Изготовление обуви своими руками — ручное производство
Обувь ручной работы пользуется большим спросом благодаря качеству и долговечности – обычно производство обуви ручной работы основано на натуральных материалах, требует более высокие требования к качеству готовой продукции. Соответственно, цена на обувь, сшитую вручную, будет выше в сравнении с изделиями, сшитыми на автоматизированном производстве.
Фирмы обуви ручного производства
Даже в век максимальной автоматизации обувь, изготовленная вручную, не является чем-то диковинным. Классические английские производства, которые высоко ценятся во всем мире:
- Crockett&Jones;
- Loake;
- Grenson;
Они выпускают обувь из натуральной кожи и замши, сшитую на ручном производстве. Этапов производства при этом значительно больше, чем при массовом автоматизированном изготовлении. Пара может изготавливаться в течение месяца, в зависимости от типа материала и сложности формы.
Что касается форм и конструкций, наиболее популярными ботинками в ручном исполнении являются:
- Оксфорды;
- Дерби.
Они отличаются по типу шнуровки. Оксфорды имеют закрытую шнуровку, скрытую передней частью ботинка. Боковые части пришивают клинообразно, возможна перфорация.
Дерби же, напротив, имеют открытую шнуровку, а боковые части нашивают поверх передней части таким образом, чтобы при развязывании шнуровки ботинок свободно расходился. Дерби также может иметь перфорацию и считается наиболее универсальной обувью для любого случая.
Особенности конструкции
Всю структуру обуви разделяют на верхнюю и нижнюю часть. В составе верхней части состоят такие элементы:
- Носок – закрывает пальцы ног, выдерживает наибольшие механические нагрузки при носке.
- Союзка – закрывает тыльную часть стопы и соединяет носок, язычок и берцы.
- Берцы – закрывают голеностопный сустав, их пришивают к союзке.
- Люверс – верхняя часть обуви, предназначенная для отверстий или крючков шнуровки.
- Задник – защищает пятку и стопу, фиксирует пятку, изготавливается из жесткой кожи.
- Язычок – покрывает верхнюю часть ступни, пришивается к союзке.
- Стелька – соединяет верхнюю и нижнюю части.
В составе нижней части изделия:
- Подошва – сшивается по контуру с верхней частью, делится на подметки, геленок, рант и наполнитель.
- Каблук – приподнимает пятку и крепится к подошве, верхний слой может быть каучуковым.
- Набойка – защищает каблук от протирания.
- Рант – связующий элемент между деталями.
- Защитные вставки – предотвращают истирание нижнего слоя каблука.
- Наполнитель – заполняет пространство под стелькой, повышает комфорт при эксплуатации.
- Супинатор – деревянная или металлическая деталь, закрепляемая между подошвой и стелькой.

Особенности конструкции
Знание конструкции обуви позволяет изготовить каждую деталь более качественно, в соответствии с ее предназначением.
Этапы изготовления
Для изготовления обуви своими руками понадобится немало времени, но сам процесс несложный и зависит, в основном, от правильности замеров и качества исходных материалов. Весь процесс можно разделить на девять этапов.
Снятие мерок
Без этого этапа не обходится пошив обуви по индивидуальному заказу, то же касается и одежды. Снятие мерок осуществляется, главным образом, для замера параметров будущей колодки.
Создание макета
Подготовив по меркам колодку, шьют предварительный макет. Для его создания шьют по готовой колодке из тонкой натуральной кожи. Здесь же следует определиться, какой вид будет у модели, как располагаются швы, имеется ли рисунок или перфорация.
Подготовка выкройки
Заготовка для будущей пары ботинок вырезается из листа натуральной замши или кожи. Важно оставлять небольшой попуск на сжатие и шов – строго по контуру замеров вырезать нельзя, иначе обувь будет мала как минимум на размер.
Стадия обметки
Сшитые по выкройкам верхние части будущей пары ботинок соединяют вместе. Это трудоемкая часть работы, поскольку при обметке верхней части ботинок может потребоваться обтачивание кожи, подравнивание края, его подкрашивание.
Натягивание заготовки
На этом этапе уже готова колодка для будущей пары ботинок, а также верхняя ее часть. Теперь эту верхнюю часть в прямом смысле натягивают встык на ранее подготовленную колодку. На этом этапе наиболее важным шагом является укладка стельки, так как от правильности ее укладки зависит удобство при эксплуатации обуви.
Нашивка ранта
Рантом называют тонкую кожаную полоску, соединяющую все части ботинка, уже натянутые на колодку. Это изобретение принадлежит Чарльзу Гудиеру – благодаря его технологии, обувь может быть расшита по местам соединения рантом и починена в случае, например, потрескавшейся колодки, подошвы.
Пришивание подошвы
Подошва может быть выполнена из разных материалов – их следует заранее уточнить у заказчика, подсказав ему наиболее подходящий вариант к желаемой паре. Часто делают кожаные или каучуковые подошвы.
Пришитые подошвы укрепляются небольшими гвоздиками – мастера используют их для прямоты и надежности каблука. Последний набирают из толстой кожи в несколько слоев.
Окрашивание подошвы
После пришивания подошвы и набивания каблука необходимо окрасить их необходимым цветом – выбор цвета зависит от тона ботинок. При подсыхании нанесенной краски, подушка полируется для нанесения фирменной маркировки мастера.
Полирование
Ручное изготовление ботинок заканчивается самым важным этапом – полированием и доведением до идеального состояния готовой пары. После полирования получается ровная, упругая, идеально вычищенная пара с прочными соединениями.
Видео по теме: Индивидуальный пошив обуви Головань
Производство обуви: оборудование, материалы и технология
Обувь всегда является востребованным товаром среди населения, поэтому обувная промышленность является популярной отраслью бизнеса. В современное время на рынке представлено много моделей данной продукции различных производителей и фабрик.
Мировая конкуренция
На сегодняшний день многие покупатели желают иметь не только качественную и практичную обувь, но и соответствующую модным тенденциям. Среди экспертов данной сферы деятельности замечено, что доходы российских фабрик и спрос на продукцию, напрямую зависят от иностранных производителей.
Обувная промышленность хорошо развита в Китае. С одной стороны, продукция из Китая славится невысокой ценой, однако, плохим качеством. С другой стороны, существует немало известных европейских брендов с продукцией высокого качества, и соответственно, завышенной стоимостью.
Из-за быстрого повышения цен на импортную продукцию и некачественного товара и Китая, все больше покупателей начинают отдавать предпочтение отечественному производителю. Поэтому многие предприниматели задумываются об открытии фабрики по производству обуви.
Чтобы потеснить китайских производителей и соперничать с европейскими поставщиками, необходимо выпустить дизайнерский модельный ряд с какой-либо изюминкой.
Технология производства обуви в промышленных масштабах осуществляется в несколько этапов:
- Проектирование и создание моделей обувного ряда с разработкой всей необходимой документации.
- Производство обуви и сбыт партий.
Технология пошива
Предварительно материалы, используемые в производстве, необходимо:
- тщательно проверить на соответствие качественным характеристикам;
- отсортировать в производственные партии;
- направить в раскройный цех.
Первым делом дизайнерами-специалистами разрабатывается дизайн и внешний вид будущей модели, создается эскиз, выполняется заготовка.
Для создания производства по пошиву обуви необходимы соответствующие материалы, одни из них являются основными, другие – вспомогательными.
Основные материалы применяются для изготовления наружных, внутренних и промежуточных элементов верхних и нижних частей изделия:
- разные виды кожи;
- меха;
- текстильные материалы.
К вспомогательным материалам относятся детали, предназначенные для отделки и украшения моделей:
- различная обувная фурнитура;
- текстильно-галантерейные изделия;
- клей.
Таким образом, для изготовления обуви существует достаточно большой выбор материалов. Однако, самый лучший из них – натуральная кожа.
Помимо натурального сырья, в последнее время все чаще применяются синтетические материалы для производства обуви, которые значительно дешевле. Однако, многие из них не только дешевле, но часто и практичнее природных аналогов.
Раскройный цех
Именно в раскройном цеху выполняется создание эскиза обуви, моделирование изделия и раскрой деталей.
Из заранее подготовленного материала изготавливаются составные части обуви, для получения которых предназначены два специальных вырубочных пресса:
- один – для работы с верхними деталями;
- второй – для нижних деталей изделия.
Некоторые части обуви вырезаются вручную при помощи трафарета.
Пошивочный участок
Верх обуви изготавливается отдельно от подошвы и включает в себя следующие детали:
- Переднюю часть изделия – носок;
- Среднюю часть изделия – союзку;
- Часть, фиксирующую верх ноги – язычок;
- Заднюю часть изделия, фиксирующую пятку – задник.
Необходимое оборудование
Перед тем как сшивать детали, необходимо каждую часть истончить, чтобы швы были ровными и аккуратными. В пошивочном цехе выполняется сшивание подготовленных деталей. Необходимо следующее оборудование для производства обуви:
- Швейные машины;
- Пошивочный конвейер;
- Машина для вставки подносков;
- Машина для загибки краев и разглаживания швов;
- Машина для формовки кожаных нашивок на носок обуви.
Технология крепления подошвы
Подошва крепится к верху обуви разными способами:
- Клеевым;
- Прошивным;
- Комбинированным;
- Вулканизацией.
Клеевой способ популярен, поскольку надежен и недорогой в выполнении. При правильном выполнении технологии склейки, вероятность проникновения влаги между верхом и подошвой практически невозможна. Однако, при склеивании некачественным клеем или с нарушением правил крепления, обувь может быстро развалиться.
Прошивной способ крепления подошвы к верху обуви недостаточно практичен к проникновению влаги, также высокая вероятность повреждения прошивной нити.
Комбинированный метод предполагает использование клеевого и прошивного способов.
Вулканизация – части изделия (верх и низ) практически свариваются в одно целое. Используя такой способ, вероятность отсоединения подошвы от верха практически исключается. Недостаток у данного способа один – ограниченность в выборе материалов.
Пошив внутренней части
Внутренняя часть обуви подшивается подкладкой, которая может быть выполнена из следующих материалов:
- кожаная;
- текстильная;
- из искусственных материалов;
- комбинированная из разных материалов;
- шерстяная на тканой основе;
- из натурального меха на кожаной основе.
От качества выполнения соединения деталей зависит качество будущей модели.
Соединение частей изделия
Способ скрепления верхних и нижних частей обуви отвечает за многие эксплуатационные характеристики:
- гибкость;
- легкость;
- износостойкость.

Гибкость обуви
После того как верх изделия будет готов, он натягивается на колодку и с нижней ее стороны закрепляется со стелькой. Этот процесс называется – «затяжка». На этом этапе в носок и задник будущей обуви устанавливаются формовочные элементы:
- в носок – подносок;
- в задник – усилитель жесткости в виде пластиковой пластины или дополнительных слоев кожи.
Колодки могут быть выполнены по-разному, в зависимости от будущей модели. Они могут быть в следующем выполнении:
- цельные;
- раздвижные;
- сочлененные;
- с выпиленным клином.
Фасон колодки зависит от тенденций моды, поскольку это является основной технической характеристикой, от которой зависит вид будущей изготовленной модели.
Производство стелек
Внутрь готового изделия вкладываются стельки. Стельки могут быть выполнены из разного сырья. Материал, из которого изготавливается стельки, должен быть качественным, поскольку именно он будет впоследствии соприкасаться с ногой человека. Стелька может быть выполнена из влагостойкого картона или синтетического нетканого материала.
Для изготовления обувных стелек выбранная ткань прессуется на специальном оборудовании. Затем машиной для шлифовки обрабатываются края и промазываются специальным клеем, после чего проходят еще одну прессовку.
Стельки к модели можно приобретать отдельно, исходя из потребностей, это могут быть:
- утепленные стельки;
- ортопедические;
- другие варианты.
Заключительный этап
Изготовление обуви после крепления подошва завершается окончательной отделкой изделия:
- необходимо отрезать излишки материала;
- вклеить мягкие подпяточники;
- вложить стельки;
- сформировать голенища.
Завершающим этапом является обработка готового изделия при помощи специальных покрытий:
- восков;
- спреев;
- кремов.
При необходимости выполняется вставка шнурков, крючков и других аксессуаров и фурнитуры.
Готовая продукция поступает в отдел проверки качества, где сортируется, маркируется, упаковывается попарно и группируется по партиям для сбыта.
Организация бизнеса
Если хорошо ознакомиться с данной отраслью, обувная промышленность может стать прибыльным доходом. Необходимо ознакомиться со всеми нюансами производства, пошива обуви, выбора материалов и оборудования, а также соблюдать ряд последовательно выполняемых операций и действий.
Для организации бизнеса в сфере производства обуви необходимо выполнение следующих пунктов:
- приобретение производственного помещения с необходимым оборудованием;
- приобретение материалов;
- сертификация и декларация продукции;
- договора по сбыту готовой продукции.
Перед тем как закупать материалы и оборудование, стоит определиться со стилем будущих коллекций. Формат изделий может быть разный – производство классической кожаной обуви, резиновые или спортивные модели. Кроме того, можно выбрать одно направление продукции: либо производство мужской обуви, либо производство женской обуви. Очень прибыльна и востребована среди покупателей детская продукция.
Следует учитывать и сезонные периоды. Как правило, сезон начинается с осени и идет до весны следующего года. В летнее время:
- пересматривается ассортимент;
- разрабатываются новые модели;
- обновляется оборудование.
Следует учитывать также, что одной из больших проблем и трудностей обувного производства, является отсутствие качественного отечественного сырья для производства обуви. Поэтому, изделия, которые производятся в нашей стране, почти наполовину состоит из импортных материалов.
Таким образом, обувная промышленность России не является сильной стороной нашей страны и уступает в объемах производимой продукции многим странам.
В заключение
Если иметь оригинальную идею, которая позволит выделить коллекцию на фоне конкурентов, а также учитывать потребности и пожелания покупателей, обувная промышленность может стать прибыльным производством.
Видео по теме: Производство обуви
Обувная промышленность — Википедия
Материал из Википедии — свободной энциклопедии
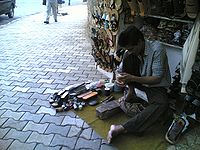
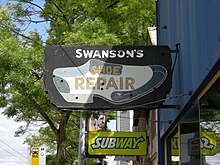
Обувная промышленность — традиционное ремесло, уходящее корнями вглубь веков и представляющее собой искусство изготовления обуви различных назначений и видов. В настоящее время ручное изготовление обуви сапожниками или башмачниками постепенно исчезает, вытесняясь индустриальным производством обуви посредством станков и операционных линий. Также исчезает кустарный, одиночный способ производства обуви, уступая место крупным компаниям-производителям.
Изготовители обуви производят большой круг различных обувных изделий, включая ботинки, туфли, полуботинки, сандалии, мокасины и сабо.
Предметы промышленности традиционно изготовляются из таких материалов, как кожа, дерево, резина, пластик, джут или другие подобные материалы, и часто состоят из множественных частей для лучшего противостояния соли, могущей повредить верхнюю основу из кожи.
Большинство сапожников используют колодки, сделанные из дерева или металла, но, в последнее время, часто материалом для колодки служит пластик. Некоторые колодки являются прямыми, в то время как другие различаются — одна для левой ноги, другая — для правой.
Профессия сапожника породила множество явлений современной культуры, например, поговорку «Сапожник без сапог» (описывающую ситуацию, когда профессионал в какой-то области напрасно не пользуется собственным умением в личных целях). Сапожниками также называют мастеров по ремонту обуви.
«Международный день сапожника» отмечается 26 ноября[1].
Некоторые варианты старых и традиционно изготовляемых видов обуви:
- Меховые полосы, обмотанные вокруг ноги, и сандалии, надетые поверх них: такую обувь часто использовали древние римляне, находящиеся на военной службе на форпостах в северной Европе.
- Сабо: деревянные ботинки, часто набиваемые соломой для обогрева ноги.
- Мокасины: простые туфли, часто без твёрдой подошвы внизу, изготовляемые индейцами Северной Америки из выделанной кожи животных. Современной промышленностью выпускается лёгкая обувь с таким же названием, напоминающая некоторые традиционные мокасины по внешнему виду, но сделанная по другой технологии.
- Рант — несущая деталь обуви
- Жёсткий подносок — промежуточная деталь верха
- Союзка — наружная деталь верха обуви
- Берцы — наружные детали верха, закрывающие тыл стопы
- Подкладка — внутренняя деталь верха обуви
- Жёсткий задник — упрочняющая деталь
- Запятник — кожаная деталь изнутри на заднике («карман» на сленге сапожников)
- Подошва — деталь низа обуви
- Стелька — подкладочная часть
- Геленок (супинатор) — деревянная или стальная пружина, поддерживает свод стопы.
- Каблук — возвышающая пяточная часть
- Голенища — верхняя часть сапог закрывающая голень
Эти видеотрывки показывают создание обуви по шагам:
- Первые шаги в процессе изготовления обуви на видео (англ.)
- следующие шаги изготовления обуви на видео (англ.)
- изготовление обуви. видео. часть 3 (англ.)
- изготовление обуви. видео. часть 4 (англ.)
- изготовление обуви. видео. часть 5 (англ.)
- изготовление обуви. видео. часть 6 (англ.)
Пошив обуви вручную: vizioner25 — LiveJournal
В этом посте я расскажу как начиналось и выложу фотоисторию последнего проекта.Когда 2 года назад я решил развивать новое хобби, то столкнулся с несколькими проблемами:
1) на русском языке информации об этом ремесле нет вообще, а если есть то в основном описываются устаревшие методы работы;
2) найти русскоязычных специалистов через интернет практически невозможно, потому что основной массив людей, которые умеют это делать уже приклонного возраста и им не до интернета;
3) купить инструмент вообще проблема, так же как и материал.
Долгие поиски привели меня к нескольким мастерам, с которыми я общаюсь до сих пор. Эти люди активно помогают, да и вообще классные ребята. Средни них — Олег Заремба из Киева, мастер очень высокой категории, его работы просто фантастика!
Здесь можно посмотреть небольшую презентацию работ (фото с fb) http://www.youtube.com/watch?v=YpvZ9kS5Mx4
А в России я общаюсь с Андереем Кавешниковым. Он так же как и я давно загорелся этим делом и весьма преуспевает в нем, правда периодически просит за советы закинуть «пятихатку на мобилку», ну или «соточку» :)) Ну, это юмор конечно у нас такой (Андрюха, не обжиайся). Андрей живет в Москве и часто помогает с покупкой материалов или инструмента. Вот его страничка в вк http://vk.com/id957804
Сейчас круг знакомств расширяется и в принципе становится проще.
В фейсбуке есть хорошее сообщество, где общаются наверно почти все европейские и американские ремесленники.
Во Владивсотоке я нашел хорошего человека и мастера из области ремонта. Вместе с Виктором Ивановичем мы учимся и пробуем новые технологии, спорим и обсуждаем о разных процессах. Вообще повезло, что здесь есть человек, которому тоже интересно. В свое время я зашел почти в каждую мастерскую по ремонту обуви с просьбой помочь — везде приклеили бороду, кроме отелье «Петелька» в центре. Поэтому если вам нужен качественный ремонт обуви — идите туда. Там спец с тридцатилетним опытом работы:)
Вот такая фабула. Далее я покажу фотки с процессами последнего пошива. Я пока учусь и мне далеко до совершенства. Каждая пара — это опыт, ошибки, позитив и работа. Пока не было проектов, которыми я 100% был бы доволен. В процессе описания каких-то процессов у меня могут быть ошибки (это для снобов «мастеров). Просто у меня есть цель в этом направлении и пока не добьюсь ее — не отступлю. Надеюсь, что эти картинки будут интересны новичкам и вообще всем, ведь это ремесло только начинает возрождаться в нашей стране.
Цель была такая — попробовать новый метод сборки, да и фасон «дерби» еще раз попрактиковать, так как Кавешников А. меня постоянно троллит оксвордами 🙂
Метод сборки называет Strom welt, картинка ниже:
В общем, обычно я пользовался верхним способом — когда рант (welt) уходил под затяжную кромку. Сейчас же я хочу оставить его снаружи, пришив де просто строчкой, а декоративной строчкой, так называемой «косичкой» (goiser stich).
Фото косички (не мое, для примера, мое будет ниже):
Итак, процесс пошел:
Делаю лекала
Перфорирую вручну
Исрпользую специальную серебрянную ручку, легко стирается и хорошо видна. Вырезаю ножом
Для зигзага использую ножницы, сейчас ищу меньший размер
Тоже самое делаю с деталями подклада, а справа лежит материал на межподклад, так как кода верха мягковата, нужно уплотнить
Помечаю линии для строчки
Под перфорацию подкладываю кожу, чтобы сохранить цвет
Приклеиваю межподклад и прошиваю детали верха
Клею тесьму, чтобы кант ботинка не растягивался
Далее приклеиваю бизик (точное название не помню 🙂 ), придает хороший вид
Сшиваю детали подклада
Тесьма ставится для того, чтобы клей при затяжке не просачивался сквозь строчку
Прошил берцы к задней части подклада
Примеряю 🙂
Сшиваю оставшиеся части
Нужно сказать, что эта машинка сделана не для машина, а для ремонта обуви — она очень грубая и большая. Поэтому я купил новую супер-секси машинку, которая предназначена для пошива 🙂 ее фото будет ниж.
Вот что получилось
Делаю предварительную затяжку, чтобы наметить место под рисунок на носу
Тем временем пробую плести косичку. Нужно сказать, что на всем видео и фото с косичками используется нить почти в 2 раза толще, чем есть у меня. Так как моя нить тоньше, то пришлось и длину стежка делать меньше, всего 5 мм. И на прошивании ранта время таким образом увеличивается в 2 раза.
Пробую деформировать так, как будет при сборке. Появились морщинки в связи с тем, что рант толстый. Поэтому я его благополучно сузил.
Был 2,5, стал вот такой
Пришло время работать со стелькой
Тем временем заготовка сформовалась и пора делать рисунок на нос, заготовка у меня уже была
Наметил и вручную выбиваю
Получилось вот так
Обязательно подкладку, иначе под перфорацией будет белая подкладка. Некоторые просто подклад красят, но на мой взглдя это не очень.
Продолжаю возиться со стелькой
Вырезал «губу» — это та часть, за готорую будет «цепляться» рант с помощью ниток.
Эластичный бинт помогает сформовать стельку, чтобы она идеально приняла форму следа колодки.
Пока стелька формуется делаею жесткие задники. Вставляются между верхом и подкладом для придания жесткоски и формоустойчивости. Потрогайте свою пару — у вас тоже есть, но скорее всего не из кожи :). В этой паре есть небольшой косяк с высотой задника, обусловлено это сборкой верха. В след раз учту
Проверяю толщину.
Вот все детали для придания формоустойчивости. Белый материал — это термопласт. При нагревании становится мягким, принимая заданную форму (ставится на носок). Так же его называю «пинг-понг», потому что он возвращается назад при нажатии. Очень удобно. Обычно я ставлю кожу на подносок, но пока не определился, что нравистя больше.
Вот так выглядит стелька после бинта — идеально прилегает к колодке
Пришло время готовить рант
Намечаю канавку под стежок с помощью специального грувера
Потом делаю разметку под стежок с помощью этого колесика (расстояние 5 мм)
Это я сравниваю разные варианты, как сделать рант еще и красивым, интересным.
В итоге вот такая штука, но в дальнейшем я использовал зиг-заг (будет видно). Вообще в процесс пошива пары проводишь много экспериментов, это увлекает 🙂
Пришло время затягивать пару и я вставляю жетский задник на свое место — между верхом и подкладом
Тоже самое с остальными деталями
Подтягиваем материал
Фиксируем гвоздями. Может показаться, что это простая операция, но на самом деле одна из самых сложных и долгих.
Получилось вот так
Между делом мне приехала профессиональная швейная машинка для пошива верха обуви Garudan, это было торжество! 🙂ё
Вот такую строчку дает 🙂
Просто шик! Жду следующую пару с нетерпением
А вот как раз установка термопласта на подносок
Вот такой цвет и фасон ранта я решил сделать
Готовлю рант — пробиваю отверстия для стежков
И вырезаю зиг-заг
Начал прошивать
Именно здесь я понял, что рант у меня толстый (2,5) — получаются морщинки на сгибе
Поэтому я сделал новый рант, а старый отпорол. Вот здесь видно, как он крепиться к стельке
Обувь изнутри
Супинатор для поддержания свода стопы + устойчивать (дада, у вас тоже такой есть в ботинке) 🙂
Пробка придает комфорт и эастичность.
А потом клеиться подошва
Подошва вид сверху
Далее делается специальный надрез с торца уреза, кожа отгинается и с помощью этого уникального инструмента делается канавка под строчку, которая сшивает подошву и рант.
Вот так и сшивается
После прошивки кожа заклеивается, таким образом строчка прячется и ей не грозит порыв из-за соприкосновения с землей (асфаль и тд).
Между делом сделал приятно Жене 🙂
После набирается каблук. К сожалению, у меня нет фото процесоов набора фликов, потому что эту черновую работу (со станком) дома я делать не могу, а в мастерской у Виктора как-то не фотографируется (забываешь).
Срезаются лишние участки и боковой урез красится
Обработка уреза для меня самая великая проблема, так как нужна специальная химия и двигатель с возможностью регулирования оборотов. Пока этот процесс у меня приметивен — натираю воском и полирую сукном + катушкой с конским волосом. Вообще у меня есть все необходимые катушки, нет химии (спиртовые грунты и тд) и 800 оборотов в минуту. Но это всего лишь дело времени, как-то так.
Пока не вощеный урез
Решил сделать такую стельку :))))) внутри полустелька из паралончика
Цвет подкала не самый лучший, но Андрей предложил хорошую идею — в следующий раз покрашу кожу
Урез после обработки
Конечный результат
И крупнее
В целом, я доволен результатом. Потратил на это дело около 1,5 месяцев. Буду продолжать выкладывать посты, потому что это позволяет структурировать работу. Помимо этого всем рекомендую вести дневник, где можно записывать всякие спорные моменты, чтобы потом проверить на паре и либо продолжать делать так же, либо не делать никогда :))
Есди вам было интересно — подпсиывайтесь
http://instagram.com/itskov
https://www.facebook.com/sergey.itskov
Из каких материалов делают обувь
Для производства туфель и ботинок используется множество разных материалов. В этой статье мы перечислим все более или менее распространённые варианты, причём расскажем о материалах не только для верха, но и для подкладки, подошв и укрепляющих элементов. Информация о каждом конкретном материале будет краткой, но в ряде случаев вы найдёте ещё и ссылки на подробные статьи о тех или иных видах кожи или подошв, которые мы опубликовали ранее.
Оглавление:
Материалы для верха обуви
Наш обзор используемых для верха обуви материалов мы начнём с перечисления разновидностей кожи.
- Box calf — гладкая телячья кожа типа full-grain (то есть с открытыми порами), равномерно окрашенная на дубильне проникающими красителями (aniline dyes ). Степень выносливости и износостойкости довольно высокая; воздухопроницаемость отличная. Box calf может использоваться и для формальной, и для неформальной обуви.
Монки из кожи box calf Berwick 4140 Burgundy
- Museum calf — гладкая телячья кожа типа full-grain, неравномерно окрашенная на дубильне проникающими красителями. Немного пятнистая, с интересной и неординарной внешностью. Степень выносливости и износостойкости довольно высокая; воздухопроницаемость отличная. Уровень формальности ниже, чем у box calf.
- Crust — гладкая телячья кожа типа full-grain, которую окрашивают только на обувной фабрике. Часто снабжается интересной патиной с цветовыми нюансами и переходами; по-настоящему однотонной не бывает. Степень выносливости ниже, чем у box calf и museum calf, потому что эта кожа более уязвима к обильным воздействиям влаги и реагентов. Долговечность, однако, может быть отличной, равно как и воздухопроницаемость. Уровень формальности варьируется от очень низкого до весьма высокого, хотя и не максимального.
- Pebblegrain, Scotch grain — зернистая телячья или коровья кожа, которую окрашивают на дубильне и дополняют особым принтом под гальку (принт наносят специальным прессом). Иногда эту кожу дополнительно жируют. Степень выносливости высокая. Воздухопроницаемость варьируется — может быть отличной, может быть посредственной. Уровень формальности низкий.
Ботинки чакка из зернистой кожи Berwick 320 Brown
- Oiled, Waxy, Wax calf, Chromex — жированная или вощёная телячья или коровья кожа, окрашенная на дубильне. Отличается очень высокой степенью устойчивости к внешним воздействиям. Воздухопроницаемость варьируется, но она всегда ниже, чем, например, у box calf. Уровень формальности низкий.
- Bookbinder/Polished/Hi-Shine — телячья и коровья кожа с глянцевитой поверхностью и закрытыми порами. Уровень формальности высокий, хотя сегодня такого рода кожу используют и для пошива совершенно неофициальной обуви. Воздухопроницаемость оставляет желать лучшего. Уровень выносливости бывает хорошим, но царапинки и потёрости с такой кожи удалить невозможно; кроме того, на ней могут образоваться сильные заломы, и она бывает жестковатой. Дополнительно заметим, что иногда термин Polished применяется к коже других видов.
- Patent — лакированная кожа. Используется для производства самой официальной обуви, которую носят со смокингами и фраками. Качество довольно сильно варьируется. Воздухопроницаемость обычно оставляет желать лучшего, а иногда она и вовсе нулевая. Чёткого разграничения между patent и bookbinder нет; поры в обоих случаях закрыты, а поверхность блестит, но лакированная кожа обычно более глянцевая, чем кожа bookbinder.
- Cordovan — кожа (или, точнее, мембрана) с конского крупа, которая проходит долгое растительное дубление. Отличается очень высокой прочностью, долговечностью, износостойкостью, но при этом в среднем более дорогая, твёрдая и жёсткая, чем телячья кожа, и к тому же хуже подходит для тёплой и тем более жаркой погоды. Кордован склонен к образованию характерных волнообразных заломов. Он может применяться для производства как строгой, так и неформальной обуви.
Помимо этого, для производства верха обуви могут использовать шкуры крокодилов, змей, страусов, акул, слонов, скатов, ящериц и других экзотических животных. Подробнее о них мы рассказывали в отдельной статье, а тут лишь заметим, что в магазинах часто встречаются туфли из телячьей или коровьей кожи с принтами под экзотику… и что переплачивать за модели из настоящих экзотических шкур, как правило, стоит лишь в том случае, если они действительно вам очень нравятся. Степень универсальности подобной обуви часто оставляет желать лучшего.
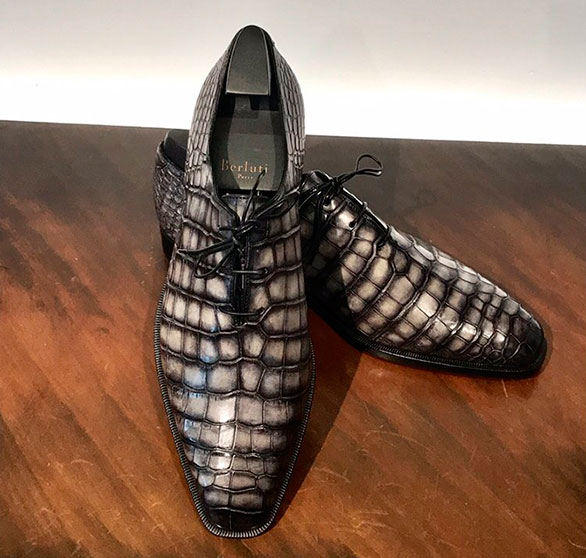
Теперь переходим к краткому обзору ворсистых материалов, получаемых из шкур животных.
- Suede — замша. Есть два основных её вида: full-grain suede (reverse suede) и split suede. Первый вариант ценится заметно выше второго и стоит заметно дороже. Как правило, full-grain замша приятнее на ощупь и благороднее на вид. Долговечность бывает высокой у обоих вариантов. Степень выносливости может быть весьма приличной, если вы обработаете замшу специальной водоотталкивающей пропиткой.
Лоферы из замши Berwick 8491 Brown Suede
Дерби из замши Berwick 5768 Dark Brown Suede
- Nubuck — нубук. Если лицевой стороной замши является «внутренняя» сторона шкуры, то лицевой стороной нубука служит «лицо» шкуры, которое было сильно отшлифовано. Подробно о разнице между замшей и нубуком мы рассказывали в отдельной статье.
- Oiled nubuck — жированный/промасленный нубук. Более устойчив к внешним воздействиям, чем обычный нубук.
Кроме того, иногда верх обуви делается из текстиля — хлопкового, льняного, синтетического или шерстяного (так, вы можете найти модели, частично изготовленные из твида или шерстяной фланели). Степень практичности таких вариантов едва ли можно назвать высокой, и в плане долговечности они обычно тоже уступают хорошей натуральной коже. Особенно часто текстиль применяется для изготовления верха спортивной и домашней обуви. В ряде случае его используют в комбинации с кожей или кожзаменителем.
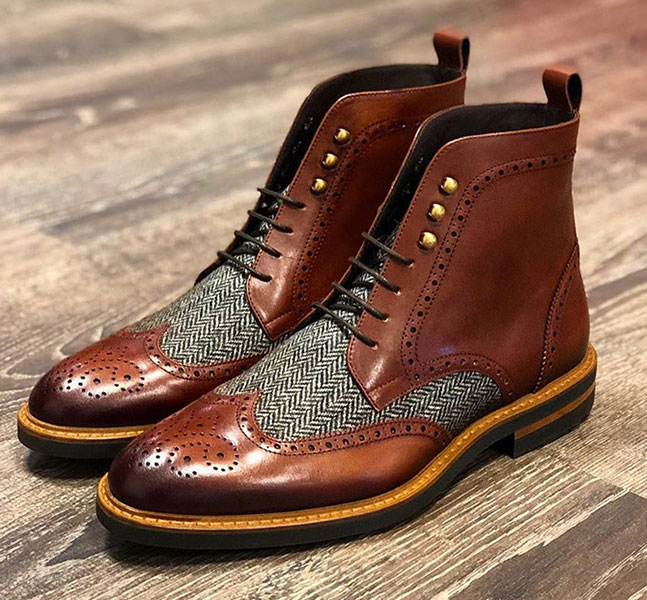
Добавим, что для производства верха некоторых неформальных моделей (например, сланцев) используется резина; помимо этого, некоторые туфли (обычно женские) сегодня снабжаются верхом из пластика. В самом нижнем ценовом сегменте распространены модели с верхом из кожзаменителя, качество которого варьируется в широких пределах. Лучшие образцы кожзаменителя долговечны и способны «дышать», но всё равно ценятся ниже, чем качественная натуральная кожа. Красивую патину они не приобретают.
Под конец нужно упомянуть кирзу — искусственный материал, про который мы подробно рассказывали в статье про кирзовые сапоги. Классическая кирза представляет собой грубоватую бюджетную ткань, пропитанную специальной синтетикой, дополненную принтом под кожу и сохраняющую воздухопроницаемость (хотя и в довольно ограниченных пределах). Современная кирза обычно делается на основе нетканых материалов.
Материалы для подошв
Подошвы классических туфель и ботинок изготавливаются либо из кожи, либо из резины. Кожаные подошвы — самый традиционный выбор; они считаются более строгими, чем их резиновые/синтетические собратья, но в то же время подходят как для официальной, так и для неформальной обуви. Кроме того, кожаные подошвы обладают способностью «дышать», а на полке магазина выглядят благородно и порой очень эффектно. Впрочем, уже после первой носки кожаная подошва обзаводится огромным количеством потёртостей и царапинок.
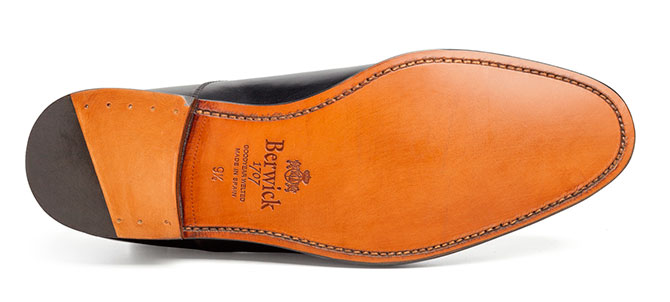
Помимо этого, кожаные подошвы не годятся для ходьбы по скользким поверхностям и весьма уязвимы к воздействию воды — по лужам в обуви с кожаными подошвами гулять точно не стоит. Если вам хочется носить туфли с такими подошвами в дождливую и снежную погоду, на подошвы нужно поставить резиновую профилактику — эту услугу оказывают практически все обувные мастерские, но мы рекомендуем обращаться в самые лучшие и проверенные, с хорошей репутацией. Профилактика не только даёт защиту от влаги, но и предохраняет подошвы от преждевременного износа (впрочем, для предотвращения преждевременного износа самых передних частей подошв лучше подходят специальные металлические накладки-«косячки»).
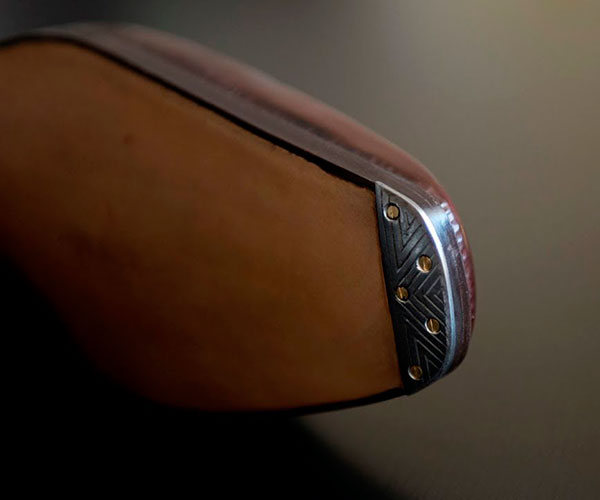
Следует добавить, что в ассортименте некоторых марок встречаются туфли на кожаной подошвой с уже установленной фабричной резиновой профилактикой (иногда, впрочем, с такими моделями можно перепутать туфли с резиновыми подошвами с декоративными кожаными вставками). Кроме того, существуют двойные кожаные подошвы, которые более устойчивы к внешним воздействиям, чем одинарные, смягчают при ходьбе действие камней и обеспечивают большую теплоизоляцию. Стоит упомянуть и кожаные подошвы типа oak bark tanned — знатоки отдают предпочтение именно им, потому что по сравнению с обычными кожаными подошвами они более лёгкие, долговечные и износостойкие. Правда, и стоят они заметно дороже.
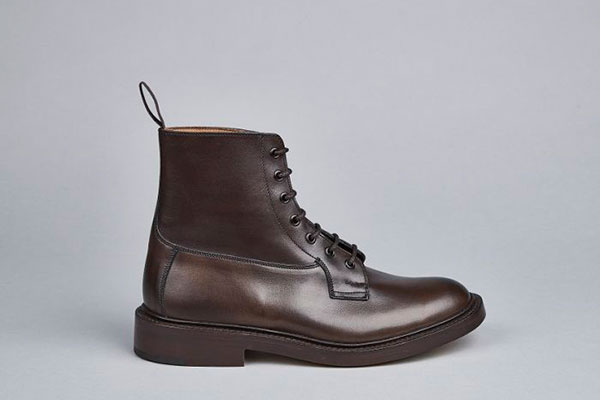
Подробнее о кожаных подошвах в целом мы рассказывали вот тут, а о кожаных подошвах типа oak bark tanned и одном из самых известных их производителей (дубильне J. Rendenbach) — в этом материале. О двойных кожаных подошвах можно почитать здесь.
Резиновые и синтетические подошвы обычно оказываются практичнее кожаных. Они бывают очень разными. И для строгой, и для неформальной обуви отлично подходят подошвы британской марки Dainite, а также очень похожие на них подошвы итальянского бренда Sestriere и соответствующая модель от итальянской компании Vibram. Они достаточно тонкие, износостойкие, простые в уходе; единственным их недостатком можно назвать плохую устойчивость на скользких поверхностях.
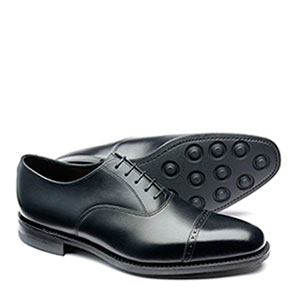
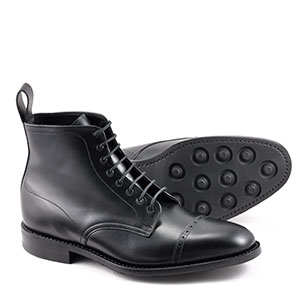
Большей устойчивостью и очень высокой практичностью отличаются подошвы британских брендов Ridgeway, Commando, а также некоторые подошвы Vibram. Внешность у них, однако, менее официальная — так, подошвы Commando точно не стоит сочетать с деловыми костюмами. Креповые подошвы (crepe soles) тоже неофициальны. Как правило, они отличаются лёгкостью и комфортом, но их качество, износостойкость и степень устойчивости на скользких поверхностях заметно варьируются от производителя к производителю.
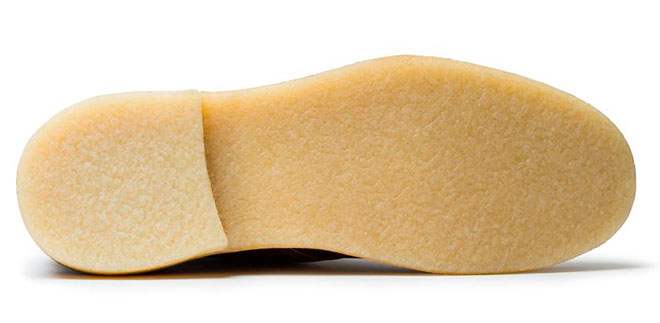
Подробная статья о вариантах подошв для классической мужской обуви доступна вот по этой ссылке. Здесь мы добавим, что масс-маркетные ботинки и туфли часто оснащаются полностью синтетическими подошвами из полиуретана (PU), термполиуретана (TPU), этиленвинилацетата (EVA), поливинилхлорида (ПВХ/PVC) и термоэластопласта (ТЭП/TRP). Полиуретан иногда комбинируют с термополиуретаном. Для зимы хорошо подходят термоэластопласт и термополиуретан. Высокой износостойкостью отличаются полиуретан и термополиуретан, а хорошими амортизирующими свойствами — термоэластопласт, этиленвинилацетат, полиуретан. Гибкостью славятся этиленвинилацетат и термоэластопласт, а также полиуретан (но последний — не на морозе).
Материалы для стелек и внутренних подмёток
Внутренние подмётки (основные стельки) делают из натуральной кожи, кожкартона и картона (genuine leather; leatherboard; cardboard / paperboard). Выше всего ценится кожа, особенно кожа растительного дубления, проходившая уже упоминавшийся выше процесс oak bark tanning. Подмётки из кожкартона в действительно высококачественные туфли не ставят, но это ещё не самый худший вариант. Внутренние подмётки из картона — признак обуви откровенно низкого уровня.
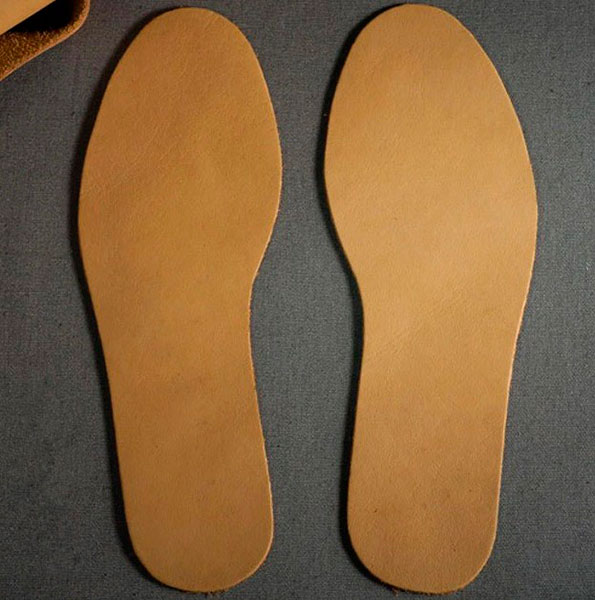
На вкладные стельки обычно идёт натуральная кожа растительного или хромового дубления. Первый вариант является самым лучшим, потому что кожа растительного дубления гипоаллергенна, очень гигроскопична и гигиенична. Важно, чтобы поры кожи вкладных стелек были открытыми, потому что в противном случае стельки будут плохо «дышать» (или вообще не будут). Стельки из синтетических материалов или текстиля являются индикатором обуви невысокого уровня.
Подробно о материалах для вкладных и основных стелек мы рассказывали в отдельной статье.
Материалы для подкладок
Подкладки высококачественных туфель изготавливаются из кожи растительного дубления или из кожи хромового дубления с открытыми порами. Первый вариант обычно ценится несколько выше. Туфли не самого высокого качества могут снабжаться подкладкой из кожи хромового дубления с закрытыми порами, которая не может похвастать гигроскопичностью и плохо «дышит» (а порой и вообще не «дышит»). Естественно, этот вариант менее предпочтителен.
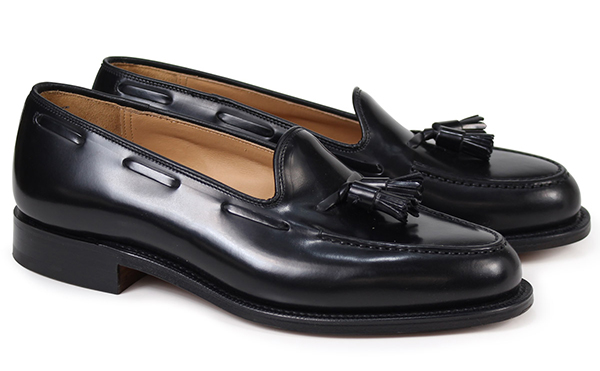
Помимо этого, иногда для подкладок используются натуральный и искусственный мех, а также текстильные материалы: лён, хлопок, синтетика. Текстильные материалы ценятся ниже натуральной кожи, но в то же время льняная подкладка не является индикатором туфель низкого уровня. Синтетика сегодня бывает разной, и высокотехнологичные её варианты могут быть практичными и комфортными, однако в классической мужской обуви использовать синтетику не принято. Мех применяется для изготовления подкладок зимних туфель и ботинок.
Под конец отметим, что отсутствие подкладки не является индикатором низкого качества туфель. Модели без подкладки, как правило, оказываются очень удачным выбором, если вы ищете обувь для тёплой и тем более жаркой погоды.
Материалы для супинаторов (геленков)
Супинаторы (геленки) — это скрытые в глубинах ботинка элементы, которые поддерживают свод стопы и противостоят деформации обуви. Здесь отметим, что для их производства используются металл, дерево, пластик, стекловолокно и натуральная кожа. Некоторые фирмы вообще обходятся без супинаторов (классическим примером является американская компания Allen Edmonds).
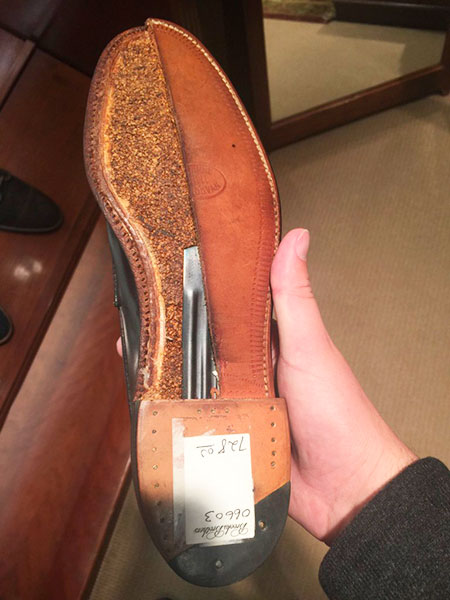
Материалы для каблуков
Качественные классические туфли и ботинки снабжаются наборными каблуками, состоящими из нескольких слоёв (фликов; heel lifts). Обувь высокого класса отличается наборными каблуками с фликами из добротной натуральной кожи. Некоторые производители используют для фликов кожкартон, который ценится ниже, выглядит хуже и менее надёжен. Кроме того, в наборном каблуке можно обнаружить резиновые элементы. Скажем, самый нижний слой является либо полностью резиновым, либо частично резиновым. Подробную информацию про составные каблуки можно найти тут.
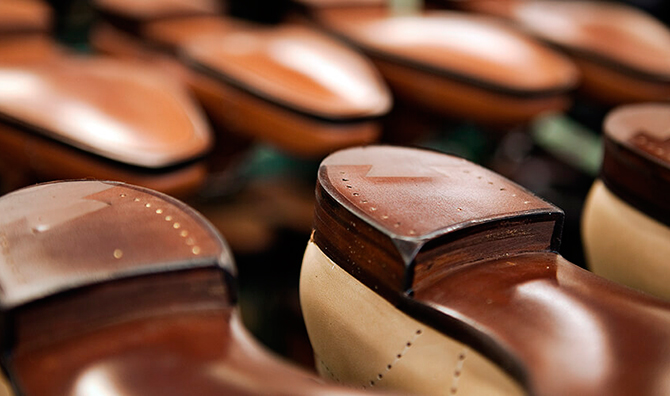
Добавим, что масс-маркетные туфли и неформальная обувь самых разных уровней (в том числе и высокого) могут снабжаться каблуками, которые составляют с подошвой единое целое… или же не составляют, но сделаны из того же материала. В качестве таких материалов могут выступать полиуретан (PU), термополиуретан (TPU), натуральная креповая резина (crepe rubber), этиленвинилацетат (EVA), термоэластопласт (ТЭП).
Материалы для уплотнителей задников
Уплотнители задников (heel counters/heel stiffeners) позволяют задней части обуви сохранять форму долгое время и придают ей надлежащую жёсткость. Они скрыты между внешней частью верха и подкладкой туфель, а для их производства используются натуральная кожа (genuine leather), кожкартон (leatherboard) и термопластик с текстилем (celastic). Кожаные уплотнители ценятся выше уплотнителей из кожкартона, а те, в свою очередь — выше термопластиковых вариантов. Дело тут не только в стоимости самих уплотнителей, но и в особенностях работы с ними. Ввиду особенностей производства обуви установка кожаных уплотнителей требует больших усилий, чем установка их собратьев из кожкартона, которые, в свою очередь, сложнее в установке, чем уплотнители из термопластика.
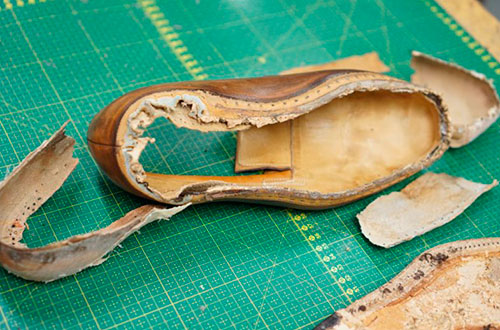
Если уплотнитель задника из термопластика или кожкартона выходит из строя (ломается), то «починить» его нельзя. Уплотнитель из кожи, однако, подлежит ремонту и восстановлению. Кроме того, кожа лучше всего со временем адаптируется под форму пятки; кожкартон — несколько хуже, а термопластик — ещё хуже. Как следствие, туфли с уплотнителями задников из термопластика при прочих равных могут быть менее комфортны в носке, чем туфли с уплотнителями задников из кожкартона и кожи. Для некоторых людей разница оказывается существенной и порой даже критичной, хотя стоит иметь в виду, что степень твёрдости и комфорта термопластиковых уплотнителей варьируется в довольно широких пределах. Кроме того, заметим, что даже в дорогой обуви можно встретить уплотнители из термопластика, а уплотнители из натуральной кожи встречаются лишь в туфлях стоимостью выше 400 евро за пару.
Материалы для уплотнителей мысков
Уплотнители мысков служат для придания необходимой жёсткости передней части обуви и для её предохранения от деформации. Как и уплотнители задников, они скрыты между подкладкой и внешней частью верха. Делаются эти элементы из текстиля, натуральной кожи и текстиля с термопластиком. Выше всего ценятся кожаные уплотнители мысков, но они встречаются лишь в очень дорогой обуви, так как их установка предполагает значительную долю ручного труда в производстве ботинок.
Даже туфли за 1000 евро могут иметь термопластиковые уплотнители мысков, но ничего страшного в них нет. Конечно, кожаные уплотнители хороши тем, что они принимают со временем форму стопы, но всё же в районе мысков стопа «сидит» в ботинке совсем не так плотно, как в районе задников, и это преимущество оказывается существенным далеко не для всех людей. Правда, кожаные уплотнители мысков позволяют немного растянуть ботинки в самой передней части, улучшив тем самым посадку.
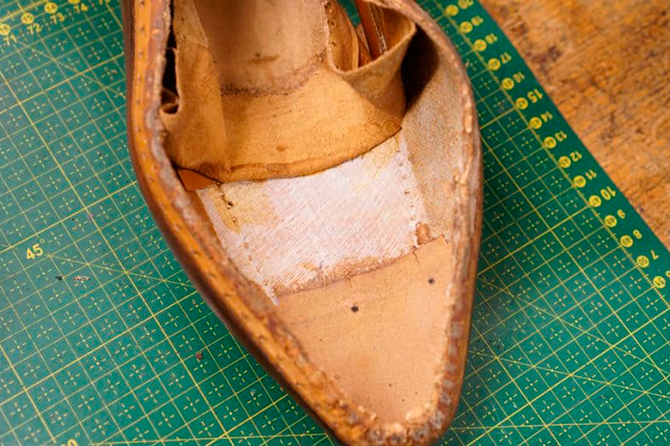
Текстильные уплотнители являются более гибкими, чем текстильно-термопластиковые, но они не способны дать ту же самую степень жёсткости, а потому при укреплении мысков строгой обуви обычно не используются… но зато их могут применять для придания формы боковым частям туфель.
Подробную статью об уплотнителях мысков можно найти тут.
string(0) «»
Как сделать подошву для обуви своими руками
О чем этот текстТехнология самостоятельного изготовления обуви
Обувь ручной работы пользуется большим спросом благодаря качеству и долговечности – обычно производство обуви ручной работы основано на натуральных материалах, требует более высокие требования к качеству готовой продукции. Соответственно, цена на обувь, сшитую вручную, будет выше в сравнении с изделиями, сшитыми на автоматизированном производстве.
Фирмы обуви ручного производства
Даже в век максимальной автоматизации обувь, изготовленная вручную, не является чем-то диковинным. Классические английские производства, которые высоко ценятся во всем мире:
Они выпускают обувь из натуральной кожи и замши, сшитую на ручном производстве. Этапов производства при этом значительно больше, чем при массовом автоматизированном изготовлении. Пара может изготавливаться в течение месяца, в зависимости от типа материала и сложности формы.
Что касается форм и конструкций, наиболее популярными ботинками в ручном исполнении являются:
Они отличаются по типу шнуровки. Оксфорды имеют закрытую шнуровку, скрытую передней частью ботинка. Боковые части пришивают клинообразно, возможна перфорация.
Дерби же, напротив, имеют открытую шнуровку, а боковые части нашивают поверх передней части таким образом, чтобы при развязывании шнуровки ботинок свободно расходился. Дерби также может иметь перфорацию и считается наиболее универсальной обувью для любого случая.
Особенности конструкции
Всю структуру обуви разделяют на верхнюю и нижнюю часть. В составе верхней части состоят такие элементы:
- Носок – закрывает пальцы ног, выдерживает наибольшие механические нагрузки при носке.
- Союзка – закрывает тыльную часть стопы и соединяет носок, язычок и берцы.
- Берцы – закрывают голеностопный сустав, их пришивают к союзке.
- Люверс – верхняя часть обуви, предназначенная для отверстий или крючков шнуровки.
- Задник – защищает пятку и стопу, фиксирует пятку, изготавливается из жесткой кожи.
- Язычок – покрывает верхнюю часть ступни, пришивается к союзке.
- Стелька – соединяет верхнюю и нижнюю части.
В составе нижней части изделия:
- Подошва – сшивается по контуру с верхней частью, делится на подметки, геленок, рант и наполнитель.
- Каблук – приподнимает пятку и крепится к подошве, верхний слой может быть каучуковым.
- Набойка – защищает каблук от протирания.
- Рант – связующий элемент между деталями.
- Защитные вставки – предотвращают истирание нижнего слоя каблука.
- Наполнитель – заполняет пространство под стелькой, повышает комфорт при эксплуатации.
- Супинатор – деревянная или металлическая деталь, закрепляемая между подошвой и стелькой.
Знание конструкции обуви позволяет изготовить каждую деталь более качественно, в соответствии с ее предназначением.
Этапы изготовления
Для изготовления обуви своими руками понадобится немало времени, но сам процесс несложный и зависит, в основном, от правильности замеров и качества исходных материалов. Весь процесс можно разделить на девять этапов.
Снятие мерок
Без этого этапа не обходится пошив обуви по индивидуальному заказу, то же касается и одежды. Снятие мерок осуществляется, главным образом, для замера параметров будущей колодки.
Создание макета
Подготовив по меркам колодку, шьют предварительный макет. Для его создания шьют по готовой колодке из тонкой натуральной кожи. Здесь же следует определиться, какой вид будет у модели, как располагаются швы, имеется ли рисунок или перфорация.
Подготовка выкройки
Заготовка для будущей пары ботинок вырезается из листа натуральной замши или кожи. Важно оставлять небольшой попуск на сжатие и шов – строго по контуру замеров вырезать нельзя, иначе обувь будет мала как минимум на размер.
Стадия обметки
Сшитые по выкройкам верхние части будущей пары ботинок соединяют вместе. Это трудоемкая часть работы, поскольку при обметке верхней части ботинок может потребоваться обтачивание кожи, подравнивание края, его подкрашивание.
Натягивание заготовки
На этом этапе уже готова колодка для будущей пары ботинок, а также верхняя ее часть. Теперь эту верхнюю часть в прямом смысле натягивают встык на ранее подготовленную колодку. На этом этапе наиболее важным шагом является укладка стельки, так как от правильности ее укладки зависит удобство при эксплуатации обуви.
Нашивка ранта
Рантом называют тонкую кожаную полоску, соединяющую все части ботинка, уже натянутые на колодку. Это изобретение принадлежит Чарльзу Гудиеру – благодаря его технологии, обувь может быть расшита по местам соединения рантом и починена в случае, например, потрескавшейся колодки, подошвы.
Пришивание подошвы
Подошва может быть выполнена из разных материалов – их следует заранее уточнить у заказчика, подсказав ему наиболее подходящий вариант к желаемой паре. Часто делают кожаные или каучуковые подошвы.
Пришитые подошвы укрепляются небольшими гвоздиками – мастера используют их для прямоты и надежности каблука. Последний набирают из толстой кожи в несколько слоев.
Окрашивание подошвы
После пришивания подошвы и набивания каблука необходимо окрасить их необходимым цветом – выбор цвета зависит от тона ботинок. При подсыхании нанесенной краски, подушка полируется для нанесения фирменной маркировки мастера.
Полирование
Ручное изготовление ботинок заканчивается самым важным этапом – полированием и доведением до идеального состояния готовой пары. После полирования получается ровная, упругая, идеально вычищенная пара с прочными соединениями.
Как сделать подошву для обуви своими руками
Метки: обувь из покрышки (читать далее…)
При чем тут лапти из бересты и подошва из жесткой резины? Поспрашивай у девушек про последствия металлических набоек для начала. Или пообщайся с людьми, которые служили и ставили победитовые или простые подковки (недельки) на сапоги. Такие все умные стали, когда интернет появился)))
Сообщества Сделай Сам Блог Подошва ботинок из покрышки своими рукамиМолодца, очуметь я бы не докумекал, мне теперь интересно на сколько такой подошвы хватит, наверное верху придет капец, а подошва останется. Как сделать подошву для обуви своими руками
Боковины (читать далее…)
- Сшейте передний шов.
- Пришейте между собой боковины.
- Можно укрепить пятку мягкой прокладкой – она делается в форме овала или ромба.
- Пришейте боковины к передним частям.
- Верх пришейте к подошве, соединив точки совмещения.
- Выровняйте припуски.
- Подровняйте и пришейте язычок – на 1-2 см ниже шнуровки.
Как сделать ботинки, туфли или просто тапочки, чтобы они были впору и нигде не терли? Для начала надо снять мерки, для чего понадобится самая обычная сантиметровая лента: Как сделать подошву для обуви своими руками
Топ проверенных способов, чтобы ваша обувь не скользила зимой (читать далее…)
Если обработать подошву водоотталкивающим средством, то ее влажность снизится, и при ходьбе увеличится сила трения. Но обработку потребуется повторять каждый раз перед выходом из дома.
Способы как сделать обувь нескользящей: Виды- Обзор ВидеоСпособ достаточно странный, но действенный. Вам потребуется, выходя из дома поверх обуви одеть носки. Хлопковая ткань отлично защитит вас от гололеда. Прослужит данный метод до тех пор, пока носки не сотрутся. Как сделать подошву для обуви своими руками
Наклейки из плотного пластыря (читать далее…)
Способ простой и несильно накладный, но ввиду быстрого изнашивания пластыря, за зиму уйти может не одна упаковка этой медицинской клейкой ленты. Причем подойдет только плотный пластырь, а не тот, которым закрывают царапины на пальцах. Заменить пластырь можно контактной лентой.
Антискользящие накладки для обуви своими рукамиПредварительно тщательно вымойте обувь и высушите и лишь потом нанесите клей на подошву. Плотно прижмите кусочки войлока и дайте клею засохнуть.
Строительный фен для прогрева поверхностей смазанных клеями — десмаколом и найритом. | Бумажный скотч. Применяется для обклейки колодки при изготовлении лекал модели. | Клеевая тесьма. Применяется при подгибке кожи в швах вокруг горловины туфля для предотвращения их растяжения при носке и при отстрачивании на швейной машинке. |
Нитки №20 и №40. №20 — ставится на верхний шов (при сборке верха обуви), а №40 ставится снизу в челнок машинки. | Клей SAR-306 (полиуретановый) (Старое название — «Десмакол»). Применяется для приклеивания подошвы. При правильном склеивании достигается высочайшая сила склеивания. Оторвать кожу можно только после сильного прогрева (около 80 град.), когда клей плавится и теряет свою прочность. | Найритовый клей — найрит — это хлорпреновый клей. Желательно работать с вытяжкой, т.к. клей довольно резок по запаху, а также вреден для глаз (по-видимому немного разъедает слизистую оболочку глаза.) Желательно искать импортный заменитель найрита. Используется при сборке верха и деталей, не испытывающих больших нагрузок на разрыв. |
Этилацетат — универсальный растворитель для найритовых клеев и десмакола. Иногда он отсутствует в магазине (для обувных комплектующих), тогда можно приобрести отдельный растворитель для найрита и отдельно для десмакола. | Сатреат — протрава. Ею предварительно промазывается полиуретановая подошва, после чего подтравливается ее верхний слой, что позволяет десмаколу глубже внедриться в подошву. Значительно усиливает силу приклеивания подошвы | Кисточки для клеев и протравы желательно использовать качественные — итальянские, т.к. не вовремя выпадающие ворсинки раздражают и замедляют работу. Для хранения кисточек используется отдельная банка, на дне которой всегда налит этилацетат. |
Сапожный молоток — используется исключительно при затяжке обуви, т.к. полукруглая поверхность ударной части позволяет обстукивать сверху кожу, которую только что приклеили к подкладке, тем самым выравнивая под кожей неравномерный слой клея, и «измельчая» случайные пузырьки воздуха, оказавшиеся в клею. Ни в коем случае нельзя этим молотком забивать гвозди и повреждать гладкую поверхность молотка. | Шила. С деревянной ручной для кожи, а без ручки для бумаги при рисовании лекал и переносе линий с одного лекала на другое. Можно пользоваться одним шилом, т.к. в нем заменяются «биты». Обычно «битов» покупается с десяток — разные по толщине и назначению. | Самый главный инструмент — сапожные клещи. Используются в основном при затяжке, но, благодаря своим малым габаритам, зачастую применяется в качестве обычного молотка. |
Щипцы — в основном применяются для выдергивания гвоздей из колодки, но частенько нужны и для других работ — очень необходимая вещь | Плоскогубцы с узкими и длинными губами — применяются при затяжке, чтобы добраться до самых узких складок между гвоздями, куда обычные клещи залезть уже не могут. | Ножницы для кожи и тканей. Не режьте ими бумагу, т.к. быстро от бумаги тупятся. Бумага это почти дерево, только тоненькое 🙂 |
А вот этими ножницами можно резать бумагу, но и кожу тоже ими удобно подрезать, особенно во время затяжки образуются иногода лишнии шмотки кожи, которые удобно подрезать маленькими ножницами. | Фигурные ножницы для кожи. Иногда на туфлях используется рифленый открытый срез кожи. Для этой цели и применяются эти ножницы. | Канцелярка — все что нужно для изготовления лекал. На розовой линейке лежат 2 стержня специально предназначенных для кожи (продаются исключительно в магазине обувных принадлежностей). Они оставляют серебристый цвет, который затем стирается салфеткой, слегка смоченной каким нибудь маслом, либо специальным затирающим маркером, который этот карандаш удаляет. |
Штангенциркуль — необходим при точении колодок и при подгонке левой колодки под правую. | Отвертка — применяется для завинчивания и вывинчивания шурупов из колодки при ее сборке и разборке. | Электродрель — применяется для сверления отверстий в колодках, для дальнейшего завинчивания в них шурупов. |
Электролобзик — применяется при выпиливании овальных слоев будущей колодки из строганной доски. Также удобен при изготовлении всевозможных стеллажей, ящичков и т.д. | Заточные бруски — один грубый для подводки вогнутых щечек ножа — для этого именно применяется брусок с овальными боками. Второй — самый тонкий брусок — для окончательной тонкой заточки режущей кромки. Бруски при работе должны быть мокрыми, поэтому хранятся вместе со своей пластиковой банкой. | Набор ножей для работы с кожей. Самый верхний — для картона и толстой стелечной кожи. Средний — чисто брусовочный нож (Применяется только для утоньшения торцов кожи. Он натачивается перед каждой парой обуви до остроты бритвы, и во время работы подводится на ремне 2-3 раза). Внизу нож для резки и подрезки обычной кожи. Ему не обязательно быть острым как брусовочному ножу, поэтому режущая кромка у него поуже. |
Обычный кухонный нож из нержавейки. Применяется для грубого обстругивания колодок. Несмотря на свою дешевизну, обладает невероятно прочной сталью. Одной хорошей заточки хватает для обработки 2-х пар сосновых колодок. | Вот такой значок на этом ноже. Очень достойная марка — купите — не пожалеете. | Сапожные гвозди. Длина 2,5 см. При покупке возьмите щепотку в руки и убедитесь что не встречается «росщип» — это когда на кончике гвоздя остаются кусочки металла. Такие бракованные гвозди быстро выведут колодку из строя. |
Рашпиль — применяется для шлифовки кожи после затяжки, когда необходимио подровнять затянутую снизу колодки кожу от остатков срезанных складок. | Зажигалки — применяются для отжига разлахмоченного края кожи после отрезки ножницами, а также для отжига узелков толстой нити, когда вручную шьются мокасины или прошивается подошва. | Два типа наждачной шкурки для обработки краев и складок гранитоля (который применяется для укрепления задника и носка туфля). |
Одежная щетка — поможет быстро смести мусор с поверхности стола, что часто бывает нужно при переходе от одной операции к другой. | Кусок мраморной пластины толщиной от 2 до 3 см. (Можно приобрести в мастерской по изготовлению памятников) Применяется при брусовке кожи, когда утончается край кожи. Для этой операции нужна идеально горизонтальная поверхность, по которой легко скользит нож. Также применяется при отбивке стыковых швов (когда 2 куска кожи сшиваются встык, а не внахлест). | Катушка для толстой нитки. Обычно толстая нитка продается в больших катушках, которую невозможно приспособить к бытовой машинке, поэтому приходится вытачивать более компактную высотой 7-8 см. Можно и меньше — на любителя. (Именно эта сделана из черенка от лопаты) |
Струбцины. Маленькие применяются при склеивании колодки, а большая при приклеивании подошвы, чтобы подошва не съехала с нужного положения и не оказалась перекошеной. Т.к. при приклейке подошвы невозможно будет исправить ошибку, т.к. десмакол хватает мертво, поэтому подошву нужно заранее, до разогрева клея тщательно выставлять и прижимать за каблук струбциной, после чего прогревать носок и клеить сначала носок, потом пятку. | Штырь. Для тех, кто не захочет точить колодки самостоятельно, а будет пользоваться покупными понадобится при вытаскивании колодки из готового туфля. Т.к. пока ее не сложишь книжкой колодка фабричная из туфля не выйдет. Самодельная колодка разбирается с помощью шурупов и легко без проблем выходит. | Штырь вставляется в специальное технологическое отверстие наверху колодки и за длинный рычаг давится в сторону носка и колодка складывается и выходит из ботинка или туфля. |