компоненты, способы и этапы работы
Начиная строительство, будущий владелец дома старается всеми возможными способами сократить расходы на стройматериалы. Низкая стоимость обычно исключает высокое качество используемых материалов, поэтому возникает проблема – качественно или дешево. Пеноблоки стали такими популярными в строительном деле благодаря своей легкости в использовании и своим характеристикам, которые делают этот материал наиболее подходящим для строительства. Высокая стоимость готовых пеноблоков привела к распространению практики самостоятельного изготовления стройматериала. Изготовление пеноблоков в домашних условиях позволяет не только существенно сократить расходы, но и получить не менее качественный материал для сооружения теплого помещения.
Как самому изготовить пенобетон?
Используя необходимое оборудование вполне можно организовать производство в домашних условиях. Производство пеноблоков требует точного выполнения технологии, соблюдения пропорций смешивания компонентов. Если вы решили сэкономить на готовых пеноблоках, изготовив их самостоятельно, следует знать, что технология изготовления домашнего пенобетона имеет некоторые особенности:
- Используйте чистый цемент, марка – от 400 и выше.
- Пену добавляют в последнюю очередь, когда остальные компоненты смешаны до однородной консистенции.
- Качество готовой пены можно проверить нехитрым способом – наберите ее в ведро и переверните емкость – пена не должна вытекать.
- Полузастывший бетон извлекают из форм и разрезают на отдельные блоки. В формах бетонная смесь должна находиться не менее суток, а после разрезания блоки оставляют досыхать на поддоне на 15 часов при температуре от 5 градусов.
Что нужно иметь для изготовления качественного пенобетона?
Чтобы сделать пенобетон своими руками, понадобится немало времени, денежных вложений. Для организации собственного производства вам потребуются специальные материалы и оборудование:
- бетоносмеситель;
- чистый сухой песок;
- качественный цемент;
- чистая вода;
- пенообразователь;
- пеногенератор;
- формы.
Рецептура имеет множество вариаций, качество прямопропорционально зависит от исходных компонентов.
Вернуться к оглавлениюСамостоятельный способ изготовления
Схема производства пенобетона.Изготовление пеноблоков начинается из расчета объема емкости, в которую потом будет выливаться готовый раствор. Исходя из полученных параметров, рассчитывают количество требуемых компонентов – на каждые 0,5 кубометра требуется 100 л воды и по 200 кг цемента и просеянного песка.
Сначала в бетономешалке смешивают песок, цемент, с помощью специального генератора и химического пенообразователя изготавливают устойчивую пену с расчетом по 500 л пены на 1 кубометр. К цементу и песку добавляют чистую воду, а затем смешивают с готовой пеной. Большинство пеногенераторов снабжены специальным насосом, что позволяет закачивать пену непосредственно в барабан бетономешалки.
Когда все компоненты будут помещены в бетоносмеситель, их необходимо тщательно смешать. Плотность материала регулируется добавлением в него дополнительного количества пены. Готовый раствор выливают в подготовленную форму, дают высохнуть. Сухие блоки извлекают из форм, оставляют на сутки для полного высыхания. Процесс производства необходимо проводит при температуре не ниже 5 градусов.
Пенообразователь можно купить в специализированных магазинах, или сделать в домашних условиях. Для этого вам понадобится 150 г едкого натра, 1 кг канифоли, 60 г столярного клея. Компоненты соединяют, немного нагревают и помешивают до состояния однородной массы. Перед процессом изготовления пены готовый раствор смешивают с водой.
Формы для будущих блоков можно сделать из фанерных или металлических листов. Изготовление требует внимательности и строгого соблюдения пропорций – они должны быть геометрически правильными. Во избежание вытекания готового растворы, их обтягивают полиэтиленом. После извлечения блоков можно сразу же наливать следующую порцию раствора.
Вернуться к оглавлениюСебестоимость самостоятельного изготовления
Лучше выбирать цемент М-400 или М-500.
Стоимость изготовленных дома пеноблоков намного ниже, чем цена готового продукта. Для приготовления 1 кубометра материала D600 вам понадобится:
- 200-250 кг песка и цемента;
- 1,5 л пенообразователя;
- вода.
К стоимости компонентов добавьте расходы на электричество, которое потребляет оборудование.
Основные расходы идут на цемент, остальные компоненты составляют четверть стоимости цемента. На масштабы финансовых вложений влияют также затраты на специальное оборудование, по желанию его можно соорудить самостоятельно. Сборка, установка – всю информацию вы сможете найти в свободном доступе. С другой стороны, если у вас мало опыта в производстве пенобетона – придется экспериментировать для получения материала, соответствующего требованиям и характеристикам. Возможно, свои качественные пеноблоки получатся не с первой попытки, придется снова тратить деньги на новую порцию компонентов.
Вернуться к оглавлениюЭтапы работы
Процесс состоит из трех главных этапов – приготовление раствора, разливка по формам, разрезание. Для изготовления качественных пеноблоков необходимо разобраться в особенностях технологии каждого из них.
Раствор пенообразователя
Прежде всего, подготавливается цементная смесь как для обыкновенного бетона. Преимущественно выбирают цемент марки М400 или М500. Проследите, чтобы песок был сухим, без посторонних примесей, ракушек или камешков. Что касается воды – подойдет обычная водопроводная.
В готовую бетонную смесь добавляют готовую пену. Как говорилось ранее, пенообразователь можно купить в магазине, или сделать самостоятельно по рецепту, описанному выше. Пену и бетонную смесь хорошо вымешивают, готовый раствор можно разливать по формам.
Вернуться к оглавлениюРазливание раствора по формам
Разливание раствора по формам.Перед тем, как поместить раствор в подготовленные формы их необходимо смазать специальным средством, не содержащим масла. Есть две методики изготовления пеноблоков – литьевая, резательная. Первый способ предполагает заливание бетонного раствора в отдельные формы. После застывания достаточно извлечь готовый блок и оставить на поддоне еще не несколько часов. Недостатки данной технологии:
- возможная деформация металла;
- повреждение блоков в процессе извлечения.
Установка неровных блоков трудоемкая, такая конструкция будет значительно уступать по качеству. Достоинством такого способа является то, что в отличие от метода резки можно сэкономить не покупая оборудование для разрезания.
Вернуться к оглавлениюТехнология резки
Процесс подразумевает разрезание цельной бетонной плиты на отдельные блоки. Преимущества данного метода:
- блоки геометрически правильные;
- ровные края;
- отсутствие сколов и неровностей.
Среди недостатков стоит указать:
- дорогостоящее оборудование;
- выбор момента для реки – при полном высыхании может смещаться струна для резки, недостаточно застывший бетон разрушается в процессе разрезания.
Рекомендации специалистов
Формы изготовляют из ламинированной фанеры или металлических листов.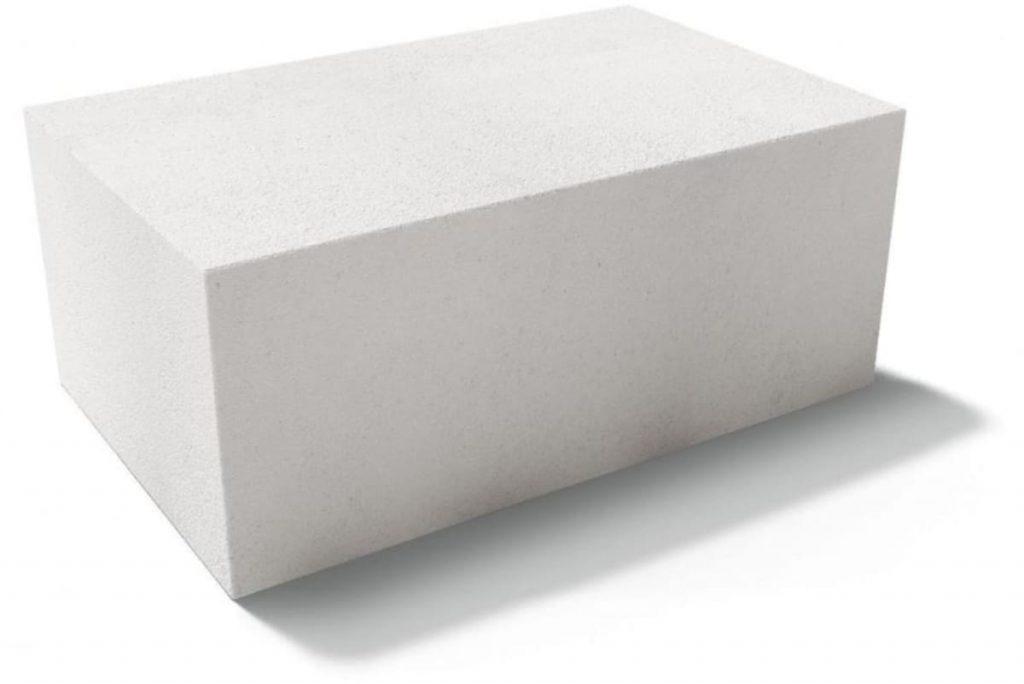
Советы профессионалов помогут избежать непредвиденных проблем в процессе производства пеноблоков в домашних условиях. Для изготовления качественного стройматериала придерживайте следующих рекомендаций:
- Формы изготовляют из фанеры или металлических листов.
- Перед заливкой раствора обработайте внутреннюю поверхность форм специальным раствором, сами формы обтяните полиэтиленом.
- Сушку проводят при оптимальной температуре в 50-60 градусов на протяжении 2 суток.
- Материал извлекают после его полного высыхания.
- Готовые блоки оставляют на поддонах еще на несколько часов, только после этого возможна их установка.
Домашняя фабрикация блоков
При наличии необходимых умений и правильном подходе к процессу изготовления, пеноблоки изготовляются быстро. Большинство профессиональных строителей предпочитают изготавливать пеноблоки, экономя денежные средства, получая моральное удовлетворение от процесса.
Вернуться к оглавлениюВывод
Домашнее производство своего пенобетона помогает значительно сократить расходы на стройматериалы. Технология изготовления проста, главным условием является четкое соответствие инструкциям. Стоимость таких блоков зависит от выбора компонентов, их цены.
производство пенобетона, оборудование, технология пенобетона
Относительно молодой строительный материал — пенобетон становится все более и более популярным в последние годы, благодаря простоте и дешевизне изготовления и возможности эффективного и удобного применения при проведении строительных работ. Основное преимущество пенобетона, отличающее его от других стеновых материалов, — это уникальный компромисс прочности, долговечности и теплоизоляционных свойств. Что немаловажно, все эти параметры одновременно имеют достаточно усредненные характеристики, соответствующие самым современным требованиям по теплоизоляции, прочности, экологичности, пожаростойкости и т.д.
Основные способы производства пенобетона
Для получения данного материала достаточно вспенить обычный раствор из цемента и песка, либо добавить в пескоцементную смесь готовую пену, изготовленную в специальном генераторе.
- Первым вариантом получения готовой смеси пенобетона является вспенивание цементного раствора непосредственно в баросмесителе.
- Вторым способом является производство пенобетона в отдельном смесителе с последующим добавлением пены, приготовленной в пеногенераторе.
Для быстрого и эффективного пенообразования производители используют специальные химические добавки — пенообразователи. Меняя дозировку пены (в соотношении с цементным раствором) можно получать различную плотность пенобетона на выходе.
Значение плотности напрямую связано с прочностью и теплоизоляционными свойствами пенобетонного изделия.
- теплоизоляционные плотностью D400-D500 (теплоизоляция несущих стен из кирпича и т.п)
- конструкционно-теплоизоляционные плотностью D600-D1000 (применение в качестве несущих стен, обладающих высокими показателями теплоизоляции)
- конструкционные D1100-D1200 (возведение несущих стен с средними показателями по теплоизоляции, лучшими чем у железобетона, но худшими чем у большинства ячеистых бетонов. Примерно такое же значение плотности имеют блоки из керамзитобетона )
Благодаря мобильным установкам пенобетон можно изготовить непосредственно на стройке, что безусловно очень удобно. Применять полученный материал можно для заливки утепляющих и конструкционных монолитных конструкций непосредственно на стройплощадке, производстве, заводе и т. д.
Стоит заметить, что в большинстве случаев изготовление пенобетонной смеси — все же стационарный процесс, преимущественно проходящий в цехах по производству пеноблоков и т.п. стеновых и теплоизоляционных панелей и плит.
Применение пенобетона
Так чем же привлекателен пенобетон, производство которого в последние годы стало активно развиваться. Наверное, потому что процесс изготовления пенобетонной смеси не требует больших вложений в оборудование; технология производства несложна; и как следствие вышесказанного — это экономически выгодно и доступно даже небольшим фирмам и частным предпринимателям.
Для получения готовой смеси нет необходимости в гравии, извести, щебне или керамзите. Основными компонентами пенобетона являются песок, портландцемент и пенообразователи. Немаловажно, что все эти материалы обладают высокими показателями по экологичности, прочности и долговечности одновременно. Доступность и низкая цена сырья для производства пенобетона — тоже идет в плюс.
Хорошая подвижность смеси позволяет заполнять ей любые форм-оснастки и блок-формы. Также есть возможность производить заливку в узкую вертикальную опалубку за счет того, что материал не требует уплотнения вибрированием при укладке.
Производственный процесс не требует особых затрат и достаточно иметь лишь баросмеситель и специальные металлические формы для отливки готовых пеноблоков стандартных размеров. Иногда применяются формы изготовленные из ламинированной фанеры.
На больших предприятиях для облегчения процесса можно производить замешивание и заливку блоков автоматизировано (с применением АСУ), что в значительной степени снижает трудозатраты, повышает качество продукции и делает процесс производства пенобетонной смеси более технологичным и нормируемым.
Преимущества пенобетона и изделий из него
Применение пенобетонных блоков и пенобетона позволяет производить строительные работы, с соблюдением самых современных нормативов по теплостойкости ограждающих конструкций построек и прочности здания в частности.
И в данной стихии пенобетон пока не имеет достойной конкуренции (за исключением газобетона — материала, близкого ему по своим основным характеристикам).
Жилье, построенное из пеноблоков, комфортабельно в проживании и обладает такими преимуществами, как:
- сохранение прохлады в помещении летом
- хорошая звукоизоляция
- высокая экологичность (сравнима с деревом)
- хорошая прочность и долговечность (близкая с кирпичу)
- идеальная поверхность стен, не требующая больших затрат и усилий при отделке
- высокая огнестойкость
- отсутствие так называемых «мостиков холода» (благодаря тонким швам клея между блоками)
- невысокая стоимость производства пеноблоков
Применение пенобетона в строительстве в значительной степени снижает затраты на возведение здания, а при производстве смеси непосредственно на стройплощадке позволяет существенно снизить и транспортные расходы. В результате заказчики получают относительно недорогую, качественную и долговечную постройку, отвечающую всем современным европейским требованиям.
Самостоятельное изготовление пенобетона
Оглавление:- Как изготовить пенобетон своими руками: нюансы
- Для чего нужен бетоносмеситель?
- Производство пенобетона: особенности
- Дополнительные моменты
Когда появляется желание начать строительство собственного дома, будущий хозяин начинает думать об экономии. Он стремится найти более дешевые строительные материалы, без потери качества. Сегодня в современном строительстве применяются новейшие разработки и современные технологии. Одной из новых разработок стало изготовление пенобетона. Этот материал был специально создан для производства пеноблоков, которые нашли широкое применение в строительстве домов малой этажности.
Схема производства пенобетона.
У пеноблоков много положительных качеств:
- отличные эксплуатационные данные,
- отвечает требованиям экологии,
- прекрасный звукоизолирующий материал,
- пропускает воздух, поэтому в таких домах никогда не бывает высокой влажности,
- хорошая прочность,
- длительное время эксплуатации.
Стоимость такого строительного материала вполне демократична. Однако часто для экономии застройщики изготавливают пеноблоки самостоятельно.
Хочется сразу сказать, что одного желания изготовить пенобетон мало. Придется одновременно стать химиком, технологом и инженером по изготовлению пеноблоков.
Как изготовить пенобетон своими руками: нюансы
Чтобы изготовить монолитный пенобетон, не обращаясь за помощью к профессионалам, необходимо ознакомиться с технологией.
Таблица технических характеристик пенобетона.
Для такого материала должен использоваться только цемент М 400. Нельзя добавлять никаких примесей. В случае применения теплоизоляционного бетона, не разрешается добавлять песок. Когда плотность бетона превысит 600 кг/м³, начинают добавлять природный песок.
В цементную смесь с песком добавляется пенообразователь. Самым подходящим считается синтетический «Ареком-4». Чтобы изготовить такой пенопреобразователь самостоятельно, необходимо иметь:
- едкий натр,
- канифоль,
- столярный клей.
Смесь измельчают, слегка нагревают, потом мешают до получения однородной массы. Данный пенообразователь требует наличия пеногенератора. После добавления воды в концентрат получается рабочий раствор.
Необходимо с особым вниманием отнестись к оборудованию, необходимому для получения пенобетона. Из всех видов агрегатов чаще всего используется:
- пеногенератор,
- бетоносмеситель,
- компрессор,
- манометр,
- формы.
У первых 4-х аппаратов абсолютно одинаковые характеристики. Они отличаются только мощностью и другими свойствами, которые не оказывают серьезного влияния на производство пенобетона. Надо заметить, что полученный материал может использоваться как в строительстве жилого дома, так и гаража.
Для получения пены необходимо использовать пеногенератор. Конструкция полуавтоматического пеногенератора включает следующие элементы:
Схема устройства пеногенератора.
- Модуль, чтобы производить доставку смеси для последующего пенообразования.
- Непосредственный модуль пенообразования.
- Модуль, проводящий автоматическую дозацию.
Глядя на эти 3 составляющие, можно легко понять, по какому принципу выполняет работу этот агрегат. На 1-ом этапе бетон отправляется в пеногенератор. Причем раствор должен полностью отвечать всем технологическим требованиям.
Затем бетон принимает 2-ой модуль, в котором происходит его смешивание с воздухом. В результате получается готовый пенобетон. В большинстве случаев подобные пеногенераторы имеют высокую производительность. Они способны за 60 с изготовить более 500 л материала.
Вернуться к оглавлениюДля чего нужен бетоносмеситель?
Этот аппарат смешивает ингредиенты, чтобы на выходе получился бетон, который можно использовать в строительстве. Когда строится гараж или какая-нибудь другая конструкция, чтобы получить пенобетон, обязательно применяется пеногенератор. Для самостоятельной работы можно обойтись и без бетоносмесителя. Эту машину может заменить большая емкость и обыкновенная лопата, но мешать раствор придется самому.
Для изготовления пенобетона понадобится форма.
Это, пожалуй, простейшая деталь во всей технологии. Ее можно изготовить из любого подручного материала. От материала требуется только гладкая поверхность и отсутствие деформации от массы бетона. Для форм самым лучшим материалом будут металлические пластины.
Наиболее важным размером является ширина, так как толщина стены находится от нее в прямой зависимости. Для стен гаража хватит и 20 см, а вот для строительства дома ширина формы должна быть более 30 см.
Надо сказать, что все описанные выше приборы можно сделать в домашних условиях самостоятельно, нужно только внимательно разобрать каждый чертеж. Более простым вариантом будет покупка таких агрегатов.
Производство пенобетона: особенности
Классификация пенобетона.
Сначала смешиваются все ингредиенты:
- песок,
- вода,
- цемент.
После получения однородной массы выполняется добавление пены. Плотность полученного пенобетона должна превышать 80 г/м³. Если этот показатель будет меньше, количество пор в пеноблоке сильно увеличится, из-за чего он будет быстро разрушаться. Определить, насколько хорошо получился пенобетон, можно простым способом. В обычное ведро наливается пена, а затем оно переворачивается кверху дном. Если плотность имеет высокий показатель, то пена вытекать не должна.
Необходимо помнить, что время, затраченное на перемешивание раствора, влияет на механические свойства пенобетона. Чем его меньше, тем качественнее он получается.
Чтоб изготовить пеноблоки, необходимо пенобетон залить в форму. Выждав некоторое время, не полностью застывший материал режется на блоки, которые необходимо продержать в форме больше 24 часов. Готовый пеноблок, извлеченный из формы, необходимо продержать на поддоне дополнительно 15 часов, причем температура окружающей среды должна быть выше 5°С.
Чтобы увеличить скорость затвердевания материала, строители применяют самые разные типы ускорители. Самым простым и доступным считается хлористый кальций. Его добавляют в смесь в количестве 2% от общего объема цемента.
Одной из главных характеристик пеноблока считается усадка при кладке. На величину усадки влияет несколько факторов:
- марка цемента,
- качество и размеры песка,
- способ выдерживания,
- содержание цемента в растворе,
- плотность пеноблока.
Дополнительные моменты
Основные эксплуатационные свойства пеноблока приблизительно соответствуют параметрам натуральной древесины. Однако такие блоки можно эксплуатировать намного дольше. Они отличные теплоизоляторы. С наступлением холодов пеноблочные стены отлично сохраняют тепло, в летнюю жару в таком доме всегда прохладно.
Самыми важными преимуществами является скорость и возможность его изготовления прямо на стройплощадке. В результате экономятся значительные бюджетные средства.
Для того чтобы изготовить пустотелые пеноблоки, разрешается пользоваться любыми цилиндрическими предметами. Есть только одно условие: каждый предмет должен иметь совершенной гладкую поверхность. Иначе разные части пеноблока начнут испытывать разное давление, это приведет к снижению прочности и уменьшению срока эксплуатации.
Недавно был изобретен поризатор. Этот новейший механизм совместил в себе 2 функции. Он работает как пеногенератор и одновременно смешивает пену и раствор. Перемешивание происходит с очень высокой скоростью. За 1 с аппарат выполняет 140 перемешиваний. В результате получается мелкопористый пенобетон, не дающий никакой усадки.
Загрузить ещёПенобетон своими руками в домашних условиях
Среди материалов, предлагаемых на рынке строительного сырья, особой популярностью пользуются пеноблоки, для изготовления которых применяются специальные установки для производства пенобетона. В достоинствах использования пеноблоков убедились многие застройщики. Ведь универсальный стройматериал обладает комплексом преимуществ. Владея технологией изготовления строительных смесей, несложно осуществить изготовление пенобетона в домашних условиях с помощью обычной бетономешалки и вспомогательного оборудования. Остановимся детально на нюансах технологии.
Изготовление пенобетона в домашних условиях – общая информация
Планируя производство пеноблоков в домашних условиях, следует изучить, какие технологические приемы используются для изготовления, разобраться, как правильно готовится цементно-песчаный раствор, а также подготовить необходимые для производства пенобетонной смеси материалы, инструмент и оборудование. Желая использовать самостоятельно изготовленные пеноблоки для строительства дома, необходимо знать свойства и характеристики пенобетонного материала. Остановимся более детально на этих моментах.
Пенобетонные блоки используются при возведении домов малой этажностиПланируем изготовить пеноблоки своими руками – выбираем способ изготовления
Используются различные технологии приготовления пенобетонной смеси на основе песка и цемента:
- Классическая. Для изготовления пеноблоков своими силами необходимо самостоятельно сделать пеногенератор или использовать покупной агрегат.
Пеногенераторная установка направляет по магистралям состав в предварительно подготовленный раствор, включающий цемент, песок и воду. Рабочая смесь, смешанная с помощью бетоносмесителя с пенообразующим компонентом, подается для заливки в специальные формы. Их внутренние размеры соответствуют габаритам готовой продукции. Раствор твердеет в ходе гидратации портландцемента с образованием внутри пенобетонного массива воздушных ячеек. Процесс набора твердости осуществляется в условиях естественной температуры окружающего воздуха.
- Поризационная. Процесс производства пенобетона по поризационной технологии осуществляется с использованием специального устройства, называемого поризатором. Агрегат осуществляет введение сухих ингредиентов в пенообразователь, подаваемый под напором. Песчано-цементные частицы оседают на поверхности пенистых пузырей с образованием рабочего пеноматериала. Подготовленная смесь под напором подается по трубам на рабочий участок. Среди профессиональных строителей указанный технологический прием известен как сухой способ минерализации.
Поризационная технология получила распространение в промышленном строительстве для непрерывной подачи пенобетонного раствора.
Для самостоятельного изготовления пенобетонных блоков наиболее распространена классическая технология с использованием пеногенератора.
Мастер может сам получить высококачественную пену, затратив на изготовление устройства минимум денегИз чего делают блоки – готовим необходимые материалы
Процесс производства пеноблоков осуществляется в соответствии с рецептурой. Она регламентирует необходимую концентрацию компонентов смеси в зависимости от требуемого удельного веса пенобетона.
Независимо от марки изготавливаемого пенобетона, в состав смеси входят следующие ингредиенты:
- вяжущее вещество, в качестве которого используется портландцемент марки М400 или М500. С возрастанием марки применяемого цемента улучшаются эксплуатационные свойства вспененного композита;
- заполнитель в виде гранулированного керамзита или мелкофракционного песка. Применение вместо песка керамзитных гранул повышает теплоизоляционные характеристики пенобетона;
- покупной или самостоятельно приготовленный пенообразователь. Важно хранить пенообразователь не более 20 дней с момента приготовления при температуре до 25 градусов Цельсия;
- вода, подогретая до температуры 20-24 градусов Цельсия. Количество добавляемой воды определяется путем выполнения расчетов, соблюдая соотношение цемента и воды 5:2.
Для изготовления десяти кубических метров пенобетонной смеси потребуется:
- портландцемент в количестве 3,2 т;
- просеянный песок 2 т;
- пенообразователь в объеме 10-15 л;
- вода – 1,3 т.
Применение качественных компонентов, а также соблюдение рецептуры и технологии гарантирует рабочие характеристики пенобетона.
Перед тем, как как сделать пеноблоки в домашних условиях, следует ознакомиться с пропорциями для его изготовленияИнструмент, приспособления и оборудование для производства пеноблоков
В состав линии для изготовления пенобетона своими силами входит следующее оборудование:
- бытовая бетономешалка;
- пеногенерирующий агрегат;
- компрессорная установка;
- механический сепаратор;
- устройство для дозировки воды;
- соединительные трубы.
Также потребуются формовочные ящики для заполнения пенобетонным раствором. Не забудьте подготовить лопаты и ведра для подачи сырья в бетоносмеситель. При увеличенных объемах производства потребуется погрузчик или шнековый транспортер, ускоряющий подачу исходного сырья. Сегодня предлагаются мобильные установки для производства пенобетона в домашних условиях, которые можно недорого арендовать. Комплектность и мощность применяемого оборудования зависит от предполагаемых объемов производства.
Какими свойствами обладает качественный пенобетон
Пенобетон – популярный стройматериал, обладающий следующими достоинствами:
- повышенными теплоизоляционными свойствами, обусловленными ячеистой структурой. Для отопления пеноблочных зданий требуется меньший объем затрат, так как в них лучше сохраняется тепло;
- устойчивостью к воздействию отрицательных температур с последующим оттаиванием. Целостность пеноблоков сохраняется на протяжении 40-50 циклов глубокого замораживания;
- стойкостью к влиянию повышенной температуры, вызванной контактированием с открытым огнем. При пожароопасных ситуациях сохраняется целостность пенобетонных строений;
- высокими шумоизоляционными характеристиками, благодаря которым обеспечиваются комфортные условия в помещении. Материал с пористой структурой эффективно поглощает внешние шумы;
- воздухопроницаемостью, способствующей поддержанию комфортной влажности и осуществлению воздухообмена. В пенобетонном помещении не развиваются микроорганизмы, не образуются колонии грибков.
К не менее важным преимуществам пенобетона также относятся:
- экологическая чистота;
- небольшой объем затрат на самостоятельное изготовление;
- легкость механической обработки;
- увеличенные габариты пеноблоков;
- небольшой вес изделий.
Наряду с достоинствами даже качественный пенобетон обладает некоторыми недостатками:
- повышенной гигроскопичностью. Пенобетонные стены нуждаются в надежной защите;
- увеличенной хрупкостью. При транспортировании и кладке следует оберегать блоки от механических повреждений.
Несмотря на недостатки, застройщики отдают предпочтение пенобетону благодаря серьезным преимуществам материала.
Технология производства пеноблоков в домашних условиях
Технология производства пеноблоков в домашних условиях предусматривает выполнение следующих работ:
Чем дольше замешивается композиция, тем больше разрушается пена, что недопустимо, так как чревато существенным снижением прочностных и иных характеристики готового пенобетона- Подготовка исходных компонентов в количествах, соответствующих рецептуре.
- Приготовление необходимого объема пенообразователя из пеноконцентрата.
- Смешивание в бетоносмесителе цементно-песчаного раствора.
- Добавление воды и введение пены с последующим смешиванием.
- Заливка пенобетонной смеси в формовочные емкости.
- Отстаивание готовых блоков в емкостях.
- Извлечение продукции из форм для дальнейшей сушки.
Для самостоятельного изготовления блоков необходимо заранее приготовить разборную форму. Остановимся более детально на особенностях выполнения отдельных видов работ.
Изготовление сборной формы для пеноблоков
Изготовление своими руками формовочного ящика для заливки пеноблоков предоставляет возможность не ограничиваться стандартными габаритами изделий. Конструируя формовочную емкость, следует учесть количество блоков, которые будут заливаться за один прием.
Для изготовления формы применяются следующие материалы:
- влагостойкая фанера;
- металлический лист;
- строганые доски.
Процесс изготовления формовочной емкости несложный:
- Подготовьте рабочий чертеж или эскиз формовочного ящика.
- Перенесите эскизные размеры на применяемый материал.
- Нарежьте боковые и поперечные заготовки требуемых размеров.
- Вырежьте дно формовочной емкости.
После изготовления отдельных элементов соберите форму. При использовании фанеры уложите внутрь ячеек полиэтилен, облегчающий извлечение готовых изделий и предохраняющий материал от поглощения влаги. Поверхность металлического ящика смажьте отработанным маслом.
Постарайтесь делать формы с максимально правильной геометриейПриготовление цементно песчаного раствора
Процесс подготовки песчано-цементной смеси выполняется по следующему алгоритму:
- Очистите песок от примесей с помощью сита.
- Взвесьте необходимое количество портландцемента и песка.
- Загрузите ингредиенты в бетоносмеситель.
- Перемешайте в течение 5 минут до однородной консистенции.
После перемешивания в готовую смесь добавьте воду и смешайте в течение трех минут с предварительно подготовленной пеной.
Какой использовать пенообразователь для пенобетона
Качество пенообразователя влияет на эксплуатационные характеристики пенобетона. Применяются различные пенообразователи:
- покупные, предлагаемые в специализированных магазинах. Они представляют собой концентрат, который разводится до требуемого состояния согласно рекомендациям предприятия-изготовителя;
- самостоятельно изготовленные. В состав самодельного пенообразователя входят едкий натр в количестве 0,15 кг, 0,06 кг столярного клея и килограмм канифоли. Ингредиенты смешивают при небольшом нагреве до однородной консистенции с последующим добавлением воды.
Самостоятельно подготовленный пенообразователь не уступает по качеству готовому концентрату.
Разливаем готовый пенобетонный раствор
Заполнение формовочных емкостей осуществляется различными способами:
- вручную при небольших объемах производства пенобетонных блоков;
- с помощью бетононасоса при изготовлении блоков в промышленных объемах.
Залитый пенобетон твердеет в течение 10-12 часов, после чего изделия извлекаются из форм, устанавливаются на поддоны и сушатся в закрытом помещении. При комнатной температуре продолжительность сушки достигает 48 часов.
Заключение
Изготовление пеноблоков в домашних условиях позволяет сэкономить денежные средства на строительство дома. Для организации производства блоков важно тщательно ознакомиться с технологическими нюансами, подобрать необходимое оборудование и изучить рецептуру.
Пенобетон своими руками: состав, технология
При возведении нового здания застройщик отслеживает одну цель — достичь максимальной экономии денег и при этом предоставить заказчику качественный и долговечный проект. Для снижения расходов на материалы в строительной сфере стали практиковать изготовление пеноблоков. При невысокой стоимости такой материал обладает массой эксплуатационных достоинств.
Как самому изготовить пенобетон
Чтобы создать качественный материал, необходимо подготовить специальное оборудование и изучить технологию изготовления. Она предусматривает следующие нюансы:
- В качестве исходного сырья для изготовления пеноблоков в домашних условиях может использоваться только чистый цемент под маркой не ниже 400.
- Пена добавляется только после тщательного перемешивания основных компонентов.
- Для проверки качества конечного продукта необходимо набрать в ведро небольшое количество смеси и перевернуть его: качественная пена не будет вытекать.
- В полузастывшем состоянии бетон достается из форм и разделяется на небольшие блоки. Оптимальный период, по истечении которого извлекается материал, составляет 24 часа. После разрезания блоки подсушиваются на поддоне в течение 15 часов при температуре выше 5°C.
Для изготовления пенобетона своими руками можно использовать такие технологии и способы:
- Автоклавный.
- Простой.
- Неавтоклавный.
- С применением бетономешалки и пеногенератора.
В большинстве случаев домашние мастера создают материал без применения печи. И хоть сама технология производства может показаться достаточно простой и доступной, при несоблюдении некоторых правил конечный продукт окажется низкокачественным и не будет соответствовать заявленным эксплуатационным требованиям.
Начиная изготовление, следует грамотно рассчитать пропорции компонентов, выбрать оптимальный временной интервал для замеса, просушивания и выдержки в формах. При соблюдении таких правил пенобетон получится надежным и долговечным.
Что нужно иметь для изготовления
Следует подготовить ряд материалов и оборудования, начиная изготовление; пенобетон можно сделать своими руками, используя:
- Бетономешалку. Ее объем определяется потребностями клиента. Для реализации проектов частного строительства хватает агрегата на 300 л.
- Среднефракционный речной песок, в составе которого отсутствуют любые примеси.
- Цементную смесь марки М400-М500. Заменять ее любыми другими компонентами запрещено.
- Парогенератор для пенобетона. Производство можно начинать и без этого оборудования, но его наличие гарантирует повышенную прочность и надежность конечной продукции.
- Воду.
- Емкости для заливки готовой смеси. В строительных магазинах предлагаются готовые формы для пеноблоков и газоблоков.
- Пенообразователь.
Существуют и другие компоненты, применяемые в особых случаях. В их числе красящая добавка, которая позволяет создавать цветной материал для помещений без отделки. Еще в состав могут вносить отвердитель, повышающий устойчивость пенобетона к отрицательным температурам, воздействию влаги и прочим негативным факторам.
Самостоятельный способ изготовления
Создавая пенобетон своими руками в домашних условиях, следует рассчитать объем емкости, куда будет помещаться готовая смесь. Руководствуясь полученным результатом, следует определить количество всех компонентов — на каждые 0,5 м³ задействуется 100 л воды и 200 кг цементной смеси с просеянным песком.
Первым делом в бетономешалку помещают песок и цемент. Затем с применением специального устройства и пенообразователя создается пена с расчетом по 500 л пены на 1 м³. Цементная смесь разбавляется водой и смешивается с пеной.
Многие системы для образования пены оборудованы насосным элементом, который позволяет быстро и эффективно закачивать консистенцию в барабан.
После помещения компонентов в емкость их нужно тщательно перемешать. Для изменения плотности в состав вносится разное количество пены. Раствор выливается в форму и просушивается. Потом сухие блоки достаются наружу и оставляются на 24 часа для просушки.
Образователь пены продается в строительных магазинах или создается своими руками. Для этой цели задействуется 150 г едкого натра, 1 кг канифоли и 60 г столярного клея. Все вещества соединяются, прогреваются, а потом размешиваются до однородного состояния. Перед производством в раствор добавляют воду.
Форму под блок можно изготовить своими руками, используя подручный материал. Такой этап требует повышенной точности и следования технологии. В противном случае геометрия блоков будет неточной. Чтобы предотвратить вытекание раствора, его следует обтянуть полиэтиленовой пленкой. Когда одна порция будет изъята, можно заливать следующую.
Себестоимость
Готовые магазинные блоки стоят намного дороже, чем самодельные изделия. Чтобы приготовить кубометр качественного материала, соответствующего марке D600, следует знать, из чего делают пено- и газобетон: Стандартный рецепт выглядит следующим образом:
- 200-250 кг песчано-цементной смеси.
- 1,5 л образователя пены.
- Вода. Можно использовать из централизованного водопровода. Главное — правильно рассчитать пропорции пенобетона и воды.
Еще следует учесть расходы на электрическую энергию, которая будет потребляться оборудованием. Они могут меняться в зависимости от региона, где находится мини-производство.
Так, в Москве электроэнергия стоит дороже, чем в Подмосковье или отдаленных регионах. Основная часть затрат идет на покупку цемента. При этом объемы финансовых вложений определяются и типом используемого оборудования.
Этапы работы
Интересуясь, как сделать пенобетон в домашних условиях, необходимо тщательно изучить технологию изготовления пеноблоков и найти оптимальный рецепт. После этого можно поэтапно выполнять требуемые действия, в точности соблюдая инструкцию.
Раствор пенообразователя
Технология пенобетона предусматривает подготовку цементного раствора. Его создают точно так же, как для традиционного бетона. В качестве цементной смеси рекомендуется использовать продукцию под марками М400 или М500.
Важно убедиться, что песок сухой и не имеет в своем составе ненужных примесей или добавок. Для разбавления компонентов используется простая вода из централизованной системы водоснабжения.
В готовый раствор добавляется пена. Пеногенератор продается в каждом строительном магазине или делается из подручных средств.
Разливание раствора по формам
Следующий этап заключается в разлитии подготовленной консистенции в заготовленные формы. Перед выполнением этого действия емкости смазываются особым раствором. Строители знают 2 методики, как сделать пеноблоки своими руками:
- Литьевая.
- Резательная.
Первая технология заключается в залитии раствора в заготовки. Когда он застынет, его можно достать из формы и выждать еще пару часов для окончательного затвердевания. Использование подобной методики имеет ряд недостатков. В первую очередь, это возможное повреждение металла, а еще деформация блоков при изъятии.
Устанавливать конструкции с неровной геометрией достаточно сложно, при этом они некачественные и недостаточно прочные. Однако метод резки более затратный, поскольку он требует покупки специального оборудования.
Технология резки
Производство пенобетонных блоков с применением технологии резки предусматривает разделение готовой плиты на несколько отдельных секций. В течение 6-9 часов исходное сырье приобретает оптимальную степень прочности и может сниматься с опалубки. Дальше подготовленный массив перемещается траверсой на резательное оборудование, и специалист приступает к процессу резки.
Плюсом подобной методики является высочайшая точность, поскольку допустимое отклонение не превышает 1 мм. Комплекс для резки оборудован специальным шнеком для снятия горбушки и витыми струнами, которые осуществляют резку материала. Для получения разных размеров блока специалист меняет положение режущих струн. 1 цикл длится в течение 5-7 минут.
После завершения мероприятия емкость с блоками помещается в место для просушивания. Уже через 12-24 часа, в зависимости от эффективности просушивания, пеноблок достается из поддона и перемещается на место хранения.
Методика обладает такими достоинствами:
- Геометрия блоков получается ровной и правильной.
- Края не имеют отклонений.
- Любые сколы и неровности исключены.
К минусам относят:
- Дополнительные затраты на покупку оборудования.
- Если бетон не застынет, он будет разрушен при выполнении резки.
Рекомендации специалистов
Специалисты рекомендуют придерживаться некоторых принципов и требований, которые позволят создать качественный материал без ошибок и отклонений:
- Для изготовления форм под будущие пеноблоки рекомендуется использовать фанеру с ламинированным покрытием или прочные листы металла.
- Перед помещением раствора в заготовку, ее следует обработать раствором, а саму конструкцию обтянуть полиэтиленовой пленкой.
- Просушивание осуществляется в температурном диапазоне +50…+60°C в течение 48 часов.
- Материал можно достать из формы только после его полного высыхания.
- Готовый блок держится на поддонах в течение нескольких часов. Только после этого его используют по назначению.
- Приступать к оштукатуриванию стен можно только через 3-4 месяца после кладки, поскольку блоки дают усадку.
- Перед началом работ по отделке следует очистить материал от грязи и пыли, а еще тщательно подготовить поверхность к нанесению слоя.
Домашняя фабрикация блоков
Если овладеть базовыми навыками производства, подготовить требуемое оборудование и материалы, в домашних условиях можно создать мини-фабрику по изготовлению пенобетона. Подобное решение позволит сэкономить деньги на покупке строительных материалов, а еще создать небольшой бизнес.
Вывод
Производство блоков из пенобетона в домашних условиях — отличный способ изготовить популярный строительный материал без переплат и неоправданных расходов. Чтобы конечный продукт соответствовал всем стандартам качества и экологичности, важно придерживаться установленного рецепта и в точности следовать инструкции.
Пенобетон своими руками: технология производства
Изготовить монолитный пенобетон своими руками в домашних условиях несложно. Главное, это подготовить необходимые инструменты и материалы, сделать формы. Чтобы изделие получилось качественным и соответствовало требуемым характеристикам, необходимо строго соблюдать технологию и этапы работы. Из готовых блоков удастся возвести крепкий дом, который прослужит не одно десятилетие.
Можно ли сделать самостоятельно?
Чтобы получить качественные пенобетонные блоки, необходимо подготовить соответствующее оборудование, а также материалы. При этом немаловажно строго соблюдать технологию приготовления, следя за правильностью пропорций используемого сырья. Если получится сделать пенобетон самостоятельно, строительство запланированного сооружения обойдется намного дешевле, нежели при покупке заводского сырья.
Какие понадобятся инструменты и материалы?
Для производства пенобетона необходимо подготовить такие материалы, как:
- просеянный песок, желательно речной;
- высококачественный цемент марки М400 и выше;
- вода;
- пенообразователь;
- модифицирующие добавки.
А также потребуется специальное оборудование для производства:
- механический смеситель для бетона;
- пеногенератор;
- формы для заливки массы.
Пеногенератор: можно ли его сделать самому?
Это специальная машина, предназначенная для образования пены, которую потом добавят в бетонную смесь, и, соединив компоненты, изготовляют пенобетон. Аппарат несложно сделать самостоятельно. Главное — это подготовить план и чертежи, где будет детально расписаны этапы изготовления установки. Вот как выглядит схема высокопарного парогенератора.
Имея на руках схему конструкции, человек сможет сам ее собрать.Сконструировать аппарат можно, применяя такие материалы и инвентарь:
- регулировочные вентили для запирания пены;
- труба;
- шланг;
- насос погружной;
- сварочный аппарат;
- компрессионная установка;
- листы из металла.
Как выглядит парогенератор для изготовления пенобетонных блоков, и принцип его работы показано в видео.
Тезнология производства: этапы работы
Приготовление раствора
Изготовление пенобетона начинается с замешивания бетонного раствора, который должен быть в меру жидкий. Важно, чтобы песок для смеси был полностью сухим, цемент выбирается марок М400, М500. Вода подойдет обычная, специально очищать ее не нужно. Для придания изделию прочности и гидрофобности, можно добавить с бетонный состав жидкое стекло. В готовую смесь с присадками добавляется пена, полученная из пенообразователя. Массу важно тщательно вымешать, чтобы не осталось никаких комков. Компоненты и их количество, необходимое для изготовления пены, представлено в таблице:
Материал | Количество, г |
Каустическая сода | 150 |
Столярный клей | 60 |
Канифоль | 1000 |
Как разлить в формы?
Данный метод предполагает заполнение раствором каждой ячейки формы.Емкость, где будет затвердевать раствор, перед заливкой смазывают маслосодержащим средством. Есть 2 метода изготовления пеноблоков:
- Литьевой. Пенобетонная смесь разливается по отдельным формам, после чего она остывает и из емкости вынимается готовое изделие. Однако этот способ имеет существенные недостатки: повреждение блочных элементов в момент извлечения, деформация металла.
- Резательный. В форму заливается готовый раствор, который после застывания разрезается пилой. Здесь тоже есть свои минусы — большое количество стружки, разрушение блоков в момент резки.
Технология резки
Чтобы избежать образования опилок во время разрезания газобетонных блоков, рекомендуется использовать струнную резальную установку. С ее помощью удастся ровно и правильно разделить схватившийся монолит. Плюсы такого метода:
- получение геометрически правильных изделий;
- отсутствие сколов и неровностей по краям;
- возможность делать блочные элементы разных размеров.
Однако у резательного метода есть и недостатки. Основным является дорогостоящее оборудование, так как вручную разрезать монолит не получится, поэтому нужно приобрести специальную установку со струной для резки. Еще один минус — важность выбора момента резки. Если изделие полностью высохнет, струна не сможет качественно и ровно разрезать монолит на блочные элементы.
Полезные рекомендации
Чтобы пеноблок получился качественным и прочным, сушить расформированную пенобетонную массу рекомендуется при температуре 50—60 °C в течение 48 часов. Для повышения физико-технических характеристик в раствор для пенобетона добавляют жидкое стекло. Формовые изделия извлекаются только после полного высыхания. Готовые блоки можно начать использовать через 2—3 часа после изъятия. Хранить пенобетон рекомендуется при плюсовых температурах, колеблющихся в диапазоне +10 — +25 градусов по Цельсию. Важно помнить, что стоимость готового изделия зависит от используемых составляющих компонентов и их цены.
метод сухой минерализации, баротехнология, методы изготовления, видео
В современном строительстве легкий стеновой материал занимает лидирующие позиции. Сегодня в промышленной сфере хорошо налажено изготовление пенобетона, при этом производственный процесс происходит на основе разных технологий, включающих в себя несколько стадий производства. Рекомендуем ознакомится с характеристиками пенобетонных блоков, что производятся массово, а так же узнать сколько в 1 кубе пеноблоков.
Технология изготовления пенобетона
Производственный процесс состоит из нескольких стадий:
- Приготовление рабочей смеси, в состав которой входят цемент, кварцевый (речной) песок либо промышленные отходы (зола уноса), вода, пенообразователь, ускорители твердения, также могут применяться воздухововлекающие добавки и пластификаторы.
- Заливка раствора в специальные металлические формы, где осуществляется формовка ячеистого камня.
- Сушка – этап твердения. Именно на этом этапе может применяться термообработка с применением камеры СВЧ лучевого типа.
- Распалубка формы.
- Нарезка камня в соответствии с размерами.
Не существует строгого соблюдения этапов в ходе производственного процесса, все зависит от выбранного способа и примененного оборудования. Об основных свойствах пенобетона расскажет эта статья.
Методы производства пенобетона
Различают следующие методы производства:
- Классический метод производства пенобетона заключается в применении отдельного приготовления бетонной смеси и пены, которые осуществляются одновременно, но только в разных агрегатах: смесь готовится в бетоносмесителе, а пена – в пеногенераторе. Когда в двух агрегатах компоненты будут соединены, в бетоносмеситель из пеногенераторной установки подается готовая пена. В данном технологическом процессе ко всем используемым ингредиентам предъявляются высокие требования, так как от этого зависит качество стенового материала.
- Баротехнология пенобетона отличается простотой и экономичностью. Недостатком является низкая прочность камня, который не может применяться в масштабном и многоэтажном строительстве. Сам процесс заключается в использовании герметичного смесителя, в который закладываются все компоненты и пенообразователь, воздух в камеру нагнетается компрессором. Тщательное размешивание содержимого камеры происходит под высоким давлением, в результате чего смесь получает хорошее насыщение воздухом. После чего полученный раствор подается по трубопроводу под давлением в специальные литьевые формы, где увеличивается в объеме за счет насыщения воздушными частицами.
- Метод сухой минерализации используется для получения высокопрочного пенобетона (от Д300 до Д900). Простой технологический процесс включает в себя два этапа: заливку пены в смеситель; соединение и перемешивание сухого цемента и песка с пеной.
Как происходит изготовление пенобетона разными способами наглядно показано на видео, размещенных в Интернете. Узнать о планетарном бетоносмесителе можно здесь.
Только от примененной технологии зависит, сколько будет стоить легкий стеновой материал. Поэтому зная, какие отличия присутствуют в технологических процессах и как производят пенобетон, можно выбрать качественный и прочный материал, который прослужит очень долго. Характеристику пеноблоков и их ценовую политику узнайте тут.
Пенобетон — материалы, свойства, преимущества и производство
🕑 Время чтения: 1 минута
Пенобетон — это тип легкого бетона, который изготавливается из цемента, песка или летучей золы, воды и пены. Пенобетон бывает в виде вспененного раствора или вспененного раствора. Пенобетон можно определить как вяжущий материал, состоящий минимум на 20 процентов из пены, которая механически вовлекается в пластичный раствор. Плотность пенобетона в сухом состоянии может варьироваться от 300 до 1600 кг / м3.Прочность пенобетона на сжатие, определенная через 28 суток, составляет от 0,2 до 10 Н / мм 2 или может быть выше. Пенобетон отличается от бетона с воздухововлекающими добавками по объему захваченного воздуха. Бетон с воздухововлекающими добавками занимает от 3 до 8 процентов воздуха. Он также отличается от замедленного раствора и газобетона по той же причине процентного содержания воздуха. В случае минометных систем замедленного действия — от 15 до 22 процентов. В случае газобетона пузырьки образуются химически. История пенобетона Пенобетон имеет долгую историю и впервые был введен в эксплуатацию в 1923 году. Первоначально он использовался в качестве изоляционного материала. За последние 20 лет усовершенствования в области производственного оборудования и повышения качества пенобетона позволили широко использовать пенобетон. Производство пенобетона При производстве пенобетона поверхностно-активное вещество растворяется в воде, которая пропускается через пеногенератор, который дает пену стабильной формы.Пена производится в смеси с цементным раствором или затиркой, так что получается вспененное количество необходимой плотности. Эти поверхностно-активные вещества также используются при производстве наполнителей с низкой плотностью. Их также называют контролируемыми материалами низкой прочности (CLSM). Здесь для получения содержания воздуха от 15 до 25 процентов пену добавляют непосредственно в смесь с низким содержанием цемента и богатого песка. Следует иметь в виду, что некоторые производители поставляют заполнители с низкой плотностью в виде пенобетона, поэтому следует соблюдать осторожность. Для производства пенобетона используются два основных метода:- Встроенный метод и
- Метод предварительного вспенивания
- Мокрый метод — встроенная система
- Сухой метод — встроенная система
- Объем пены
- Содержание цемента в смеси
- Наполнитель
- Возраст
Таблица.1. Типичные свойства пенобетона в затвердевшем состоянии
Плотность в сухом состоянии кг / м 3 | Прочность на сжатие Н / мм 2 | Предел прочности Н / мм 2 | Водопоглощение кг / м 2 |
400 | 0,5 — 1 | 0,05-0,1 | 75 |
600 | 1-1.5 | 0,2-0,3 | 33 |
800 | 1,5 -2 | 0,3-0,4 | 15 |
1000 | 2,5 -3 | 0,4-0,6 | 7 |
1200 | 4,5-5,5 | 0,6–1,1 | 5 |
1400 | 6-8 | 0,8–1,2 | 5 |
16 00 | 7.5-10 | 1–1,6 | 5 |
- Пенобетонная смесь не оседает. Следовательно, уплотнение не требуется.
- Собственный вес уменьшен, так как это легкий бетон
- Пенобетон в свежем состоянии имеет сыпучую консистенцию.Это свойство поможет полностью заполнить пустоты.
- Пенобетонная конструкция обладает отличной способностью распределять и распределять нагрузку.
- Пенобетон Не создает значительных боковых нагрузок
- Свойство водопоглощения
- Партии пенобетона просты в производстве, поэтому проверка и контроль качества легко выполняются.
- Пенобетон имеет повышенную устойчивость к замерзанию и оттаиванию
- Безопасное и быстрое выполнение работ
- Рентабельность, меньше обслуживания
- Наличие воды в смешанном материале делает пенобетон очень чувствительным.
- Сложность в отделке
- Время смешивания больше
- С увеличением плотности снижаются прочность на сжатие и прочность на изгиб.
Пенобетон — обзор
1.6.2.2 Составляющие материала
Пенобетон представляет собой смесь цемента, песка, воды и пенобетона, причем подавляющее большинство пенобетона не содержит агрегаты, а только мелкий песок (рис. 1.8) [4]. Чрезвычайно легкий пенобетон содержит только цемент, воду и пену. Сырьем для производства пенобетона являются вяжущее, заполнители, пенообразователь и вода.OPC используется с содержанием от 300 до 600 кг / м 3 . В дополнение к OPC, быстротвердеющему PC, высокоглиноземистые цементы могут использоваться для сокращения времени схватывания и улучшения начальной прочности. Возможна частичная замена цемента FA, GGBS и другими мелкими материалами. SF может быть добавлен для улучшения прочности бетона на сжатие. Однако следует убедиться в совместимости этих добавок с пенообразователями. GGBS придает пенобетону вязкую, почти липкую консистенцию.Использование FA делает смесь более текучей. Ключевым требованием здесь является наличие стабильной пены.
Рисунок 1.8. Материалы, применяемые для пенобетона.
Используется только мелкий песок с размером частиц до 5 мм, так как крупный заполнитель имеет тенденцию оседать в легкой строительной смеси и вызывает схлопывание пены во время перемешивания. Предпочтительны песок очень низкой плотности с модулем крупности приблизительно 1,5, включая FA, известь, карбонат кальция, щебень, гранитную пыль, гранулы пенополистирола, мелкие частицы спеченного заполнителя FA, резиновые крошки, переработанное стекло и формовочный песок.Легкие заполнители, такие как спеченный заполнитель FA и вермикулит, также могут быть использованы для производства пенобетона.
Предварительно сформованная пена представляет собой смесь пенообразователя, воды и воздуха с плотностью 75 кг / м. 3 . Добавление предварительно сформованной пены снижает плотность смеси, увеличивая выход. Чем больше добавлено количество пены, тем легче получаемый материал. При производстве пенобетона используются два вида пены: мокрая пена и сухая пена. Влажную пену получают путем распыления раствора пенообразователя и воды на мелкую сетку.Пена, получаемая в этом случае, по внешнему виду похожа на пену для пены для ванн с размером пузырьков от 2 до 5 мм. Однако добавляемая пена должна оставаться стабильной, не разрушаясь во время перекачивания, укладки и отверждения. Этот фактор становится заметным, когда количество пены превышает 50% от базовой смеси (то есть при плотности приблизительно 1100 кг / м 3 ). Пенобетон ниже этой плотности необходимо производить и использовать с осторожностью. Водоцементное соотношение обычно колеблется от 0.От 4 до 0,8, в зависимости от пропорций смеси и требований к консистенции. Когда очень мелкие материалы используются в больших количествах, потребность в воде увеличивается, что снижает прочность пенобетона. В пенобетон можно использовать химические добавки, такие как SP, VMA и ускорители, однако необходимо обеспечить их влияние на стабильность пены. Добавление волокон, таких как полипропиленовые и полиэфирные волокна, может использоваться для ограничения как пластической, так и усадочной деформации при высыхании. Компоненты базовой смеси могут вступать в реакцию с некоторыми вспенивающими химикатами, что приводит к дестабилизации смеси.
IRJET-Запрошенная вами страница не найдена на нашем сайте
IRJET приглашает статьи из различных инженерных и технологических и научных дисциплин для Тома 8, выпуск 9 (сентябрь 2021 г.)
Отправить сейчас
IRJET Vol-8, выпуск 9 , Сентябрь 2021 Публикация в процессе …
Обзор статей
IRJET получил «Импакт-фактор научного журнала: 7,529» за 2020 год.
Проверить здесь
IRJET получил сертификат регистрации ISO 9001: 2008 для свою систему управления качеством.
IRJET приглашает специалистов по различным инженерным и технологическим дисциплинам, научным дисциплинам для Тома 8, выпуск 9 (сентябрь 2021 г.)
Отправить сейчас
IRJET Vol-8, выпуск 9, сентябрь 2021 г. Публикация продолжается …
Просмотр Документы
IRJET получил «Импакт-фактор научного журнала: 7,529» за 2020 год.
Проверить здесь
IRJET получил сертификат регистрации ISO 9001: 2008 для своей системы менеджмента качества.
IRJET приглашает специалистов по различным инженерным и технологическим дисциплинам, научным дисциплинам для Тома 8, выпуск 9 (сентябрь 2021 г.)
Отправить сейчас
IRJET Vol-8, выпуск 9, сентябрь 2021 г. Публикация продолжается …
Просмотр Документы
IRJET получил «Импакт-фактор научного журнала: 7,529» за 2020 год.
Проверить здесь
IRJET получил сертификат регистрации ISO 9001: 2008 для своей системы менеджмента качества.
IRJET приглашает специалистов по различным инженерным и технологическим дисциплинам, научным дисциплинам для Тома 8, выпуск 9 (сентябрь 2021 г.)
Отправить сейчас
IRJET Vol-8, выпуск 9, сентябрь 2021 г. Публикация продолжается …
Просмотр Документы
IRJET получил «Импакт-фактор научного журнала: 7,529» за 2020 год.
Проверить здесь
IRJET получил сертификат регистрации ISO 9001: 2008 для своей системы менеджмента качества.
IRJET приглашает специалистов по различным инженерным и технологическим дисциплинам, научным дисциплинам для Тома 8, выпуск 9 (сентябрь 2021 г.)
Отправить сейчас
IRJET Vol-8, выпуск 9, сентябрь 2021 г. Публикация продолжается …
Просмотр Документы
IRJET получил «Импакт-фактор научного журнала: 7,529» за 2020 год.
Проверить здесь
IRJET получил сертификат регистрации ISO 9001: 2008 для своей системы менеджмента качества.
IRJET приглашает специалистов по различным инженерным и технологическим дисциплинам, научным дисциплинам для Тома 8, выпуск 9 (сентябрь 2021 г.)
Отправить сейчас
IRJET Vol-8, выпуск 9, сентябрь 2021 г. Публикация продолжается …
Просмотр Документы
IRJET получил «Импакт-фактор научного журнала: 7,529» за 2020 год.
Проверить здесь
IRJET получил сертификат регистрации ISO 9001: 2008 для своей системы менеджмента качества.
IRJET приглашает специалистов по различным инженерным и технологическим дисциплинам, научным дисциплинам для Тома 8, выпуск 9 (сентябрь 2021 г.)
Отправить сейчас
IRJET Vol-8, выпуск 9, сентябрь 2021 г. Публикация продолжается …
Просмотр Документы
IRJET получил «Импакт-фактор научного журнала: 7,529» за 2020 год.
Проверить здесь
IRJET получил сертификат регистрации ISO 9001: 2008 для своей системы менеджмента качества.
IRJET приглашает специалистов по различным инженерным и технологическим дисциплинам, научным дисциплинам для Тома 8, выпуск 9 (сентябрь 2021 г.)
Отправить сейчас
IRJET Vol-8, выпуск 9, сентябрь 2021 г. Публикация продолжается …
Просмотр Документы
IRJET получил «Импакт-фактор научного журнала: 7,529» за 2020 год.
Проверить здесь
IRJET получил сертификат регистрации ISO 9001: 2008 для своей системы менеджмента качества.
Основы ячеистого бетона | Richway
Если вы только начинаете работать с ячеистым бетоном или у вас есть базовые вопросы о ячеистом бетоне, вот отличное место для начала. Мы объясним, что такое ячеистый бетон, для чего он используется, а также расскажем о часто задаваемых вопросах. Если после прочтения этой страницы у вас остались вопросы, позвоните нам, чтобы обсудить ваши вопросы, или посетите другие страницы наших ресурсов, чтобы узнать больше о ячеистом бетоне.
Что такое ячеистый бетон?
Ячеистый бетон низкой плотности, как определено в главе 523.1 ACI, представляет собой бетон, изготовленный из гидравлического цемента, воды и предварительно отформованной пены для образования затвердевшего материала, имеющего плотность при сушке в печи 50 фунтов на кубический фут (PCF) или меньше.
Хотя определение ACI определяет ячеистый бетон низкой плотности с плотностью ниже 50 фунтов на квадратный фут, ячеистый бетон может иметь плотность от 20 до 120 фунтов на квадратный дюйм.
В более широком смысле любой цементный раствор или вяжущий материал, в котором используется пена, генерируемая извне, для увеличения содержания воздуха выше 10%, может считаться ячеистым бетоном.Ячеистый бетон может иметь другие названия, включая пеноцемент, пенобетон или легкую текучую заливку.
Несмотря на то, что существует ряд легких вяжущих материалов, ключевым отличительным фактором между ячеистым бетоном и другими легкими вяжущими материалами является использование пены, образующейся извне, для уменьшения плотности. Вероятно, наиболее близким материалом к ячеистому бетону является газобетон автоклавного твердения (AAC).
Основными отличиями являются процессы, используемые для создания воздуха в материале, и необходимое оборудование.AAC использует химическую реакцию внутри самой суспензии для образования воздушных пустот для снижения плотности. Однако производство ячеистого бетона с пеной, генерируемой извне, обеспечивает более универсальный материал за небольшую часть капитальных затрат, необходимых для оборудования.
Применение и преимущества ячеистого бетона
Ячеистый бетон имеет множество применений и не имеет единственного преимущества. В зависимости от области применения он может быть выбран из-за его теплоизоляционных и звукоизоляционных свойств, прокачиваемости и текучести, простоты обращения из-за его небольшого веса или в качестве экономичной альтернативы заполняющим материалам.Во всем мире ячеистый бетон используется в строительстве, например, для настилов крыш и настилов пола, а также в геотехнических приложениях, таких как заполнение кольцевого пространства в футеровке скольжения и отказ от заполнения пустот. Ячеистый бетон также можно найти в архитектуре и сборных железобетонных изделиях. Ниже приведены наиболее распространенные области применения ячеистого бетона; однако это не исчерпывающий список.
Заполнение пустот: Воронки, колодцы, туннели, цистерны, заброшенные инженерные трубы, затирка кольцевого раствора.Легко течет и обеспечивает меньший вес на почве.
Восстановление почвы: Когда существуют плохие грунтовые условия, ячеистый бетон может быть использован для создания прочного основания при одновременном снижении нагрузки на грунт.
Заливка траншеи для инженерных коммуникаций: Защищает и поддерживает инженерные коммуникации, а также снижает или устраняет необходимость в уплотнении.
Альтернатива текучей засыпке / геопеной: Для любых применений, где используются текучие засыпки или блоки из геопены, ячеистый бетон является отличной альтернативой и во многих случаях предпочтительным материалом.
Засыпка траншеи водовыпуска: Предотвращает последующее оседание почвы и последующие провалы на дороге.
Заполнение абатмента моста / эстакады: Устраняет оседание после строительства. Поскольку ячеистый бетон не требует уплотнения, он не сжимается со временем, создавая «провал» на подходе к мосту или эстакаде. Кроме того, практически исключаются боковые нагрузки на существующий абатмент.
Засыпка подпорной стены / стены MSE: Снижение боковой нагрузки является основным преимуществом.Ячеистый бетон также может значительно снизить потенциальное повреждение георешетки во время засыпки.
Панели ограждения вдоль автомагистралей: Для звукового контроля и визуального блокирования. Потенциал экономии за счет снижения веса.
Противоударные барьеры / Поглощение энергии: Предварительно отлитые кубики переменной плотности или залить их на месте.
Настилы пола: Снижает вес конструкции при сохранении качества бетонного пола. Используется для выравнивания и замены смесей на основе гипса.
Настилы крыши: Уменьшает вес и обеспечивает тепло- и звукоизоляцию. Возможны умеренные уклоны.
Сборные железобетонные изделия: Снижает вес и стоимость. Снижает транспортные расходы / позволяет загружать больше штук на грузовик. Более легкий монтаж.
Тепловая засыпка и заполнение вспомогательной плиты: Обеспечивает теплоизоляцию и водонепроницаемость, а также снижает гидростатическую боковую нагрузку на фундамент.
I Внутренние стены: Отливка на месте или сборка панелей.Снижает вес и стоимость ниже бетонной стены полной плотности. Более звукоизоляция и огнестойкость, чем каркасная стена.
Основание подпорной стены: Правильная конструкция смеси должна быть самовыравнивающейся и может значительно ускорить строительство основания и улучшить грузоподъемность.
Палубы тротуаров, патио и крыльца: Снижает вес и стоимость.
Резные скульптуры из бетона: Ячеистый бетон в диапазоне 40-60 PCF можно вырезать и формировать с помощью цепных пил, ручных инструментов и других методов для создания произведений искусства из уникального материала.
Часто задаваемые вопросы по ячеистому бетону
Примечание. Следующие ответы верны, насколько нам известно, но могут не применяться в определенных приложениях или ситуациях. Большинство из них предназначены для предоставления общей информации, а не для информации о конкретном проекте или приложении.
Каков процесс изготовления ячеистого бетона?
Есть два метода производства ячеистого бетона. Первый — это периодический метод производства, при котором пена, образующаяся извне, вводится в барабан миксера в течение расчетного периода времени.Второй — это метод непрерывного производства, при котором пена впрыскивается в линию на напорной стороне насоса. Richway предлагает оборудование для обоих методов производства.
Какова прочность ячеистого бетона?
По мере уменьшения плотности уменьшается и прочность на сжатие. См. Таблицы и диаграммы прочности для получения более подробной информации, но, например, плотность 60 фунтов на квадратный фут будет иметь прочность в диапазоне от 600 до 1000 фунтов на квадратный дюйм.
Является ли очистка грузовика проблемой при использовании пакетного метода?
Обычно это будет проще, но если есть цементная паста без какой-либо пены, покрывающей барабан, это может быть труднее.
Какой установлен срок для ячеистого бетона?
Время схватывания ячеистого бетона обычно немного больше по сравнению с «обычным» бетоном из-за поверхностно-активных веществ, используемых при производстве пены. Однако, как и все, что производится с портландцементом, время изготовления и размещения ограничено. Как правило, мы рекомендуем ограничивать рабочее время примерно четырьмя часами после смешивания Portland с водой или примерно тремя часами после добавления пены.По прошествии этого времени материал следует оставить в покое, чтобы продолжить процесс схватывания. Продолжение перекачивания или перемещения материала может привести к его разрушению. Однако установленное время может варьироваться в зависимости от области применения, условий рабочей площадки и использования замедлителей или ускорителей.
Я немного прочитал о ячеистом бетоне, и здесь используется термин «предварительно сформированная пена». Почему вы используете термин «созданный извне»?
Мы думаем, что «производимый извне» — это гораздо более четкая терминология и не подразумевает жесткую пену на нефтяной основе или что-то, что было получено задолго до ее использования.Пена имеет консистенцию плотной густой пены шампуня и образуется «на ходу», когда она смешивается или впрыскивается в смеситель. Он генерируется извне, а не внутри самого смесителя, как в случае с воздухововлекающим агентом.
Сколько цементного порошка используется на дворе ячеистого бетона?
Если чистый цементный раствор используется с соотношением 0,50 в / ц, базовый раствор на ярд будет содержать примерно 2060 фунтов цемента и 1030 фунтов воды с плотностью 115 PCF.Если затем добавить пену до плотности 30 PCF, у нас будет 3,65 ярда материала 30 PCF с примерно 565 фунтами цемента на ярд. У нас есть калькулятор расчета смеси, доступный на нашем веб-сайте, который рассчитывает вес партии смеси, время дозирования пены и анализ сценария затрат.
Можно ли использовать летучую золу или другие пуццоланы в ячеистом бетоне?
Да. Как и в случае с бетоном стандартной плотности, окончательные свойства материала будут затронуты, как правило, так же, как альтернативные пуццоланы будут влиять на «нормальный» бетон.Что касается летучей золы, следует отметить, что зола с высоким содержанием углерода может разрушать пену, поэтому ее следует избегать.
Могу ли я использовать редукторы воды и другие добавки?
Да, можно использовать разбавители воды, которые помогут с диспергированием и смачиванием цементного порошка перед добавлением пены. Также можно использовать большинство других добавок, но во всех случаях тесты следует проводить до того, как будет завершен дизайн смеси. Некоторые суперпластификаторы могут разрушить пену, поэтому необходимо провести тщательное тестирование.Воздухововлекающие добавки обычно не используются при производстве суспензии для изготовления ячеистого бетона, поскольку пена — это воздух, добавляемый к смеси.
А как насчет размещения и отделки?
Ячеистый бетон легко перекачивается. При высоком содержании воды и низкой плотности он может быть фактически самовыравнивающимся, но его всегда легче перемещать, чем бетон стандартной плотности. Обычно его легко отделывать, но при некоторых значениях плотности он липкий и его трудно затирать шпателем.Как правило, для геотехнических применений отделка не требуется.
Есть проблемы с перекачкой?
Насосы для ячеистого бетона и очень хорошая текучесть.
Просмотреть все ресурсы
Дизайн материалов и оценка характеристик пенобетона для цифрового производства
Реферат
Трехмерная (3D) печать пенобетоном, который известен своими отличными физико-механическими свойствами, еще не проводилась целенаправленно исследованы.В данной статье представлен методический подход к созданию смесей из пенобетонов, пригодных для 3D-печати, и систематическое исследование возможностей применения этого типа материала в цифровом строительстве. Три различных пенобетонных состава с соотношением воды к вяжущему между 0,33–0,36 и плотностью от 1100 до 1580 кг / м 3 в свежем состоянии были произведены методом предварительного вспенивания с использованием пенообразователя на белковой основе. На основе испытаний в свежем состоянии, включая 3D-печать как таковую, был определен оптимальный состав и охарактеризована его прочность на сжатие и изгиб.Пенобетон, пригодный для печати, показал низкую теплопроводность и относительно высокую прочность на сжатие, превышающую 10 МПа; Таким образом, он соответствовал требованиям, предъявляемым к строительным материалам, используемым для изготовления несущих стеновых элементов в многоэтажных домах. Таким образом, он подходит для приложений 3D-печати, одновременно выполняя как несущие, так и изолирующие функции.
Ключевые слова: цифровое изготовление , 3D-печать, пенобетон, дизайн смеси, испытание материалов
1. Введение
Пенобетон (FC) — это легкий цементный материал с ячеистой структурой, получаемый путем введения воздушных пустот в строительный раствор или цемент вставить.Он может иметь плотность от 200 до 1900 кг / м 3 . Пенобетон плотностью менее 400 кг / м 3 используется в основном в качестве наполнителя или изоляционного материала [1,2,3]. Из-за технической и инженерной незнания большинства практиков и предполагаемых трудностей в достижении достаточно высокой прочности в последние несколько десятилетий пенобетон в значительной степени игнорировался для использования в конструкционных приложениях. В большинстве случаев пенобетон использовался для заполнения пустот, выполнял функцию теплоизоляции и действовал как акустический глушитель.Достижения в области химических и механических технологий вспенивания, добавок в бетон и других добавок значительно улучшили стабильность и механические свойства пенобетона. В настоящее время потенциал этого материала для структурного применения хорошо известен, и многочисленные исследовательские проекты были сосредоточены на улучшении свойств пенобетона, особенно в отношении его механических характеристик несущей способности [2,4,5].
Группы, работающие с предвидением в области цифрового производства, определили будущую потребность в устойчивых строительных материалах, которые являются экономически эффективными и экологически чистыми [6].Ожидается, что после завершения предварительных исследований и описания фундаментальных принципов цифрового производства из вяжущих материалов следующим шагом станет переосмысление технологии, включая сокращение материальных затрат и воздействия на окружающую среду. Пенобетон имеет небольшой удельный вес, что снижает собственные нагрузки и, таким образом, позволяет уменьшить габариты фундамента и количество арматуры. Кроме того, низкая теплопроводность пенобетона позволяет сократить использование дополнительных изоляционных материалов, которые в основном основаны на нефтехимических полимерах с высоким содержанием CO 2 и очень ограниченной возможностью вторичной переработки.В отличие от таких материалов, пенобетон состоит из минеральных компонентов с незначительным содержанием химических примесей [7]. Кроме того, поскольку применение дополнительных изоляционных панелей может больше не потребоваться, можно ожидать значительного сокращения энергопотребления и времени на транспортировку и монтаж, а также снижение шума на строительной площадке. Подводя итог, пенобетон признан универсальным строительным материалом, экологически чистым и технически эффективным.
Концепция 3D-печати бетона на месте (CONPrint3D), разработанная в Техническом университете Дрездена, способствует реализации преимуществ аддитивных технологий в строительной отрасли [8]. В отличие от концепций, продвигающих печать интегрированной опалубки, CONPrint3D подчеркивает сокращение второстепенных шагов, таких как заполнение печатных форм [9,10]. Эта технология позволяет печатать стены большой толщины, заменяя кладку.Применение пенобетона в рамках концепции CONPrint3D является многообещающим и потенциально позволяет изготавливать несущие стены и конструктивные элементы с такими свойствами, как превосходная теплоизоляция, звукопоглощение и огнестойкость [11,12]. Авторы ожидают, что применение различных материалов на основе цемента в 3D-печати бетона упростит формулирование новых строительных стандартов и перейдет к полной автоматизации строительных процессов. Изменяя плотность и толщину стен из пенобетона, напечатанных на 3D-принтере, можно полностью или частично отказаться от дополнительных систем изоляции.Еще одним аспектом, облегчающим применение пенобетона в качестве материала, выполняющего как изоляционные, так и структурные функции, является легкость его переработки и утилизации.
В литературе есть пример, описывающий автоматизированное нанесение пенобетона на вертикальные поверхности методом экструзии [13]. Авторы поместили пенобетон на голые стены существующих зданий, чтобы получить изоляцию фасада, пригодную для вторичной переработки и свободную по дизайну и форме.Использованный материал обладал видимой стабильностью формы, прочностные характеристики не изучались.
Faliano et al. В [14,15] описаны пенобетоны с плотностью в сухом состоянии от 400 до 800 кг / м 3 и прочностью на сжатие от 1,5 до 9 МПа, которые, кроме того, сохраняют стабильность размеров после экструзии. Отношение воды к цементу (в / ц) было установлено на 0,3 во всех смесях. Ни наполнители, ни заполнители не использовались. Предварительно сформированная пена была приготовлена с пенообразователем на белковой основе.Исследование дает широкий спектр результатов, связанных с влиянием условий отверждения на прочность на растяжение и сжатие. Однако описанная экспериментальная процедура не представляла типичных процедур 3D-печати с помощью роботизированных печатающих головок. Материал был скорее заполнен стальной опалубкой и вручную вытеснен с опалубки на ранней стадии гидратации. Техника осаждения, использованная Faliano et al. имитирует автоматическую экструзию и обеспечивает первое заполнение поведения материала с точки зрения стабильности формы и развития прочности в сыром виде.
Не существует стандартного способа измерения свойств сборки. Как правило, возможность сборки оценивается путем печати определенного количества слоев с определенной скоростью [16,17,18,19]. На данный момент трудно оценить возможную конструктивность пенобетона, разработанного Faliano et al. [11,12], поскольку время покоя пенобетона и его реологические характеристики в свежем состоянии не уточняются. В исследовании подчеркивалось использование агентов, повышающих вязкость (VEA), и указывалось на необходимость дополнительных исследований поведения экструдированного пенобетона в свежем состоянии.Авторы предполагали возможность применения экструдированных пенобетонных смесей плотностью до 200 кг / м 3 3 . Как конструкционные, так и неструктурные области применения экструдируемых элементов из пенобетона были признаны эффективными и экологически безопасными. Одним из предложенных вариантов применения было формирование многослойных изоляционных панелей на месте.
В общем, бетон, который подходит для цифрового строительства, должен быть хорошо экструдируемым и демонстрировать адекватную строительную способность.Кроме того, напечатанные слои должны иметь хорошие межслойные связи [9,16,20,21]. Наконец, материал должен обладать соответствующими механическими свойствами, например прочностью на сжатие [9,21,22,23]. Обычный пенобетон отличается хорошей обрабатываемостью и текучестью, что является многообещающим с точки зрения технологических параметров экструзии и прокачиваемости, необходимых для 3D-печати. Обычно пенобетон перекачивается к месту укладки и, как правило, не требует уплотнения; пенобетон можно успешно перекачивать на значительные расстояния и высоты [1].Таким образом, с этой точки зрения он подходит для технологий 3D-печати на основе экструзии. Однако необходимо учитывать потенциальное влияние перекачки на характеристики пены, поскольку они могут повлиять на стабильность смеси и привести к изменению ее плотности.
Другой важной особенностью материала для печати является его способность к наращиванию, которая складывается из стабильности формы напечатанных слоев под их собственным весом и способности удерживать следующие слои с минимальной деформацией [20].Другими словами, строительная способность пенобетона может быть описана как сочетание самостойкости и достаточной жесткости с ранним схватыванием. Что касается самоустойчивости, пенобетон обычно воспринимается как сыпучий, самоуплотняющийся материал. Признано, что при более низких плотностях текучесть снижается из-за уменьшения собственного веса и адгезии между твердыми частицами и пузырьками воздуха [24]. Однако предыдущие исследования пенобетона показали, что снижение текучести по сравнению с обычными применениями, такими как заполнение пустот, часто рассматривается как признак низкого качества или несоответствующего дизайна смеси [4].Имея в виду 3D-печать в качестве технологии нанесения, должно быть возможно получение перекачиваемого и самостабильного пенобетона, но на сегодняшний день этот подход не был тщательно исследован, поэтому необходимы дальнейшие исследования.
В исследованиях, связанных с 3D-печатью с использованием бетона с нормальным весом, быстрое схватывание обычно достигается за счет использования ускоряющих добавок или выбора цементов с более коротким временем схватывания, то есть быстротвердеющих сульфоалюминатных или алюминатных цементов [6,25]. Такими же подходами можно добиться быстрого схватывания пенобетона.Однако, как сообщается в [26], использование ускоряющих схватывание материалов в пенобетоне не всегда дает такой же эффект, как в бетоне с нормальным весом. Более того, они могут вызвать нестабильность и повлиять на качество пенобетона. В некоторых исследованиях использовались различные типы цемента, характеризующиеся быстрым схватыванием [27,28]. Быстротвердеющий портландцемент часто используется для снижения рисков нестабильности и сегрегации, а также для обеспечения того, чтобы пенобетон на очень ранней стадии развил прочную однородную микроструктуру.Также было замечено, что добавление алюминатного цемента, сокращая время схватывания, может снизить прочность пенобетона на сжатие [29]. Кроме того, упомянутые специальные вяжущие материалы относительно дороги, что ограничивает область их применения.
Еще одним важным аспектом печатных элементов является их межслойное склеивание. Он сильно влияет на механические свойства, долговечность и удобство эксплуатации 3D-печатных конструкций; см., например, [30,31,32]. Качество межслойной связи зависит от множества факторов, связанных со свойствами свежего бетона и техникой печати, т.е.е., временной интервал между слоями, форма и размер нити и т. д. Не было найдено литературы, которая могла бы помочь оценить поведение пенобетона с этой точки зрения. Что касается проницаемости пенобетона и его устойчивости к агрессивным средам, было доказано, что его ячеистая пористая структура не обязательно делает его менее устойчивым к проникновению влаги по сравнению с обычным плотным бетоном, поскольку воздушные пустоты не связаны между собой и действуют как буфер, предотвращающий капиллярное всасывание и другие транспортные процессы.
Как правило, существует два механизма введения больших объемов воздушных пустот в смесь: (1) использование газообразующих химикатов, таких как алюминиевый порошок, и (2) использование пенообразователей. Добавление газообразующих агентов приводит к образованию пузырьков в результате химических реакций с щелочными продуктами гидратации, например гидроксидом кальция [33]. Этот метод используется для производства газобетона, который еще называют газобетоном. Как сообщают Холт и Райвио [31], пенобетон, полученный с добавлением алюминиевой пудры, имеет ряд существенных недостатков, таких как относительно высокая стоимость, а также более низкая прочность, более высокое содержание влаги и более выраженная усадка по сравнению с традиционным бетоном.Свойства газобетона можно значительно улучшить путем отверждения паром под высоким давлением в автоклаве. Однако такое отверждение было бы контрпродуктивным, поскольку основным преимуществом технологии 3D-печати бетона является сокращение промежуточных этапов, таких как сложное литье и отверждение.
В альтернативном подходе пенобетон может быть получен либо путем добавления пенообразователя к цементному тесту с последующим интенсивным перемешиванием, которое называется методом смешанного вспенивания, либо путем смешивания отдельно полученной пены с цементным тестом, что, как известно как метод предварительного вспенивания [1,4].В отличие от добавления газообразующих химикатов, использование пенообразователей при производстве пенобетона имеет более высокий потенциал для применения в 3D-печати. В основном это объясняется относительной легкостью корректировки свежих и затвердевших свойств путем варьирования сырья и химических добавок [1,2,7,24,26,34].
Смешанный метод вспенивания широко применяется в строительной индустрии для производства пенобетона. Однако этот метод ограничен использованием синтетических пенообразователей и сильно зависит от используемого смесительного устройства.Напротив, метод предварительного вспенивания позволяет определять плотность материала путем точного добавления необходимого количества пены к основной смеси. Поскольку соотношение пены и основного материала может быть больше 1: 1, пена становится основным фактором влияния [35]. Стабильность воздушных пустот во время перекачивания и перемешивания с цементной матрицей важна для обеспечения требуемых характеристик пенобетона в свежем и затвердевшем состояниях. Для пенобетона с синтетическими пенообразователями легче обращаться, они менее подвержены воздействию экстремальных температур и могут храниться дольше.Синтетические пенообразователи можно использовать как в технологиях предварительного вспенивания, так и в технологиях смешанного вспенивания. Более того, они, как правило, менее дороги и требуют значительно меньше энергии для производства высококачественной пены [35]. Тем не менее, синтетические поверхностно-активные вещества не могут соответствовать характеристикам агентов на основе белков из-за их большего размера пузырьков и менее изолированных ячеек, что приводит к более низкой прочности бетона [35,36]. Пены, полученные с использованием пенообразователей на белковой основе, характеризуются меньшим размером пузырьков воздуха, более высокой стабильностью, т.е.е. меньший дренаж воды и более прочная изолированная пузырьковая структура по сравнению с пенами, полученными с помощью синтетических пенообразователей [1,2]. Также сообщалось, что пенобетон, полученный с использованием поверхностно-активных веществ на белковой основе, имеет отношение прочности к плотности от 50% до 100% выше по сравнению с пенобетоном, полученным с использованием синтетического пенообразователя [35,36].
Основываясь на соображениях, упомянутых в отношении характеристик двух существующих поверхностно-активных веществ, в данном исследовании основное внимание уделяется технологии предварительного вспенивания с использованием пенообразователя на белковой основе.показана структура экспериментальной части представленного исследования. Настоящее исследование посвящено получению пригодного для печати пенобетона, который является стабильным и дает адекватные реологические и механические свойства, подходящие для 3D-печати. Составляющие материалы были выбраны специально для достижения достаточной когезии и стабильности формы сразу после нанесения материала печатающей головкой, а также адекватных долгосрочных механических свойств для структурных приложений. Было подготовлено четыре рецепта.Желаемая плотность свежих смесей была указана в пределах 1100–1600 кг / м 3 . Наконец, изоляционные свойства пенобетона для печати сравнивались с изоляционными свойствами обычного бетона для печати (справочный материал описан в [37]).
Обзор экспериментальной программы.
2. Материалы и методы
2.1. Методология проектирования смесей и экспериментальная программа
Схема подхода к проектированию смесей, разработанная в рамках исследовательского проекта CONPrint3D-Ultralight, представлена в.Этот подход также может быть применен к смешанному методу вспенивания. Тогда определение характеристик пены не требуется. Разработка смеси пенобетона с использованием метода предварительного вспенивания разделена на два этапа, а именно: определение состава матрицы на основе цемента и определение количества пены, которое нужно добавить для достижения желаемой плотности. В частности, общий подход к дизайну смеси можно разделить на четыре этапа, как показано на. Итеративная оптимизация используется для получения удовлетворительных композиций пенобетона, пригодных для печати.
Подход к составлению смеси для пенобетона, пригодного для печати.
Во-первых, ограничения, такие как диапазон водоцементного отношения (в / ц) и содержание цемента, должны быть установлены в соответствии с предполагаемым применением. На основании информации из литературы можно определить подходящие пропорции и материалы. Производство и характеристики пены приведены ниже. Целью этого этапа является получение достаточно стабильной пены, способной выдержать процесс перемешивания. Параллельно с этим путем итеративного тестирования определяются водопотребление и вяжущий состав матрицы на основе цемента, включая дозировку суперпластификатора (SP).Обрабатываемость оценивалась путем измерения значений диаметра распределенного потока в соответствии с европейским стандартом DIN EN 1015-3: 1998 и, таким образом, с использованием так называемого конуса Хэгермана и применения 15 ходов [38]. На первом этапе цель этой процедуры состоит в том, чтобы получить матрицу на основе цемента с минимальным количеством воды, но этого достаточно для пластификации матрицы с рекомендованной дозировкой SP. В то же время матрица на основе цемента должна быть достаточно текучей, чтобы обеспечить хорошее включение пены в смесь.Чрезмерно жесткая матрица на основе цемента приводит к разрушению или разрушению пены, в то время как чрезмерно жидкая матрица расслаивается. В этом исследовании первая оценка добавления воды была сделана в соответствии с процедурой, описанной Окамурой и Одзавой [39]. В результате первого шага получается стабильная пена и соответственно жидкая матрица на основе цемента.
Третий этап направлен на проверку реологических свойств свежего пенобетона, которые должны соответствовать требованиям процесса 3D-печати по пригодности для печати, экструдируемости и сборке [39,40,41,42].Состав связующего можно регулировать для достижения требуемых свойств, включая использование дополнительных химических добавок и дальнейшую оптимизацию пены.
Последний этап определяет испытания свойств пенобетона в затвердевшем состоянии, таких как его прочность на сжатие и изгиб, теплопроводность и / или долговечность. На этой стадии отношение воды к связующему (вес / вес) может быть уменьшено; в качестве альтернативы может быть введено усиление в виде диспергированных нановолокон или микроволокон [1,3,43].Представленный подход был использован в данном исследовании для разработки пенобетонов с различной плотностью путем изменения их состава и режимов перемешивания. Реологические свойства в свежем состоянии и механические свойства в затвердевшем состоянии — по схеме, приведенной в — были испытаны, и их результаты представлены в разделе 3.
2.2. Определение потребности в воде
Важно указать подходящее содержание воды в пенобетоне. Стандартной процедуры не существует, особенно когда должны быть выполнены требования по пригодности для печати, прокачиваемости и наращиванию.В настоящей работе водопотребление цементной матрицы определялось методом Окамуры и Одзавы [39]. Состав испытанных порошков приведен в.
Таблица 1
Композиции связующего, испытанные в соответствии с процедурой Окамуры.
Связующее | Тип цемента | Состав по объему [зола-унос: цемент] | Соотношение золы-уноса [по массе] |
---|---|---|---|
A-0 | CEM II | : 1000.00 | |
A-1 | CEM II | 40:60 | 0,47 |
2.3. Сырье
Использовали композитный портландцемент типа II CEM II / A-M (S-LL) 52,5 R (OPTERRA Zement GmbH, Werk Karsdorf, Германия). В качестве вторичного вяжущего материала была выбрана летучая зола каменного угля Steament H-4 (STEAG Power Minerals GmbH, Динслакен, Германия). Химический состав и измеренный гранулометрический состав представлены соответственно в и.Хотя химический состав был взят из таблиц данных поставщиков материалов, распределение частиц по размерам было оценено с помощью лазерной дифракции (LS 13320, Beckman Coulter, Крефельд, Германия). Летучая зола соответствует стандарту DIN EN 450 [44] и может использоваться в качестве добавки к бетону в соответствии с DIN EN 206-1 [45]. Таким образом, он был принят как полученный в данном исследовании и не охарактеризован далее. Второстепенные составляющие показаны, тогда как значения для основных составляющих SiO 2 и Al 2 O 3 не приводятся.Внедрение летучей золы в состав бетона, с одной стороны, позволило снизить водопотребность сухих компонентов при сохранении заданного реологического поведения; с другой стороны, это улучшило устойчивость смесей. SP на основе поликарбоксилатного эфира (PCE) (MasterGlenium SKY 593, BASF Construction Solutions GmbH, Тростберг, Германия) использовали в матрице на основе цемента для регулирования удобоукладываемости при пониженном содержании воды. Содержание воды в СП составляло 77% по массе.Плотность СП составила 1050 кг / м 3 3 . Для производства пены использовали пенообразователь на белковой основе (Oxal PLB6, MC-Bauchemie GmbH & Co. KG, Боттроп, Германия).
Гранулометрический состав твердых компонентов.
Таблица 2
Химический состав цемента и летучей золы (LOI = потери при возгорании, n.d. = не определено).
Материал | Плотность [г / см 3 ] | Химический состав [% по массе] | ||||||||||||||||||||||||||||||||
---|---|---|---|---|---|---|---|---|---|---|---|---|---|---|---|---|---|---|---|---|---|---|---|---|---|---|---|---|---|---|---|---|---|---|
Остаток | SiO 2 | Al 6334 3 O 2 O 3 | CaO | MgO | SO 3 | K 2 O | Na 2 O | LOI | CO 4 CO 4 2 | CEM II / AM (S-LL) 52.5 R | 3,12 | 0,74 | 20,63 | 5,35 | 2,82 | 60,94 | 2,14 | 3,52 | 1,05 | 0,22 | 0,22 | nd | нет данных | нет данных | нет данных | 3,6 | н.о. | 0,6 | н.о. | 2,9 | 1,8 | н.о. | <0.01 | |
2.4. Процедура смешивания
На предварительном этапе было приготовлено три литра матричной пасты на основе цемента для оценки потребности в воде с использованием тарельчатого смесителя (Hobart NCM20, The Hobart Manufacturing Company Ltd, Лондон, Великобритания, вместимость 5 л). описывает процедуру смешивания.
Таблица 3
Методика смешивания связующей пасты для определения водопотребности порошков.
Время [мин: с] | Скорость [об / мин] | Действие |
---|---|---|
0:00 | 0 | Добавьте воду к твердым частицам |
00: 00–1: | 2500 | Перемешивание на низкой скорости |
1: 00–1: 30 | 5000 | Перемешивание на высокой скорости |
1: 30–3: 00 | 0 | Отдых, в течение этого времени , очистить стены |
3: 00–4: 00 | 5000 | Перемешивание на высокой скорости |
Пенобетон производился с помощью конического многороторного коллоидного смесителя (KNIELE KKM30, Kniele GmbH, Bad Бухау, Германия).Для каждого эксперимента было приготовлено 30 л пенобетона по методике согласно. После смешивания связующей матрицы пошагово добавляли отдельно полученную пену: 40%; затем еще 40% и, наконец, оставшиеся 20% от общего объема пены.
Таблица 4
Порядок перемешивания пенобетона.
Время [мин: с] | Скорость [об / мин] | Действие |
---|---|---|
0:00 | 0 | Добавьте воды к твердым частицам в смесительном баке |
0:00 –2: 00 | 3000 | Перемешивание на высокой скорости |
2: 00–2: 30 | 0 | Проверить смесь на однородность |
2: 30–4: 30 | 3000 | Смешивание на высокой скорости |
4: 30–5: 00 | 0 | Добавление 40% всего объема пены |
5: 00–7: 00 | 1500 | Смешивание матрицы и пены вместе на низкой скорости |
7: 00–8: 00 | 0 | Добавление еще 40% от всего объема пены |
8: 00–10: 00 | 1500 | Смешивание матрицы и пена вместе на низкой скорости |
10: 00–11: 00 | 0 901 26 | Добавление оставшихся 20% от общего объема пены |
11: 00–13: 00 | 1500 | Смешивание матрицы и пены вместе на медленной скорости |
2.5. Процесс 3D-печати
Эксперименты по экструзии и осаждению проводились с использованием двух устройств: (а) автономный винтовой насос (PCP1) DURAPACT DP 326S (DURAPACT Gesellschaft für Faserbetontechnologie mbH, Хаан, Германия) и (б) 3D-бетон. испытательное устройство для печати (3DPTD, устройство для 3D-печати по индивидуальному заказу, разработанное TU Dresden, Дрезден, Германия), оснащенное PCP2; видеть . Использовалась труба диаметром 25 мм, а выход из сопла устанавливался вручную для нанесения бетонных слоев.На рисунке b выходное отверстие сопла расположено автономно с помощью предварительно запрограммированного сценария Lua, который является языком программирования. При использовании PCP1 скорость откачки была установлена на уровне 10 л / мин, а выходное отверстие сопла имело круглое поперечное сечение диаметром 20 мм. Эксперименты по печати с использованием специально разработанного 3DPTD были выполнены с двумя различными прямоугольными геометриями сопла 10 мм на 50 мм и 20 мм на 30 мм, чтобы исследовать влияние этого параметра на печатные характеристики пенобетона. Скорость печати 40 мм / с была выбрана на основании предварительных исследований экструдируемости.Были изготовлены образцы с прямыми стенками длиной 700 мм с интервалом времени послойного напыления 30 с. Чтобы оценить способность к наращиванию состава смеси, было нанесено максимальное количество слоев, один поверх другого, до тех пор, пока не произошло саморазрушение. Кроме того, стены, состоящие всего из трех слоев, были напечатаны и в конечном итоге использовались при подготовке образцов для механических испытаний.
( a ) Автономный винтовой насос (PCP), DUROPACT DP 326S и ( b ) устройство для тестирования 3D-печати бетона (3DPTD).
2.6. Подготовка образца
Каждая напечатанная стена была перенесена в климатическую камеру в возрасте 24 часов и отверждена при постоянной температуре 20 ° C, относительной влажности 65% и при отсутствии ветра в течение 27 дней. Эта процедура специально не соответствует стандарту DIN EN 12390-2 [46], который предписывает совсем другие условия отверждения, а именно влажное отверждение. Поскольку в 3D-печати бетона не используется опалубка, а практические варианты отверждения очень ограничены из-за особенностей процесса печати, авторы решили использовать стандартный лабораторный климат на протяжении всей экспериментальной программы, включая подготовку бетона, 3D-печать, отверждение и т. Д. и тестирование.Такие климатические условия лучше всего представляют перспективную экспозицию крупногабаритных печатных элементов конструкций в практике строительства. В возрасте шести дней стены распилили, чтобы изготовить образцы для механических испытаний. Пиление происходило без добавления воды, чтобы избежать впитывания; затем образцы были возвращены в климатическую камеру. Кубики с длиной кромки 40 мм были подготовлены для испытаний на прочность на сжатие, тогда как размеры образцов для испытаний на изгиб варьировались в диапазоне от 30 до 33 мм в ширину и от 50 до 56 мм в высоту, что соответствует размеру трех отпечатанных слои.Неровные боковые поверхности слоев не шлифовали. Длина балочных образцов 160 мм. Погрузочная площадка была равномерно закалена быстротвердеющим гипсом.
2.7. Механические испытания
показывает установки для испытаний на изгиб и сжатие. Испытания на изгиб проводились под контролем поперечного смещения со скоростью смещения 0,5 мм / мин. Для измерения прочности на сжатие загрузочные плиты испытательной установки были 40 мм на 40 мм в соответствии с поперечным сечением кубов.Для каждого материала было испытано не менее трех образцов.
Измерение механических свойств напечатанных образцов: ( a ) испытание на трехточечный изгиб (Zwick 1445, ZwickRoell GmbH & Co. KG, Ульм, Германия), ( b ) испытание на одноосное сжатие (EU20, VEB Werkstoffprüfmaschinen, Лейпциг, Германия).
2,8. Измерения теплопроводности
Образцы размером 70 × 70 × 20 мм 3 были вырезаны из стен, напечатанных таким же образом, как и для механических испытаний.Изоляционные свойства оптимального состава смеси были измерены с помощью анализатора теплопередачи ISOMET 2104 (Applied Precision Ltd, Братислава, Словакия). В этом приборе применяется метод динамического измерения, который позволяет сократить период измерения теплопроводности до 10–16 минут.
2.9. Сканирующая электронная микроскопия и световая микроскопия
Сканирующая электронная микроскопия (SEM) использовалась для визуализации микроструктуры пенобетона. Устройство для сканирующего электронного микроскопа Quanta 250 FEG (Thermo Fisher Scientific, Уолтем, Массачусетс, США) работало в так называемом «режиме низкого вакуума», в результате чего непроводящие образцы отображались в том виде, в каком они были получены без напыления.
Пористая структура пенобетона состоит из пор геля, капиллярных пор, а также захваченных и захваченных воздушных пустот [3]. Гелевые и капиллярные поры не оценивались, потому что эти свойства матрицы на основе цемента не считались существенными в данном исследовании. Между тем, оценивались только захваченные и захваченные воздушные пустоты диаметром более 0,01 мм. Размеры воздушных пустот в пенобетоне изучали с помощью цифрового микроскопа VHX 6000 (Keyence Deutschland GmbH, Ной-Изенбург, Германия) с инструментом анализа изображений высокого разрешения.Метод SEM не позволяет захватить большую площадь, а требует длительных последовательностей изображений и сшивания изображений. Напротив, цифровой световой микроскоп позволил гораздо проще генерировать обзорные изображения богатой порами микроструктуры с наиболее подходящей степенью разрешения. Образцы измерений теплопроводности использовались в дальнейшем для измерения пористости. Их обрабатывали в три этапа: (1) шлифовка наблюдаемой поверхности наждачной бумагой разной степени тяжести, (2) окрашивание выглаженной поверхности черным фломастером и 3) заполнение протянутых пор порошком контрастного цвета ( белый BaSO 4 ).Эта часть подготовки образца соответствует стандарту DIN EN 480-11: 2005 [47]. Для оценки рассматривалась площадь 1905,0 мм². После того, как поры были заполнены и контраст между порами и остальной поверхностью был заархивирован, было создано двоичное изображение, состоящее из двух (случайных) цветов. показывает типичную последовательность обработки изображений.
Типичное исходное изображение и последовательность обработанных изображений пенобетона: ( a ) полированный образец, ( b ) цветное изображение, ( c ) двоичное изображение, обработанное для вычислительных измерений параметров воздушной полости.
Производство пеноблоков — Машины для пенобетона
Давно известно, что изготовление пеноблоков своими руками намного выгоднее, чем покупать готовые блоки из пенобетона.
Производство пеноблоков своими руками: почему
Сегодня на рынках стройматериалов можно найти легкие пеноблоки по очень разной цене. И зачастую качество этих блоков не всегда зависит от цены.Цена на пеноблоки может зависеть от многих факторов. И не всегда можно четко определить для себя, по каким критериям выбрать пеноблоки. Именно поэтому возникает идея, о возможности изготовления пеноблоков своими руками нужных размеров и плотности. На практике, если рассчитать стоимость самостоятельного изготовления пеноблоков, расчет выглядит очень привлекательно. Именно поэтому опытные строители предпочитают делать пеноблоки своими руками.
Изготовление блоков CLC своими руками: цены
Для производства 1 кубометра пенобетона плотностью D600 на наших заводах необходимы следующие материалы:
- 300 кг цемента
- 300 кг песка
- 210 литров воды
- 600 г пенообразователя
- пластификатор УП-2
- Электроэнергия для работы завода по производству пенобетона
По состоянию на 27 сентября , 2016 г. средняя стоимость 1 кубометра пенобетона в России составляет от 1700 до 1900 рублей.Если увидите где-то более оптимистичные цифры — не верьте. Скорее всего, это уловка, чтобы купить что-то для производства пенобетона. Фактически, вы можете встретить меньшие цифры, если у вас есть опыт и / или доступ к материалам по сниженным ценам, но это не средние цифры. В любом случае, если вы собираетесь делать пеноблоки своими руками, то 90% стоимости составляет стоимость цемента.
Для изготовления пеноблоков своими руками потребуется: оборудование для пенобетона, компрессор воздушный, форма для блоков clc.
Производство пенобетонных блоков своими руками: Советы
Если вы серьезно относитесь к тому, чтобы начать делать пеноблоки своими руками, то не пренебрегайте некоторыми советами:
Строгое соблюдение рецептуры, рекомендованной производителем оборудования. Любой уважающий себя производитель выставленных на продажу пенобетонных машин обязательно предоставит вам рецепты смесей. Мы делаем это бесплатно. Приобретая наше оборудование, вы также получаете рецепты производства пенобетона.Чтобы избежать лишних затрат и не тратить время зря, не стоит экспериментировать и что-то придумывать. Рецепты проверены годами. Некоторые новички, пытаясь сэкономить на цементе, стараются уменьшить его количество в смеси. Не стоит этого делать.
Соответствие условиям эксплуатации оборудования. Особого внимания заслуживает электроснабжение установок по производству пенобетона. Если напряжение в вашей сети низкое, установка может не запуститься.Или даже может сгореть пусковая обмотка электродвигателя. Обычно это происходит, когда начинающий строитель пытается начать установку, подключив ее через множество удлинителей или проводов с небольшим сечением, которое не соответствует рекомендациям производителя.
ВО ИЗБЕЖАНИЕ ПРОБЛЕМ ВНИМАТЕЛЬНО ПРОЧИТАЙТЕ ПАСПОРТ ОБОРУДОВАНИЯ ДЛЯ ПРОИЗВОДСТВА ПЕНОБЕТОНА!
Анализ и оптимизация процессов производства пенобетона с помощью программного обеспечения для моделирования — AnyLogic Simulation Software
Problem
Вновь построенный завод по производству пенобетона СЕТ-Холдинга в Орловской области не вышел на проектную мощность.Руководство завода обвинило в низкой производительности человеческий фактор: производственная технология была инновационной и сложной для сотрудников завода. СЕТ-Холдинг нанял консультантов для анализа ситуации и увеличения производственных мощностей. Консультанты решили построить имитационную модель завода с помощью программного обеспечения AnyLogic.
Решение
Имитационная модель оптимизации производства, построенная с помощью AnyLogic (нажмите, чтобы увеличить)
Имитационная модель детально имитирует процессы производства пенобетона, включая приготовление смеси, заливку смеси, резку, разделение, автоклавирование, разгрузку, перемещение тележек, кранов, рабочих и поддонов.Необходимые параметры были загружены в модель из внешней базы данных, в которой хранятся результаты измерений длительности операций: для каждой операции есть диапазон результатов и возможности выбора из заданных значений.
Также демонстрировалась модель:
- Заполненность бункеров сырьем
- Время работы и простой мельниц
- Хранилище
- Состояние автоклавов
Состояние оборудования завода представлено отдельными графиками, которые помогают пользователю визуально оценить соотношение времени работы оборудования и времени простоя.
Имитационная модель позволяла отслеживать различные параметры производительности предприятия: процент используемых ресурсов (использование линий резки и пресс-форм, длина очереди для разделения и количество используемых поддонов), ежедневная статистика количества готовых массовых сжатий (разделенных и разобранных) ), состояние всех разливаемых форм и количество неработающих форм. Кроме того, с помощью графиков можно отслеживать тенденции производительности и уровень использования форм.
Результат
Имитационная модель производственного процесса, построенная с помощью AnyLogic (нажмите, чтобы увеличить)
Разработанная модель позволила руководству завода детально рассмотреть деятельность предприятия.Модель точно моделировала все производственные процессы и поэтому идеально подходила для анализа проблем, принятия решений и прогнозирования изменений.
Имитационная модель производства позволила руководству увидеть картину работы цеха и предвидеть ход событий в случае различных поломок и нештатных ситуаций.