аксессуары. Для создания декора используют специальные инструменты. Чаще всего банты или стразы сажаются на клей, реже производители используют миниатюрные гвозди. Для домашнего украшения туфель оптимальным вариантом будет как раз сильнодействующее клеящее вещество, предназначенное специально для декорирования.
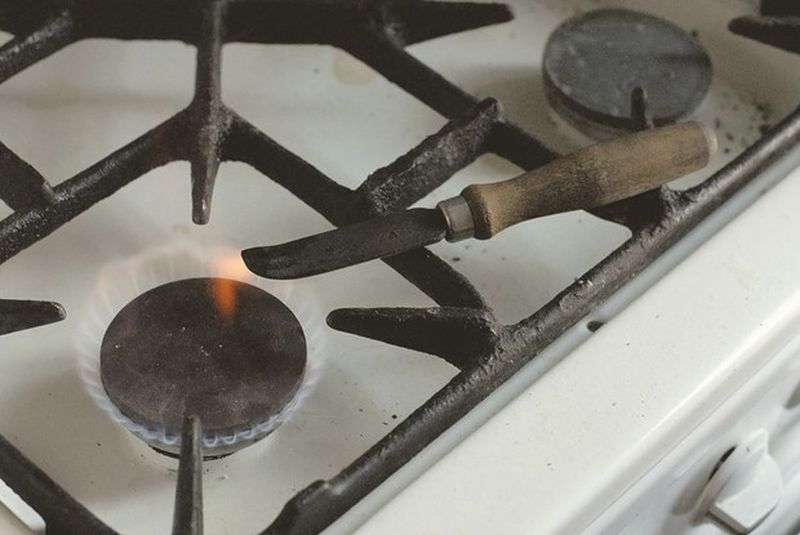
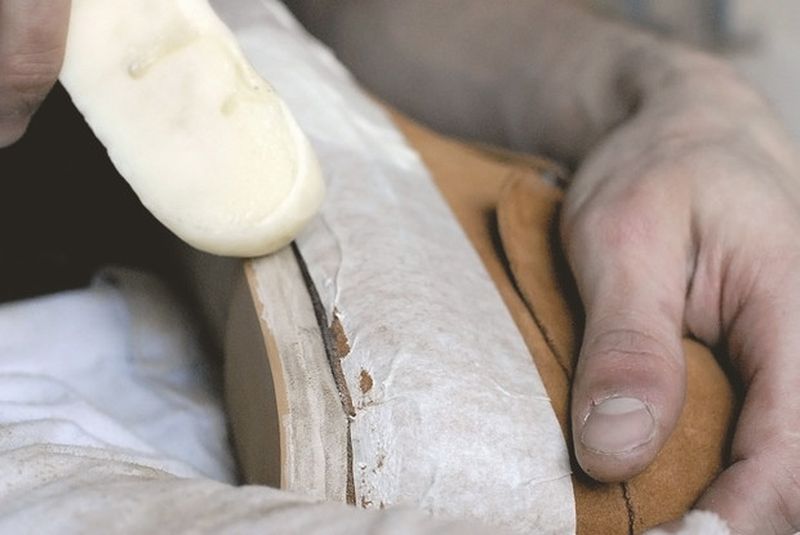
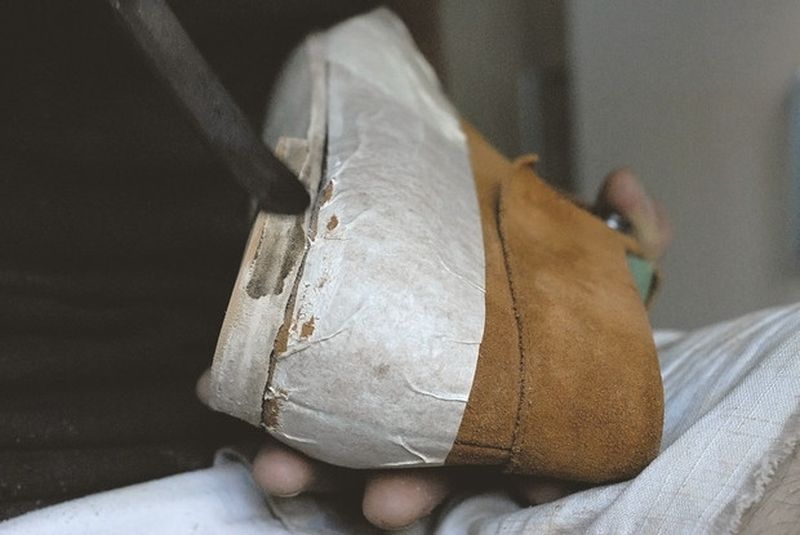
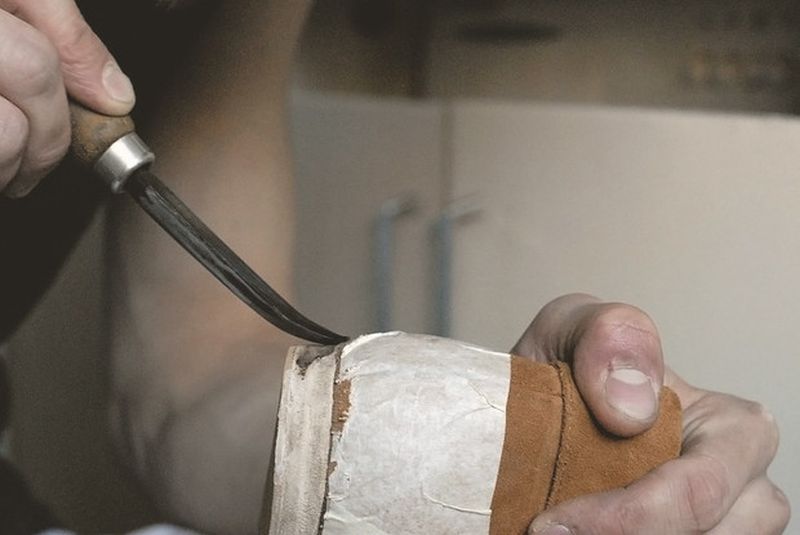
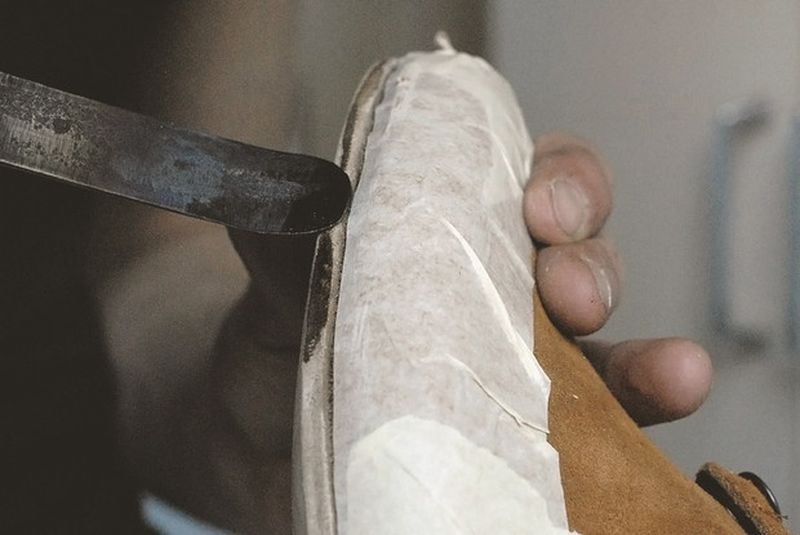
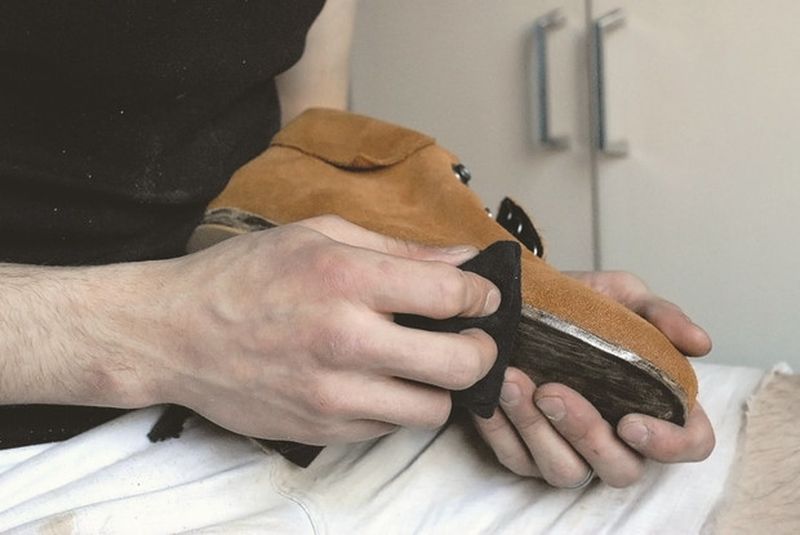
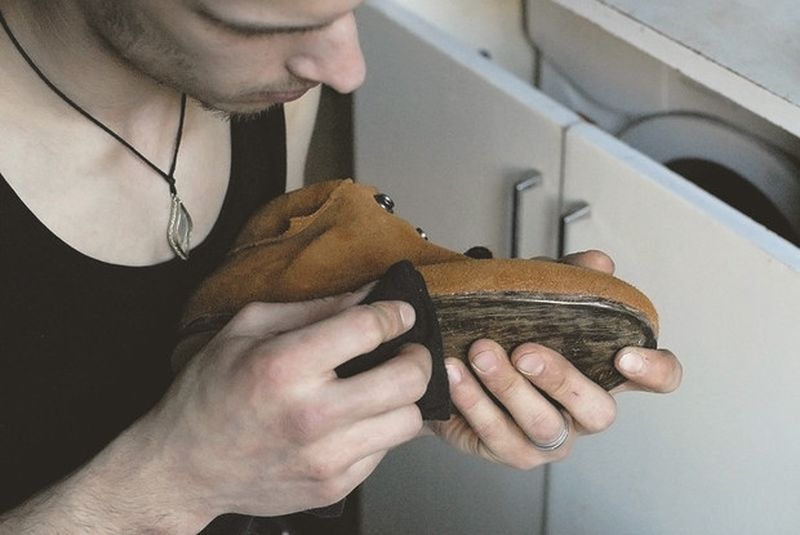
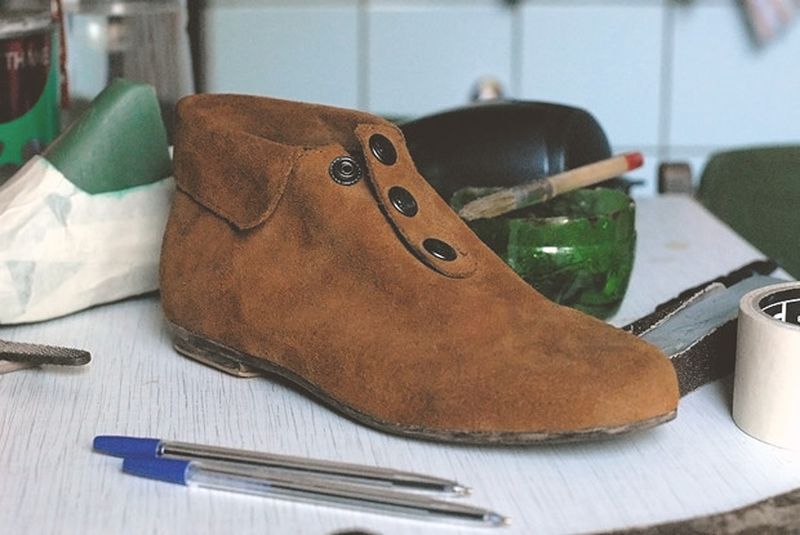
Видео
Мужская работа или как я училась делать обувь
Уже не помню как все начиналось и что именно меня сподвигло на пошив обуви. Возможно желание уметь то, чего не умею и кажется нереально трудным. А может быть желание заняться тем, чем не получилось раньше.
Так или иначе обдумывала это решение очень долго. Взвешивала доводы за и против, и конечно сумма за обучение тоже требовала согласия всего моего внутреннего я. Но время не изменило решения и вот я пошла.
Предстояло приобрести ещё много материалов для обучения и для непосредственного изготовления. Как обычно бывает времени отведенного на объяснение материала и особенно на его усвоение и повтор оказалось мало. Необходимо было вникать, повторять и тренироваться дома.
Можно сказать мне повезло в том, что нас было мало человек и больше времени уделялось каждому. Конечно, если изучать все с нуля, это очень сложно. Но с каждым занятием, я поднимала из своих глубин, подзабытые знания и умения.
Для всего этого процесса необходимо знание не только строения человека, его скелета, системы мышц, других систем, их взаимодействие и функции, но также конструирование базисных моделей. Это важнейший материал, именно на нем строится вся последующая работа.
Мы знакомились с итальянской методикой построения обуви. Она больше рассчитана на творческий процесс и доработку уже в материале, там меньше формул и четких характеристик. Поэтому она больше подходит для ручного изготовления обуви, дает возможности творчества. Несмотря на это, нужно было обязательно запомнить несколько расчетных формул и постоянных величин.
Как оказалось существует несколько способов построения отдельных элементов, видимо каждый мастер делает как ему удобно. и конечно есть абсолютно обязательные основы, которые нужно соблюдать, чтобы получить анатомически правильную конструкцию и в конечном итоге саму обувь.
У каждого, кто пришел на эти курсы были свои мысли и цели. У каждого были разные возможности. У каждого своя колодка и поэтому все получилось разное.
После построения базовых моделей, мы в итоге должны были построить свою. По чертежам выбранных моделей нужно было выполнить деталировку верха и подкладки. Благодаря разным формам колодок и разным рукам, рисовавшим конструкцию и детали, одинаковая модель была настолько разной. В этом я убедилась абсолютно точно.
С этим багажом мы шли на сборку заготовки. Там под чутким руководством раскроили верх, подкладку и дублирующий материал. Одновременно получили знания по выбору материалов, по дефектам допустимым и нет, по нормам раскладки деталей и прочее. Конечно при раскрое нескольких пар мастера стараются сократить отходы и использовать материал по максимуму. Поэтому в процессе раскроя есть нормы и правила. Если раскрой деталей идет из натуральной кожи, то необходимо знать топографические участки шкуры. Чтобы пара была одинаковой не только по материалу, но и по качеству, необходимо производить раскрой по правилам.
Сборка заготовки дело крапотливое, требует внимания и сосредоточение. Также у каждой конструкции есть своя последовательность операций сборки. Она может быть на швейной машинке, так и ручная. Качество и аккуратность сборки будет отражаться в готовом изделии. Ничего не должно мешать ноге в обуви, все нитки и узелки аккуратно убираются внутрь между деталями.
Много всяких тонкостей, о которых можно только лично, на своем опыте и с мастером узнать. Так сказать из рук в руки. Заготовка готова, приступаем к самому сложном — затяжка на колодку. Для меня это было очень интересно, это было то, чего я совсем не умела и делала впервые. Все это подогревало мой интерес, несмотря на физически сложные вещи.
Это надо понимать именно буквально — нужна определенная сила для многих операций. Запросто можно вспотеть. Видимо поэтому изготовление обуви считается мужской профессией. Вообщем, этот процесс мне очень понравился. Сложность самого процесса затяжки во многом зависит от самого материала заготовки, от его качества и свойств. Некоторые материалы лучше смочить водой для лучшей податливости. Какие-то и так хорошо затягиваются.
И вроде бы все делается приблизительно, так скажем на глазок… Но этот глазок должен быть хорошо заточен и откалиброван. Немного неприятных моментов было связано с запахами клея и ацетона. Хорошо это решается проветриванием помещения. Ещё один момент, затяжку надо делать побыстрее, пока совсем не высох клей. Нужно успеть разгладить складочки и замены, иначе они останутся в готовой обуви. А дальше, выравнивая складки образовавшиеся по следу колодки, параллельно вбивать зятяжные гвоздики, чтобы уменьшить толщину затяжной кромки и закрепить для формовки. Но это все оказалось не самым сложным.
Самое самое сложное это вырезание подошвы и её приклеивание. Конечно можно подобрать готовую под вашу колодку, но раз уж мы учимся — так учимся всему. И вырезанию подошвы и каблука тоже. Самым опасным инструментом, на мой взгляд, был обувной нож для вырезания подошвы. Он самый большой и должен быть самым острым, потому как вырезать подошву — очень тяжело. Делается это в несколько приемов. Вообщем ручное изготовление обуви дело очень занимательное, но требующие мужской силы. Поэтому да, сапожником должен быть мужчина. А с другой стороны, используя современные девайсы, приспособления и инструменты, возможно облегчить этот процесс.
Итогом всего курса была готовая полупара, почти доделанная к ней вторая и много правил и требований к рабочему месту, инструментам и самим действиям во время процесса.
Ещё я узнала, что замшу сейчас почти не изготавливают, это очень дорогой материал, требующий особого сырья и дорогой отделки. Так что вот, покупаем мы с вами либо, велюр, либо список.
Екатеринбуржец, ставший мастером–обувщиком о том, как и зачем делать ботинки своими руками
Уютное помещение освещают солнечные лучи. Заходя в мастерскую, чувствуешь слегка уловимые ароматы кожи и воска. В окружении старинных инструментов, шуршащей кальки и кожаных лоскутов мастер вручную собирает уникальную пару обуви. Иван Белов – владелец мастерской, по профессии юрист, но это никак не мешает ему заниматься тем, что нравится. Он рассказал It’s My City, как создается обувь ручной работы.
Как появилась идея открыть мастерскую?
Случилось это два с половиной года назад: я смотрел видео-ролики в интернете, и в них процесс создания обуви показался мне не только интересным, но и «простым». После детального изучения технологии решил заняться этим более углубленно. На деле же оказалось, что это не так просто. Я искал различные курсы, но по тем или иным причинам они не подходили, приходилось учиться по роликам в интернете и книгам.
В итоге мне удалось выйти на специалиста в Москве. Договорился и поехал к нему на несколько дней. Ехал целенаправленно и с неким «чемоданом» теоретических знаний, не подкрепленных практикой. Именно там, в процессе построения первой пары и пришло понимание, что это то ремесло, которое действительно мне интересно.
В день отъезда из Москвы не было ничего необычного, кроме того факта, что я шагал в ботинках сделанных своими руками
После возвращения стал задумываться о покупке необходимых материалов. Первой и серьезной статьей расходов стала покупка швейной машинки, а вот с инструментами возникли трудности. Основная часть закупалась в Германии, потому что у нас найти хороший инструмент практически невозможно. Кожу тоже нужно закупать заграницей, поскольку все известные дубильни (производители качественных кож) находятся именно там.
Мастерская в ее сегодняшнем виде, со знаниями и философией, появилась год назад. Весь процесс изготовления обуви происходит именно здесь, в Екатеринбурге.
С чего начинают делать обувь?
Все начинается с замеров. Человек приходит, с каждой ноги я снимаю мерки. Для этого изготавливаются индивидуальные колодки. Колодка – самая важная деталь в процессе изготовления обуви, в индивидуальном изготовлении она максимально повторяет форму стопы и влияет на внешний вид будущей пары. Так что в следующий раз заказчик может мне позвонить из любой точки земного шара и заказать ботинки, просто прислав рисунок.
Следующий этап – лекала будущего ботинка, затем из них вырезаются все из кожи и натягивается на колодку с помощью затяжных клещей, после приколачивается гвоздями и прошивается. Затем идут подошва, стельки, каблук. Это тоже делается из кожи. Прежде чем сделать основную пару, я делаю пробную и как минимум три раза мы встречаемся с заказчиком. Весь процесс создания обуви делается вручную, без использования промышленных мощностей.
Чтобы делать обувь, не нужно каких-то исключительных инструментов. Все инструменты обычные. Например, гвозди – расходный, но необходимый материал. Помню, когда я был маленьким, то помогал деду что-то колотить, и одной из моих задач было выпрямлять гвозди для будущих работ. Сейчас я, конечно, этого не делаю, но бережное отношение к инструменту осталось с детства.
Ваш самый любимый этап в создании обуви?
Я пытался понять, что мне больше всего нравится в этом ремесле, но здесь все по-своему интересно. Мне нравится рисовать, моделировать, работать с кожей. Единственное – не нравится ждать, когда я сниму ботинок с колодки. В старые времена нужно было выдерживать ботинок два–три месяца. Сейчас все быстрее, у меня с момента замеров до готовой пары проходит примерно 35-40 дней.
А вообще, здорово прикоснуться к ремеслу, которое когда–то определило сегодняшний уровень производства обуви. Сейчас традиции сапожного мастерства не утеряны, но про них забывают. Раньше же все делали вручную и у нас, и заграницей.
А зачем в современной жизни необходимо делать обувь вручную?
Здорово стать сопричастным к одному из древнейших ремесел. Сегодня ручной труд востребован у тех людей, которые его понимают. Не составляет проблемы прийти в магазин и купить обувь, но там вы не можете повлиять на нее.
В мастерской вы не найдете готовую коллекцию обуви и не купите готовые ботинки, выбрав их из каталога
Здесь можно полностью влиять на все: от материала до ширины стежков, любой человек может стать дизайнером и конструктором. И тут важен не только конечный результат, но и сам процесс. Ручное производство обуви основано на индивидуальном отношении.
Какие у вас планы на будущее?
В ближайшее время буду я принимать участие в чемпионате мира по изготовлению обуви, который пройдет в Лондоне. За два с половиной месяца нужно изготовить ботинок определенной модели и отправить на оценку жюри. Там соберутся судьи-мастера обувного ремесла, которые несколько десятков лет делают обувь. И даже просто поучаствовать и представить на обзор ботинки, которые создаются в Екатеринбурге – уже большое достижение.
А вообще я хочу развивать это искусство и ремесло, привлекать и вовлекать в него как можно больше людей. История знает много имен мастеров сапожного дела, а тайны ремесла передавались из поколения в поколение. Все тонкости, нюансы, мельчайшие детали, которые отличают ручную обувь от изделий массового производства, по книгам не узнаешь. Это можно узнать, только наблюдая за работой мастера, постепенно проникая в его секреты. Я готов делиться теми знаниями, которые наработал в течение нескольких лет. Двери моей мастерской открыты для всех желающих: кто хочет просто посмотреть или узнать об истории сапожного дела, или научиться этому ремеслу. Особых знаний и навыков, для того чтобы начать, не требуется, главное – желание.
Фотографии предоставлены Иваном Беловым
Кожаная обувь своими руками — Как это сделано, как это работает, как это устроено — LiveJournal
Итак приступим), так как мы шьём руками, по всем правилам, то не плохо бы было сделать обувь удобной), поэтому перво — наперво снимаем мерку с ноги. Тут нам потребуется 3 (можно и 2) размера, пучки, взъём и подъём через пятку и форма следа.Далее правим колодку по снятым меркам с припусками под суточное изменение стопы и динамическую деформацию, в носочной части для пальцев оставляем свободное пространство и придаём желаемую форму носу.
Обклеиваем колодку малярным скотчем, важно обклеить без натяжения, если где то плохо ложится лучше надрезать, складки допускаются.
Наносим основные линии, это линия середины колодки (через гребень колодки, как бы делит колодку на 2 части) и линию кальцаты (линия между 2мя наивысшими точками боков колодок). Далее приступаем к творчеству, рисуем то что хотим видеть в итоге. Это методика хороша при индивидуальном пошиве, сразу видно что будем иметь в итоге, Миланская технология, типо).
Снимаем скотч с колодки, это будет наша развёртка с нанесённым дизайном. Делаем корректировку. На фото не полная корректировка, ещё в пятке нужна, поспешил с фото.
По развёртке строим выкройки, я делаю с картона или ватмана. Припуски под шов делаю 8-10 мм, под затяжную кромку 15-20 мм, по мурзилкам пишут что подл затяжную кромку можно меньше, но я перестраховываюсь, так сказать припуск на рукожопость) На фото выкройки для верха, для подклада не фотал, при построении выкроек для подклада важно учесть чтобы шав верха и подклада не накладывались друг на друга, иначе будет тереть ногу.
По выкройкам раскраиваем кожу и подклад, я использую кожу 1.2-1,5 мм растительного дубления, важно учитывать линии растяжения, иначе обувь быстро потеряет форму и превратиться в калошу. На фото опять раскроены только детали верха, без подклада.
В местах где детали сшиваются между собой срезаем край кожи (шерфовка, брусовка) чтобы шов не выделялся и не давил ногу, край должен выходить в 0, при сшивании получится 1 толщина кожи, а не 2, большой + к комфорту. Опять только верх, с подкладом всё тоже самое.
Делаем перфорацию, в вконтакте продают готовые пробойники для брогирования, но я делал простыми пробойниками диаметром 3 и 1 мм.
Сшиваем детали, важно делать всё симметрично, иначе при затяжке будет большой геморой. Так как машинки я не имею, то шью руками, + к надёжности и долговечности))). Отверстия под шов делаю самодельным пробойником выполненным из перьевого сверла, шаг 2 мм, зуб 0.6 мм, нитки вощёные, шов забивается воском и хорошо держит воду. На фото собранный верх с пришитой подкладкой, пятка из замши.
Готовим затяжную стельку, вырезаем с чепрака или воротка 2,5-3,5 кусок по контуру следа колодки с припуском около 1-1,5 см, хорошо смачиваем и провяливаем, размещаем по следу колодки и натягиваем хорошо фиксируя гвоздиками по контуру и в центре и обстукиваем. Ждём какое то время пока высохнет.
Немного увлажняем край и срезаем лишнее, добиваемся ровного и аккуратного контура, шкурим, можно и тяп ляп отрезать, но мне внутренний перфекционист не позволяет, внутри под вставной стелькой будет видно неровность.
Этап так этап, не даром совпало с пунктом 13 в повествовании, т.к у меня нет настоящего инструмента для вырезания губы, делаю эту операцию простым косячком, самая не любимая операция я бы сказал. Суть, вырезать в половину толщины на толстом чепраке возвышение куда будет пришиваться рант и верх.
Прокалываем отверстия по всему периметру изогнутым шилом, можно и в процессе шитья накалоть, но так удобнее. В разных методиках эту операцию делают по разному, кто то только до талии прошивает, кто то до каблука, я предпочитаю по всему периметру прошить. Итого около 90 *2 дырочек)))
Сушим
Приступаем к предварительной затяжке, как говорят к посадке. Выполняю это на «мокрую», цель растянуть кожу и придать форму колодки, возможно придётся повозиться чтобы все элементы дизайна были на своих местах. Язык и по канту прихватываем гвоздиками чтобы была нужная высота и расположение. Верхний край берцев и кант должен быть на своём месте, иначе будет тереть ногу. Выжидаем время, 2-3 дня. На фото тут стелька до вырезания губы, посадку чуть раньше делал на втором чтобы одинаковое время выстаивались.
Готовим подноски и задники, чепрак растишка 2-2,5 мм, мочим, вялим, околочиваем немного и вырезаем по форме задника и подноска.
Вынимаем гвозди и смотрим что у нас вышло с верхом, всё устроило, смачиваем, затягиваем отдельно от верха подклад, тянем как следует чтобы вытянуть хорошо кожу, фиксируем гвоздиками.
Ставим подносок и пятку, прихватываем гвоздями и хорошенько растягиваем и фиксируем гвоздями, немного подсушиваем и остервенело околачиваем чтобы кожа уплотнилась по максимуму, окончательно сушим и ещё всё хорошенько обстукиваем. После шкурим всё, придаём носу желаемую форму и сглаживаем переходы, чтобы пальцем не ощущался стык подноска и задника с подкладом. Не обязательная операция, но я делаю, между подноском и задником приклеиваем кусочек не тянущейся ткани, шириной около 25 мм, так называемые «бочки», исключают деформацию обуви при длительной носке, использую латексный эко клей).
Через шаблон мажем подносок и задник латексным клеем и затягиваем верх на мокрую, отставляем. ждём когда всё высохнет.
Отгибаем гвоздики поднимаем затяжную кромку мажем клеем хорошо и опять загибаем гвозди, остукиваем до появления чёткой грани. Сушим. Вынимаем гвозди.
Околачиваем верх устраняя все неровности, этот процесс может длиться несколько часов. добиваемся идеала))
Красим, я использовал проф краску Kenda Farben, в данном случае цвет Mogano, т.е красное дерево.
Опять всё околочиваем, по появляющемуся блеску выявляем все неровности и ещё раз околачиваем, этим можно заниматься пару дней)))
Жируем, использую копытное масло. Даём впитаться хорошенько.
Мега матерный этап, пришиваем рант, суть в том чтобы кривым шилом пройти через губу, кромку подклада и верха и выйти в рант и продеть нитку и затянуть седельным швов с «узелком» Узелок не даст располстись шву даже если половина стяжков перетрётся лет через 20))) Да, нитка пропитывается спец составом или воском.
Срезаем лишнее от верха и подклада, ровняем всё.
Ставим супинатор (геленок) метал, можно дерево. Фиксируем его кожей.
Заполняем пустое пространство пробкой, некий амортизатор и со временем примет форму ноги, ещё плюсик к комфорту. Раньше считалось что такой наполнитель снимает усталость и помогает при головных болях, не берусь утверждать))))))))))))
Далее к сожалению не фотографировал, грязный процесс)
Готовим подошву и флики для каблука. Для этого берём кожу растишку толщной 4-5 мм, вымачиваем хорошо, сутки провяливаем и выколачиваем.
Приклеиваем подошву
Нарезаем канавку под нитку, можно спрятать нитку , но я не стал заморачиваться так как всё равно планировал ставить профилактику.
Прокалываем отверстия через рант и подошву и выходим в прорезанный канал, хорошо затягиваем, шьётся седельным швом с узлом.
В области пятки подрезаем выступ и приступаем к набору каблука.
Первый флик каблука равняем и срезаем немного под углом чтобы выдержать плоскоть каблука, для того чтобы каблук опирался всей поверхностью.
Приклеиваем последующие флики до нужной высоты.
Стеклуем и приклеиваем набойку каблука и профилактику.
Обтачиваем урез подошвы и каблука, стеклим.
Приколачиваем набойку каблука гвоздями
Обрабатываем срез подошвы, красим пропитываем восками до нужного вида.
Снимаем технологические затяжки с места шнуровки, прокрашиваем что не прокрасилось.
Финишируем кожу, использую сначала жидкие воски от Kenda Farben, затем ещё околачиваем, ещё раз мажем восками. Даём высохнуть сутки. Далее полируем карнаубским воском. На фото готовых брог они после недельной носки и новый глянец наносить было лень))
Забываем о них на 1-2 недели. можно дольше, кожа привыкает к колодке и принимает форму.
Делаем шнурки, из чепрачной части шкуры.
Снимаем с колодки, примеряем, радуемся) Возможно, какие то этапы забыл описать. На всё про всё ушло чуть более 1 месяца.
Небольшой рассчет себестоимости обуви ручной работы, расскажу на своём примере, во сколько обошлись мне броги, только стоимость материалов, стоимость инструмента не учитываю. Данный подсчёт не имеет ни чего общего с коммерческой ценой пошива обуви, где оплачивается аренда мастерской, работа мастера и т.д.
Итак, кожа растительного дубления, средняя цена около 40 р за дц, в шкуре в среднем 150-170 дц + доставка, на одну пару, верх + подклад ушло около около 50 дц = 2266р
Низ обуви, чепрак растительного дубления толщина 4мм, цена около 50р за дц + доставка, средний размер 70-100 дц, на пару уходит около 35 дц = 2150р
Клей латексный, литр 800р, на пару уходит около 150 мл = 120р
Супинаторы = 30 р
Нитки примерно р 100
Гвоздики, 50р)
Краска, литр 1200, на пару уходит около 150 мл, = 180р
Финишные средства, округлим за всё 200р
Профилактика 150р
Набойки на каблук 150р
Итого примерно получаем сумму равную 5396, не мало, можно купить 2 пары китайской обуви которая если повезёт, прослужит по 1 сезону
Не буду рекламировать обувь ручной работы, каждый сам выбирает что ему важно и предпочтительнее, я предпочитаю носить обувь которая сшита идеально по ноге и будет служить очень долго, можно сказать даже десятилетие)), из обслуживания требуется только пропитка маслом, воск и замена профилактики раз в пару лет)
Источник
Если у вас есть производство или сервис, о котором вы хотите рассказать нашим читателям, пишите Аслану ([email protected]) и мы сделаем самый лучший репортаж, который увидят не только читатели сообщества, но и сайта Как это сделано
Еще раз напомню, что посты теперь можно читать на канале в Телеграме
и как обычно в инстаграме. Жмите на ссылки, подписывайтесь и комментируйте, если вопросы по делу, я всегда отвечаю.
Жми на кнопку, чтобы подписаться на «Как это сделано»!
Обувь ручной работы: этапы производства
Туфли и ботинки, сделанные полностью вручную, встречаются сегодня очень редко и стоят дорого — примерно от 400 евро, если мы говорим о Венгрии, и примерно от 600 евро, если речь идёт о Западной Европе и более или менее известных мануфактурах. На производство такой обуви затрачивается много времени, но оно того стоит: у туфель полностью ручной работы, например, можно большее число раз заменять подошву; они немного по-другому выглядят, а зачастую ещё и более комфортны. В этой статье мы опишем ключевые этапы создания туфель ручной работы на ранту.
Оглавление:
Раскрой кожи
Естественно, кожа для обуви ручной работы кроится только вручную. Если речь идёт о пошиве обуви на заказ, то используются индивидуальные, специально созданные лекала для вырезания кусков кожи. Для готовой обуви используются стандартные лекала, обычно изготовленные из плексиглаза или другого современного материала.
Для раскраивания шкур обувщики используют нож-кликер, а сама эта процедура называется кликингом (clicking).
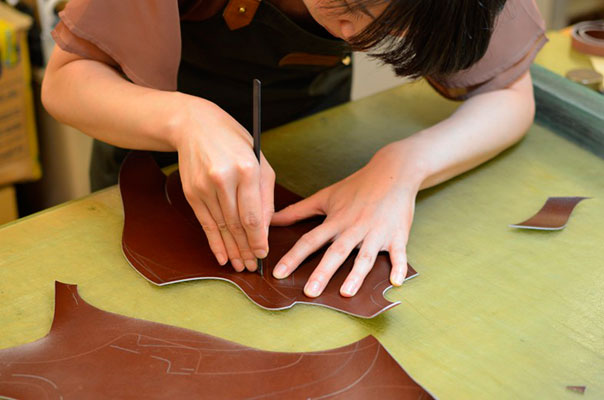
Перед выполняющим её работником стоит непростая задача: нужно использовать шкуру максимально рационально, отбраковав при этом все участки с дефектами. В случае с очень дорогой обувью, сшитой на заказ, используются лишь самые лучшие участки шкуры, причём многие шкуры отбраковываются ещё на этапе закупки.
Сшивание частей верха
На следующем этапе, который называется клоузингом (closing), вырезанные части кожи сшиваются друг с другом — и получается верх обуви.
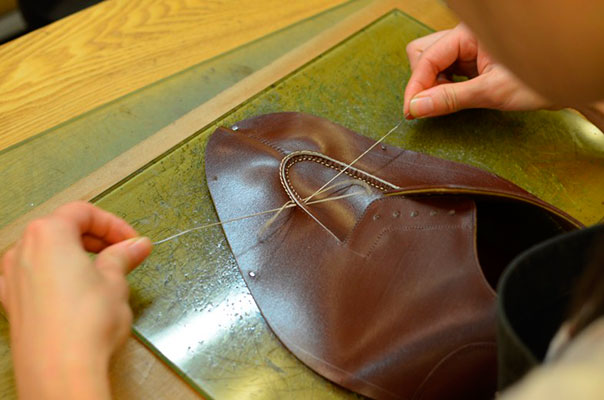
Помимо этого, верх сшивается с подкладкой, а также осуществляется декорирование отдельных частей верха — например, брогирование. На обуви полностью ручной работы брогирование делается вручную, без использования машин — и это занимает довольно много времени по сравнению с брогированием на фабричной обуви, где одна машина может делать дырочки одновременно на десяти кусках кожи.
Натягивание верха на колодку
Готовый верх обуви нужно натянуть на колодку, и эту операцию — ластинг (lasting) — делает ластер (laster). В случае с фабричной обувью ластинг обычно осуществляется полностью или частично с помощью специальных машин, что заметно сокращает издержки.
Как пишет немецкий эксперт по мужскому стилю Бернхард Ретцель, «ластер — это ремесленник, натягивающий кожу на деревянную колодку и временно прибивающий её гвоздиками. Позже, когда верх накрепко пришивается к ранту, гвозди снова вынимаются. Молоток часто намагничивается для облегчения манипуляций с множеством мелких гвоздей».
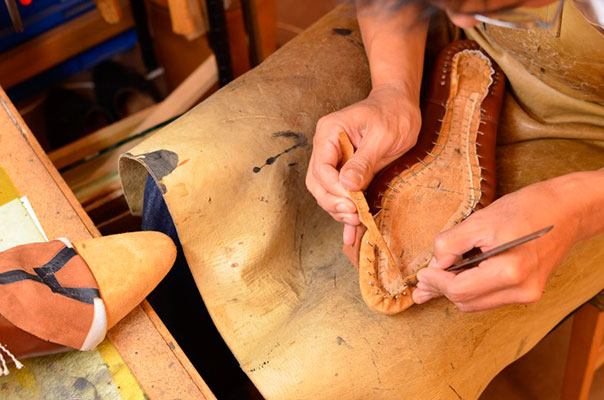
Стоит добавить, что раньше колодки изготавливались исключительно из дерева, но сегодня в ряде случаев даже для обуви на заказ (bespoke) используются колодки из пластика. У производителей готовой обуви имеются готовые колодки, а мастера, которые шьют заказную обувь, либо вытачивают колодки под клиента, либо используют готовые колодки разных размеров и форм, к которым по мере надобности прикрепляют в необходимые места куски кожи, чтобы добиться соответствия формы колодки форме стопы клиента.
Подготовка внутренней подмётки и пришивание ранта
Обувь полностью ручной работы часто шьётся с использованием ранта, причём этот рант пришивается вручную. Во внутренней подмётке (insole) вручную вырезается гребень, и после этого к нему и к верху вручную пришивается рант; сама подмётка тоже вырезается вручную. Это довольно трудоёмкая операция, и в случае с фабричной обувью сам процесс упрощают: гребень не вырезают в самой подмётке, а приклеивают к ней, используя заметно более тонкие подмётки (а сам гребень при этом сделан из текстиля). Рант к подмётке и верху на фабричной обуви пристрачивает машина, и делает это очень быстро.

Вырезание гребня на внутренней подметке

Сшивание ранта, гребня и верха обуви
В чем же заключается преимущество ручной работы на данном этапе? Знатоки говорят, что ручное крепление ранта (hand-welting) позволяет большее число раз заменять подошву; кроме того, hand-welted обувь при прочих равных оказывается более комфортной.
Пришивание подошвы и крепление каблука
После того, как рант соединен с внутренней подмёткой и верхом, на подмётку помещают пробковый наполнитель (cork filling) — это могут быть пробковые брикеты или же вязкая смесь на основе пробковой крошки.
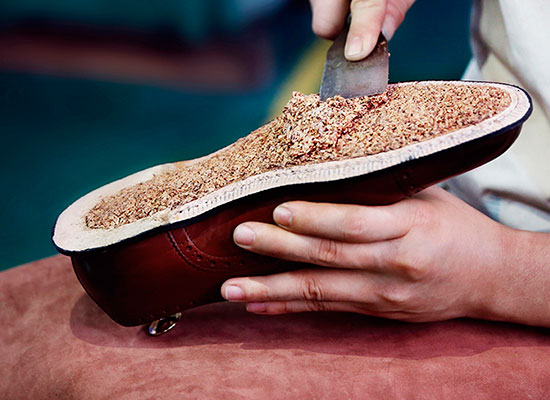
На следующем этапе — soling — рант сшивается с внешней подошвой (outsole).
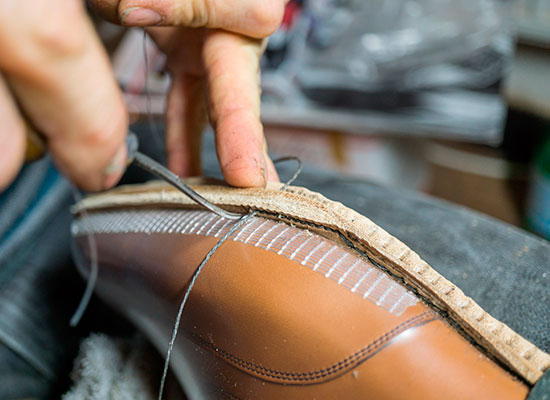
На обуви полностью ручной работы это делается вручную, иглой и нитью — такая операция трудоёмкая и длительная, и поэтому даже на hand-lasted и hand-welted обуви шов, соединяющий рант и внешнюю подошву, довольно часто выполняется с помощью машины. После крепления к верху «талия» (средняя часть) подошвы на туфлях ручной работы обычно изящно закругляется.
Далее осуществляется сборка каблука. На классических туфлях каблуки наборные — они сделаны из нескольких слоев кожи и резины, которые крепятся друг к другу и к подошве при помощи клея и маленьких гвоздиков. На сравнительно недорогих фабричных туфлях часто используются слои не из кожи, а из кожкартона — это обходится дешевле.
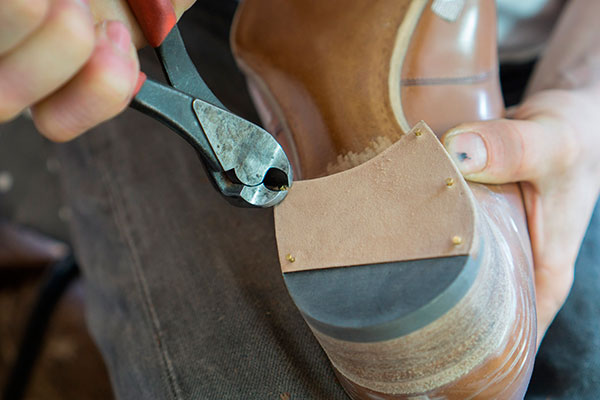
Финишинговые процедуры
После крепления подошвы и каблука туфли проходят ещё несколько процедур. В частности, ребро подошвы и каблука, и сами каблук и подошва шлифуются, вручную окрашиваются и полируются. Верх туфель вручную полируется, на него может наноситься уникальная патина с помощью красок и кремов.

Окрашивание каблука

Окрашивание верха обуви
Внешняя сторона подошвы и её верхний край иногда обрабатываются вручную зубчатыми колесиками. Затем в туфли вставляются стельки, обувь проверяют на отсутствие дефектов, после чего зашнуровывают и упаковывают.
string(0) «»
как делают обувь ручной работы » Я Устал
Думаю многим будет интересно как создаётся «bespoke» обувь. В этом посте покажу разные этапы создания пары и прокомментирую фото.
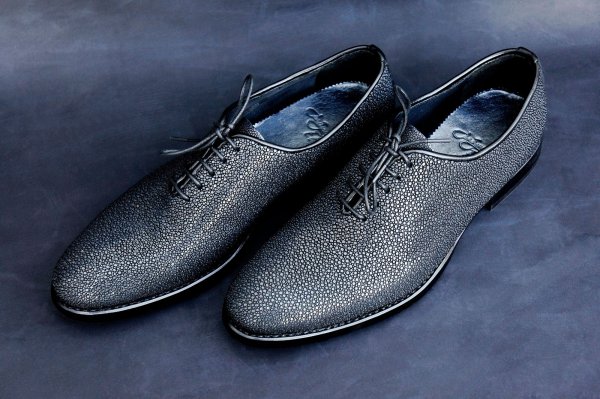
Сразу объясню что такое «bestpoke» и какая обувь ещё бывает.
Ready-to-wear (RTW), off-the-rack (OTR) — обувь, сшитая по готовым стандартизированным лекалам (колодкам) и продающаяся в магазинах.
Made-to-order (MTO) — обувь, созданная на стандартных колодках, но по индивидуальному заказу. Далеко не bespoke и даже не MTM, но в то же время — уже и не RTW.
Made-to-measure (MTM) — одежда и обувь, изготовленные по стандартизированным лекалам, слегка измененным по меркам заказчика, а также с учетом пожеланий заказчика относительно материала, фурнитуры и некоторых других деталей.
Bespoke — обувь ручной работы, изготовленная на заказ по индивидуальным выкройкам, на колодках изготовленных по размерам стопы клиента. Учитываются любые пожелания относительно материалов, фурнитуры и пр.
Начинается всё со снятия мерок, выбора фасона будущей пары обуви, рекомендаций модельера (бывает что в связи с анатомическими особенностями некоторые модели будут лучше смотреться или более удобны), подробно обсуждаем материал и особенности дизайна.
В этот раз выбор пал на кожу морского ската.
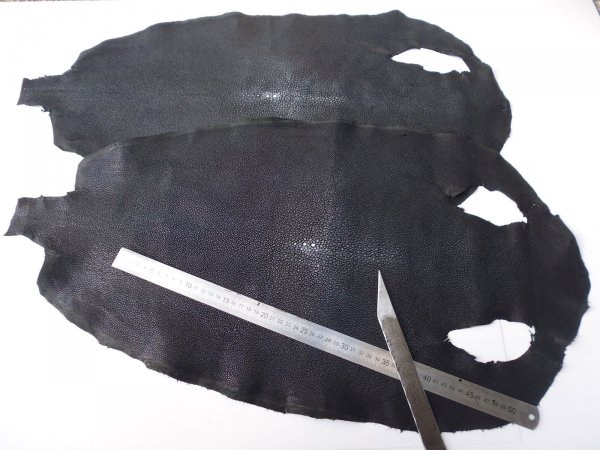
Если не удаётся выбрать из уже существующих моделей колодок, подключаем дизайнера, и получаем:
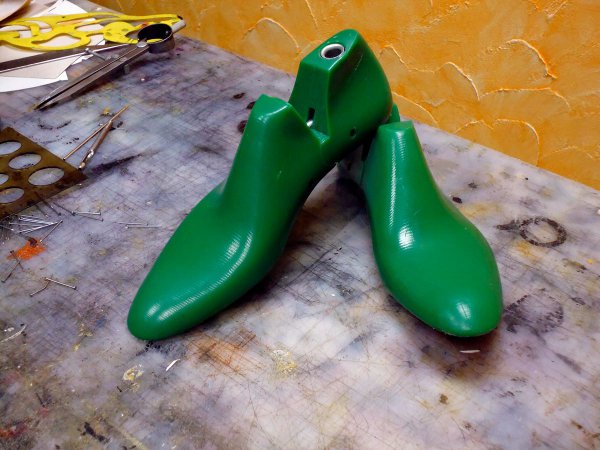
На колодке создаётся образ будущей пары, наносятся основные линии (на фото изготавливается другая пара, но суть ясна)
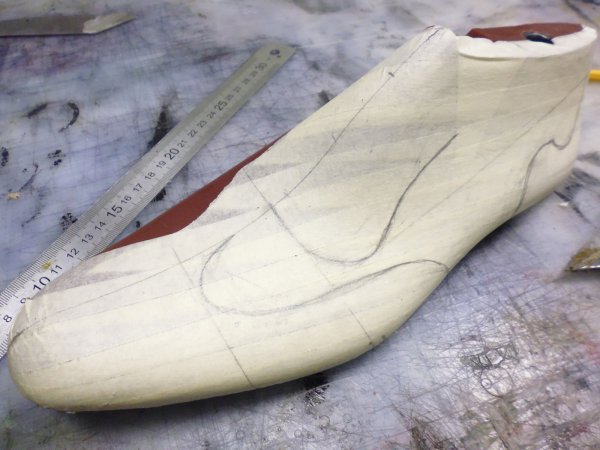
Переносим на плоскость, делаем более изящные изгибы, где необходимо припуски и прочие технологические тонкости и получаем первые выкройки.
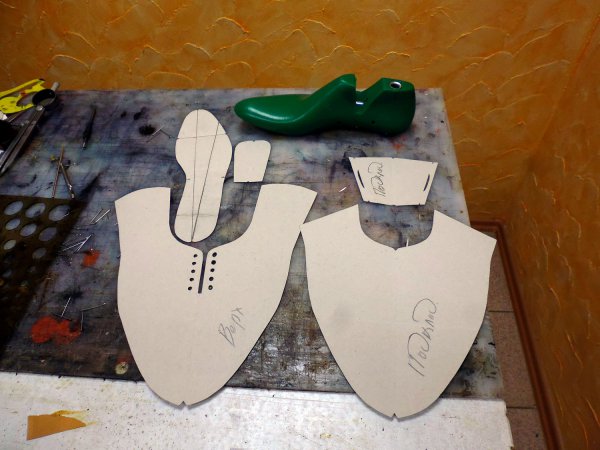
Изготавливаем примерочную модель и приглашаем клиента на примерку. Примерочная модель изготавливается из низкосортной кожи и недорогих материалов. Эта модель визуализирует все пожелания клиента в дизайне, служит для выявления недостатков, корректировки выкроек, а возможно и самой колодки. После одобрительной примерки начинается работа над полноценной парой.
По заранее изготовленным лекалам делается раскрой материала с учетом его структуры, тягучести и имеющихся пороков.
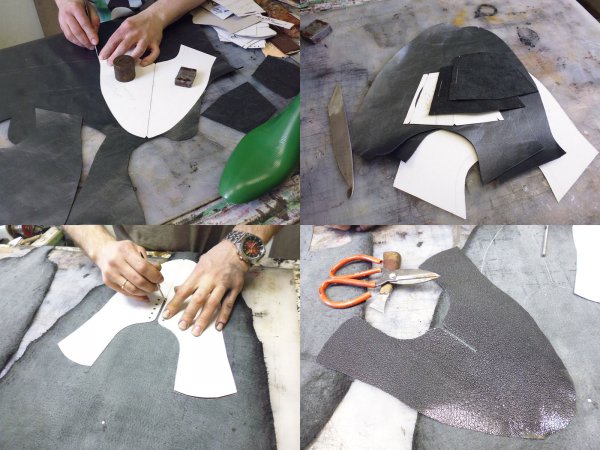
Производится брусовка краев для гладкого сочленения деталей внахлёст, после сшиваются между собой в определенной последовательности.
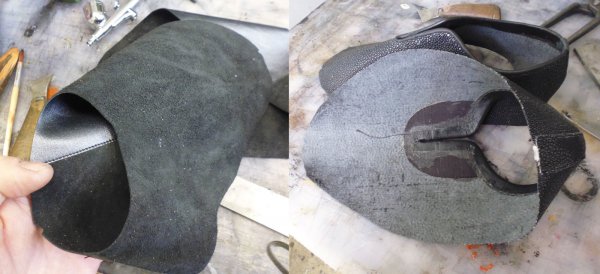
После сшивания деталей приступаем к изготовлению несущей стельки из чепрачной кожи растительного дубления.
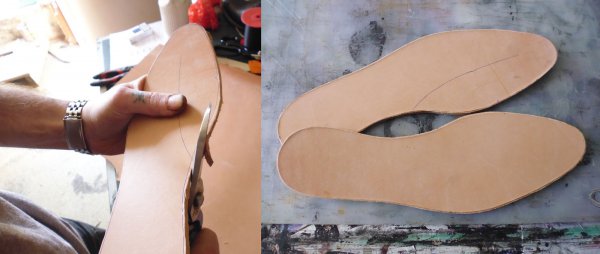
На ней прорезается бортик (губа), в губе делаются отверстия через которые будет пришит в ручную кожаный рант, такой тип крепления подошвы называется «Hand welted» или по русски — ручное рантовое крепление (аналогичная прошивка, но выполненная машиной «Goodyear welted»).
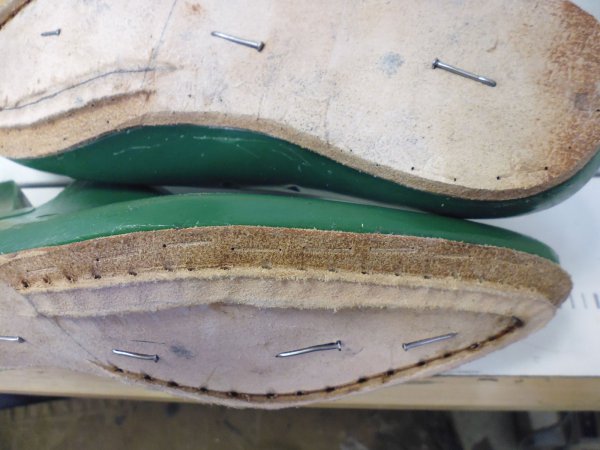
Теперь можно переходить к затяжке пары на колодку.
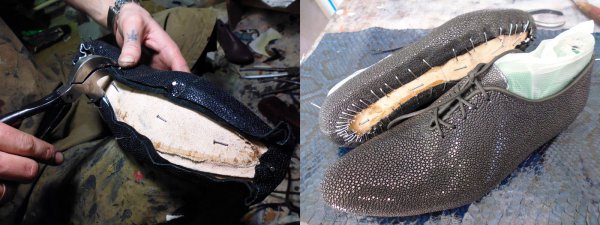
Следующий этап вшивания кожаного ранта (заранее подготовленного из чепрачной кожи).
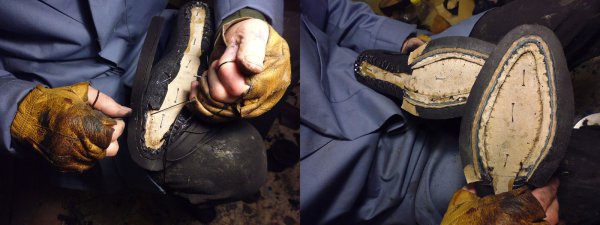
Пришло время подошвы с заранее выдавленным логотипом. После приклейки выполняется сшивание кожаного ранта с подошвой. Тем временем набираются каблуки из кожаных «фликов» и устанавливаются на пару. Обтачиваем рашпилем, вышкуриваем наждачной бумагой разной зернистости, окрашиваем. В данной паре также устанавливаем набойку и профилактику.
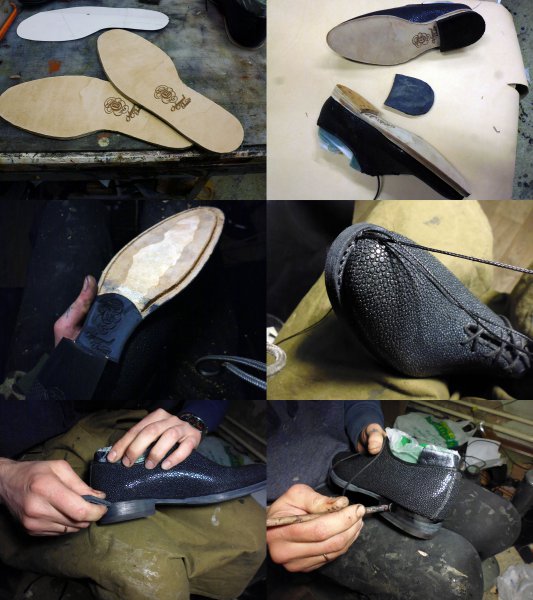
И настала работа по выглаживанию и полировке уреза подошвы, каблука и верха. После полировки можно достать колодку и изготовить вкладную стельку, вдеть шнурки и пара готова!
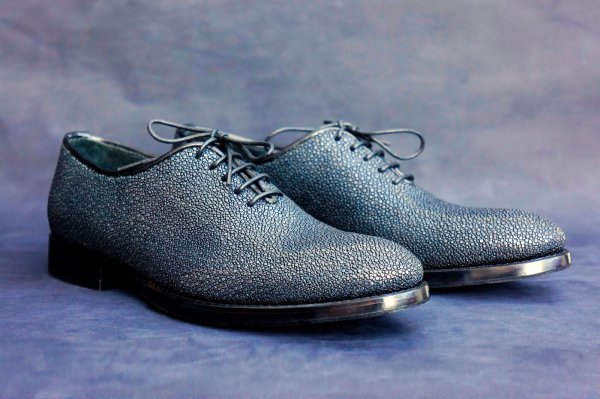
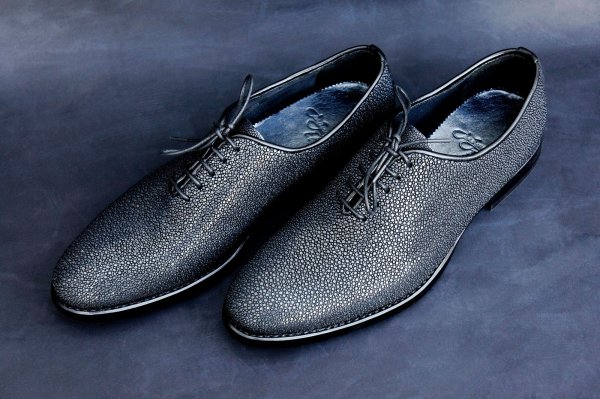
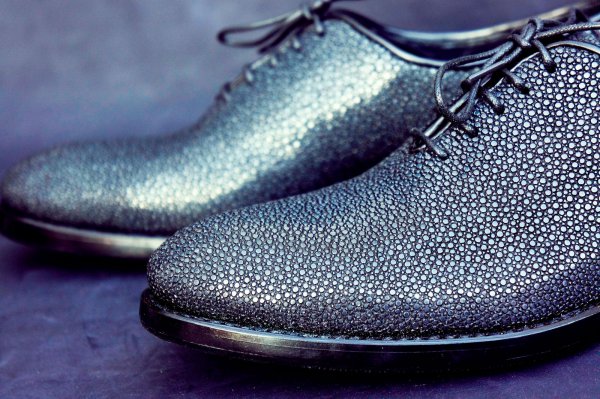